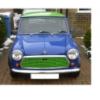
Preparing Heritage Panel
#1
Posted 04 November 2016 - 04:42 PM
Thanks as always😀😀
#2
Posted 04 November 2016 - 05:06 PM
This is what I have been doing on Paddy. Then once all of the welding is complete I will seam seal every joint I can get to.
#3
Posted 04 November 2016 - 05:11 PM
I measured and marked out using a white paint pen exactly where my spot welds were going to be put, I then used a small wire brush on a drill and removed the e-coat paint just enough to get decent spot welds, by doing this I only removed enough e-coat paint and got nice and neat uniformed welds along the panel as I like to keep as much e-coat as possible.
When the spot welding was completed I then used a syringe filled with paint (I think I used POR15) and started to gently feed it in through the joint at the top of the panel allowing for gravity and capillary action to occur. Then I gently used a panel hammer and dolly to dress the edge nice, neat and as flat as possible which squeezed some of the paint out, and finally brushed some more of the paint on the back of the seem (depends on which panel of course) just for added measure and finally use a good quality seam sealer, my preference is tiger seal.
Some people to choose the zinc or copper weld through spray (available from Frost Restoration etc.) some use what your proposing or POR15 but I think that as long as you can get something in the gap after welding to stop moisture from entering and it is durable, I don't think you will go far wrong.
Edited by neal, 04 November 2016 - 05:12 PM.
#4
Posted 04 November 2016 - 08:24 PM
thanks for the answers neal and sonikk4, will hopeing to make a start tomorrow. Its kind of what i were thinking
#5
Posted 04 November 2016 - 08:45 PM
I measured and marked out using a white paint pen exactly where my spot welds were going to be put, I then used a small wire brush on a drill and removed the e-coat paint just enough to get decent spot welds, by doing this I only removed enough e-coat paint and got nice and neat uniformed welds along the panel as I like to keep as much e-coat as possible.
When the spot welding was completed I then used a syringe filled with paint (I think I used POR15) and started to gently feed it in through the joint at the top of the panel allowing for gravity and capillary action to occur. Then I gently used a panel hammer and dolly to dress the edge nice, neat and as flat as possible which squeezed some of the paint out, and finally brushed some more of the paint on the back of the seem (depends on which panel of course) just for added measure and finally use a good quality seam sealer, my preference is tiger seal.
Some people to choose the zinc or copper weld through spray (available from Frost Restoration etc.) some use what your proposing or POR15 but I think that as long as you can get something in the gap after welding to stop moisture from entering and it is durable, I don't think you will go far wrong.
The only trouble with the coating on Heritage panels that i have found is it covers spider tracks of rust. I have had two panels now where i have suffered this so always wary about leaving it on.
It is however far far superior to the cack grey / black primer coat that magnum use. Always worth inspecting before doing anything welding wise.
#6
Posted 04 November 2016 - 09:02 PM
I measured and marked out using a white paint pen exactly where my spot welds were going to be put, I then used a small wire brush on a drill and removed the e-coat paint just enough to get decent spot welds, by doing this I only removed enough e-coat paint and got nice and neat uniformed welds along the panel as I like to keep as much e-coat as possible.
When the spot welding was completed I then used a syringe filled with paint (I think I used POR15) and started to gently feed it in through the joint at the top of the panel allowing for gravity and capillary action to occur. Then I gently used a panel hammer and dolly to dress the edge nice, neat and as flat as possible which squeezed some of the paint out, and finally brushed some more of the paint on the back of the seem (depends on which panel of course) just for added measure and finally use a good quality seam sealer, my preference is tiger seal.
Some people to choose the zinc or copper weld through spray (available from Frost Restoration etc.) some use what your proposing or POR15 but I think that as long as you can get something in the gap after welding to stop moisture from entering and it is durable, I don't think you will go far wrong.
The only trouble with the coating on Heritage panels that i have found is it covers spider tracks of rust. I have had two panels now where i have suffered this so always wary about leaving it on.
It is however far far superior to the cack grey / black primer coat that magnum use. Always worth inspecting before doing anything welding wise.
This is a very good point, I forgot to mention this as I had forgot, looking back, yes you're absolutely right sonikk4 :)
Teamwork rules!
#7
Posted 04 November 2016 - 09:03 PM
I think in my case it's easier for me to clean it all off where welding and use the sprays,
#8
Posted 04 November 2016 - 09:04 PM
I think in my case it's easier for me to clean it all off where welding and use the sprays,
It's up to you mate, either way I'm sure you'll make a good job.
As sonikk4 said you can see the little spider runs when inspecting the seams
Edited by neal, 04 November 2016 - 09:06 PM.
#9
Posted 04 November 2016 - 09:06 PM
I think in my case it's easier for me to clean it all off where welding and use the sprays,
It's up to you mate, either way I'm sure you'll make a good job.
I can only hope so !!!!
#10
Posted 04 November 2016 - 09:07 PM
That's the thing, its entirely up to you whatever method you use but its always worth listening to the voice of experience.
I've learnt from my mistakes.
#11
Posted 04 November 2016 - 09:11 PM
That's the thing, its entirely up to you whatever method you use but its always worth listening to the voice of experience.
I've learnt from my mistakes.
Defo...... It wouldn't be fun if you didn't learn anything along the way and you never stop learning.
#12
Posted 04 November 2016 - 09:12 PM
I've made a start on the floor just popped a couple of pics up on "floor fitting" and I have to say the voices are worth listening to on here!! Already saved me a few hassles ie. take out the companion bins and crossmember because I think another floor half would have been required because it were still fiddly getting it in place !!!!
1 user(s) are reading this topic
0 members, 1 guests, 0 anonymous users