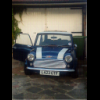
Welding Help
#1
Posted 14 April 2011 - 07:57 PM
I've got a MIG 140 and i'm trying to weld scrap bits together. I've cleaned the scrap bits of metal up and wiped them down
I'm having no luck welding as all im getting is it either being to much power and blowing through or too little and splattering.
I've not a clue what setting to try now.
Its a Wolf Mig 140, and im using gasless right now,
What setting's do you use and is gas better then non-gas? what welder do you use?
Cheers!
#2
Posted 14 April 2011 - 10:06 PM
hi guys,
I've got a MIG 140 and i'm trying to weld scrap bits together. I've cleaned the scrap bits of metal up and wiped them down
I'm having no luck welding as all im getting is it either being to much power and blowing through or too little and splattering.
I've not a clue what setting to try now.
Its a Wolf Mig 140, and im using gasless right now,
What setting's do you use and is gas better then non-gas? what welder do you use?
Cheers!
right your weld will look a mess all the time as its a gasless mig. i think it is pretty much impossible to get a nice clean weld with one. for a nice weld you really need gas. if its buring holes then turn the power down if its not penetrating turn up the wire feed just got to have a play about with it. i use a sealey professional mig welder 450 amp wich will probley be out your price range at £3000
#3
Posted 15 April 2011 - 06:42 AM
#4
Posted 15 April 2011 - 06:03 PM
or get somebody you know that can to give you a hand to learn. practice is the only way you are going to progress. If you don't want to do either then trial and error is going to be the only way. Gasless mig is a messy compared to gas mig welds but how strong it is will not be a problem when it is done correctly
450 amp is going to be a 3 phase joneseyboy and far too powerful to use on bodywork a 140 will be ample
#5
Posted 15 April 2011 - 06:44 PM
There are so many factors that affect your welding that the best advice has already been given, get tuition.............
I have workshop and mobile welding sets as part of my job, I`ve just bought a little esab caddy mig 160 amp, 230v. It takes 7kg rolls and can be carried anywhere, as with most top brand stuff, great arc and stable wire feed. £550 +vat.
I live in north notts and would happily give you a few pointers if you can get your set to my workshop on a sat morning. Then at least you can make sure your set is ok and that its just technique needed.
Seen a few guys trying to learn on sets that have had so many problems that a welding engineer couldnt have put a decent weld down. Not a very encouraging start.
Good luck and if I can be of help, feel free to contact me.
John
#6
Posted 15 April 2011 - 07:01 PM
Rather frustrating.
Cheers!
#7
Posted 15 April 2011 - 08:03 PM
And yes Charles it is three phase and we do a lot of commercial vehicles that's why its so powerful but its fine for cars aswell on a low setting once you get used to it.
#8
Posted 16 April 2011 - 02:18 PM
If you are trying to do this this and seam welding i would recommend trying the pulse welding method instead.
Yes you can seam weld a butt joint but when the metal is this 0.9mm it only takes a moments lapse in concentration to blow through. Personally i would tack weld the whole panel in place using one inch spaced tacks then pulse weld in between one set of tacks miss a set and so on. This will help to minimize distortion by not building up as much heat.
If however you have laid the panel in place with an overlap you should be able to seam weld this but again only do an inch at a time to minimize distortion. This you can seam weld the underside of the panel as well to give a very strong joint.
If you are doing this method and are still blowing holes then up your wire speed slightly to see if this helps and if not then you will need to reduce your power setting.
#9
Posted 21 April 2011 - 04:48 PM
1 user(s) are reading this topic
0 members, 1 guests, 0 anonymous users