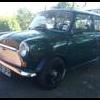
Thread Repair Kit For Head Studs.... Two Question's
#1
Posted 16 January 2012 - 09:08 PM
Will this be the correct thread for repairing head stud threads in the block ....
Also has any one succesfuly used this type of kit with out any problems.
#2
Posted 16 January 2012 - 09:11 PM
You need a pillar drill to drill the holes for tapping as it's vital the drill goes in vertically or the stud will end up at an angle.
#3
Posted 16 January 2012 - 09:14 PM
Absolutely ideal for the job.
You need a pillar drill to drill the holes for tapping as it's vital the drill goes in vertically or the stud will end up at an angle.
So you dont think it would be posible to do it on the car? as I dont realy want to be removing the block.
#4
Posted 16 January 2012 - 09:22 PM
Plug all the oil, water and push rod holes so that you can't get swarf down them. Then get someone to help and confirm when the drill is vertical. I used two pieces of aluminium extruded angle against the drill to try to keep it square and it did work as the stud was more-or-less vertical - still a bit of a bodge-job though.
Good luck with it.
#5
Posted 16 January 2012 - 09:33 PM
It is only one stud and it lasted when i tapped it a year ago when the stud pulled the thread from the block. last minute quick job evening before work in morning. I dident expect it to hold for as long as it has.
helicoil should last lonnger than a year if it lasted a year just tapped and ramed in then. Our drill has spirit levels on it so might help with square and levelness.
Thank you for your help 'uncle cooperman' sounds strange saying that haha.
Edited by me madjoe 90, 16 January 2012 - 09:34 PM.
#6
Posted 16 January 2012 - 09:35 PM
any hire shop will be able to rent you one cheap or something similar - even a bolt on drill base would work
the magnet is very strong on steel - so I can't see why it wouldn't work on a block
make sure you get the right voltage if you do rent one
ps a Mag drill with a rotabroach on steelwork is awesome - will even drill upside down without support (but with safety chain)
Edited by sledgehammer, 16 January 2012 - 09:39 PM.
#7
Posted 16 January 2012 - 09:42 PM
#8
Posted 16 January 2012 - 09:44 PM
#9
Posted 16 January 2012 - 09:50 PM
Mind if you use a drill with spirit levels that the engine is also perfectly level, or you might drill a vertical hole into a tilted engine...
verry good point ill go down the other route maby using a big engineers square or something symiler.
#10
Posted 16 January 2012 - 09:52 PM
#11
Posted 16 January 2012 - 09:55 PM
It may be worth considering using a Magdrill with a normal chuck (not the rotabroach)- http://magdrill.com -
any hire shop will be able to rent you one cheap or something similar - even a bolt on drill base would work
the magnet is very strong on steel - so I can't see why it wouldn't work on a block
make sure you get the right voltage if you do rent one
ps a Mag drill with a rotabroach on steelwork is awesome - will even drill upside down without support (but with safety chain)
looks good thanks for the idea may come in handy for future jobs at work. Although I think ill just drill it with a normal drill I have faith that it will be straight enougth... as i say dont want to become to much of an involved task. and its not muchof a high performance engine just an old fairly tired 998.
![=]](https://www.theminiforum.co.uk/forums/public/style_emoticons/default/sideways.gif)
#12
Posted 16 January 2012 - 10:02 PM
#13
Posted 16 January 2012 - 10:10 PM
Ive seen it done with a pillar drill bolted to the top of the block.
You mean like a bench top one I may have one of these some where...
#14
Posted 17 January 2012 - 09:43 PM
Leave the stand clamped, put the tap in the chuck, and rotate BY HAND till the tap is started properly. (Assuming the tap is capable of being mounted properly in a drill chuck). Then you can take the drill away and use a tap wrench to complete the job.
#15
Posted 17 January 2012 - 10:10 PM
If a Mag Drill is not an option, AND you have a friend with a pillar drill, have him/her make a drill guide for you. Give them the HeliCoil drill bit and ask them to drill a hole through a flat block of aluminum at least an inch thick. Press that aluminum block on top of the engine block when you drill for the HeliCoil. The aluminum block will last long enough for you to drill a handful of holes and it will keep the drill bit perpendicular to the top of the engine block. That is much easier than trying to rig up a perpendicular fixture using angle iron or wood.
1 user(s) are reading this topic
0 members, 1 guests, 0 anonymous users