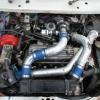
Making Panels. Eg. A Curved Piece With A Lip.
Started by
Austinminimark
, Jul 07 2012 09:59 PM
16 replies to this topic
#1
Posted 07 July 2012 - 09:59 PM
wondering if anyone can help me.
after months of frustration trying to learn to make panels.
for ages ive watched one of my friends make panels in a vice no matter how complicated with ease.
unfortuantly i dont see him anymore so i cant ask him to teach me.
wonder if any one knows of any good videos or books on making panels with hammer,dollies vice etc..???
its mainly making a curved piece with a 90 degree lip on one edge all the way round.
doesnt matter weather i do the lip first or last the metal always seems to starighten back out or the lip get too small or better yet get no where near before going to thin and me walking away swearing and chucking things.
im talking no cheating (cutting slits and welding back together, or in two peices)
one solid piece.
can any one help???
any photos or advice would be great. something ive tryed to learn for ages now and just cant quite grasp it.
after months of frustration trying to learn to make panels.
for ages ive watched one of my friends make panels in a vice no matter how complicated with ease.
unfortuantly i dont see him anymore so i cant ask him to teach me.
wonder if any one knows of any good videos or books on making panels with hammer,dollies vice etc..???
its mainly making a curved piece with a 90 degree lip on one edge all the way round.
doesnt matter weather i do the lip first or last the metal always seems to starighten back out or the lip get too small or better yet get no where near before going to thin and me walking away swearing and chucking things.
im talking no cheating (cutting slits and welding back together, or in two peices)
one solid piece.
can any one help???
any photos or advice would be great. something ive tryed to learn for ages now and just cant quite grasp it.
#3
Posted 07 July 2012 - 10:34 PM
Fold 90 degree bend. use a flat pien hammer and hammer flange, this should allow the part to curve away from the flange. Ie the flange on the outside of the curve.
For the other direction you open the vice a little and smack the flat pien into the metal over the gap between the vice jaws. This should create a little peak.
You then need to flatten this down using the flat face of a hammer.
Hope that helped?
For the other direction you open the vice a little and smack the flat pien into the metal over the gap between the vice jaws. This should create a little peak.
You then need to flatten this down using the flat face of a hammer.
Hope that helped?
#4
Posted 08 July 2012 - 08:15 AM
cheapest way is a shot bag and a couple of decent hammers and maybe folding pliers?
have a look on frost's web site.
have a look on frost's web site.
#5
Posted 08 July 2012 - 03:54 PM
I agree with Anon, A decent 'shot' bag and round faced rubber hammers for forming curves. A good strong vice with some pieces of cut off angle iron to pinch the steel between and form right angles, lips, flanges etc plus a set of panel beaters hammers and dollies is a must.
You can soften or aneal mild steel sheet by heating it to a dull red or even just beyond a blue colour, then allowing it to cool naturally.
This will allow you to form any nice curves easier but be aware that it will distort the metal, therefore better to do it before you make any final shapes or measured joints etc
You can soften or aneal mild steel sheet by heating it to a dull red or even just beyond a blue colour, then allowing it to cool naturally.
This will allow you to form any nice curves easier but be aware that it will distort the metal, therefore better to do it before you make any final shapes or measured joints etc
#6
Posted 08 July 2012 - 04:07 PM
You could make it out of two pieces. Cut your curved shape first that you are happy with then add the lip. Tack weld it in place then once happy pulse weld together then grind back flush.
#7
Posted 08 July 2012 - 09:52 PM
thanks guys
still not quite getting what im on about. ill add photos the retro rides link is close but not. just basically imagine a smooth curve the along the edge has a bent lip at 90 degrees but wen trying to add the lip it straightens and deforms, i know it can be done because ive watched someone make one he even did a u shap curve with 90 degree lips on both sides.
still not quite getting what im on about. ill add photos the retro rides link is close but not. just basically imagine a smooth curve the along the edge has a bent lip at 90 degrees but wen trying to add the lip it straightens and deforms, i know it can be done because ive watched someone make one he even did a u shap curve with 90 degree lips on both sides.
#9
Posted 09 July 2012 - 11:32 AM
You can buy a shrinker / stretcher tool like this to accomplish what you need
http://www.frost.co....combo-3258.html
http://www.frost.co....combo-3258.html
#10
Posted 09 July 2012 - 07:46 PM
thanks mr j thats was basically what i was trying to achieve but a little bit bigger thanks.
looked at stretcher shrinkers and english wheels but at the moment thats a bit too much for what I'm doing
looked at stretcher shrinkers and english wheels but at the moment thats a bit too much for what I'm doing
#11
Posted 10 July 2012 - 11:03 AM
might be an option using panel dollys, they are quite expensive though, i spent about £200 on dollys recently found the sykes pickavant ones to be very good! as for making panels im a real beginer, but i have seen many panel beaters using anvils to make panels in miniutes haha!
#12
Posted 10 July 2012 - 11:15 AM
Make a former out of a hard wood / tufnol etc then clamp your metal to this. Then use either a hide faced hammer / nylon to beat the sheet around the former. I use this method for forming aluminium to various shapes for repair sections on aircraft.
One thing you do need to remember you will thin the metal so be careful. Also constant hitting will age harden the metal. Not so critical with steel but very much so with aluminium.
One thing you do need to remember you will thin the metal so be careful. Also constant hitting will age harden the metal. Not so critical with steel but very much so with aluminium.
#13
Posted 11 July 2012 - 09:08 PM
okay thanks.
after research on stretchers/shrinkers i think they would be a good investment but at the moment id like to learn to make panels well by hand.
after research on stretchers/shrinkers i think they would be a good investment but at the moment id like to learn to make panels well by hand.
#14
Posted 11 July 2012 - 09:12 PM
I made a lot of the small intricate repair panels by hand on Project Erm. Some out of three or more pieces shaped and welded together to form the correct shape.
You cannot always get the shape you need by using hammers and dollies etc so you need to think outside the box so to speak and its amazing what you can make.
You cannot always get the shape you need by using hammers and dollies etc so you need to think outside the box so to speak and its amazing what you can make.
#15
Posted 12 July 2012 - 09:14 AM
just think of it this way... everything in this world has been made by someone, somehow with someform of skills etc... so you can do it mate just gota practise to achieve what you want
1 user(s) are reading this topic
0 members, 1 guests, 0 anonymous users