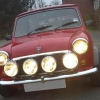
Top & Bottom Engine Stabiliser Bushes. Poly Or Rubber?
#1
Posted 18 March 2014 - 06:36 PM
For some reason i bought the rubber ones with the metal insert for the top and the poly ones for the bottom.
Would this be ok or should i go either all rubber or all poly? If so which are best?
#2
Posted 18 March 2014 - 07:25 PM
no as the bottom uses a bigger bolt http://www.minispare...s.aspx?2~12~119
you need part 19 for lower arm
#3
Posted 18 March 2014 - 07:59 PM
#4
Posted 18 March 2014 - 09:19 PM
no as the bottom uses a bigger bolt http://www.minispare...s.aspx?2~12~119
you need part 19 for lower arm
Thanks, so your saying the metal tube going through the rubber bush needs to be replaced with this? Which end is it or is it both?
#5
Posted 18 March 2014 - 11:15 PM
yes as the bottom bolt is bigger........yes both
Edited by mk1leg, 18 March 2014 - 11:15 PM.
#6
Posted 19 March 2014 - 09:32 AM
#7
Posted 19 March 2014 - 12:09 PM
I think that is incorrect, as other suppliers show, and I have used, exactly the same bushes for top and bottom. The bottom bushes do not use a sleeve, at least not on the two Minis I had with that arrangement, but rather a 3/8" UNF bolt running directly in the bushes. The top steady uses, as I think we are agreed, 5/16" UNF bolts, with a sleeve, which if you measure it will probably turn out to be 3/8" OD.
I do believe that the confusion is caused by the fact that the majority of aftermarket bushes are supplied for the top steady, which EVERY Mini has (except for a few non-standard configurations), and which the average Mini owner is able to change. Only later ones had the lower steady, and most people are unaware of it, and if it fails remain blissfully ignorant of it, thinking that the problems that it causes are elsewhere. (On this forum, I suspect that virtually everyone knows better, we do look under our cars! We do some very advanced repairs and maintenance too, stuff that probably no Rover dealer ever tackled.) Anyway, the relevance of that is that aftermarket bush kits (formerly stocked by Halfords and every car accessory shop) used to be, and I think still are, supplied with conical inserts, often of plated steel, but sometimes hard nylon, to expand the bush tightly in the eye of the steady bar to make it stiffer. That is amateurish design, a result of failing to understand the true nature of the problems that used to arise, which were not fixed by stiffening the top steady, but by adding the bottom steady, as close as possible to directly below it, to react the torque correctly. The other amateurish designs of steady, including one which purports to be "ultimate", from a company whose products are all very amateurish, fail to react the torque in the right place, and as such are a waste of money, as they move the problems about without fixing them. (There are configurations of extra steadies which will work well, of course, and you could probably even make them at home.) Alternatively to the bottom steady, it would have been possible to increase the fore and aft stiffness of the main engine mounts, at the expense of noise and vibration, as their degree of compliance was the cause of the problem, not softness of the top steady bushes, but I would not expect the cowboys who design many aftermarket parts to understand that. The rear-facing pair of lower steadies in the BL era was an attempt to restrain fore and aft movement on the main mounts, unfortunately only partially successful, and was soon replaced by the single lower steady, right below the upper steady. Two less bushes, less metalwork and bolts, so less cost, and it worked a lot better.
Anyway, rant over, and it may now be apparent that you really do need, and are right to think about improving, your upper and lower steadies. However you do not necessarily need an extreme degree of stiffness when you have functional top AND bottom steadies. OK, for racing, you may, in certain circumstances, want not solid (things WILL break) but rose jointed steadies, with no compliance whatsoever, but for road use a small amount of stiffening as compared to standard is all that will be needed. To that end, and because some poly bushes are known to fail due to engine heat, I would suggest that you get one poly and one rubber bush kit, fit two of the polys at the body end of the top steady, and the other two at the subframe end of the bottom steady, then the rubbers go at the engine end of the top steady and gearbox end of the bottom steady.
For racing, you would ideally use a "kinematic" mounting arrangement, where one lower steady is a big rose bearing which can slide slightly on its shaft (to make up for changes in subframe and/or engine width), and the other is a plain rose bearing, both mounted to stub shafts roughly parallel to the crankshaft axis, and the top and only steady simply double rose jointed. I think that is the minimal configuration where all forces can be reacted without any conflict due to dimensional changes. On a road car, the noise and vibration would be unacceptable, and I have no idea what it might do to the fatigue life (normally infinite) of the subframe and shell. Maybe someone had done that on a race car, if so I would be intrigued to know if it actually gave any significant advantage. Maybe the extra noise, as the whole car shook, shuddered and vibrated, scared off the competition? But it is a valid mounting technique in certain situations, where thermal expansion or dimensional tolerances in one item must not feed unnecessary stress into another.
On the road, the resilience of one pair of rubbers in each steady will make the car more pleasant to drive, and may reduce the incidence of fractured bottom steady brackets.
#8
Posted 19 March 2014 - 01:53 PM
Anyway, rant over, and it may now be apparent that you really do need, and are right to think about improving, your upper and lower steadies. However you do not necessarily need an extreme degree of stiffness when you have functional top AND bottom steadies. OK, for racing, you may, in certain circumstances, want not solid (things WILL break) but rose jointed steadies, with no compliance whatsoever, but for road use a small amount of stiffening as compared to standard is all that will be needed. To that end, and because some poly bushes are known to fail due to engine heat, I would suggest that you get one poly and one rubber bush kit, fit two of the polys at the body end of the top steady, and the other two at the subframe end of the bottom steady, then the rubbers go at the engine end of the top steady and gearbox end of the bottom steady.
Superb idea, that is exactly what I'll do thanks.
#9
Posted 20 March 2014 - 01:14 PM
I think if you search back through the forum, you may, if you can find anything at all, find that it was not originally my idea, although I may have added to it in some small way. I can't remember who originally thought of it. But that is the point of public forums, you give out an idea and people run with it. Benefits everyone, which is why we are here. If the originator of the idea sees this, please come forward and claim your well-deserved recognition. That is never begrudged.
In an entirely different philosophy, everyone with ideas keeps them to themselves (yelping and whining about "intellectual property", which is not a term that the law actually recognises) and those who will pay an exorbitant fee for them. Now why does that remind me of Bill Gates? Sad that he could never take such a hard line against bugs in his software.....
#10
Posted 23 March 2014 - 08:20 PM
#11
Posted 24 March 2014 - 11:18 AM
The same as any other 5/16" UNF bolt, which unless otherwise stated is 18 lb ft.
1 user(s) are reading this topic
0 members, 1 guests, 0 anonymous users