Hi, I'm a bit of a novice at welding and keep coming across the same problem, which is that it that I keep on blowing holes in the metal I'm welding... I've tried turning down the juice and the wire speed, which mostly works, except that I find that I'm not getting much penetration. One thing that I thought it might be is that when I weld, I aim at the point at which the two pieces of metal touch... Should I start on one side and work across to the other? Thanks!
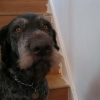
Keep On Blowing Holes When Welding, Any Suggestions?
#1
Posted 22 August 2013 - 04:56 PM
#2
Posted 22 August 2013 - 05:00 PM
#3
Posted 22 August 2013 - 05:06 PM
Are you welding with a gas or gasless welder?
Sorry if I'm teaching you to suck eggs, but hold the gun with both hands, pulse weld, move a few inches down the seam, pulse weld move a few inches, then when you get to the end go and weld next to your first weld. This will allow the panel to cool.
Welding is one of those things where practice makes perfect!
#4
Posted 22 August 2013 - 05:43 PM
Welding is one of those things where practice makes perfect!
I second that!
I was a panel beater for years and did all kinds of welding day in, day out in my time in the profession. After I left I didn't touch a welder for 4 years and although I remembered how to do it, I still had to put in a lot of practice to get back into the swing of it. People can give you hints and tips but it really comes down to your own style in the end. As long as you get plenty of penetration and a good strong weld then that's all you need to worry about.
You will find as you go on that your welds will get neater and cleaner which not only looks better, it saves ALOT of grinding and dressing not to mention £££ on grinding discs etc.
Good luck
Ben
#5
Posted 22 August 2013 - 05:44 PM
Yeah I suppose the key is just to make sure the metal has cooled, a basic principle but one that is important to remember! And as you say, it just comes down to practice... Thanks!
#6
Posted 22 August 2013 - 09:36 PM
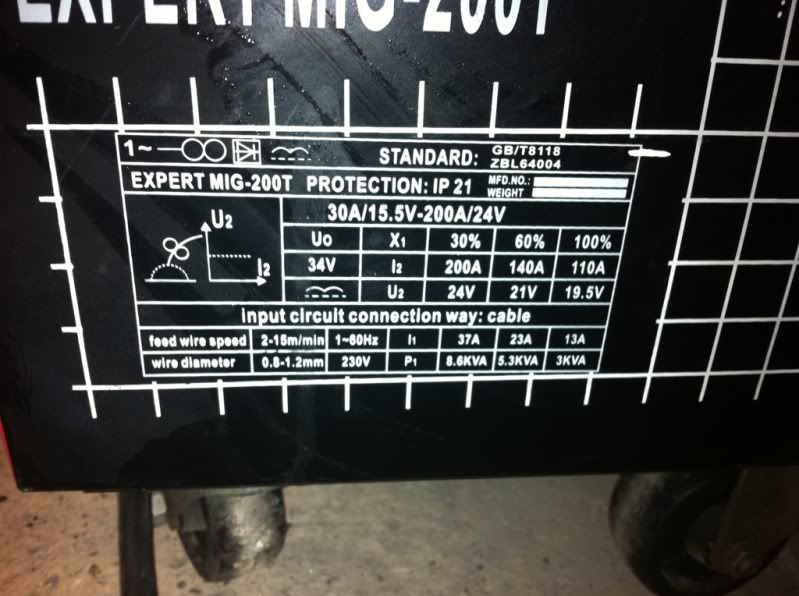
#7
Posted 22 August 2013 - 10:03 PM
Hi
I was having the same problems as you - being fairly new to mig welding myself. I thought I had the power up too high and so I did hte same as you - I reduced the power and the wire feed speed. That allowed me to make a weld and keep working a location until I could get enough heat in to it to guarantee good penetration. The problem with that is that it can still blow holes as the metal turns to a molten pool and, unsurprisingly, runs out of the hole.It also means you get a messy weld and waste a lot of time and money dressing the weld and re-doing it. I was also trying to do a section then move on a few inches and weld and then go back and fill in the gaps. That does work I believe, and is ok when the metal is very thin but I found I couldnt get it looking tidy.
I got some great help from NordicMini on this site. He lives not too far away from me and he showed me another way to do it.
I turn the power up, turn the wire feed speed up and pulse. The duration of the pulse is something you have to get right is linked to the thickness of the metal. The point is to have the power up high enough that you can get the metal hot, quickly, and have the wire feed speed up high so that it gets metal in to there quickly at the same time. I now pulse in short bursts right next to each other, moving a few millimetres at a time and I've found that I can produce very tidy welds with excellent penetration, and that need almost no dressing or going over.
As with all other posts here though, get some metal of the thickness you are looking to weld and practice, practice, practice.
Try it this way and see how you get on.
Oh - one more very significant thing that I did was switch from gas-less to gas (95% carbon dioxide, 5% argon). Have the gas 'speed' high enough that the weld is a good, gray colour and not black and you will have far less spatter.
Good luck,
Rod
RodAndTom
#8
Posted 22 August 2013 - 10:34 PM
I've tried turning down the juice and the wire speed
When you turn down the juice, leave the wire where it is. Or turn up the wire speed and leave the juice where it is
Small adjustments can make it easier to weld the thin stuff. Don't go from side to side, there is no need, it's concentrates the heat in a very small area, the trick is to either pulse or to move the torch quickly, both ways help to prevent to much heat build up in the same area
Plenty of practice before you get going on the mini
Cheers
David
#9
Posted 23 August 2013 - 12:31 PM
Some good advice there, thanks David!
#10
Posted 23 August 2013 - 01:19 PM
I'm fairly new to welding myself and had the same issues as you
What made the difference for me was switching to 0.6 wire and an argon gas mix you get much better welds
Also I second the pulse weld method that's what I've been using on my mini it's ideal for thin panels .
You can crank up the power and wire on thicker stuff like the heel board and get a good seam but as most folk say on here it's all about practicing
Good luck
#11
Posted 24 August 2013 - 11:07 PM
You can also use a copper (NOT any other metal, especially ali!) backing bar, preferably with a small groove to allow a bead to form on the reverse side. Ideal for beginners, and has been said, the correct gas helps enormously.
Actually, the backing bar is very good, even in the hands of an experienced welder, for long butt joints such as when replacing half floor pans, as it allows a longer continuous run of weld. You could do maybe 2 inches and leave a 4 inch gap, repeat all the way to the end, then go over it again, doing the next 2 inches of each section, etc, to minimise distortion.
1 user(s) are reading this topic
0 members, 1 guests, 0 anonymous users