I'm using a Clarke 135te welder and hobby gas 5 (5%co2)
I'm prepping the panels and clamping them together with intergrips. The gap between is 1mm-ish. I tack them together as shown below
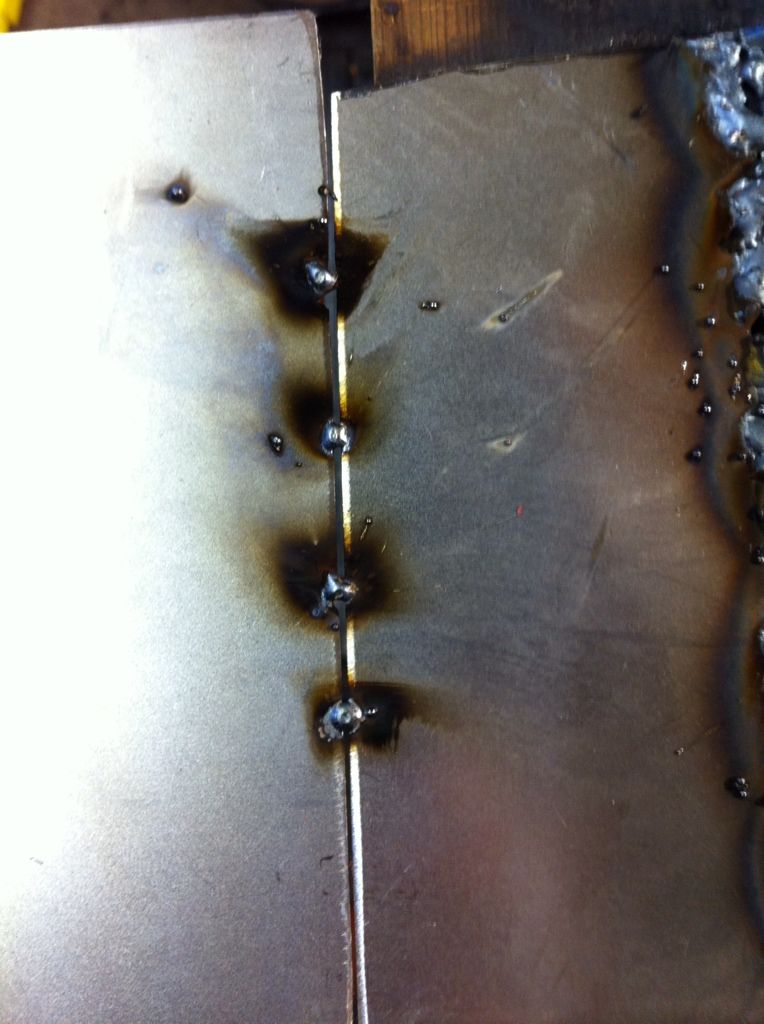
But regardless of my settings I just blow holes in the panels.
Below from left to right:
1 = position 2, min, wire speed 7
2 = position 2, min, speed 6
3 = position 1, min, speed 6
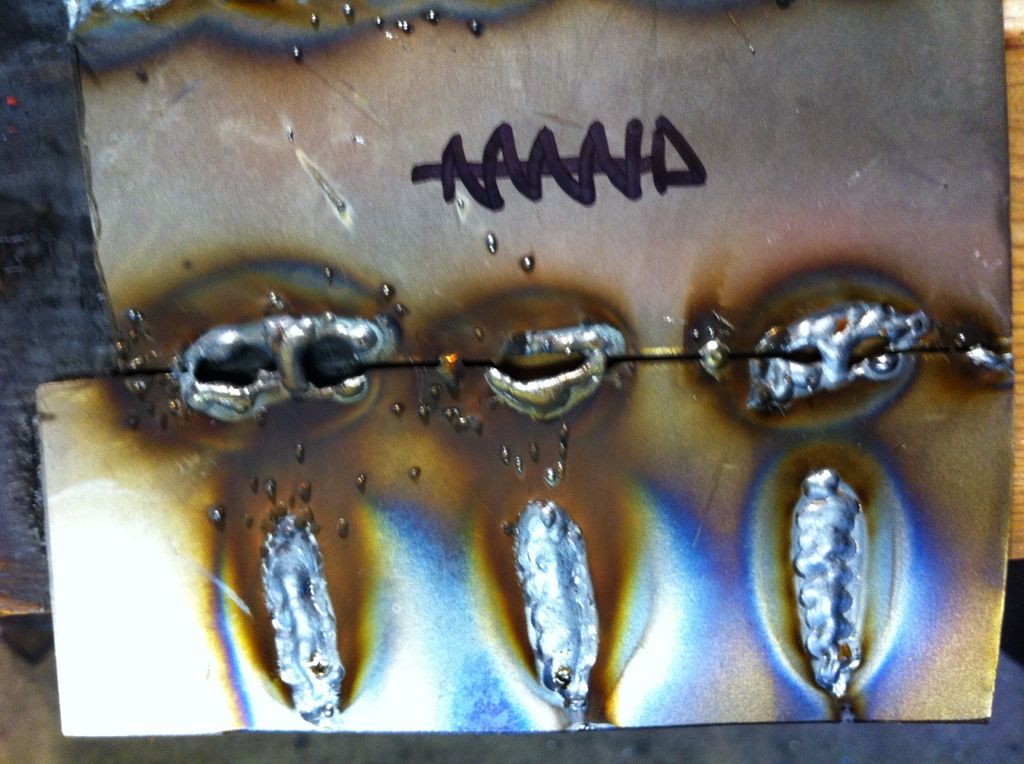
Im welding in the pattern shown, and below each butt weld is a run of each weld.
Penetration below (Top = 3 and bottom = 1):

Any ideas what I'm doing wrong?
Also what flow should I set my regulator to. ( does it matter? ) currently set as below
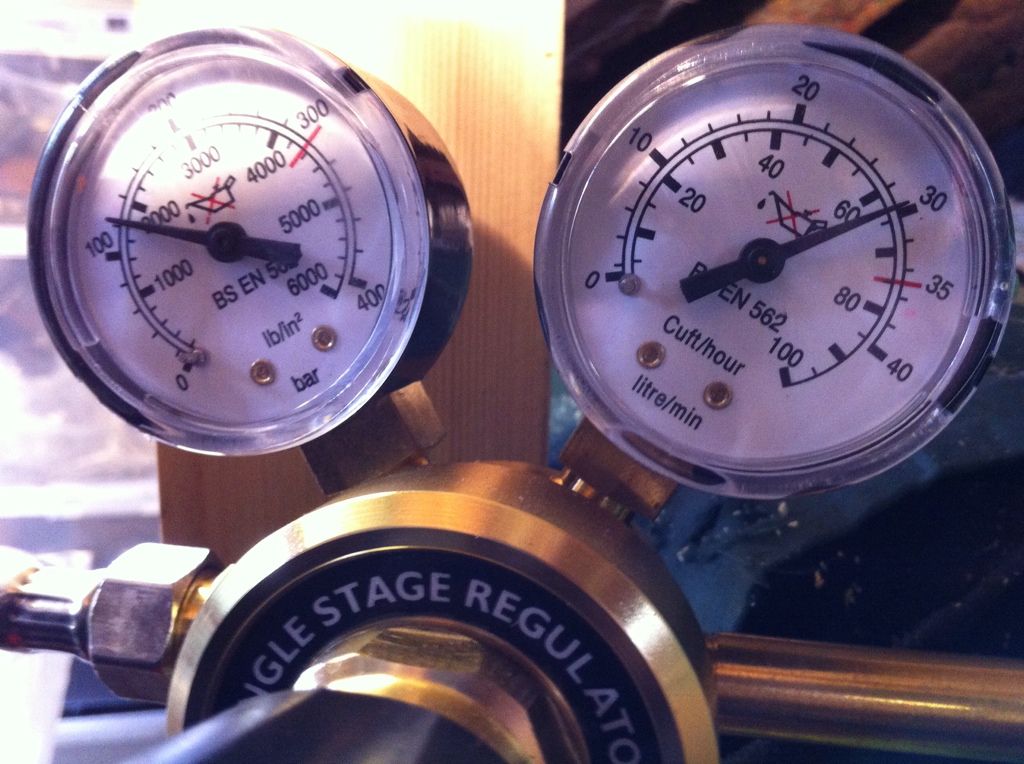
Thanks Chris