Edited by Cmontgomeryc, 24 September 2018 - 08:04 AM.
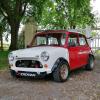
Tight Spot On Crankshaft
#1
Posted 24 September 2018 - 08:03 AM
#2
Posted 24 September 2018 - 08:28 AM
It sounds like one of the journals is out-of-round. If you have a micrometer, either metric or imperial (with 10ths) then you can double check. If that's true then you need to go back to the grinder.
#3
Posted 24 September 2018 - 08:41 AM
A ghetto check (as you already have scored the bearings) would be to use a permanent marker on the journel to show a high spot when rotated
#4
Posted 24 September 2018 - 08:41 AM
#5
Posted 24 September 2018 - 08:45 AM
There should be no marks on any of the journals and certainly no scoring
If you can see anything or feel anything it needs to go back to the machine shop
As above it needs checking for round and taper, but scoring is debris or damage from something
All the drillings need cleaning out again, block and crank
It also needs checking for straightness preferably whilst in the block
#6
Posted 24 September 2018 - 08:59 AM
If it's scoring, then there's something there that shouldn't be.
It's quite easy to have a contaminate in there. When you clean it all, clean it again, and even then, it won't be clean enough. I do use a Kerosene based cleaner in my engine cleaning bath, but that's only for a 'preliminary' clean. One up side is it does leave an oily film so parts have some protection from rust, likewise, the down side of it is it leaves an oily film that captures dust very easy.
Following this preliminary clean, I clean the parts again with Paint Thinners as this leaves no residue and is very clean, the down side being, they need oil in short time or certain times of the year, they'll begin to rust before your eyes.
When fitting the Bearing Shells, they are slightly expanded in size from the tunnel size. When fitting them, the backs inevitably scrap on the block, which can cause shaving of the shell back. Some of these shavings can end up between the shell and the block, distorting the shell and causing it to rub on the crank.
When the crank is re-ground, the grinder man should as part of that process, enlarge the chamfers on the journal surface where of the Oil Way Drillings. This is usually done by hand with a die grinder and it is possible that one of these may have a bur from this process.
#7
Posted 25 September 2018 - 11:48 AM
#8
Posted 27 September 2018 - 06:43 PM
Also could be a bend in the crank
Good suggestion, and I would be surprised if DTI picks up out of round journals unless the regrind has been spectacularly incompetent.
Here is suggested check for bend in crank when you have the DTI available:
- assemble crank (no rods) into crankcase with only the two end bearings. no cap or shells for centre
- first see if crank rotates easier with no tight spots
- then if running free put DTI on centre main journal (avoid oilway) and rotate, checking DTI for runout at centre main
About 1 thou runout is unlikely to cause issues. 2 thou or more likely needs corrected.
#9
Posted 27 September 2018 - 07:19 PM
The crank has been reground, so surely, if there was a bend in it, it will have resulted in more being taken off one side than the other and the crank now being "true", but less 'in balance'.
#10
Posted 27 September 2018 - 07:49 PM
Also could be a bend in the crank
Good suggestion, and I would be surprised if DTI picks up out of round journals unless the regrind has been spectacularly incompetent.
Here is suggested check for bend in crank when you have the DTI available:
- assemble crank (no rods) into crankcase with only the two end bearings. no cap or shells for centre
- first see if crank rotates easier with no tight spots
- then if running free put DTI on centre main journal (avoid oilway) and rotate, checking DTI for runout at centre main
About 1 thou runout is unlikely to cause issues. 2 thou or more likely needs corrected.
All good suggestions, however, if I can suggest, at 1 thou run-out, there will likely be an issue. Running clearance is 0.001 to 0.0027". From what I see, most Crank GrInders tend to go for the tighter limit (o.001") when grinding (I wish they wouldn't), so at 0.001" run-out, all the clearance will have been eaten up.
Although these are very small numbers, they need even more care. Eg, a crank with 1/2 a thou run-out has 50% of the bottom end of the range of clearance taken away.
I think in all fairness, we need to see some photos.
#11
Posted 27 September 2018 - 09:30 PM
OK, so if my idea that the grinding would result in a true shaft, doesn't work, and the shaft is bent, as it rotates, it is going to rub all the way round, not just in one place.
#12
Posted 27 September 2018 - 09:48 PM
OK, so if my idea that the grinding would result in a true shaft, doesn't work, and the shaft is bent, as it rotates, it is going to rub all the way round, not just in one place.
It also depends on the alignment of the main bearing housings.
#13
Posted 28 September 2018 - 01:40 AM
OK, so if my idea that the grinding would result in a true shaft, doesn't work, and the shaft is bent, as it rotates, it is going to rub all the way round, not just in one place.
It also depends on the alignment of the main bearing housings.
Also, if it really is bent (and that's not at all unusual to find), it's always best after confirming that's the case, to straighten it 100% before re-grinding, otherwise, the flywheel will really whip around big time, making matters worse.
When checking for a what appears to be a bent crank, especially if it's ever been re-ground, the Nose and in particular, the Tail should also be checked for run out. If these have run-out, then the crank is bent, if however, the Centre Main has run-out and the Tail doesn't, then somewhere it's most likely had a poor grind job done.
#14
Posted 28 September 2018 - 10:25 AM
Crankshafts all have some tolerances. In fact there are several in addition to the journal diameters.
They are straightness, stroke and index.
Some crank grinders can only re-grind on existing centres, so tolerances (inaccuracies) will still be as they were.
However, more well-equipped machine shops can straighten, stroke and index a crank. This is usually done with top performance cranks for competition engines. The main bearings are all re-ground on an accurate centre-line, then the big end journals are ground to be exactly the correct and identical stroke and at the same time journals 1 & 4 are ground to be exactly 180 degrees opposite from 2 & 3. Hence straight, stroked and indexed.
Accurate it is, but cheap it ain't! My Cooper 'S' has such a crank which is, of course, also fully balanced as a bottom end assembly.
It can be surprising how far out even a brand new A-Series, or A+, crankshaft can be.
1 user(s) are reading this topic
0 members, 1 guests, 0 anonymous users