Right i have finally got the time and some panels to make a start on my pickup No.2!
heres a few pics of what she looks like.
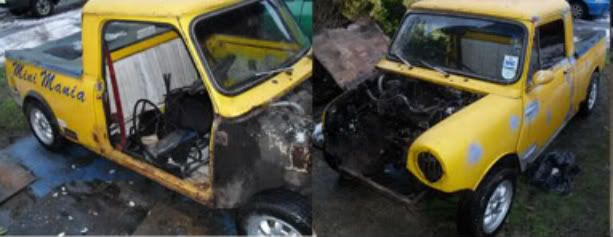
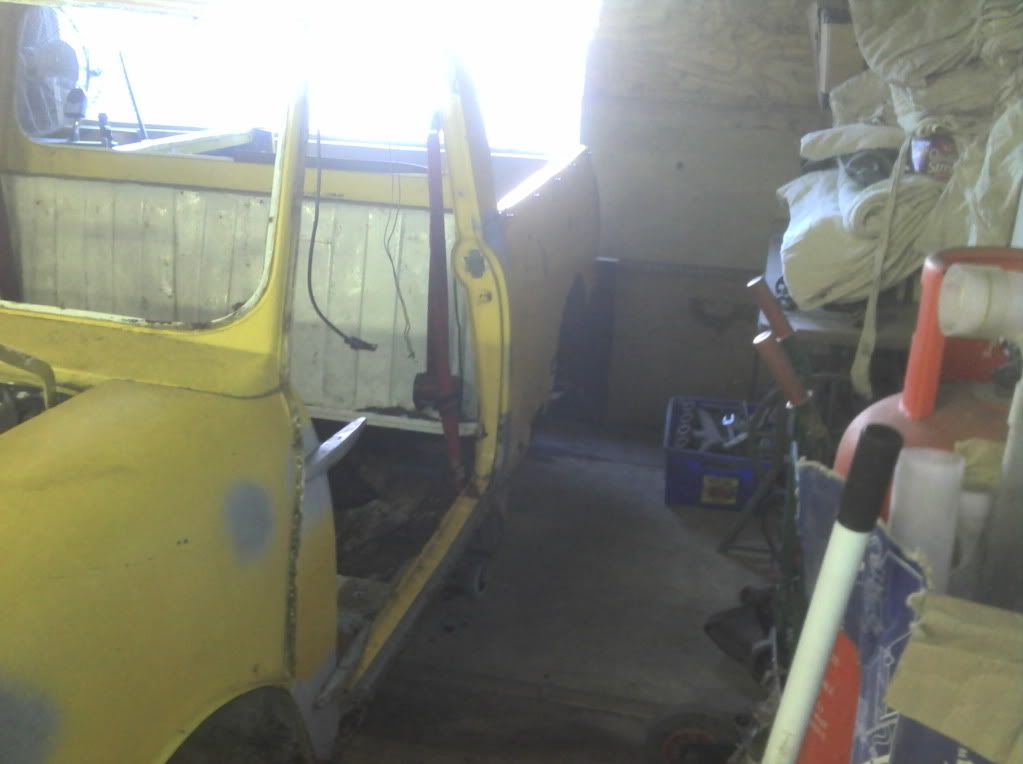
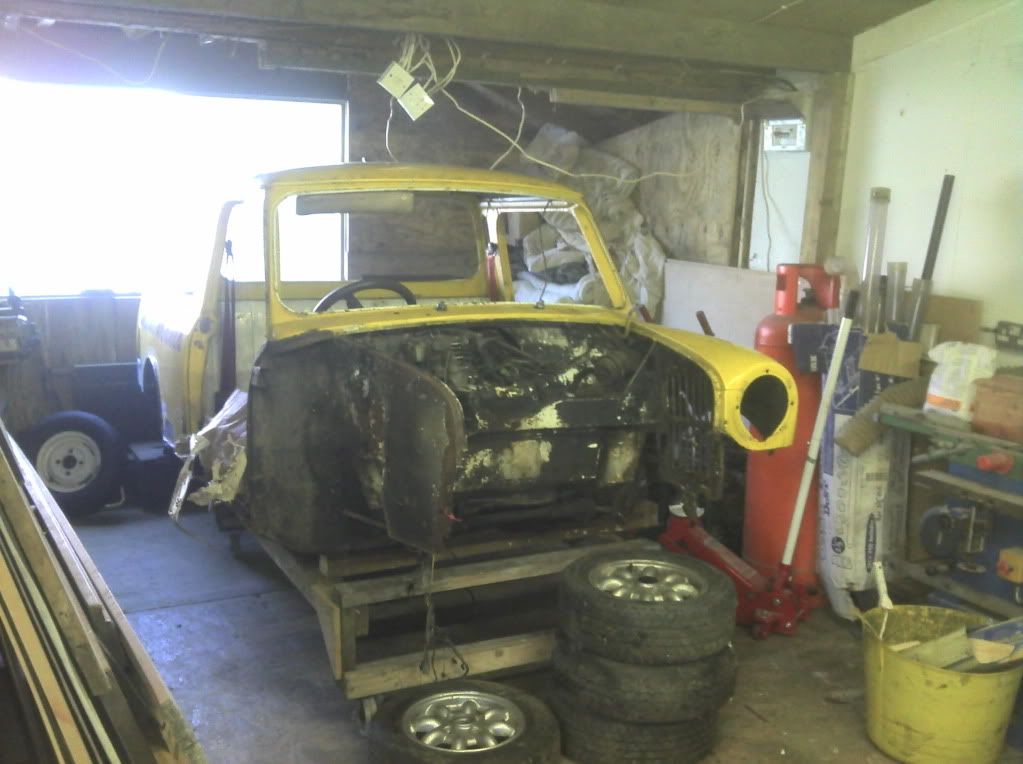
this pickup is needing much of the same sort of work that my dads pickup went through! there isnt a lot of the front floor pan left and what is needing repairs! the rear load bed is pretty rotten as are the rear quaters and bottoms of the wings!
so ideally i could do with another mini van base that we managed to acquire for my dads pickup resto!
Hmmm i think that was a once in a lifetime find!!
heres a link to our previous restoration project. http://www.theminifo...__fromsearch__1
so over the last year ive been looking for a rotten saloon mini that has got a fairly rot free floor pan! not easy to come by, but have managed to get one!
before you ask, i know the pickup is at least 6 inches longer than a saloon mini, but when the made the pickup they didnt make a longer floor pan they just made an extension panel which is available from the likes of Moss and Sommerford.
right after digging the floorpan out from the depths of our workshop we investigated it and came up with a plan of what to do and where to start first.
after looking at it it was apparent that the front footwells need some work on them, they arent totally gone but need some metal cutting out and replacing. because im a bit tight on money at the moment i cant afford to buy the floorpan replacement panels so ive had a go at cutting repairs out of a left over van floor panel from my dads mates body shop.
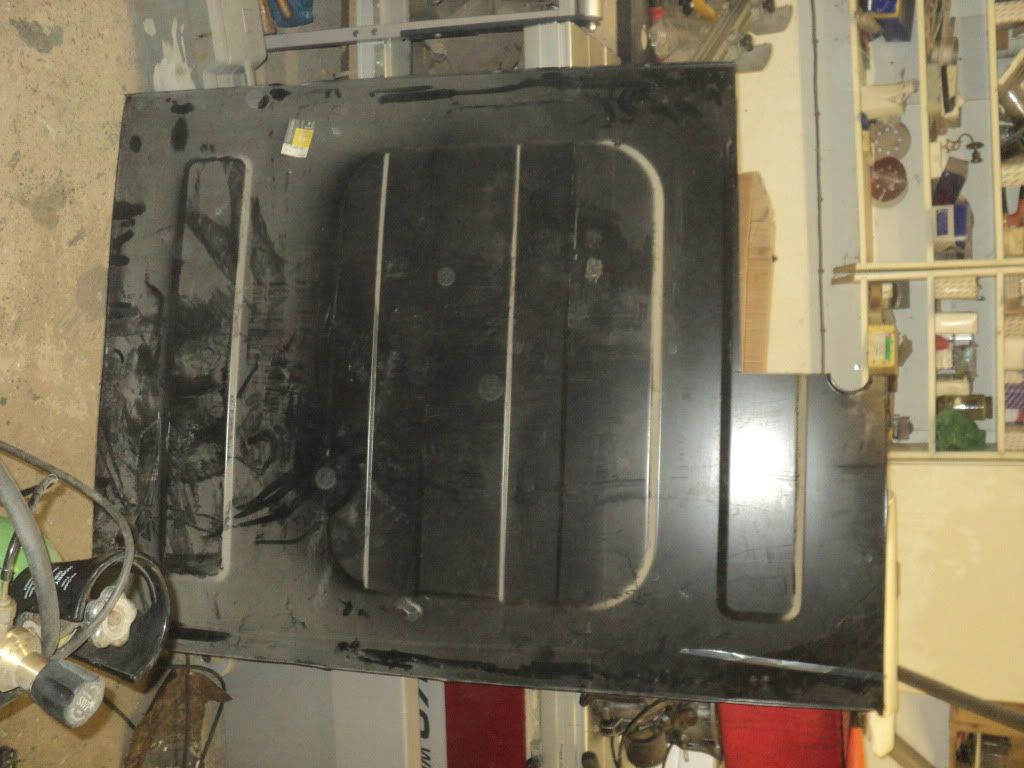
i templated the panel for the floor pan with some strong card then cut it out of the left over panel.
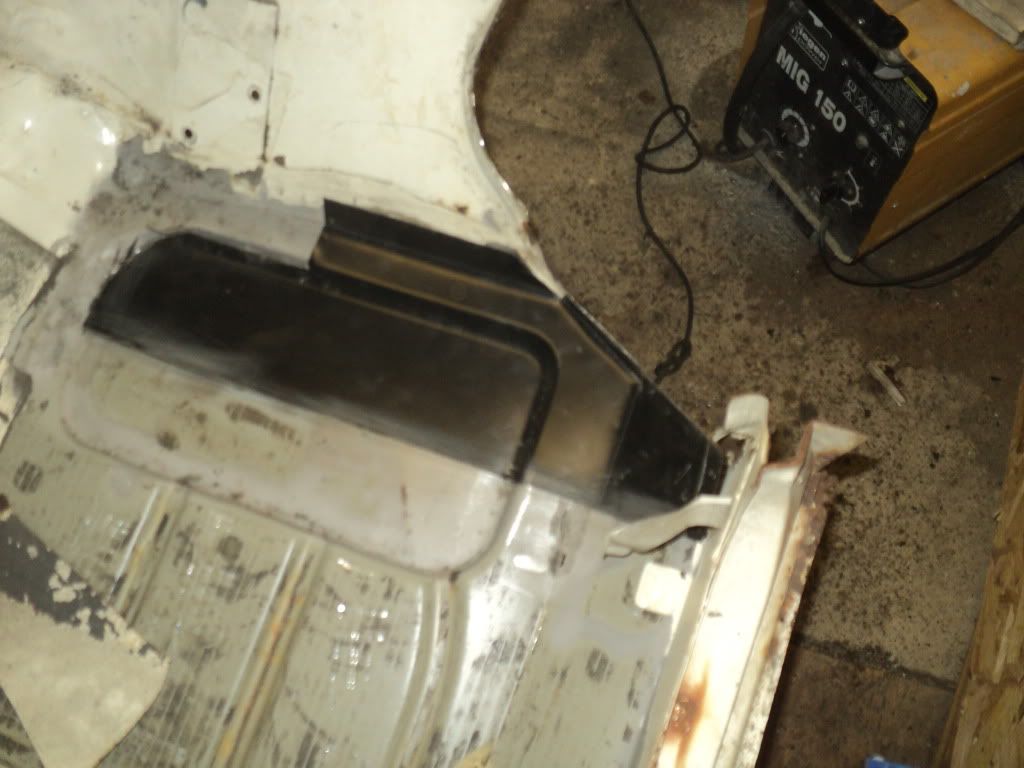
once i was happy that the panel was bent in the right places and fitted properly i scribed round it with a knife and cut out the rusty metal underneath.
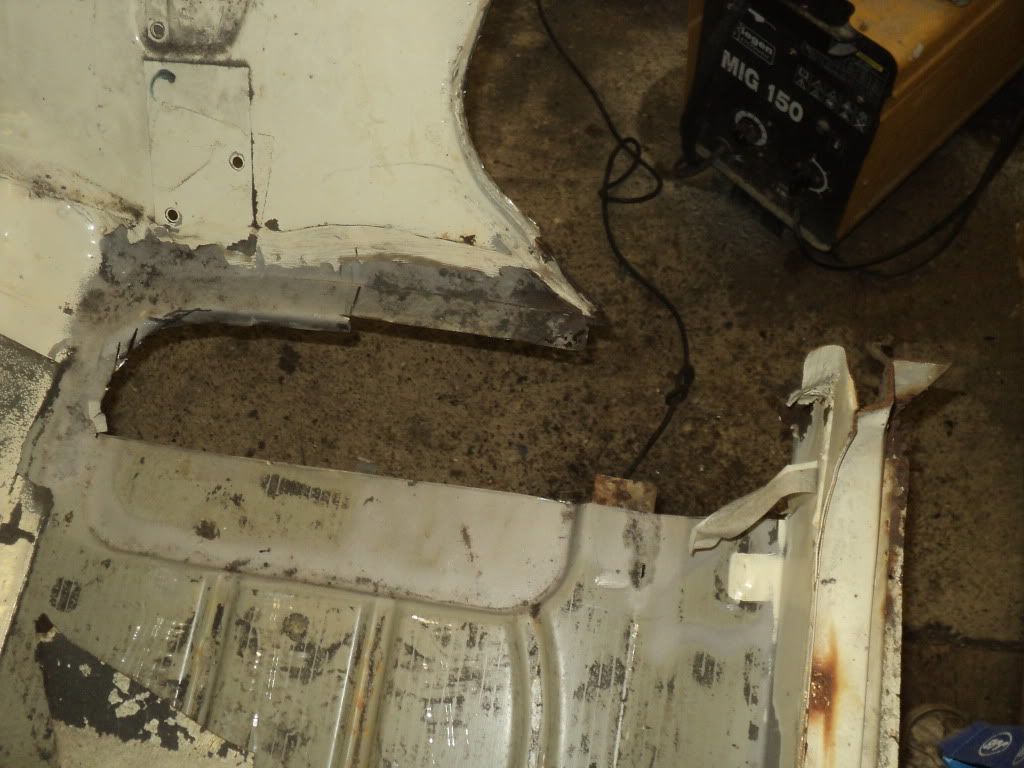
i procceded to tack the panel in place making sure i moved around the panel to minimise the distortion.
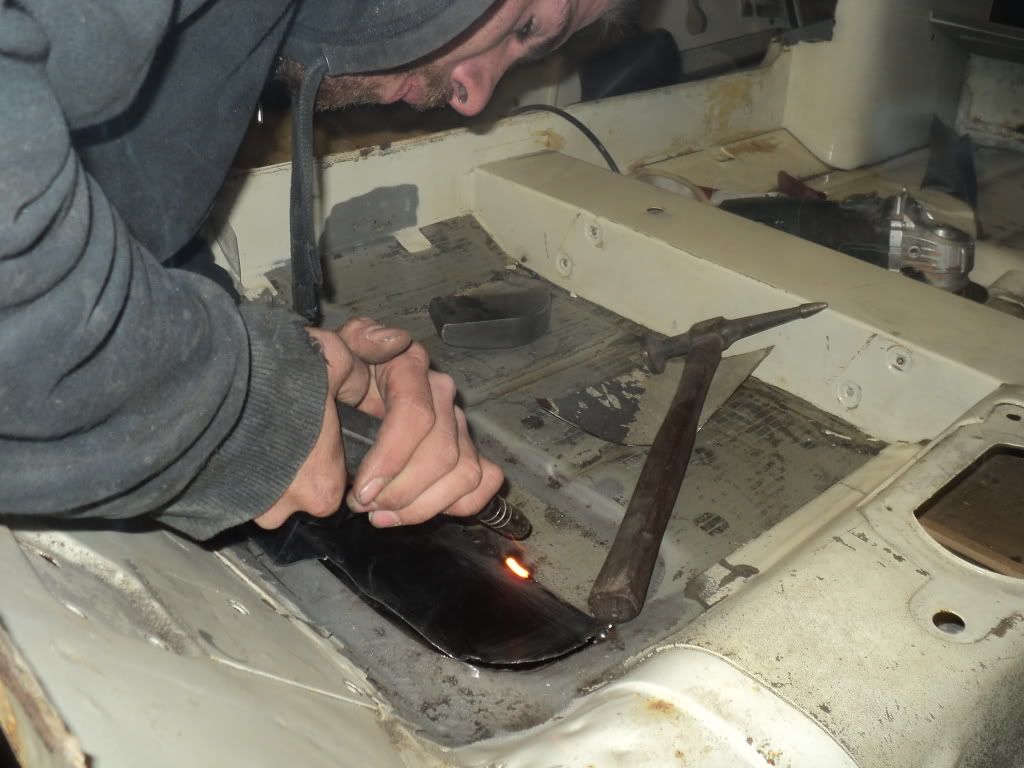
once this was done i turned the floor pan over and seam welded all around the panel.
with that done i turned my attention to the other floor pan which didnt need so much cutting out!
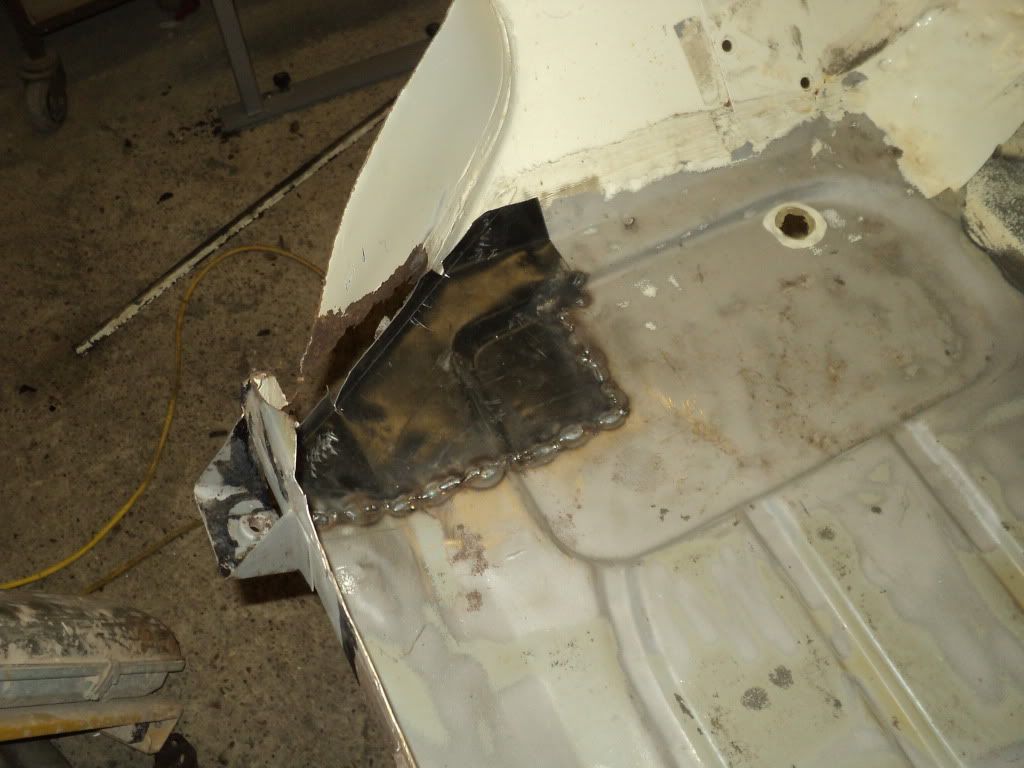
Edited by pickupmad87, 08 May 2020 - 06:58 PM.