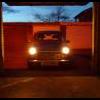
Ball Joint Shims
#1
Posted 24 March 2012 - 10:01 PM
Tried fitting my ball joints today, all was going well until i tried to shim them up. I used up all 6 shims in the kit and the ball pin was still tight and didn't want to move much. I estimate that im going to need at least 8 shims on there before i get anywhere near right.
Surley thats not right? Can anyone share some infomation on whay this might be happening.
Many thanks
#2
Posted 24 March 2012 - 10:05 PM
#3
Posted 24 March 2012 - 11:07 PM
#4
Posted 25 March 2012 - 09:26 AM
Just make sure that they move freely once shimmed. A thou of free play will not be noticeable once they are greased, but a thou too tight, and they will snap, sooner or later, possibly with disastrous results.
I have been in the habit of setting them up slightly looser than some people here suggest, but they always lasted at least 60,000 to 80,000 miles so I think I was doing something right.
For the very finest adjustment, once you are close with the shimming, to go tighter lap the face of the nut that goes against the shims, or to go looser, lap the back of the ball seat, either on a carpenter's oilstone or a sheet of abrasive on a flat surface. You can adjust to a small fraction of a thou that way, and it is very satisfying to be able to wiggle them through their full travel with your little finger while being unable to feel any play. It does not take all that long, as you are only doing a very fine adjustment.
#5
Posted 25 March 2012 - 11:59 PM
Most of the time you will get it close enough with the shims alone, but if the optimum setting happens to be midway between possible total shim thicknesses, a little bit of lapping to make the final adjustment works wonders.
#6
Posted 26 March 2012 - 04:38 PM
#7
Posted 27 March 2012 - 06:11 PM
#8
Posted 27 March 2012 - 06:35 PM
what is lapping? I'm confused?
#9
Posted 27 March 2012 - 07:28 PM
The first meaning is where some fine grinding paste is applied to both the small and large radii of the ball, and it is fitted loosely into the hub, the nut being nipped up very lightly by hand. The ball pin is then worked through all possible angles (you could possibly spin the pin with a cordless drill on very low speed, but you still need to work it through its extreme angles in every direction), keeping the nut nipped up very lightly, for a few minutes, until the mating faces fit properly to each other. Having well-fitting surfaces makes the joint work better and last longer. It never used to be needed, when they were made better. Obviously you must get rid of every last trace of grinding paste!
The second meaning was lapping the back (flat) face of the ball seat or the face of the nut, to adjust the clearance of the joint to finer accuracy than is possible by shims. Imagine that you could rub a shim down to half its thickness for final tweaking, and you will get the picture. You can't adjust the shim, because it is too delicate, so you adjust something else, I have used a carpenter's oilstone successfully, but you can also rub on a piece of abrasive paper, face up on a very flat surface such as a piece of plate glass.
The joints last very much longer if they are accurately shimmed, but always err on the slack side. Too tight, and the pin is likely to suffer fatigue fracture some time later, which may be catastrophic. Once assembled, with a trace of thin oil, if there is some minimal drag but you can wiggle through their full travel with fingers only, they are good. If they flop over under their own weight, but you can't feel any end float, they are also good. If you can wiggle them to any angle with the tip of your little finger, but they have just enough friction to stay put at any angle, they are perfect. When greased they will feel just slightly tighter. If there are some noticeably tight spots, but mostly loose, lap the ball some more and try again.
#10
Posted 27 March 2012 - 11:43 PM
He is saying that taking a tiny bit off the nut may allow finer tuning of the fit of the assembly than you can achieve with shims alone. He was not advocating "no shims" or sanding the nut away to nothing to re-use old parts.
#11
Posted 28 March 2012 - 07:51 AM
I don't know why he thought I was advocating lapping worn-out joints. When the ball becomes mis-shapen, they are scrap, because they will always bind drastically on full deflection. They need to be spherical, as you and I know.
You can't even skim them in a lathe, because you would go through the hardening, and they would have a very short life, and they would not match the radii of the seat and nut. When they are worn, they are only fit for recycling.
#12
Posted 28 March 2012 - 08:43 AM
#13
Posted 28 March 2012 - 06:40 PM
Fine adjustment of what, shims come in thin versions as well......... or maybe the cheap crap ones don't.
Personally I won't use anything but Quinton Hazell ball joints and they certainly have all the shims you need................
Must say I also love the bit where you stop the grease getting through as well...........
Thats funny because i have Quinton Hazell ball joints and they have nowhere near the amount of shims i require. I managed to do a bit of lapping yesterday it's looking better but not perfect. Still going to need more shims to make it work.
#14
Posted 28 March 2012 - 09:57 PM
The shims come in various thicknesses, and the thinnest is usually 2 thou. Some of us like to set out balljoints up rather closer than that.
I recommend that you read what others are writing more carefully before making comments which are not related to what was actually written.
#15
Posted 28 March 2012 - 11:39 PM
Where ball joints are concerned, there has been some extremely dangerous advice given in the past, which was very likely to result in fatigue fracture, which can result in people being killed. Do you actually know what fatigue fracture is, and why it would occur if the ball joint was incorrectly shimmed?
1 user(s) are reading this topic
0 members, 1 guests, 0 anonymous users