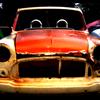
Help! De-seaming Structural Implications
#1
Posted 11 May 2011 - 02:01 PM
I've completed the de-seaming process on my project roadster for uni, in my write up i need to justify deseaming the body and comment on the technical aspects of the process, not just the process itself.
My common sense tells me that the deseamed shell will be stronger/ more rigid? than a shell that has the original seams.
because the load will be spread across the whole of the panels, not just concentrated around the spot welds on the orig seams..but i need to prove this.
does anyone know where i can find the info that i need (if you can decipher my ramblings)
Thanks very much
Fordy
#2
Posted 11 May 2011 - 02:13 PM
As for technical reasons for doing it, it reduces the front cross section by a huge amount and improves the drag performance of the body dramatically. There are numbers published somewhere, can't remember where just now though.
#3
Posted 11 May 2011 - 03:26 PM
you could look at...
Rigidity of a flat butted join versus a flanged, spot welded one - wouldn't be hard to knock up a few test pieces to pull 'n twist to the point of failure. The 3D section of a flanged joint suggests it's a foregone conclusion, but a flange can also be a lever.
A tensile strength comparison - pi x diameter means you can get a greater length of weld interface using spots along a panel joint than with a continuous seam.
Exposure of the seams to impact and folding in a collision.
#4
Posted 12 May 2011 - 07:07 PM
With regards to the pro' and con's for de seaming if done properly and lead filled to finish then it will look really good and should last. With flange's like previously mentioned there was no real consistency to how many spot welds were applied to them when joining and as to crash testing,well it does not take much to turn a standard mini into a much smaller parcel. Plus they seem to attract rust especially the later models.
Each to their own here really, if done well by a competent welder using some common sense then there is no real reason to think why a de seamed car would be weaker than a non de seamed vehicle.
The only way to test properly would be to use Euro NCAP testing of a standard built mini and a de seamed one to see what would happen. Will this happen, no but it would be interesting to see the results.
#5
Posted 12 May 2011 - 07:11 PM
#6
Posted 12 May 2011 - 08:37 PM
#7
Posted 13 May 2011 - 12:34 PM
hope that some use to you
#8
Posted 13 May 2011 - 04:28 PM
thank you so so much!
#9
Posted 13 May 2011 - 07:42 PM
Tape was applied to the gutters and seams at the front in the hope that drag might be reduced. And there was a very small reduction of 0.004 on the drag coefficient but also a small increase in positive lift. A similar, possibly greater effect might be expected from de-seaming a shell.
Source: http://www.carbonwee...sting_mini.html
#10
Posted 14 May 2011 - 11:23 AM
There is an article on the Carbon Weezel website where they took a hillclimb mini to wind tunnel, one of the results was for de-seaming:
Tape was applied to the gutters and seams at the front in the hope that drag might be reduced. And there was a very small reduction of 0.004 on the drag coefficient but also a small increase in positive lift. A similar, possibly greater effect might be expected from de-seaming a shell.
Source: http://www.carbonwee...sting_mini.html
Nice find!
1 user(s) are reading this topic
0 members, 1 guests, 0 anonymous users