Looking good!
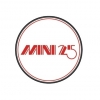
Three Classics. One Passion.
#121
Posted 22 August 2015 - 04:39 PM
#122
Posted 22 August 2015 - 06:53 PM
Thanks Ben.
#123
Posted 22 August 2015 - 08:07 PM
Great project :)
#124
Posted 22 August 2015 - 08:42 PM
#125
Posted 24 August 2015 - 09:06 PM
#126
Posted 25 August 2015 - 03:50 PM
Thanks Tom. The one clamped up in the photos was from Bingley Hall Show last year and the other side was from M Machine (both heritage).
Once I'd got it all clamped up it seemed ok, but I've got to fit the other side inner wing first, then I'll clamp and mock the whole front end up to make sure its all in line.
Gonna have a read through your Build thread now
#127
Posted 25 August 2015 - 09:20 PM
#128
Posted 26 August 2015 - 09:21 AM
Hey, good stuff. Just wondering with Felix about the floor repairs. Are you overlapping the panel or butt welding? I'm doing the same thing and I have the same welder. I'm using 0.6 and gas and still get blow through, even set on 1 and min. Any ideas? Thanks in advance.
#129
Posted 26 August 2015 - 01:48 PM
I'm using 0.6 and gas and still get blow through, even set on 1 and min. Any ideas? Thanks in advance.
There are lots of reasons for blow through
Technique - Moving too slowly across work piece and trying to do a continuous weld are the most common. Try pulse welding..
Wire speed too high or low
Bad earth
Join gap to large
Obviously power too high is another but you said you have it on minimum
#130
Posted 27 August 2015 - 08:56 AM
I'm using 0.6 and gas and still get blow through, even set on 1 and min. Any ideas? Thanks in advance.
There are lots of reasons for blow through
Technique - Moving too slowly across work piece and trying to do a continuous weld are the most common. Try pulse welding..
Wire speed too high or low
Bad earth
Join gap to large
Obviously power too high is another but you said you have it on minimum
Thanks for that. Just sorted it.
#131
Posted 27 August 2015 - 10:22 AM
I'm using 0.6 and gas and still get blow through, even set on 1 and min. Any ideas? Thanks in advance.
There are lots of reasons for blow through
Technique - Moving too slowly across work piece and trying to do a continuous weld are the most common. Try pulse welding..
Wire speed too high or low
Bad earth
Join gap to large
Obviously power too high is another but you said you have it on minimum
Thanks for that. Just sorted it.
which was it?
#132
Posted 29 August 2015 - 06:46 AM
I'm using 0.6 and gas and still get blow through, even set on 1 and min. Any ideas? Thanks in advance.
There are lots of reasons for blow through
Technique - Moving too slowly across work piece and trying to do a continuous weld are the most common. Try pulse welding..
Wire speed too high or low
Bad earth
Join gap to large
Obviously power too high is another but you said you have it on minimum
Thanks for that. Just sorted it.
which was it?
I went for pulse welding. Thanks
#133
Posted 29 August 2015 - 07:23 AM
#134
Posted 05 September 2015 - 03:49 PM
Hey, good stuff. Just wondering with Felix about the floor repairs. Are you overlapping the panel or butt welding? I'm doing the same thing and I have the same welder. I'm using 0.6 and gas and still get blow through, even set on 1 and min. Any ideas? Thanks in advance.
I'll be butt welding them in.
#135
Posted 05 September 2015 - 03:55 PM
You're doing a fantastic job, paint work especially. Just an idea re welding with interior etc in. Use old woolen blanks to cover seats etc. Sparks don't normally go through due to its fire retarding qualities.
Thanks mate. I have a 3m x 3m fabric welding sheet I use over the interior for use while hot working so its all good.
2 user(s) are reading this topic
0 members, 2 guests, 0 anonymous users