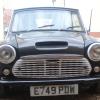
Help Needed - Snapped Engine Steady Bolt...
#1
Posted 12 April 2016 - 04:35 PM
The way I see it the only option I have is to drill it out, having never done this before and being in an awkward position I don't feel confident doing this.
Is there anyone near Diss in Norfolk who would come and do this for beer tokens?
As an alternative could I fit the engine steady that fits to the thermostat housing? Would this one by itself be enough?
Thanks in advance,
Steve.
#2
Posted 12 April 2016 - 04:39 PM
http://www.minispare...|Back to search
#3
Posted 12 April 2016 - 04:51 PM
I am very tempted to buy some easy out extractor things as I would like to do the job properly, but I know that the stud had gone through to the water jacket, so if I bugger the thread up I will be even more stuck!
Presumably the bracket in your link bolts to the two bolts in the middle of the picture below?
What sort of bolt is used to hold the engine steady to the bracket in the link?
Thanks for the quick reply!
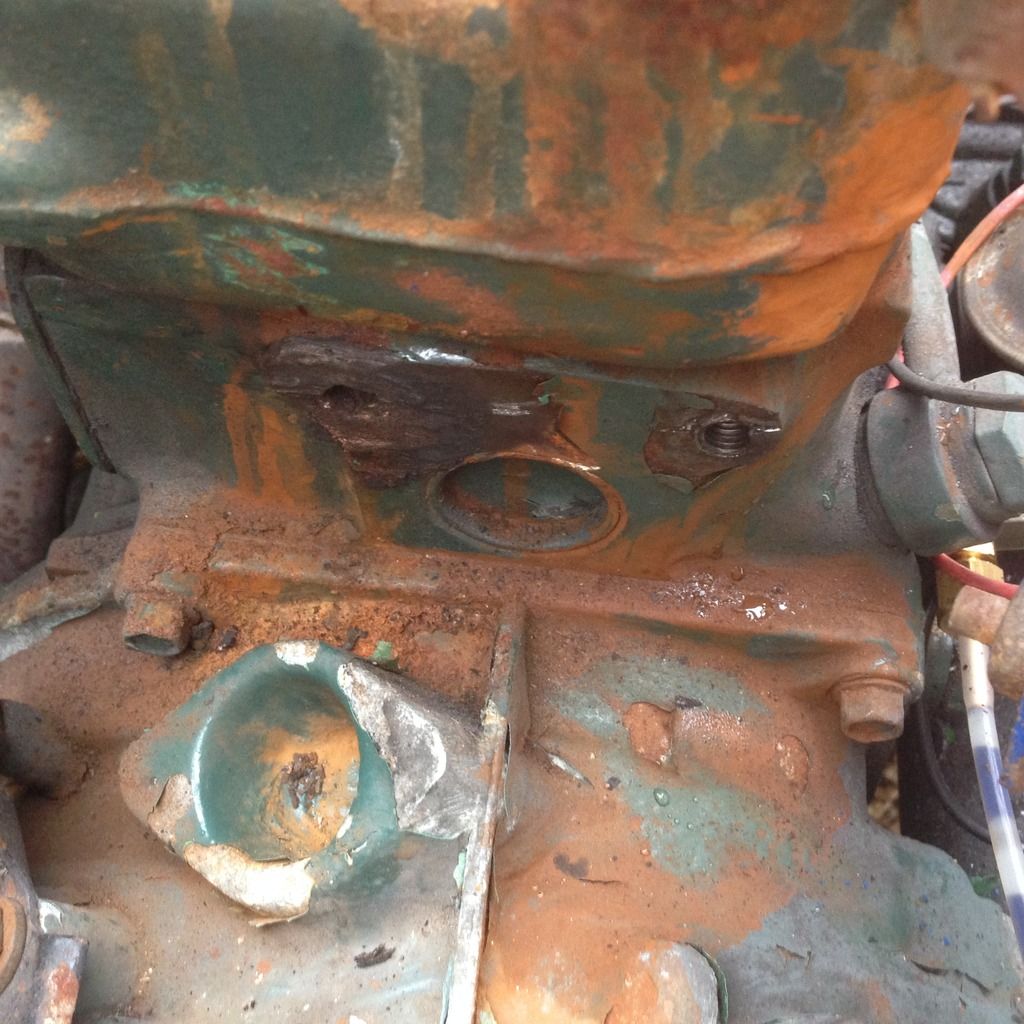
#4
Posted 12 April 2016 - 05:02 PM
You can drill out the broken bolt using a 90 degree drill attachment then drill further and fit a Heli-coil. The thread size is 5/16" UNF.
#5
Posted 12 April 2016 - 05:50 PM
Whilst I know that is the correct thing to do cooper man, I don't have a 90degree drill adapter or any taps or helicoils so once I have paid all that, I don't feel comfortable doing it so an option like swift_general has offered up seems inviting. What bolt would be needed to use that bracket?
Cheers
Steve
#6
Posted 12 April 2016 - 05:56 PM
I guess we are talking about the rear bolt hole?
And you mention that you are through to the water jacket.
I think you have bigger issues at the moment.
#7
Posted 12 April 2016 - 05:56 PM
It's a bit odd that a bolt should shear in use. There are two bolts holding the stepped bracket onto the block; a short one and a long one which goes through he steady bar. Have they both sheared or only the long one? If just the long one I suspect it was broken when the engine was installed (that's when I have done it ) and it was not noticed. The steady bar was probably held in place (just) by the clamping effect of the other bolt, then it broke away after a bit of driving.
#8
Posted 12 April 2016 - 06:15 PM
When I removed it to change the bushes on the engine steady, water pissed out, so someone in a past life has gone into the water jacket. When I refitted the bolt it sealed so I don't think it's too much of an issue?
The shorter front bolt is still fine
#9
Posted 12 April 2016 - 06:24 PM
Can't see how a 5/16" dia steel bolt could shear. The shear load to break it would be around 1 ton and that is in simple shear rather than supported by the bracket.
Normally that bolt only breaks when being (over) tightened during assembly.
#10
Posted 12 April 2016 - 06:37 PM
At the bottom are broken steady repair kits.
They will get you out of trouble if you don't fancy drilling out the snapped bolt.
#11
Posted 12 April 2016 - 06:47 PM

Cooper man - all I know is that the bolt was fine when I put it in, whether I over tightened it or under tightened it, when I left it it was in one piece and has been fine for a week - but now half is missing and half is stuck in the block.
#12
Posted 12 April 2016 - 09:48 PM
Edited by Swift_General, 12 April 2016 - 09:51 PM.
#13
Posted 12 April 2016 - 10:19 PM
Of course the you have to get the bolt off the bit!
But they do seem to be more successful than easi-outs and work in small drills.
#14
Posted 12 April 2016 - 11:39 PM
Nothing wrong with easi outs, we used them a lot in aircraft and still do so..... I have lots of the things what they are not good with is rusted in bolts, but as you had copper slipped yours it would be fine, I suspect you didn't have the correct support bracket in place hence why is broke, they are SAE5 bolts so not overly strong but still more than capable of doing the job if supported and bot bolts are tightened correctly.
Cooperman is right about the 1000kg shear capacity, but this becomes a little different when you don't have the supporting bracket and you get a combination of tensile and shear forces, this combination in your case has caused fatigue, in just the same way that Uri Gella breaks spoons.
Part item number 23 in the picture below
image.axd.jpg 8.05K
4 downloads
Edited by MRA, 12 April 2016 - 11:41 PM.
#15
Posted 13 April 2016 - 08:01 AM
Of no use here, but I must admit I prefer the early set up with the backing plate connecting the two bolts together too.
1 user(s) are reading this topic
0 members, 1 guests, 0 anonymous users