Hi guys, long time no hear.....I have been to look at a mini van that needs restoration. It pretty much needs all the floor pans replaced....I have never attempted to weld but really want this project to be all my own work. So can anyone tell me how easy or otherwse it is to replace the floor pans....in particular the rears?? The load bay is ok and I was wondering how to get to the floors, do you just weld from underneath?? Also the rear wheel arches are rusted through (i guess this is near the rear subframe mount points.....how would you go about replacing this?
Thanks in advance?
~~~~~Please delete this text before posting the topic~~~~~~
Please give your topic a title that quickly describes your problem. Just putting 'Help my Mini doesn't work' is useless to anyone trying to help.
~~~~~~~~~~~~~~~~~~~~~~~~~~~~~~~~~~~~~~~~~~~~~~~~~~~~~~~~~~~
Model:
Year:
Description of problem (please be as in depth as possible):
Any non-standard parts that might be involved with the problem?
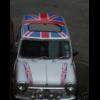
Mini Van Replace Floor
Started by
Adelante
, Jan 16 2011 05:40 PM
1 reply to this topic
#1
Posted 16 January 2011 - 05:40 PM
#2
Posted 16 January 2011 - 07:39 PM
The short answer is not that easy.
First learn to weld. I would look at doing an evening welding course or similar. You may find that it just isn't for you and will save money from buying a van that you can't do and equipment that you won't ever use (as well as the consumables that go with it). I wish I had done a course on mig welding before starting my mini project. I could arc weld so had some experience but I have looked back at my earlier work and realise that I need to go back, grind it out and re do it (Easter's job: redo rear boot floor seam). Would have saved me a lot of time and possibly some money.
If doing a full restoration job then first is to strip the vehicle (best way of not setting fire to important stuff in my experience). To replace floor pans then you will need to brace the van, across the doors, sills, side to side and any where it is likely to bend with the floor removed. Then using a combination of drill bits (for spot welds), tin snips, hack saws, grinders and any other cutting/grinding tools you have at your disposal remove the old rusted floor. Next all edges that need to be welded need to be cleaned ( the more effort you put into cleaning them and the better you do it, the better your welds will be). Anything that needs welding to that is rotten will need to be cut out and replaced. Finally once everything is solid to weld to the new panel will need offering up to it. It will most likely need trimming to get it to fit (depends on the quality of the panel). Then clamped into place and tack welded together. Check that everything is straight then (if it is straight) commence burning it together.
Remember to put some paint on anything that is bare as soon as possible if it has been welded or going to be left for a while as it is amazing how soon it starts to rust up again.
Some people recommend leaving as much of the original metal in place. Depending on the severity of the corrosion this may be true. My mini had a couple of small(ish) holes in places about the size of the palm of my hand. These I have welded patches into. If you can see day light through the majority of the floor then I would replace the whole panel. At least you know then that the floor is solid. (my personal preference and opinion)
Anything that was spot welded originally can be spot welded again. If not then it must be seam welded.
A few people told me that a good project to start of with to test you welding skills is to build a dolly and/or spit so that you can move the car around and roll it over to make it easier to work on. The dolly I built can take the full weight of a mini (that includes engine and suspension although not interior). Remember to use caster wheels that can take the load (can get them of ebay for about £20).
Good luck with the possible project.
First learn to weld. I would look at doing an evening welding course or similar. You may find that it just isn't for you and will save money from buying a van that you can't do and equipment that you won't ever use (as well as the consumables that go with it). I wish I had done a course on mig welding before starting my mini project. I could arc weld so had some experience but I have looked back at my earlier work and realise that I need to go back, grind it out and re do it (Easter's job: redo rear boot floor seam). Would have saved me a lot of time and possibly some money.
If doing a full restoration job then first is to strip the vehicle (best way of not setting fire to important stuff in my experience). To replace floor pans then you will need to brace the van, across the doors, sills, side to side and any where it is likely to bend with the floor removed. Then using a combination of drill bits (for spot welds), tin snips, hack saws, grinders and any other cutting/grinding tools you have at your disposal remove the old rusted floor. Next all edges that need to be welded need to be cleaned ( the more effort you put into cleaning them and the better you do it, the better your welds will be). Anything that needs welding to that is rotten will need to be cut out and replaced. Finally once everything is solid to weld to the new panel will need offering up to it. It will most likely need trimming to get it to fit (depends on the quality of the panel). Then clamped into place and tack welded together. Check that everything is straight then (if it is straight) commence burning it together.
Remember to put some paint on anything that is bare as soon as possible if it has been welded or going to be left for a while as it is amazing how soon it starts to rust up again.
Some people recommend leaving as much of the original metal in place. Depending on the severity of the corrosion this may be true. My mini had a couple of small(ish) holes in places about the size of the palm of my hand. These I have welded patches into. If you can see day light through the majority of the floor then I would replace the whole panel. At least you know then that the floor is solid. (my personal preference and opinion)
Anything that was spot welded originally can be spot welded again. If not then it must be seam welded.
A few people told me that a good project to start of with to test you welding skills is to build a dolly and/or spit so that you can move the car around and roll it over to make it easier to work on. The dolly I built can take the full weight of a mini (that includes engine and suspension although not interior). Remember to use caster wheels that can take the load (can get them of ebay for about £20).
Good luck with the possible project.
1 user(s) are reading this topic
0 members, 1 guests, 0 anonymous users