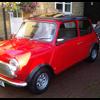
Welding And Gas ?
#1
Posted 05 February 2011 - 02:28 PM
Many thanks Andy
#2
Posted 05 February 2011 - 02:42 PM
I was going to use the 5% argon CO2 mix
These people seem cheaper than BOC and as you're in Kent delivery charges are reasonable.
There was a thread the other day about getting some welding classes running in Kent,
http://www.theminifo...x...79806&st=15
Edit to add link
Edited by Carlos W, 05 February 2011 - 02:48 PM.
#3
Posted 05 February 2011 - 02:48 PM
welding class would be great i would be instrested , well me and my dad.
Cheers Andy
#4
Posted 05 February 2011 - 02:49 PM
#5
Posted 05 February 2011 - 02:50 PM
#6
Posted 05 February 2011 - 03:08 PM
They all differ you just need to find a setting that works well for you. Generally you will only need a low power setting for mini panels as they are so thin, how ever on the thicker stuff like the rear heelboard will need a slightly higher setting for correct weld penetration.
Wire wise .6mm is fine for what you need to do although for heavier welding then .8mm would be better. Stick with the .6mm as this is what i have been using for Project Erm and it has been more than good enough.
The rest is down to practise, get yourself some old panels of the same thickness .9mm make sure the area you are going to weld is totally clean, no paint/primer etc. Where you attach the earth needs to be immaculately clean as this will determine how good the welds will be. Bad earth means bad or no welds its as simple as that.
To start try tack welding the panels together, use a spacing of 1" between welds. Once you are happy the tacks are strong, good penetration (turn the piece other you should see a high point of metal with heat rings.)
The next step you can do pulse welding which is multiple tack welds contacting each other to basically form a continuous weld. If this works well then you can start to do seam welding. Still keep a spacing of an inch tack welds, seam weld in between each tack to keep the distortion down so weld an inch miss an inch and so on.
This is just a general rule of thumb. There is a mig welding forum which will give you all the info you could possibly need.
#7
Posted 05 February 2011 - 03:19 PM
and yes i have just been looking through that forum at the tips and learning to weld and have found out abit.
oh and yh i knew i forgot something i have a Clarke MIG255TEC which is this welder http://www.machinema...ial-mig-welders
Cheers Andy
Edited by andymini12, 05 February 2011 - 03:20 PM.
#8
Posted 05 February 2011 - 03:22 PM
i think i will get gas from there then. that is something i will do next week. so i need to get a CO2 and argon mix but what percent of the mix ?Adams are in Margate, but for the £5 they charge to deliver within Kent I don't think it's worth driving the 100 mile round trip to go and collect it!
Cheers Andy
#9
Posted 05 February 2011 - 04:03 PM
Start on your lowest power setting and wire feed speed at two, this is only a guess as your wire speed range will be greater than mine. Go from there really. Gas pressure depends whether you are welding inside or outside. The gas regulator does it have two gauges, one for bottle pressure the other for nozzle pressure? for me as i weld inside i tend not to use the gauge reading but just have mine set to a gentle hiss which is fine for me. If i'm outside then i try to shiled the welding area and also increase the gas pressure to prevent loss of shielding gas.
#10
Posted 05 February 2011 - 04:09 PM
and i will try those power settings and wire feed when i get gas and have ago at welding. and im not sure if i have 2 gauges i carnt remember i will have a look later. i just need to know what mix to get now 5% or 20%.
Cheers Andy
#11
Posted 05 February 2011 - 04:24 PM
#12
Posted 05 February 2011 - 04:41 PM
thanks for all the help.
Andy
#13
Posted 05 February 2011 - 04:44 PM
thanks for all the help.
Andy
#14
Posted 05 February 2011 - 06:26 PM
You do of course have one of those don't you?
I use straight CO2 with the mig welder on car bodywork and have never seen a difference between it and either CO2/Argon mix or pure Argon on mild steel. The only place I use anything different is with the TIG but then I don't use that for bodywork.
Iain
#15
Posted 05 February 2011 - 06:39 PM

i think im going to go for the argon mix, appently it helps it not splat as much.
Andy
1 user(s) are reading this topic
0 members, 1 guests, 0 anonymous users