I was almost certain that I had asked this question the last time I did this job but If I did, I can't find where I asked and it's another area I'd rather just be right.
I've just reinstalled the driveshafts back in the hubs after completing the ball joint rebuild. I've torqued the driveshafts with a flat washer to seat everything correctly, carefully removed the nut and flat washer, installed the conical washer and torqued to 197 lb/ft. Now obviously the next thing is to tighten it to the next split pin hole and install the split pin.
Now this might sound a silly question but, if it happens to have lined up with a split pin hole after torquing, is that fine or does it rely on you tightening past that to the next one to be at the appropriate torque?
At the moment the split pin hole is just at the edge where it's about to go under the nut if I tighten it any further, so there is scope there for the nut to back off a small amount before hitting the split pin. Is that fine?
I can grab some pictures if I'm not explaining the situation clearly.
Thanks for any help.
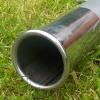
Driveshaft Installation - Torque And Split Pins

Best Answer Spider , 06 August 2017 - 07:59 PM
Now this might sound a silly question but, if it happens to have lined up with a split pin hole after torquing, is that fine or does it rely on you tightening past that to the next one to be at the appropriate torque?
At the moment the split pin hole is just at the edge where it's about to go under the nut if I tighten it any further, so there is scope there for the nut to back off a small amount before hitting the split pin. Is that fine?
That'll be fine.
Go to the full post
#1
Posted 06 August 2017 - 10:13 AM
#2
Posted 06 August 2017 - 10:54 AM
You can either go up to the next recess in the castellated nut or back it off very slightly. Once the split pin is in and bent over it isn't going anywhere. I prefer to go up rather than down but that isn't always possible.
#3
Posted 06 August 2017 - 02:07 PM
Edited by Swift_General, 06 August 2017 - 02:20 PM.
#4
Posted 06 August 2017 - 02:29 PM
If you are just over the split pin hole at the correct torque and struggling to tighten to the next gap in the nut then simply linnish a little material from the back of the nut.
good idea i never thought of that .... i ended up backing off to the previous hole as i was putting more torque in than the mini brakes could stop
#5
Posted 06 August 2017 - 06:11 PM
as long as you have preloaded the bearings without the C washer
#6
Posted 06 August 2017 - 07:59 PM Best Answer
Now this might sound a silly question but, if it happens to have lined up with a split pin hole after torquing, is that fine or does it rely on you tightening past that to the next one to be at the appropriate torque?
At the moment the split pin hole is just at the edge where it's about to go under the nut if I tighten it any further, so there is scope there for the nut to back off a small amount before hitting the split pin. Is that fine?
That'll be fine.
#7
Posted 21 August 2017 - 01:21 PM
I managed to get this job finished off and ticked off the list yesterday so she's back on her wheels and another step closer to the road.
Thanks to everyone who offered advice, I appreciate it.
1 user(s) are reading this topic
0 members, 1 guests, 0 anonymous users