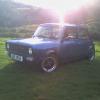
Best place to wire in......
#1
Posted 26 July 2006 - 08:02 AM
anyone recommend where to plum these into thats both safe and nice n tidy wiring, dont wana splice the loom as much as i can help it!
#2
Posted 26 July 2006 - 09:03 AM
If you want a feed for the illumination you will have to splice from the lighting loom. It depends on the placement of the rev counter but you can either come off the back of the lights switch. Test the connections on the back of the switch with a voltage tester to see which one goes live when you switch on the sidelights. If you are placing it near to your existing clocks then you can tap off the back of the dashboard. IMO it would be best to come off the back of the switch as it cleaner. Using solder and heatshrink looks a lot nicer than using the blue scotch blocks (I think that what they are called!) that basically cut through the insulation on a wire to achieve a connection. If you really want to make it look stock then buying a suitable male and female connector from RS, maplins or your local electrical shop incoporating all the connections for the rev counter, and wiring this in will mean that you can remove the rev counter all togeather at a later stage if you so wish!! Hope this helps.
#3
Posted 26 July 2006 - 09:03 AM
If you want a feed for the illumination you will have to splice from the lighting loom. It depends on the placement of the rev counter but you can either come off the back of the lights switch. Test the connections on the back of the switch with a voltage tester to see which one goes live when you switch on the sidelights. If you are placing it near to your existing clocks then you can tap off the back of the dashboard. IMO it would be best to come off the back of the switch as it cleaner. Using solder and heatshrink looks a lot nicer than using the blue scotch blocks (I think that what they are called!) that basically cut through the insulation on a wire to achieve a connection. If you really want to make it look stock then buying a suitable male and female connector from RS, maplins or your local electrical shop incoporating all the connections for the rev counter, and wiring this in will mean that you can remove the rev counter all togeather at a later stage if you so wish!! Hope this helps.
#4
Posted 26 July 2006 - 09:17 AM
A couple of options really depending on what you want to achieve:
1. If you are mounting the revcounter in a dash then you can splice into the loom coming from the back of you headlight switch. Test the wires on the back to see which one comes live when you turn on the sidelights and splice into this wire. You can do this using an item called a scotch block (the blue one from halfords etc). This IMO are bloody awful bits of kit as they simply cut through the insulation on a wire to achieve a connection. If i were doing it i would cut and soldera connection into the wire and then use heatshrink to tidy it up. You can also use crimps to achieve the same end result.
2. To make it even better i would get myself a male and female connector block from maplins/RS and wire the whole unit through this, so you can later remove the whole unit if you need to (saves cutting wires when you come to change/remove your dash etc.
There are many ways to do it and it is down to personal preference!!!
Hope this helps.
by the way the two wires are as you said, one for earth and one for the positive supply. Depending on what type of illumination is inside of your clock depends on which is which.... If it is a bulb inside then it won't matter as you can connect a bulb either way round. If it a LED then one will be pos one earth/neg. Best to research manual to check, if you have one, otherwise, google normally provides good search results for manuals etc
Hope this helps!
WOW THREE POSTS.
I'LL PUT THAT DOWN TO A ******* INTERNET CONNECTION AT WORK!!!
D'OH

How do you delete these things <runs for manual>
Edited by Gizzum, 26 July 2006 - 09:21 AM.
#5
Posted 26 July 2006 - 09:24 AM
#6
Posted 26 July 2006 - 12:27 PM
#7
Posted 26 July 2006 - 01:31 PM
Best way to wire this in is to piggy back off the red/green wire feeding the illumination to the other gauges. The feed out of the headlight switch (red wire) is unfused.
Soldering joints on a car isn't the best idea, the solder makes the connections brittle, and prone to failure, use decent crimp connectors!
#8
Posted 26 July 2006 - 02:45 PM
looks like im using two scotch locks!
#9
Posted 26 July 2006 - 06:45 PM
Two different ways, no splicing. Or you can find any sidelight bullet connector and use a new multi bullet to join the existing wires together and take your new tapping from it. Three ways, no splicing.
#10
Posted 27 July 2006 - 08:02 AM
#11
Posted 28 July 2006 - 07:06 AM
It now seems that splicing is a bad idea!!! Why? If you are going to do a permanent fit to the ccar then surely, wiring in a new line or doing a splice from an existing feed is slightly better than using crimps. I have a ratchet crimper and have a couple of times had a dodgy one. By soldering and tidying up with heatshrink you are guarenteed a 99% connection (dry joints excepted!) Plus it just looks so much tidier! So come on give me a reason for no splicing! I can except ceejams explaination that it will make the joint brittle. But we are not going to be hanging off these wires. Plus a crimp joint will come apart easier than a soldered joint the last time I checked....
Confused
Head Hurts
Help

#12
Posted 28 July 2006 - 09:43 AM
By soldering and tidying up with heatshrink you are guarenteed a 99% connection (dry joints excepted!) Plus it just looks so much tidier! So come on give me a reason for no splicing! I can except ceejams explaination that it will make the joint brittle. But we are not going to be hanging off these wires. Plus a crimp joint will come apart easier than a soldered joint the last time I checked....
As I said above, the solder makes flexible wires into solid ones, and we all know how much a car (especially a Mini) vibrates along the road. You may not be hanging off the wires, but those vibrations cause solder joints to fail, where (properly done) crimp joints do not, the cable is still flexible, and if the correct sized wire/cimp/tool are used the the cable should not pull out. I've seen some REALLY badly doen crimps (with needle nose pliers or similar) and granted these DO fall apart

Piggy back spade connectors are quite useful, just beware that there's normally an uninsulated section.
Not wanting an argument, but having done a degre in E&E engineering, and now working in the ESI I've come to my own conclusions about this one

#13
Posted 28 July 2006 - 01:45 PM

#14
Posted 28 July 2006 - 07:01 PM
Just the opinion of an ex-solderer.
(Yes, it was a C**p job.)

#15
Posted 03 August 2006 - 08:22 AM
I know minis vibrate but come on, enough to make a soldered joint fail!!! behave. I have been a royal naval engineer for the last ten years and i have never seen a soldered joint fail due to vibrations, and, believe me when i say that a type 42 destroyer vibrates a little bit more than a mini, epecially when the big gun on the pointy end goes bang!!!! Also, last time i checked, i didn't find to many flexible crimps!!! I think this is down to personal preference. I will go with soldering everytime, for a permanent addition. don't get me wrong there are a lot of crimps in my mini, but only used when connecting to original spade connectors, like coil and fuse box connections, and earths. But to get a clean look to a loom with out hundreds of piggyback connectors and scotch blocks it has to be solder!
2 user(s) are reading this topic
0 members, 2 guests, 0 anonymous users