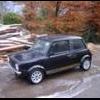
How Do You Enlarge Your Combustion Chamber?
#1
Posted 12 April 2009 - 08:06 PM
is is possible to do it at home or do you need to send it to a machine shop??
i need as much as possible for a supercharged 1380, somthing like 28cc would be good.
cheers
#2
Posted 12 April 2009 - 08:17 PM
At home you'd need a good die grinder and a range of different cutting stones and attachments, some diagrams of shapes/patterns to work to and a burette to measure the chamber sizes as you go along.
Have a read of this: http://miniclassic.y...dify-heads.html
Also this: http://www.turbo-min...4648/30148.html
and some pricing info here: http://www.turbo-mini.com/66122.html
#3
Posted 13 April 2009 - 08:53 AM
#4
Posted 14 April 2009 - 06:40 PM
cheers
#5
Posted 14 April 2009 - 06:46 PM
#6
Posted 14 April 2009 - 06:50 PM
if i am amimng for 8:1 then i need 15cc extra at TDC, my head chambers are 19cc and piston dish are 7cc. i have worked out that if i enlarge my combustion chamber to 30cc and get 11cc pistons then i would be pretty near 8:1
i am trying to avoid using the decompression plate if possible
cheers
#7
Posted 14 April 2009 - 07:14 PM
#8
Posted 14 April 2009 - 07:24 PM
http://www.pelicanpa...ssion_ratio.htm
#9
Posted 14 April 2009 - 07:30 PM
how to calculate your comp ratio is explained here in this link, it makes it a hell of a lot easier than working it out by hand...
http://www.pelicanpa...ssion_ratio.htm
Thanks, just need to work out what to put in each cell!!!
#10
Posted 14 April 2009 - 07:39 PM
It all came out nicely to size. I did one chamber first until it was the right size, then made a template of the periphery of the chamber and using 'engineers blue marker', marked the other profiles. Finally checking the volumes I aimed for +/- 0.25 cc per chamber and this was easy to obtain.
Now, to get the chambers much bigger for a larger capacity engine (1380+) running, maybe, higher boost could be a problem. How about using the very old way of making a thin copper plate to the exact shape of a head gasket, then fitting it with a standard (BK450?) gasket each side. The BK450 has a volume of 4 cc and it would be easy to get a piece of copper with a volume of about 4 cc (i.e. the same thickness as a BK450). That way you'll gain the extra 8 cc or thereabouts that you need. Double gaskets without a copper plate between are not a good idea. I guess one could use a steel plate instead. I would use AP Racing head studs and torque it down to around 58 lb.ft. torque.
This will also effect the rocker geometry and the rocker shaft feet may need machining down by the extra thickness.
#11
Posted 14 April 2009 - 09:01 PM
I had a 1293 engine in recently which had blown-up after 4 miles from new build. It had a Metro turbocharger with a boost of +6.5 lbs. Unfortunately the so-called engine builder did no calculations with a result that it not only had the wrong pistons, but a geometric comp ratio of 10.5:1 which gave a comp ratio of something like 14.8:1 under boost. Also the distributor had not been re-curved to delay the advance so it just detonated. It's not surprising that it broke all its pistons. The original builder just did not want to know so I rebuilt it. I needed a comp ratio of 8.4:1 and got this by fitting Omega pistons with a 10.5 cc dish and opening out the head chambers to 24.5 cc using a die grinder with the usual assortment of bits, a syringe to measure to volumes, a piece of flat perspex with 2 holes to put over the chamber face when measuring and a couple of flap-wheels nd a lot of patience.
It all came out nicely to size. I did one chamber first until it was the right size, then made a template of the periphery of the chamber and using 'engineers blue marker', marked the other profiles. Finally checking the volumes I aimed for +/- 0.25 cc per chamber and this was easy to obtain.
Now, to get the chambers much bigger for a larger capacity engine (1380+) running, maybe, higher boost could be a problem. How about using the very old way of making a thin copper plate to the exact shape of a head gasket, then fitting it with a standard (BK450?) gasket each side. The BK450 has a volume of 4 cc and it would be easy to get a piece of copper with a volume of about 4 cc (i.e. the same thickness as a BK450). That way you'll gain the extra 8 cc or thereabouts that you need. Double gaskets without a copper plate between are not a good idea. I guess one could use a steel plate instead. I would use AP Racing head studs and torque it down to around 58 lb.ft. torque.
This will also effect the rocker geometry and the rocker shaft feet may need machining down by the extra thickness.
thanks for your reply, did you enlarge your chambers yourself, could you just describe how you did this and with what tools? did you manage to avoid the valves or did you replace them with old ones? or did you remove them?
cheers
rob
#12
Posted 15 April 2009 - 03:55 PM
I've done loads of heads over many years. I replace the valves with 'gash' old ones for the main grinding work. I use a 22000 rpm die-grinder and a Bosch electric drill. Actually, the electric drill is just as effective as the die-grinder and seems easier to control. Most of the tuning books will show you the critical areas to remove to improve flow in the head and the 12G940 seems to have lots of 'meat' which can be safely removed. The main areas for metal removal are around the inlet valve to enable the gases to enter more easily, remove a lot of the 'beak', then remove around the exhaust valve. Mark the full circumference of the bore onto the head by using 'engineers blue' marker fluid and run a scriber (or sharp screwdriver) around the bore circumference of a head gasket which you hold in place.
If you can, practise on a old scrap head before starting on the real one. Measure using 10 cc syringe which you can buy from Boots the Chemist. I use paraffin to measure after making sure the head is sitting absolutely level with the valves in and a plug in. Have a flat piece of perspex with 2 holes. One hole is for filling and the other for the air to get out. Use a bit of grease to seal around the edge of the chamber. You'll see when it's full and the air is all out. It's easier than it sounds.
Once one is the right shape and size, make a cardboard template of the chamber edge and use this to mark the others. Then grind them out to the same volume.
Finally smooth out the rough ground surface with small flap-wheels in the electric drill. The last bit of grinding is done with the valves out and you have to be very careful not to cut the valve seats. It can be done with care. I would aim for a combustion chamber of no more than 24.5 cc, 25 cc at most, then use dished pistons and/or double gaskets with a thin spacer plate to get the ideal volume for the boost you want to use.
Make sure you have calculations for it all and check them before finalising the configuration.
Good luck with this,
Peter
Good luck with this.
1 user(s) are reading this topic
0 members, 1 guests, 0 anonymous users