Hi
I've just embarked on a mammoth task of building a Z cars Type R. Basically bought a bare shell which is in need of a lot of work.
First query - Floors. I've bought 2 panels front to back from M-machine with inner and outer sills attached. What's the best method for fitting, lining these up? Is it possible to fit these with the door step still in place and do I still need to brace the car if the door step is in place? I have both MIG and TIG welder so was thinking plug weld along the outer seam with MIG but maybe TIG the butt joints for neatness inside. Any good tips on getting a good butt joint?
Second Query - Fibre glass fronts. I will be fitting a fibre glass front but was wondering if anyone has fitted one with built in A-panels? If so, what are they like? The current A-panels will be coming off so would rather replace with the rust free option if any good. I plan to fit a 2-piece front, with the wings etc being semi-permanently fixed in place, only allowing the bonnet to come off.
Thanks
Steve
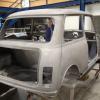
Bodywork - Floors, Sills And Fibre Glass Fronts!
Started by
ukharrisst
, May 10 2012 03:49 PM
1 reply to this topic
#1
Posted 10 May 2012 - 03:49 PM
#2
Posted 13 May 2012 - 03:23 PM
I would brace the car as you will be cutting out a large section of floor each time. Yes leave the door step in place if its ok. If its showing any sign of rot then have a good look inside as they tend to rot from the inside out and change the complete thing.
For butt welding the floors to the tunnel etc i would rough cut out the old floor and then trim to size until you a gap of approximately 1mm, enough to fit intergrips to keep it altogether. Personally i would stick with the MIG as i don't have any experience with TIG welding. Good penetration of the welds is paramount here as you well know.
You could leave the welds proud but for me flush is the way here as long as you are confident with the strength of the welds. Some folk joggle the joints and weld each side but that's a personal choice.
Plug welding the inner and outer sills to the door step is fine unless of course you have an access to a spot welder.
For butt welding the floors to the tunnel etc i would rough cut out the old floor and then trim to size until you a gap of approximately 1mm, enough to fit intergrips to keep it altogether. Personally i would stick with the MIG as i don't have any experience with TIG welding. Good penetration of the welds is paramount here as you well know.
You could leave the welds proud but for me flush is the way here as long as you are confident with the strength of the welds. Some folk joggle the joints and weld each side but that's a personal choice.
Plug welding the inner and outer sills to the door step is fine unless of course you have an access to a spot welder.
1 user(s) are reading this topic
0 members, 1 guests, 0 anonymous users