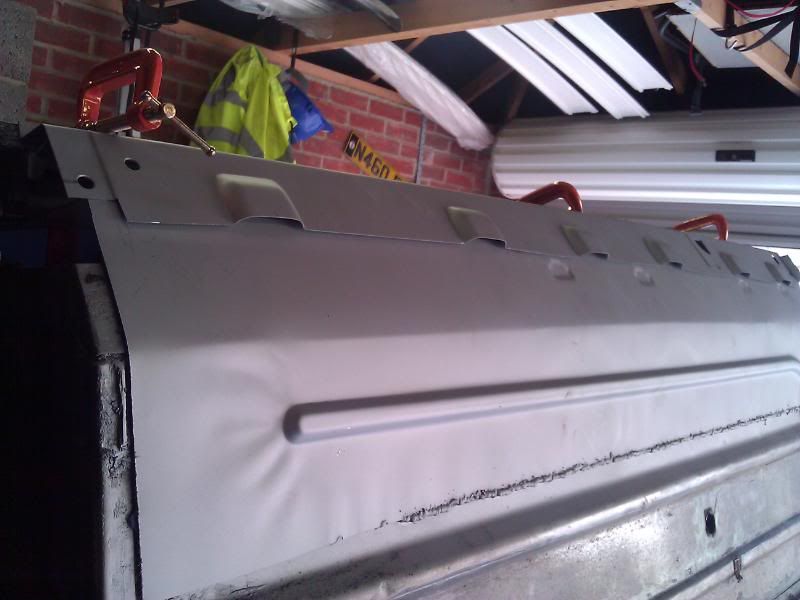
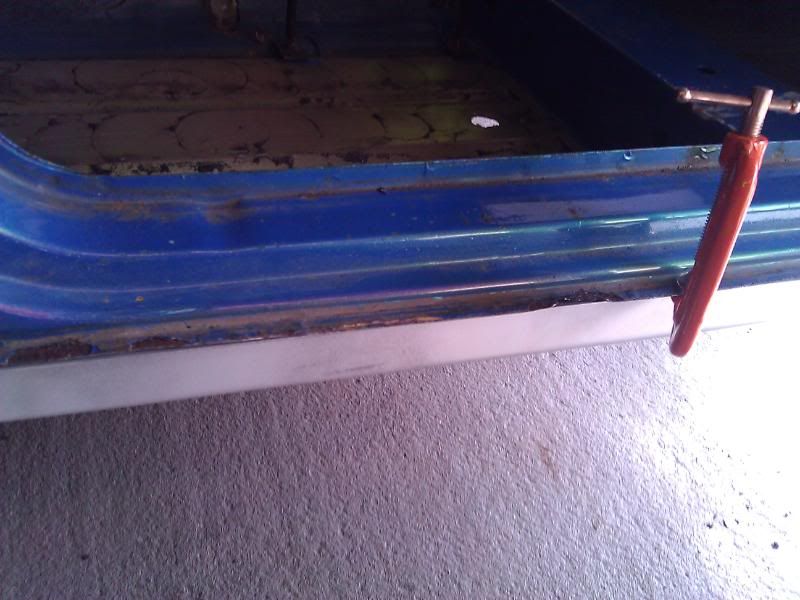
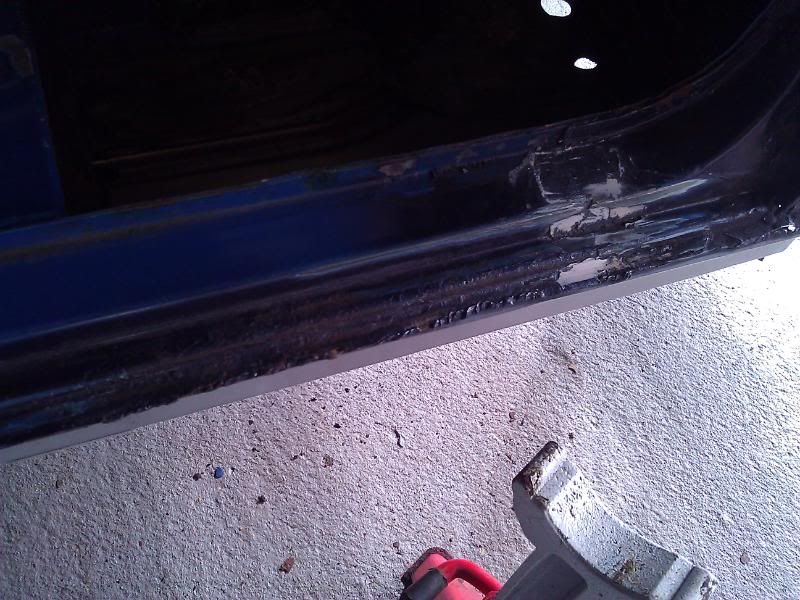
Can i grind this back to make it flat / neater - treat the rust, etch prime and then spot weld thinking of hiring one for the week (£80)
any help appreciated
Cheers Kev
Posted 25 September 2011 - 10:52 AM
Posted 25 September 2011 - 11:16 AM
Posted 25 September 2011 - 11:28 AM
Posted 25 September 2011 - 11:39 AM
Posted 25 September 2011 - 11:40 AM
Posted 25 September 2011 - 11:53 AM
Posted 25 September 2011 - 01:36 PM
Posted 25 September 2011 - 01:43 PM
i think atm i am worried about the quailty of the welding that has been done on the floor, dont look like alot of pentration in that weld so no strength
Posted 25 September 2011 - 06:33 PM
Posted 25 September 2011 - 06:47 PM
Posted 26 September 2011 - 04:09 PM
Posted 26 September 2011 - 05:44 PM
Posted 26 September 2011 - 05:51 PM
Posted 15 October 2011 - 05:50 PM
0 members, 1 guests, 0 anonymous users