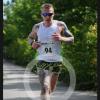
Abit Of Advice Needed Before I Part With My Hard Earned!
Started by
leadly
, Jul 28 2010 10:54 PM
11 replies to this topic
#1
Posted 28 July 2010 - 10:54 PM
Hey people, getting to the stage on my mini now where welding can finally take place, which brings me to my first question.
What thickness of sheet metal should I buy/aqquire to use for patching holes up with?
Would one thickness do for anywhere on the car or should I be buying an assortment of thickness' for different sections?
I need to weld in bit and bobs to the following areas:
o/s footwell, a shocking bit of welding has been done by a previous owner as there's hole in the welds. so i'll re-do that
Patch in the boot floor
A rather large hole in the n/s passenger bin
Small patches on door steps
Few bits on the window frames
My second question is whats the best tool to use when trimming up patches for a perfect fit, I'v got a collection but want to know what others use.
I think thats all for now but i'll add more after I get back from the garage tomorrow.
Thanks in advance,
- Rich
What thickness of sheet metal should I buy/aqquire to use for patching holes up with?
Would one thickness do for anywhere on the car or should I be buying an assortment of thickness' for different sections?
I need to weld in bit and bobs to the following areas:
o/s footwell, a shocking bit of welding has been done by a previous owner as there's hole in the welds. so i'll re-do that
Patch in the boot floor
A rather large hole in the n/s passenger bin
Small patches on door steps
Few bits on the window frames
My second question is whats the best tool to use when trimming up patches for a perfect fit, I'v got a collection but want to know what others use.
I think thats all for now but i'll add more after I get back from the garage tomorrow.
Thanks in advance,
- Rich
#2
Posted 28 July 2010 - 11:03 PM
Blag some scrap from a local fabricitors, bodyshop etc. 18 gauge should do you - likely to be a little bit thicker. A sharp pair of snips are good for trimming where the waste is narrow enough to curl up.
#3
Posted 28 July 2010 - 11:53 PM
Cheers for that, I was gonna go down to my local place to order some square tubing so I mite be able to blag a little more if i'm buying something.
#4
Posted 29 July 2010 - 12:31 AM
Tools for cutting/shaping your sheet metal... I used the following recently:
- Colin.
- Set of aviation snips (left hand, right hand, and straight snips) - you'll pick up an OK quality set of 3 on eBay for pennies.
- 4 1/2" angle grinder with a 1mm cutting disc (goes through 18 gauge like butter!)
- 4 1/2" angle grinder with a flap disc (good for trimming if you didn't cut off enough with the snips, and great for tidying up excess/messy weld)
- Colin.
#5
Posted 29 July 2010 - 04:35 AM
not sure what its called in english but 0.8mm thick is what i used to repair patches.
And i agree with the disk choice for the grinder
Michael
And i agree with the disk choice for the grinder
Michael
#6
Posted 29 July 2010 - 09:06 AM
Cheers guys, think i'll nip to machine mart on my way home from town today then to wee what they have.
Here you got Kez, abit of reference for yah!
Gauge mm (approx.)
34 --------- 0.16
32 --------- 0.20
30 --------- 0.25
28 --------- 0.32
26 --------- 0.40
24 --------- 0.51
22 --------- 0.64
20 --------- 0.81
18 --------- 1.02
16 --------- 1.29
14 --------- 1.62
12 --------- 2.05
Here you got Kez, abit of reference for yah!
Gauge mm (approx.)
34 --------- 0.16
32 --------- 0.20
30 --------- 0.25
28 --------- 0.32
26 --------- 0.40
24 --------- 0.51
22 --------- 0.64
20 --------- 0.81
18 --------- 1.02
16 --------- 1.29
14 --------- 1.62
12 --------- 2.05
#7
Posted 29 July 2010 - 09:17 AM
I don't know where your table comes from but this is what I recognise, 20 guage is perfect for mini repairs, I find 18 guage hard work on patches
16 ---- 1.626
18 ---- 1.219
20 ---- 0.914
22 ---- 0.711
Cheers
David
16 ---- 1.626
18 ---- 1.219
20 ---- 0.914
22 ---- 0.711
Cheers
David
#8
Posted 29 July 2010 - 09:19 AM
Car bodies will typically be between 18 & 22 gauge, of course when they've been through a press thickness varies, even on the same panel.
My old text book agrees with R1
16swg---64thou ---- 1.626
18 " ---48thou ---- 1.219
20 " ---36thou ---- 0.914
22 " ---28thou ---- 0.711
My old text book agrees with R1
16swg---64thou ---- 1.626
18 " ---48thou ---- 1.219
20 " ---36thou ---- 0.914
22 " ---28thou ---- 0.711
#9
Posted 29 July 2010 - 09:33 AM
Just been on ebay and bought a 3pc aviation snips set for £7.99 and got a pack of 5 zincronium flap discs for £4.20.
Already got the 1mm cutting disc's and angle grinder tucked away in the garage.
When the weathers to bad to work on my mini I tend to stay indoors and buy things on ebay that I might need one day. Can get quite expensive when it seems to be all year round. lol
Already got the 1mm cutting disc's and angle grinder tucked away in the garage.
When the weathers to bad to work on my mini I tend to stay indoors and buy things on ebay that I might need one day. Can get quite expensive when it seems to be all year round. lol
#10
Posted 29 July 2010 - 09:38 AM
that guide i found was the first thing that came up on google, so just assumed it would be right.
Cheers guys.
20 gauge it is then
Cheers guys.
20 gauge it is then
#11
Posted 29 July 2010 - 06:12 PM
0.9mm for most body parts, 1.2mm for rear heelboard, front bulkhead crossmember.
#12
Posted 29 July 2010 - 06:47 PM
That's exactly what I'm using. I picked up a 4' x 2' sheet of 1.2mm from my local motor factors for about £12 or so. 0.9mm was a bit cheaper,
JR
JR
1 user(s) are reading this topic
0 members, 1 guests, 0 anonymous users