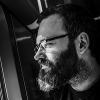
Custom Made: Light Weight Doors
#16
Posted 11 August 2019 - 11:53 AM
#17
Posted 11 August 2019 - 12:39 PM
You could also look at "lift a dot" fasteners if you're going with straps. They'd be a bit more secure and resist wear better.
You've got a constant load in the weight of the window so you'd ideally need a mechanism to match it to the rising force provided by a spring or bungee - you could easily find yourself back where you started with something quite similar to the original winder mechanism.
#18
Posted 11 August 2019 - 12:42 PM
Sorry i did not get it the first Time. :) Indeed it coud be an interesting mechanism. I'll look into those fastner too! Thx!
#19
Posted 11 August 2019 - 01:05 PM
#20
Posted 11 August 2019 - 09:15 PM
was just thinking i dont suppose there would be a problem with using a 50mm stip of velcro to pul the window up with?
#21
Posted 11 August 2019 - 09:57 PM
was just thinking i dont suppose there would be a problem with using a 50mm stip of velcro to pul the window up with?
That will definitively work. You Can but military grade velcro. You Can pull a car with a 10x50cm2 velcro junction. I used velcro to remake a Breuer Arm chair and it's solid.
However it's not the look i am looking for in this car. :)
#22
Posted 25 August 2019 - 07:17 PM
One may argue that nobody will see it but it is precisely because nobody will see it that it has to be good. :)
Edited by Benoit_Dupont, 25 August 2019 - 07:18 PM.
#23
Posted 01 September 2019 - 10:00 AM
Allright ! Time for an update on this project.
As mentionned, I was not too happy with my own aluminium chopping skills so I had it CNC'd out of aluminium.
before going any further, I should start with a clean door frame and repair all the bits and pieces from it. So in this episode, this is what I wanted to share with you. here we go, today it's all about this:
IMG_20190831_122209-01-W600.jpg 36.17K
0 downloads
I have used a fixed soldering mask for a long time and it's the first time i switch to LCD. It took me a while to trust the thing. I kind of value my eyes. but it works well. A bit of advise, if I may: don't go for a cheap "Amazonian" thing: your eyes, you only get a pair of those and no spare parts.
if the reaction time of the LCD is slightly off, or if the LCD fails to fire, you are in for a lot of trouble. Be carefull as well how you tune it. Since I do mostly weld points, and not cords, I set it to maximum dimming and a quite long reset time so the display stays dark quite some time. I got this one for about 250€. it's not that expensive and it works. it comes with poor taste deco on it that makes you like like a motorcycle racing-while-soldering badass ? I guess ? Maybe that's the intention ? Anyway it looke terrible but who cares.
As we all know, owning a british car is loving your live extra crispy. so here is the bottom of the door frame cut out
IMG_20190831_140855_045-W600.jpg 52.59K
1 downloads
first thing is to close all the welding spots that I drilled when removing the outer skin. here is one for example:
IMG_20190831_123852-W600.jpg 31.3K
1 downloads
on my door there were 4 to 5, but I am not sure how it varies from doors to doors. for instance, my left and right doors did not have the same amount of welding spots.
so if you intend to remove the outer skin, before you start pulling on that like a maniac, keep in mind that:
- there is one just below each pillar. (2 then)
- there is one next to the door handle screw. (what a poor design choice...)
- there is one at the level of the top hinge, bottom hole (the 3rd one then)
- That's 4. and then I found one on the bottom edge of the door, approx 8cm to the front edge... but only on the left door
check at least those areas for welding spots. they maybe others that I am not aware of, but at least this is what I got. I drilled those as I don't know of any other method to remove spot weld.
here is an exemple of pillar filled with metal and grinded.
IMG_20190831_125754-W600.jpg 34.48K
0 downloads
it's probably not the best, but it will do fine. if you have any tips, I'm all ears!
then I add to cut out the bottom door "lip". it was beyond salvage. so I cut it out and remade a strip to attach dimension:
IMG_20190831_141046_897-W600.jpg 57.8K
1 downloads
if you are new at this, a bit of trick. Again, I don't pretend it is "state of the Art" technic, but it has helped me so my apologies to the real pro welder of this forum of it ain't really the best stuff:
when you attach a new piece of metal to the old one, it is very difficult to solder "edge to edge". Even if you cut your metal best, as soon as you put the welder in action, it will difform, drill, or push the metal away. So I find out that it is easier, at lest for me to cut the metal 1cm longer than necessary and use a specific tool. I am not sure how it's called in english. in french it's a "pince à soyer". Google tells me it's "dimpling pliers", but I doubt it's accurate. please correct me with the exact name of that tool.
it looks like that:
pince-a-soyer-et-a-poinconner-T-2936075-7835683_1.jpg 4.25K
0 downloads
what this thing does is that it create a lip on the edge of metal so you can overlap the metal plates without changing the flatness of it.
So anyway, I used that, so I can actually solder the short edge of the metals not "edge to edge", but "edge to edge + metal on the back". this helps greatly.
in this particular case, after I was done with welding, I grinded those extra overlap bits away so my repair does not have extra thickness.
here it is corrected. it may not look the best but that will do and it is structurally more sound than the crispy bit.
IMG_20190831_164017-W600.jpg 37.97K
0 downloads
if you are new at welding, keep in mind it's kind of a patience game. you can not cord weld a new bit like. the best is to go slow, and weld first the external bits with one spot. (use clamps of course to maintain the part in place). keep the ground of the welder as close as possible to the welding zone and on the old piece of metal. not the new one.
once you have soldered the outer spots, solder one spot in the middle of the new part, then one spot in the middle of the 2 formed segments, then one spot in the middle of the obtained segments and so on.
always wait a bit between welds: if you overheat the new piece of metal, it will stress and distord and here goes your flatness. so take your time.
once you are done, grind it and immediatly apply anti-rust primer. welding spots are fairly sensitive to corrosion they should be protected.
Again, my apologies to the pro-welder there if you have better advises, they are more than welcome. it's my humble method. it got me through several cars restauration, but of course at my own pace :)
finally, I got my window mechanism machined and here is how it looks like now: quite an evolution from the previous !
IMG_20190831_201606-W600.jpg 38.58K
0 downloads
it's machined in aluminium.
IMG_20190831_211749_434-W600.jpg 45.05K
0 downloads
it looks nice, it works but I'm not yet completely happy with it. I will switch to a different material to get more strenght out of it. I'm considering Carbon fiber and/or full stainless steel.
hope you liked it ! you can also follow what I do on my instagram page if you like. I will of course post here anyway: my instagram is @benoitdupontphoto
cheers !
Edited by Benoit_Dupont, 01 September 2019 - 10:03 AM.
#24
Posted 01 September 2019 - 03:08 PM
The tool's what we'd call an edge joggler.
It's not a verb that I think gets much use
#25
Posted 01 September 2019 - 07:48 PM
The tool's what we'd call an edge joggler.
It's not a verb that I think gets much use
Thx for the info! I'll think of it next time I'm joggling my joggler! [Sounds kind of dirty actually] :)
#26
Posted 08 September 2019 - 06:41 PM
allright, did not get much done this week-end as I had to redo a part of my workshop for a project I'll be sharing with you guys in due time.
but in the meantime, here is a detail shot of one of the mod made to the door:
IMG_20190908_195006_832-W600.jpg 35.66K
0 downloads
Just some holes with finishing grommets on the edge of the door. won't save you any weight, maybe a couple of grams but that's absolutely not the point. major weight saving on those doors will come from:
- aluminium skins
- new window pull mechanism instead of winder
- inner door panel removal
- maybe (but I'm not sure where I stand on this), 5mm Lexan side windows that will slide up and down.
I might go for DSN Retrosport door hinges, but I still have doubts about their capacity to handle the weight. I guess they work marvel with fiberglass doors, but lightened metal, not sure...
from the exterior and interior, it will look as stock as possible. What is important for me is detail, even if nobody will see it once the door is closed. I just like the idea that those holes are there on the side of the door.
I might go for DSN Retrosport door hinges, but I still have doubts about their capacity to handle the weight. I guess they work marvel with fiberglass doors, but lightened metal, not sure...
#27
Posted 21 September 2019 - 06:04 PM
Hi,
so quick update today on this topic. i made quite some progress. I received from manufacturing the V3 prototype. quite some changes:
- the design is is much more rigid with new brace plates on the back of the window
- all made of stainless steel, because the 1.5mm aluminium was too much of a risk in the end. it bended too much.
here below are 3 generation of this prototype and I must say I'm quite pleased. I'm a long way from home made DIY cut aluminium.
IMG_20190921_185438-W600.jpg 20.03K
1 downloads
because the entire thing is now stainless, I has to change my hardware as well. So I bought stainless steel rivets, bolts and nuts, to be sure I don't get galvanic corrosion.
because it is so rigid, the extra little thickness of the rivet makes the window click in nicely and firmly. no need for glue, which was one of my concerns.
IMG_20190921_181015-W600.jpg 32.45K
2 downloads
it still does not weight much (500g) in total.
New stainless support plates have been also manufactured and produced. they also replace the banged up aluminium I hammered some time ago.
IMG_20190921_181024-W600.jpg 25.27K
0 downloads
on the inner side of the door, I have now placed the retaining bolts for the window pull mechanism and it works nicely. the lenght of the stud is calcuated so that it will sit flush with the standard door card. I'm expecting old door cards tomorrow so I can start testing without damaging good ones.
my next problem to solve is actually not a trivial one. i discussed this previously with some of you guys and i have been looking for a way to secure the leather strap. there are several systems that would be ideal: Loxx for instance, or dot fasteners. both have been used in automotive and even military application. no doublt this will work. however there is a catch:
when the window is going down, the fastners have to go inside the door. and if they are too big, well they will get stuck, or prevent the window from going up again.
So I found a blind nut with a lip, all in stainless still that works well. it keeps the window up or down and it's all in shiny stainless so it will look ok on the door card.
But this lip is too sharp and every time I manoeuver the window, it tears a bit the leather. in the long run, it's not acceptable.
ideally I would need a ball end. I do find some but they are often more bolt than nut. and a bolt is no option: because when the door card is in place and the door skin too: there is no way to hold the bolt in place while puting the bolt in place. I could of course use rivetted bolt, or soldered bolt. but those are not that common of a tools and I would like to keep it simple.
So I think I will go for heavy duty eyelets and see what happens. some are heavy duty and are for instance used for trucking.
in a ideally world an innocenti window would be so much simpler because the window is not that wide and it slides straight but ok, you have to do with what you have. :)
#28
Posted 07 October 2019 - 07:23 PM
Quick update tonight.
allright I have been working on the straps and I found great eyelets to make my system work. check it out!
IMG_20190929_160246-W600.jpg 31.42K
0 downloads
those are 15mm Nickel Eyelet. the leather strap is not yet treated, that's why it looks a bit grey. this is called "fat" or "oily" thick 3.6mm leather that will develop a nice patina over time. The door card will have 2 stainless steel blind M5 button for safey: one at the top and one at the bottom:
IMG_20190929_160242-W600.jpg 33.38K
0 downloads
the one at the bottom is not too low so one can fetch it in the car easily. the one. the additional eyelet at the bottom serves for 2 reasons:
first when the window is fully down; the eyelet will attach to the top button nicely.
second it adds weight which keeps the strap nicely flat.
I have this set-up in the workshop to see how the strap will react.
next thing will be to edge kote it and burnish it to make the edges smooth.
how by the way, all the metal with stripe patterns on the door internal sheet will go. :)
that's all for tonight folks ! have a good one !
0 user(s) are reading this topic
0 members, 0 guests, 0 anonymous users