Hi guys. Well i think I can probably call this a success, it was a bit more hassle than I thought because the bolt I was planning on using wasn’t quite long enough. Any way I’ll let the photos do the talking.
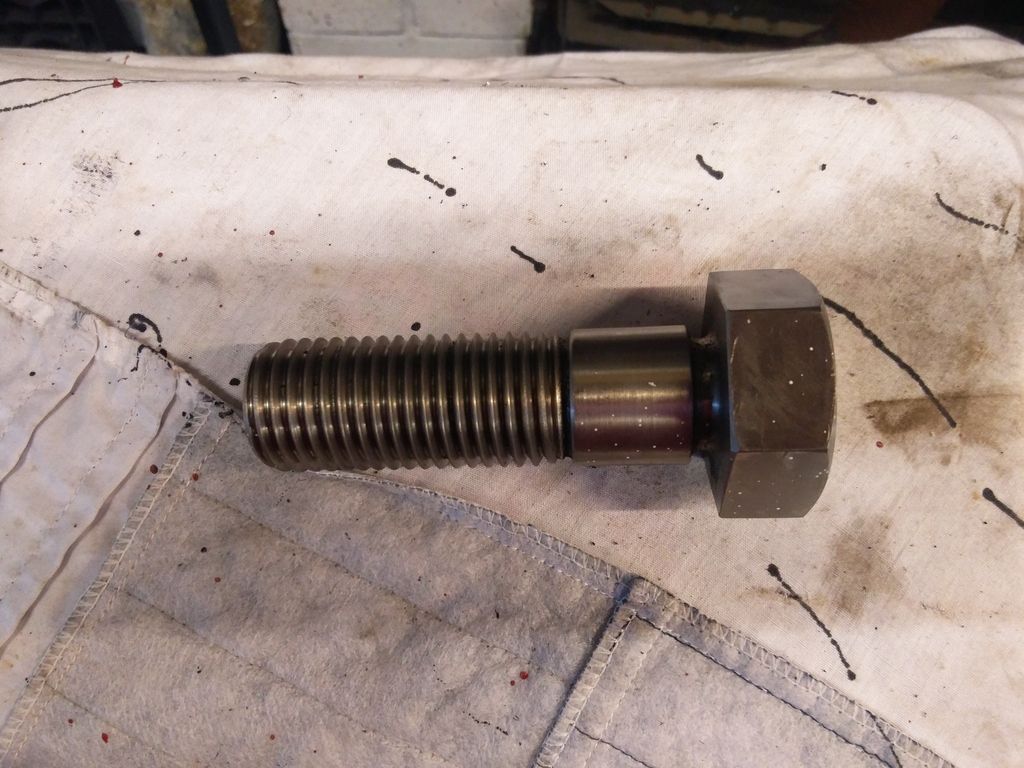
This is the bolt that’s too short so the first thing was to lop the head off it
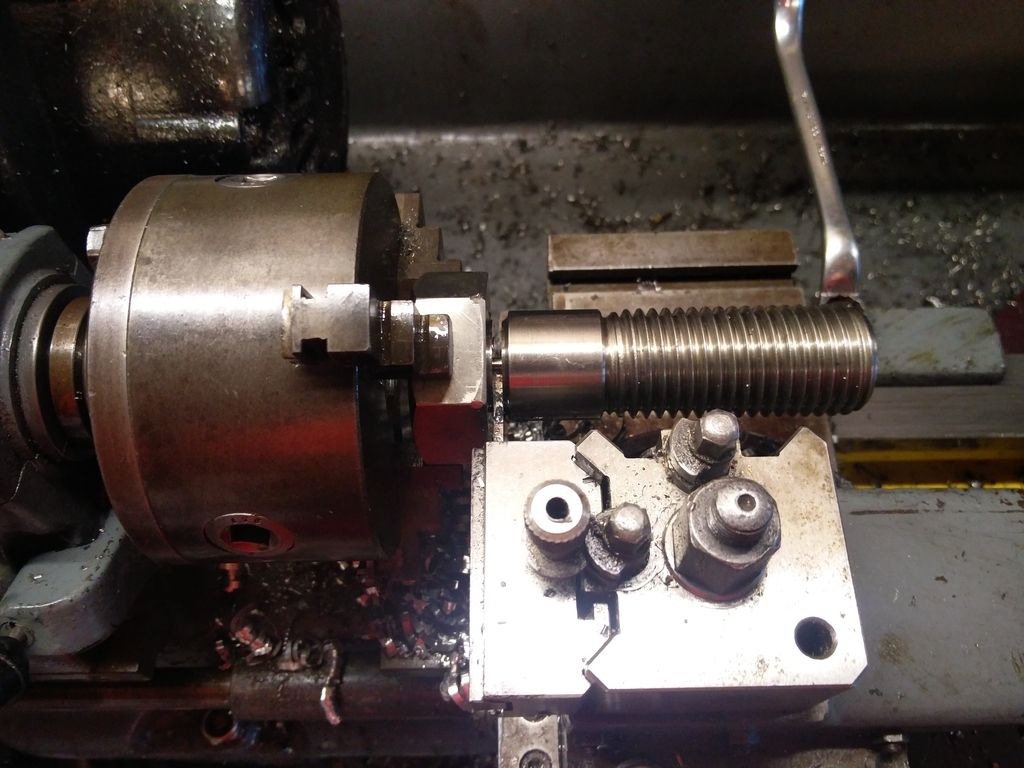
And then bore out the centre to 25.5mm and stick some chamfers on it
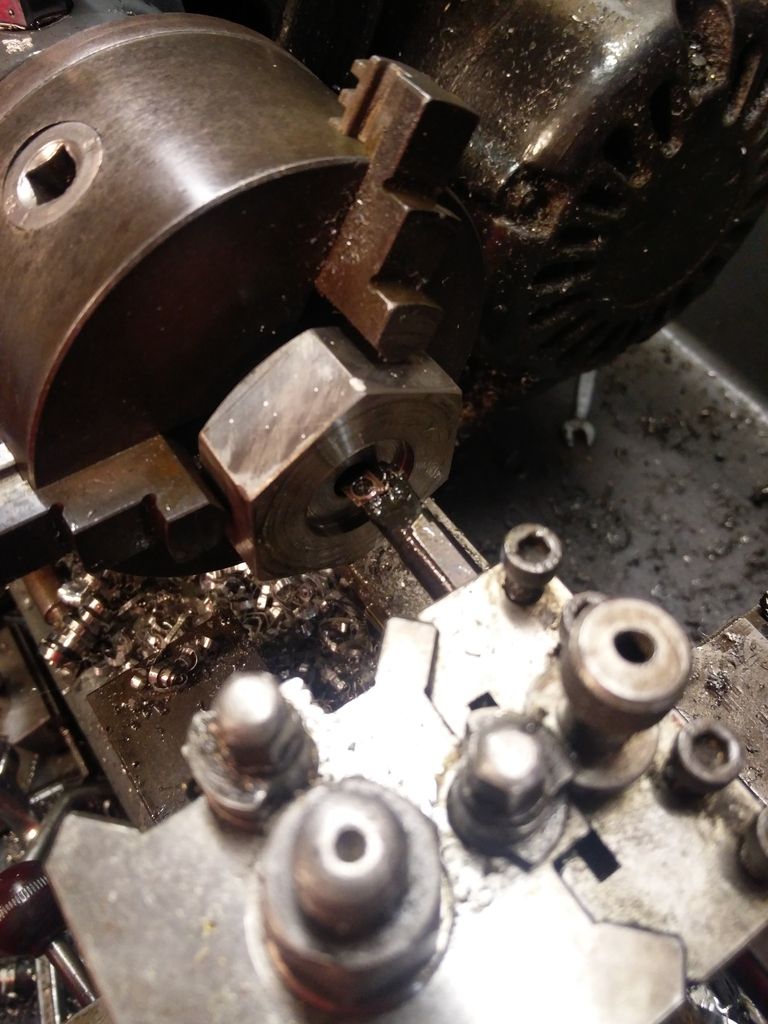

Then i used this titanium valve stem which was quite handily 25.5mm to start with, i lopped a bit off and put a chamfer on it
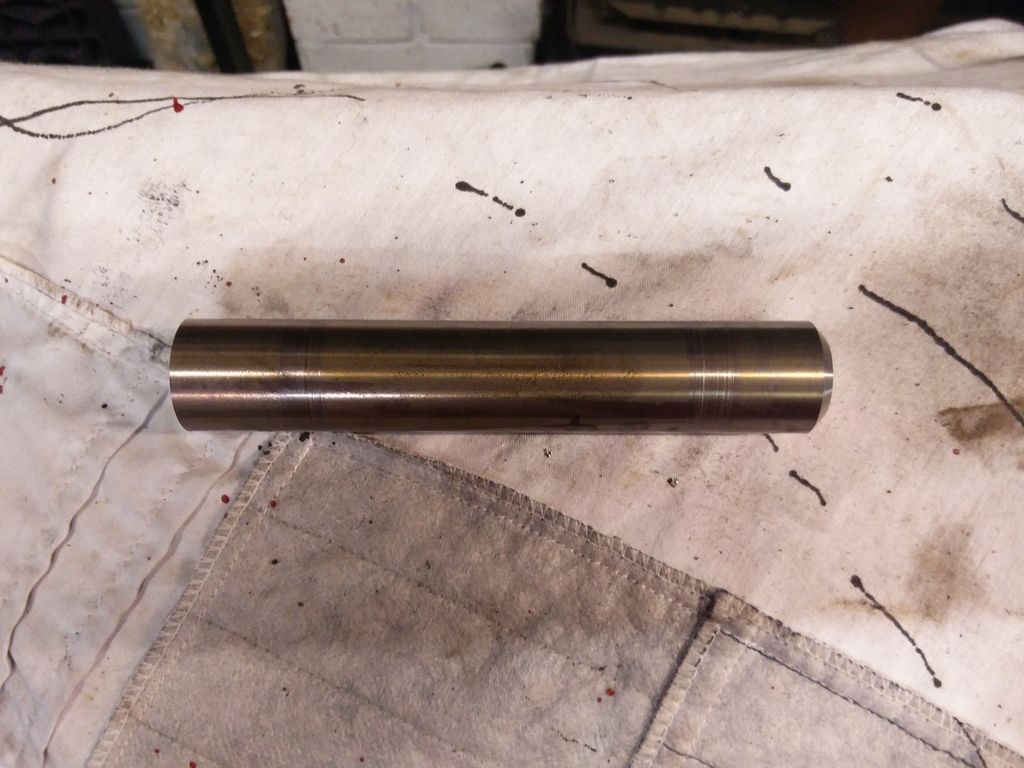
And then fitted them together, they are a very tight fit and the head gets put in the oven and the bar/shank put in the freezer to get them to fit. A quick blast round the head with a blow torch gets them to separate again. Chamfered on the back to.
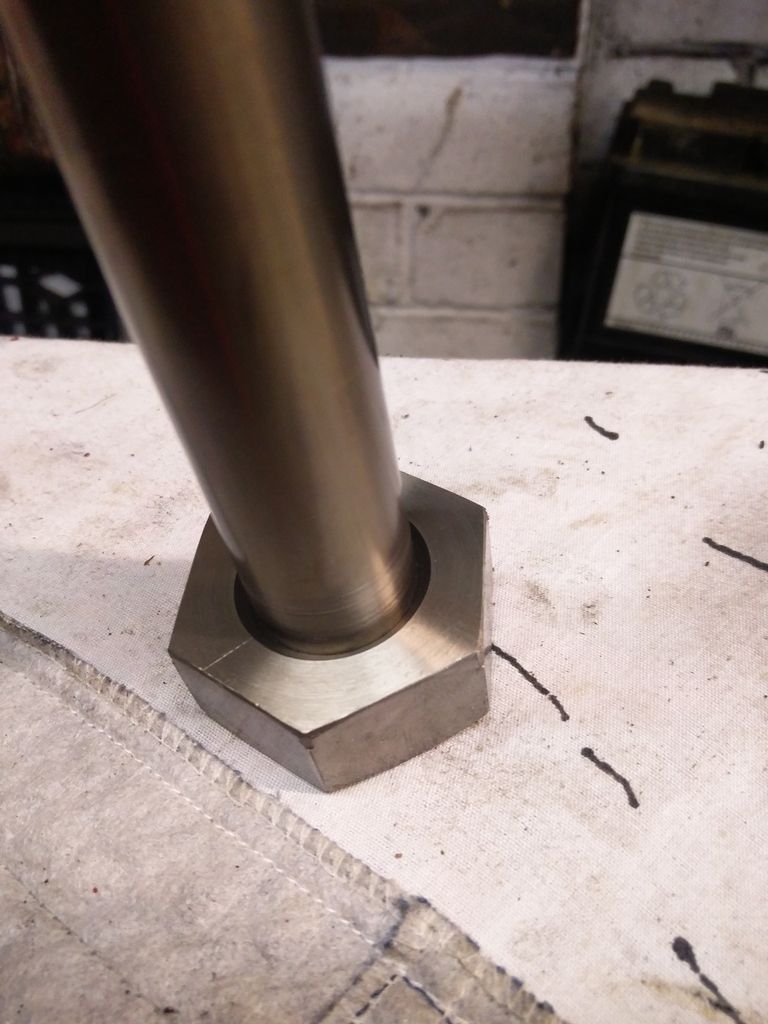
Next was to mill the head down to the correct size of 1 5/16 and put a flange on it
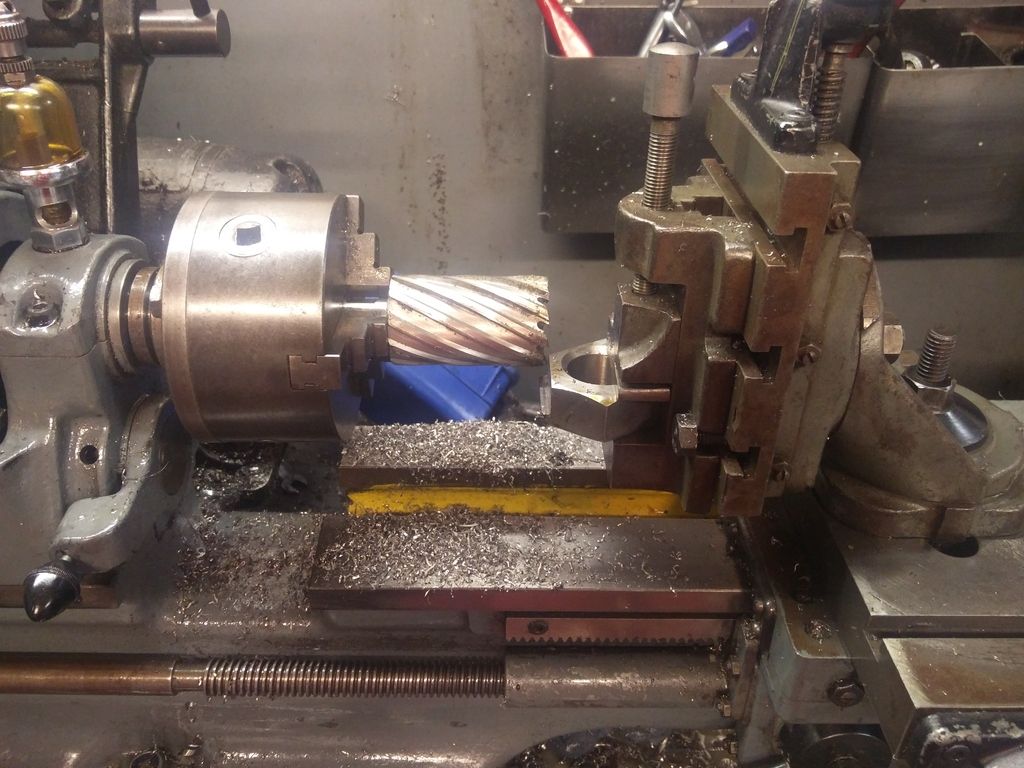
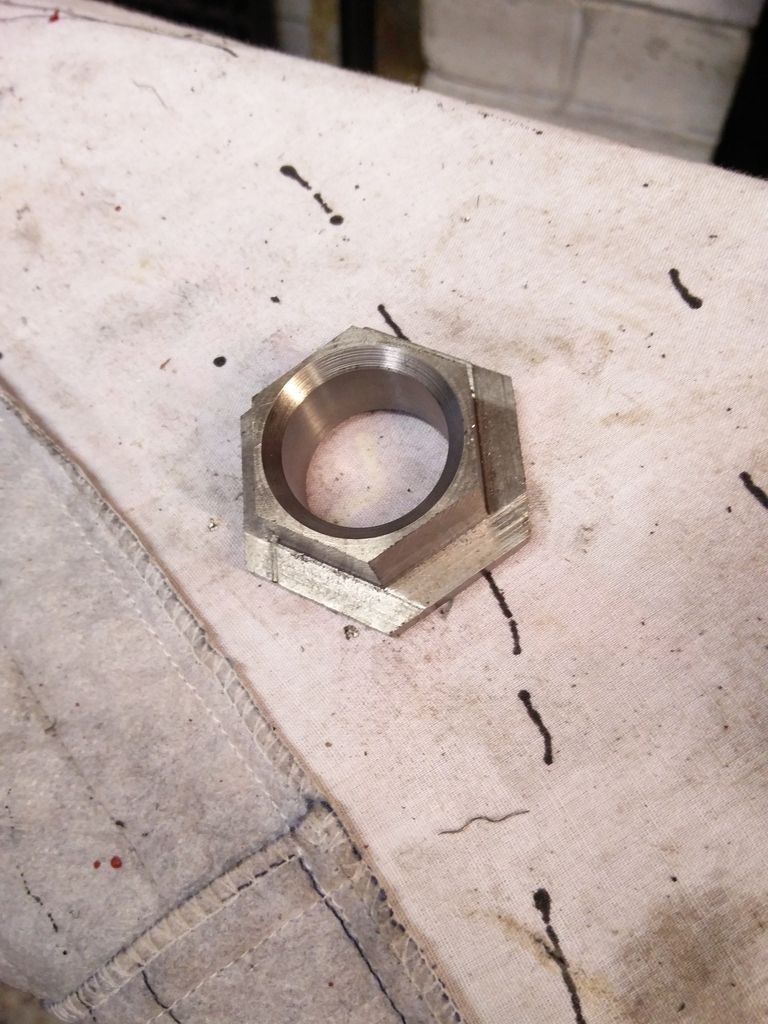
Back together
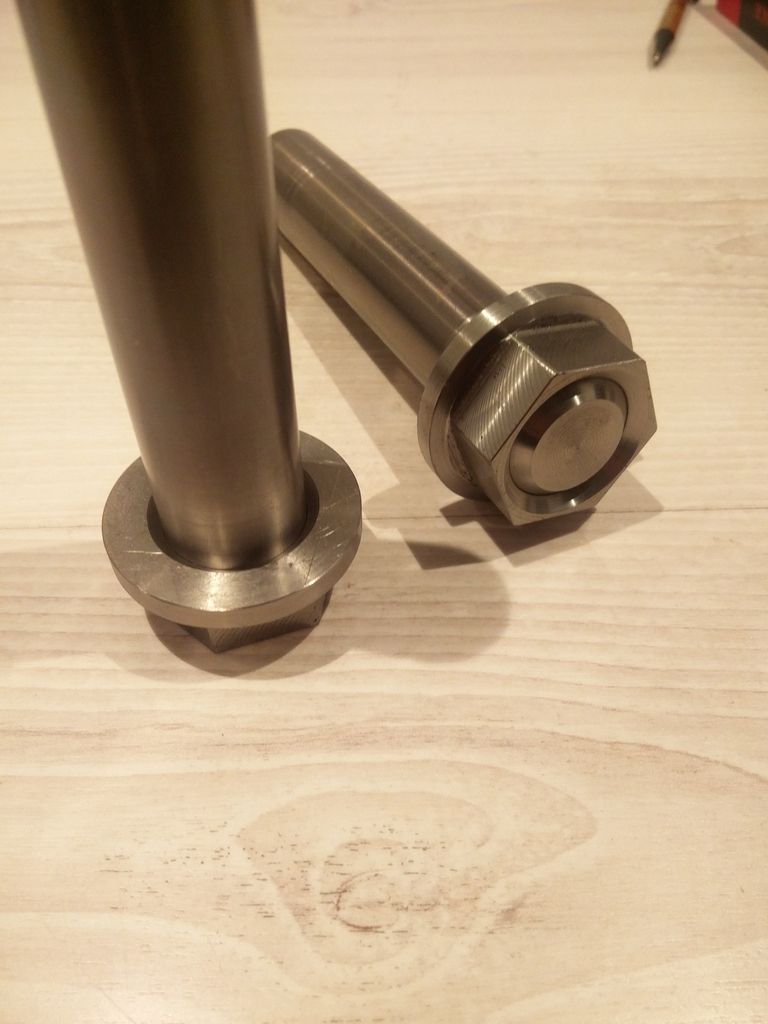
Then welded them up on both sides
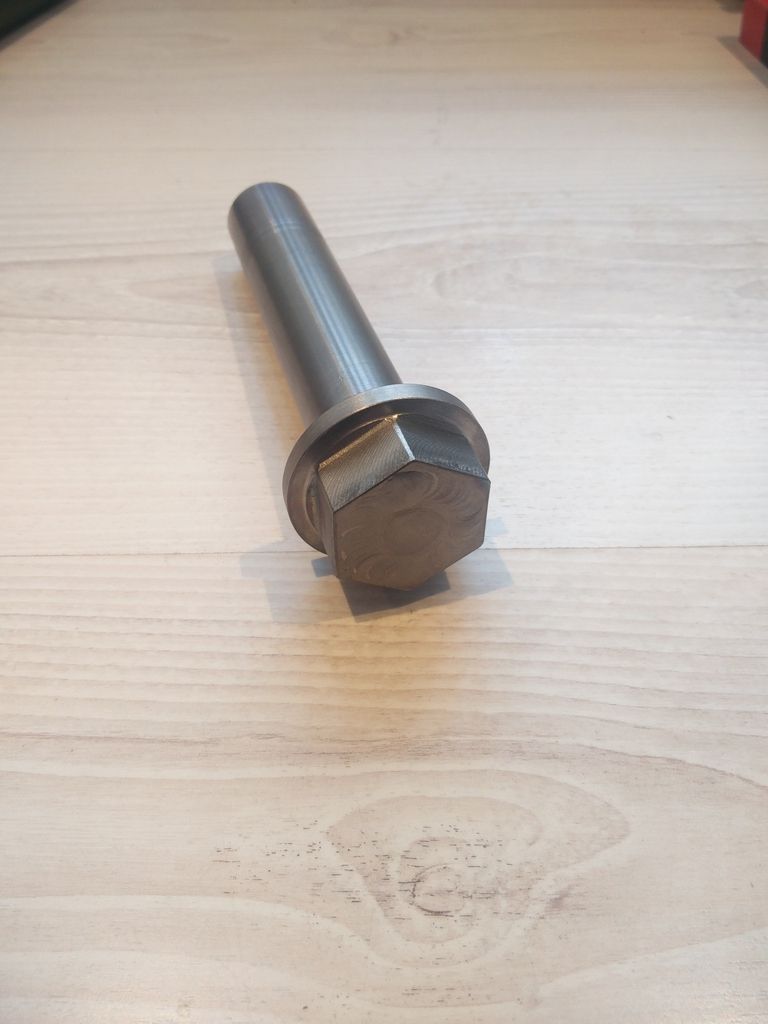
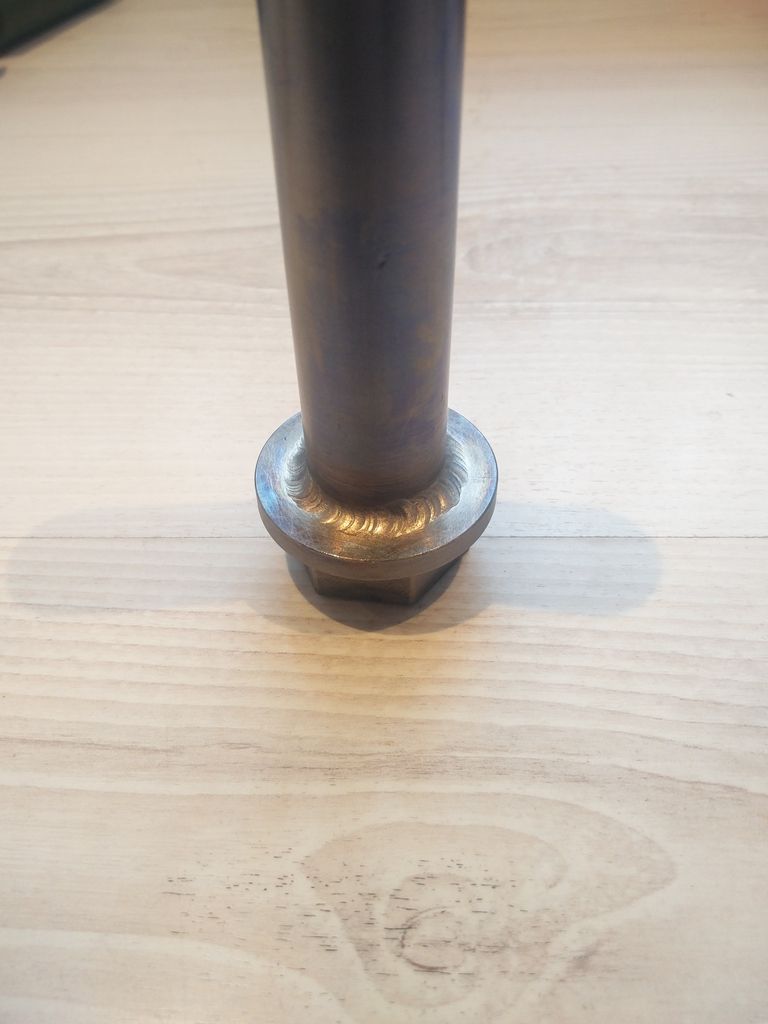
And skimmed them off
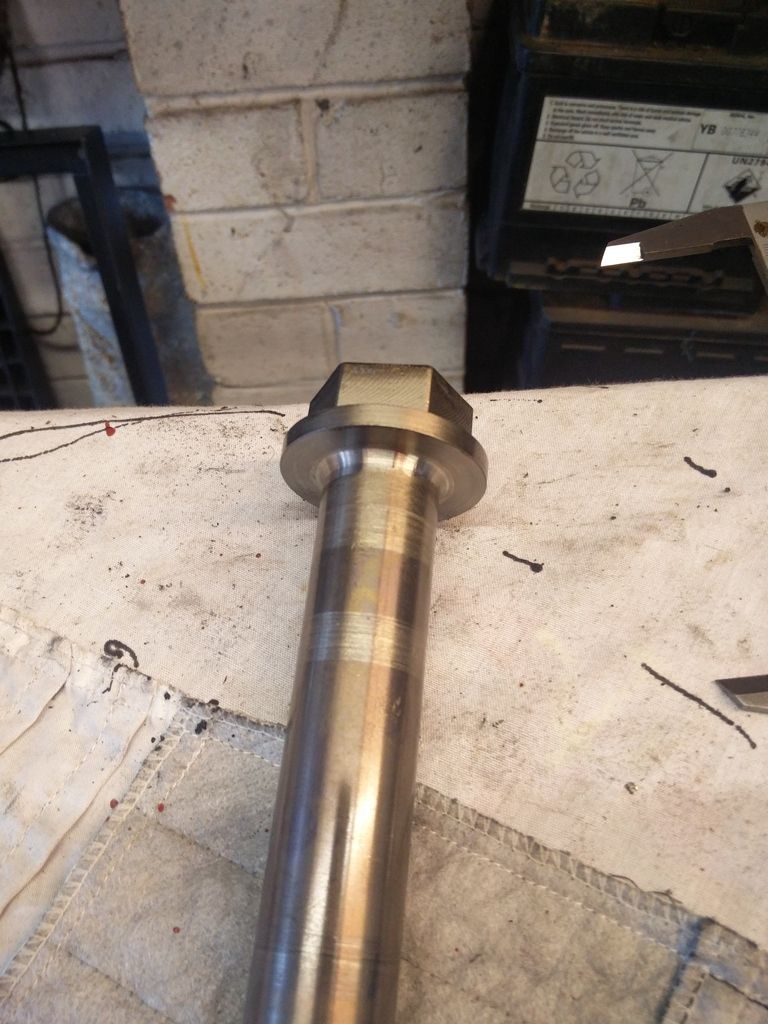
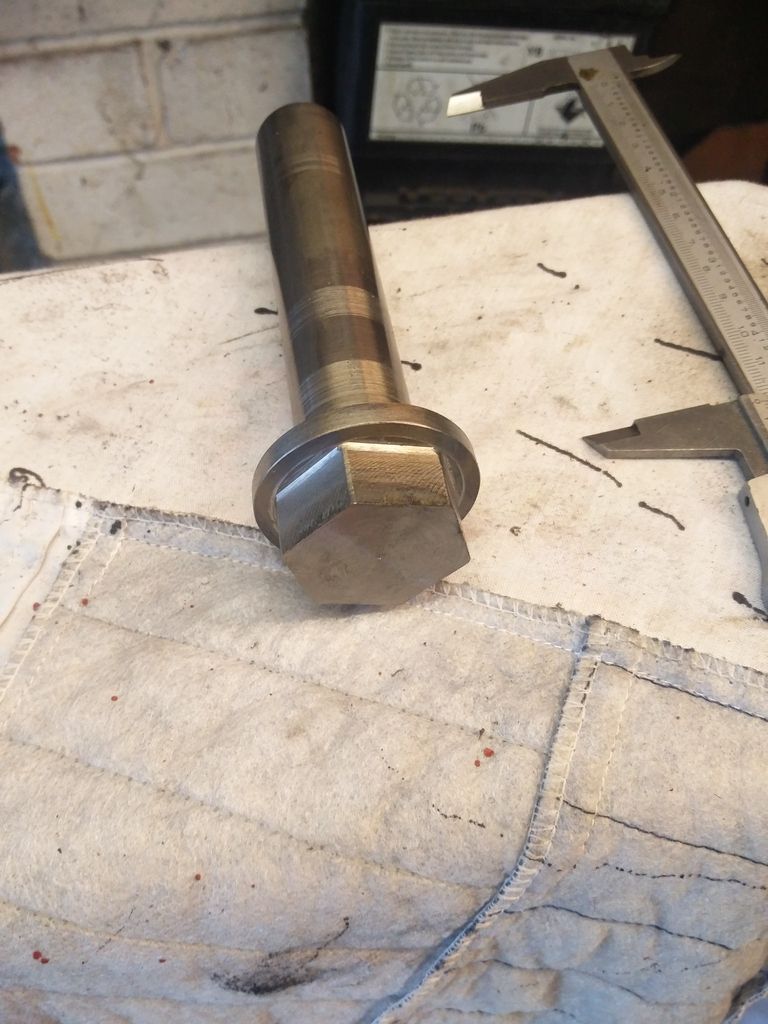
I then turned the end down and threaded it
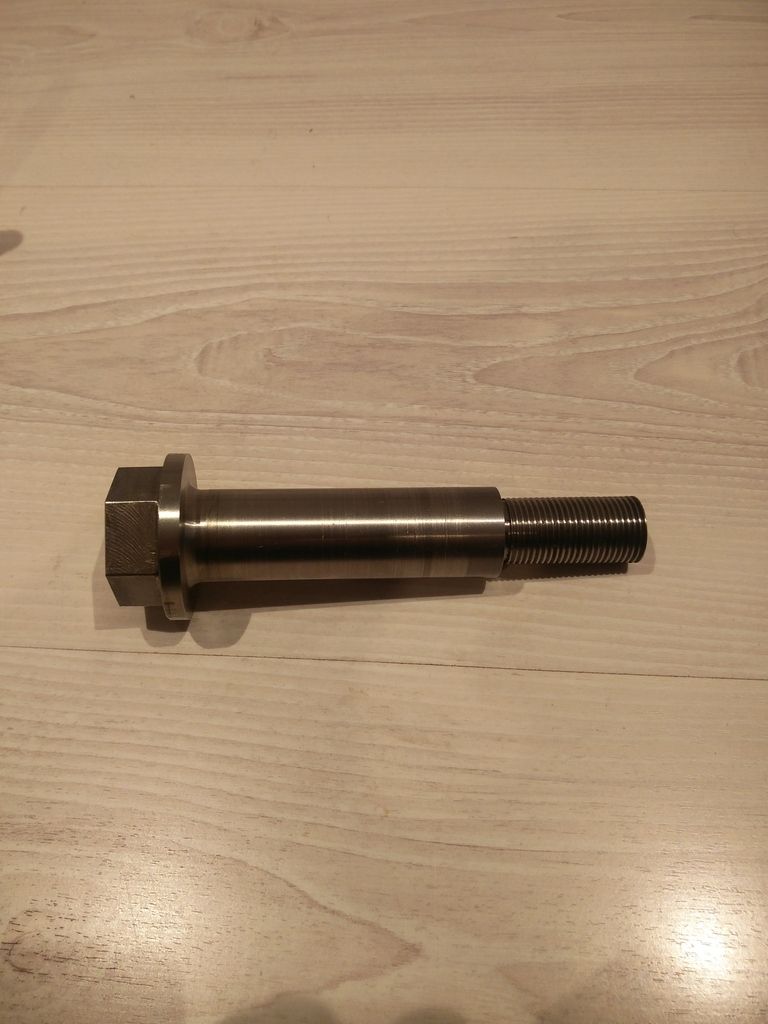
And that’s about it, the new ones come out at 310 grams. I’m not sure what sort of saving that is, i had a look on the weights thread but could only find the double tower bolt version. So if anyone knows what the original ones weigh that would be great.
I also made the bolts for the front mount on the rear subframe.
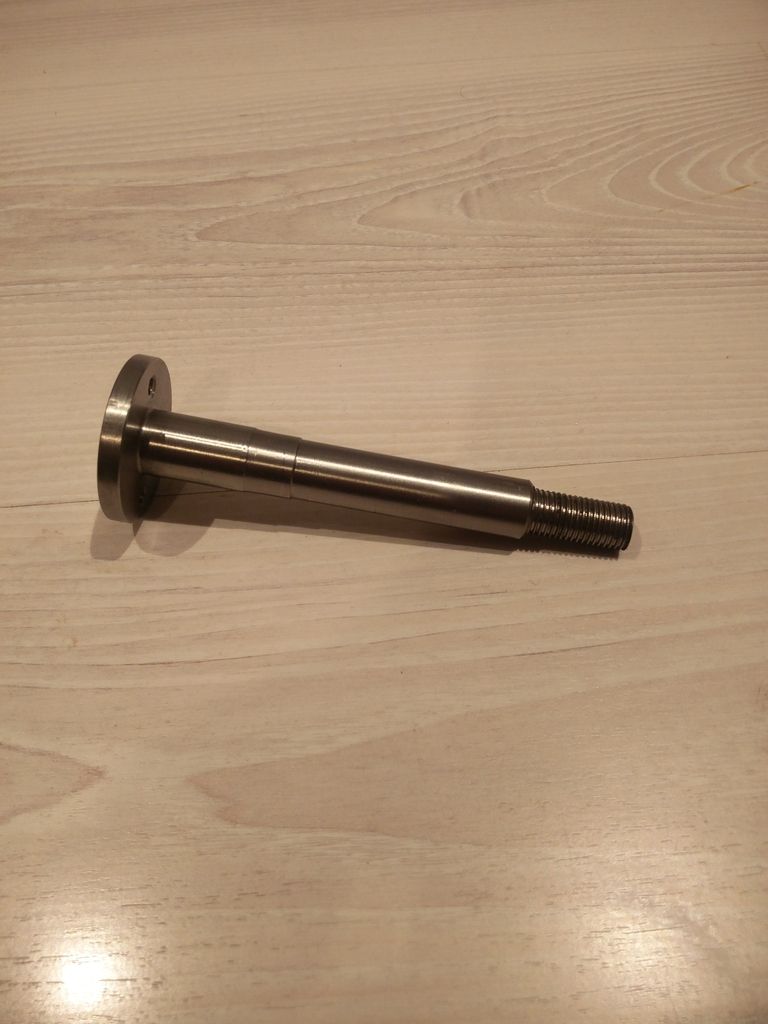
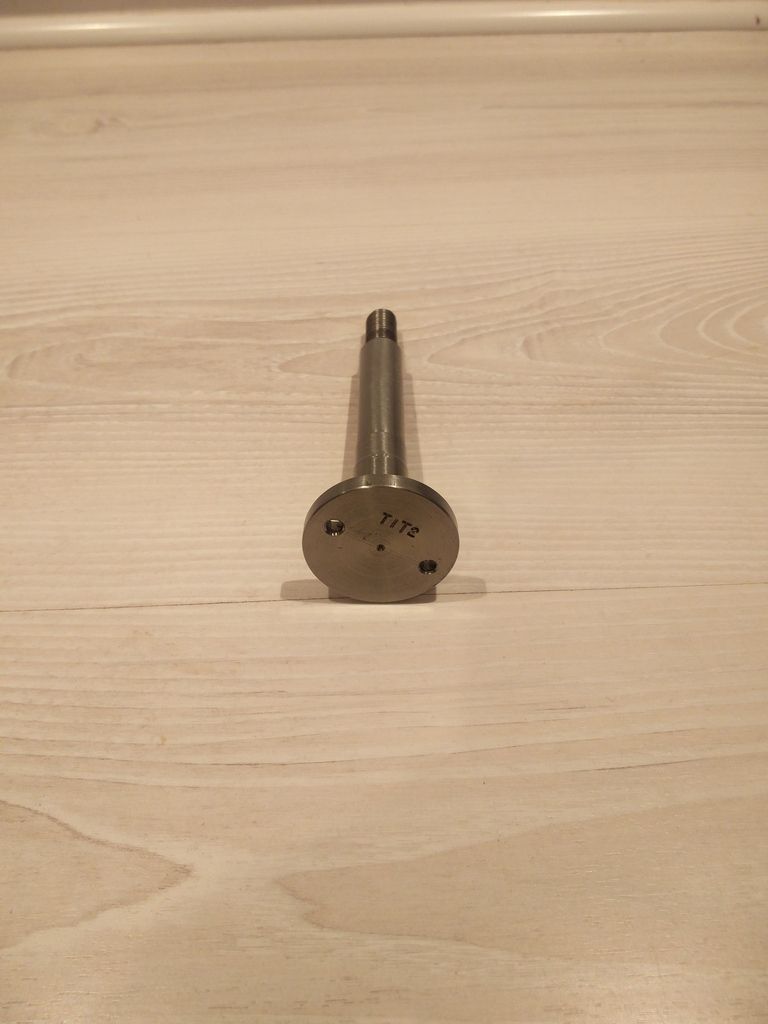
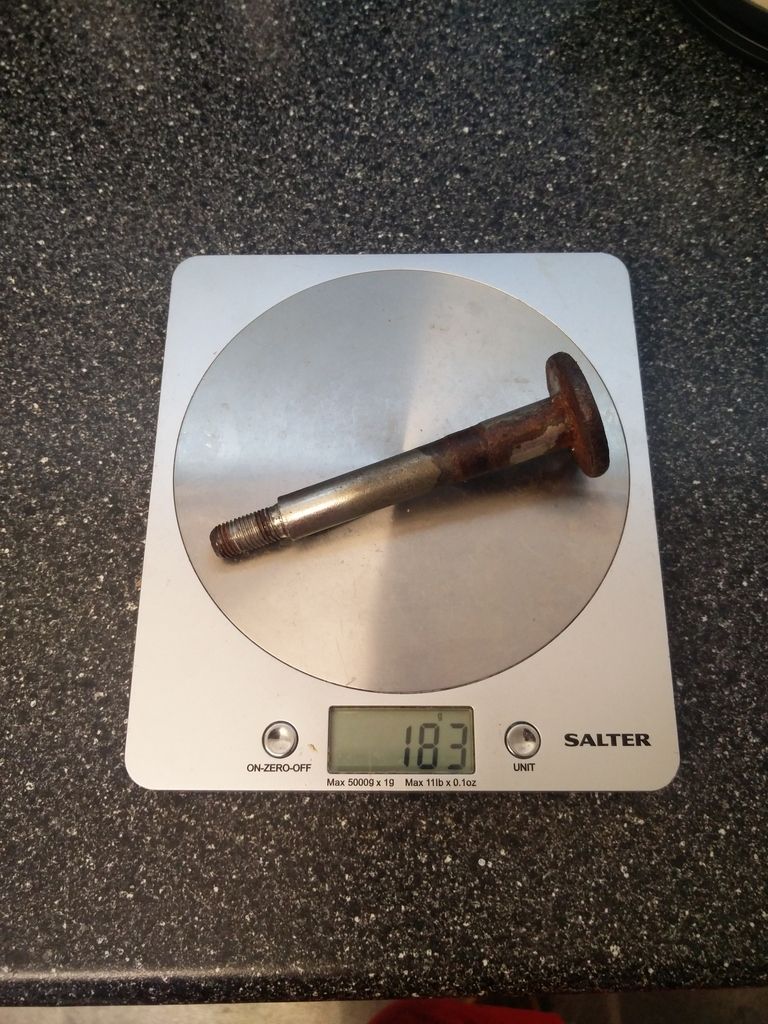
