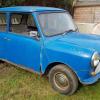
Dummy Engine Build Question
#1
Posted 02 June 2015 - 06:44 PM
#2
Posted 02 June 2015 - 07:19 PM
yes you should, then check the end float, if the end float is too much order yourself some thicker thrust bearings so it is right for when it comes to go together:)
#3
Posted 02 June 2015 - 07:25 PM
#4
Posted 02 June 2015 - 07:27 PM
1st trial build is normally done with crank main bearings, thrust bearings, rods & pistons, but with the piston rings removed so that the ring gaps can be individually measured and so that there is no piston ring 'drag' on the bores thus enabling smooth rotation of crank with rods assembled to be confirmed.
The main bearing bolts (nuts for Cooper 'S') and the big end nuts should be torqued to 75% of final figure.
Measure end float and set to 0.002" to 0.004" by using thicker thrusts if necessary. Measure how far down the bores the piston tops are when at TDC and have the block 'decked' to bring them to within 0.002" +/- 0.002" of the block deck level. Note that with a 1275, for each 0.010" the piston tops are down the bore at TDC, the combustion volume increases by 1 cc.
#5
Posted 02 June 2015 - 07:29 PM
Cheers. I have just done it and there is very little end float if any at all but all still turns lovely. Is this ok?
have you tested it with a dial test indicator? this would be a good thing to have if you don't have one as is very useful when setting cam timing:) you should have about 3-4 thou of end float ideally
and again a dti would be a very good engine building tool for you to get, they don't cost to much and placed like tool station sell them
Edited by kyle9832, 02 June 2015 - 07:30 PM.
#6
Posted 02 June 2015 - 07:45 PM
#7
Posted 02 June 2015 - 08:08 PM
When building an engine a DTI is indispensable. It is hard to measure end float of crankshaft or primary gear or to establish TDC and angle of max valve opening when doing the accurate cam timing without one.
On ebay for £14 with gauge and magnetic base.
#8
Posted 03 June 2015 - 12:14 PM
When building an engine a DTI is indispensable. It is hard to measure end float of crankshaft or primary gear or to establish TDC and angle of max valve opening when doing the accurate cam timing without one.
On ebay for £14 with gauge and magnetic base.
i have just ordered one up
i did notice on one of the new big end bearings, the oil hole is slightly out of alignment to the hole on the block. is this normal?
#9
Posted 03 June 2015 - 12:16 PM
When building an engine a DTI is indispensable. It is hard to measure end float of crankshaft or primary gear or to establish TDC and angle of max valve opening when doing the accurate cam timing without one.
On ebay for £14 with gauge and magnetic base.
i have just ordered one up
i did notice on one of the new big end bearings, the oil hole is slightly out of alignment to the hole on the block. is this normal?
Wait for someone who knows what they're talking about to come along and confirm, but this sounds so wrong
#10
Posted 03 June 2015 - 12:18 PM
Check refitting and swapping around the bearings at first. Once you're sure theres a misalignement, best practice would be modifying the oil feed in the block. This will mean you have to wash the block again.
#11
Posted 03 June 2015 - 07:37 PM
I'm a bit confused. A big-end oil feed hole cannot be out of line with the block as it fits on the crankshaft.
I have seen main bearing shells where the oil feed hole does not quite line up. It doesn't ever seem to be an issue although the hole can be made to line up if it seems a long way off. Just file it out a bit with a small draw file. Make sure no DGS gets into the engine.
#12
Posted 03 June 2015 - 08:50 PM
i did notice on one of the new big end bearings, the oil hole is slightly out of alignment to the hole on the block. is this normal?
Often they are, but best to correct them.
Be very careful when doing it. It maybe tempting to grab the die grinder to do this job, however I would strong suggest correcting it with a file. Die grinders are great tools especially for rapid material removal, however, it is very easy to slip when doing something of a delicate nature and end up in a real pickle. The Bearings shells need every bit of support they can get, so you really don't want to mar the tunnels in any way.
#13
Posted 03 June 2015 - 09:38 PM
Sorry I might be saying the wrong thing. It's the main bearings that fit the crank on the block. The bearing oil hole is not central to the hole in the block. It looks like the hole in the bearing should be about 2mm over. I will post up a picture for you to see. There is still a decent hole but should all of the hole be visible?I'm a bit confused. A big-end oil feed hole cannot be out of line with the block as it fits on the crankshaft.
I have seen main bearing shells where the oil feed hole does not quite line up. It doesn't ever seem to be an issue although the hole can be made to line up if it seems a long way off. Just file it out a bit with a small draw file. Make sure no DGS gets into the engine.
#14
Posted 03 June 2015 - 09:50 PM
Daft question time; can you measure endfloat with no thrust washers installed then work out the correct ones to order, or fit old ones which have been measured for thickness then measure endfloat and workout what is required from that? To me it seems like a pain to order new ones then find out they might not be the correct ones once fitted
#15
Posted 03 June 2015 - 09:56 PM
Daft question time; can you measure endfloat with no thrust washers installed then work out the correct ones to order, or fit old ones which have been measured for thickness then measure endfloat and workout what is required from that? To me it seems like a pain to order new ones then find out they might not be the correct ones once fitted
Not advisable. It is best to fit a set and then measure, swap out if need be. In a pinch you can use the old ones, just fit one half on each side that originally came from the non-thrust side, though this is not the best way to do it.
1 user(s) are reading this topic
0 members, 1 guests, 0 anonymous users