I am in the process of rebuilding my A+ 1275 (91 Rover Cooper), trying to make sure I check everything correctly. Recently read about the idler gear end float and decided to measure it. I measured the end float using a feeler gauge with the transfer cover and new gasket bolted up to the gearbox only. I am able to slide in a .012 gauge between the inner idler washer and bearing. I found the mini mania video where they did this same thing and I am slightly confused on the math portion of what I need to order. My current washers are .130 and .134. Is the goal to end up with less than .006 using this method to measure? so would that mean I need to get a washer that is .136 and ditch my .130? My idler is not a straight cut gear, from what I have read that changes the float tolerance needed as well.
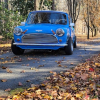
Idler Gear End Float
#1
Posted 01 December 2018 - 01:52 AM
#2
Posted 01 December 2018 - 04:58 AM
Yes, you'll want at least a 0.136" thrust on one side and it wouldn't hurt to fit one of the same size on the other side too.
#3
Posted 01 December 2018 - 05:11 AM
As Moke says get two 0.136 inch thrust washers and that will leave you with a 0.004 inch float which is ideal. They are rather expensive new, but they then they take a lot of abuse.
#4
Posted 01 December 2018 - 10:06 AM
I have a dial gauge coming in the mail in a couple days I might remeasure with that to see I come up with the same number.
#5
Posted 01 December 2018 - 10:23 AM
I haven't watched that video and in fact, I stopped watching any of their stuff when I saw him bash (and I mean really bashing) away at a bearing to fit it.
From your description here, that sounds really confusing and a needlessly difficult way of getting there !
The Factory Advice on the End Float for the A+ type Idler Gear is to set it between 0.0035 and 0,0065".
I wouldn't recommend going any tighter than the 0,0035" the Factory Recommend. If you set it to 0.004", that's about as good as it gets.
#6
Posted 01 December 2018 - 11:30 AM
I haven't watched that video and in fact, I stopped watching any of their stuff when I saw him bash (and I mean really bashing) away at a bearing to fit it.
I thought that was the proper way to install bearings though?
so with the way I measured it there shouldn't be any fear of the gap closing a little more once the engine is on and the upper bolts are secured?
#7
Posted 01 December 2018 - 11:40 AM
#8
Posted 27 December 2018 - 09:00 AM
Picking up on this issue, is there a straightforward way to measure the thrust washer tickness needed when the flywheel housing is off the car, but the gearbox is still in situ. Don't want to be taking the engine out if I can possibly help it (don't have the lifting gear for a start) but when I tighten the flywheel housing to the block and gearbox, the primary gear is locked solid. So, I presume that someone has fitted thrust washers that are too thick and they need replacing with the correct size.
#9
Posted 27 December 2018 - 09:19 AM
Are you using a genuine gasket?
#10
Posted 27 December 2018 - 09:40 AM
Picking up on this issue, is there a straightforward way to measure the thrust washer tickness needed when the flywheel housing is off the car, but the gearbox is still in situ. Don't want to be taking the engine out if I can possibly help it (don't have the lifting gear for a start) but when I tighten the flywheel housing to the block and gearbox, the primary gear is locked solid. So, I presume that someone has fitted thrust washers that are too thick and they need replacing with the correct size.
This is by no means fool proof !!
You can lay the Transfer housing down, fit the idler gear with it's trusts, lay a gasket on, then take a straight edge across the gasket over the Idler Gear Thrust that's facing up, the measure the clearance there. From that, you need to subtract an amount for gasket crush (probably around 0.001") and this might get you close. You should also check that the Thrust Face on the Gearbox is still on the same plain as the Gasket Face and if it's not, add how much the Thrust Face has been worn by.
Even when things are good, this is a far from ideal way to check it, more of a guide really. I offer no money back guarantees !!
#11
Posted 27 December 2018 - 12:04 PM
Do you mean the idler gear is locked solid?
Are you using a genuine gasket?
As in I cannot turn the primary gear by hand once the flywheel housing has been torqued up, so yes I am assuming the idler gear thrusts have locked the gear train solid.
The back story to this is that my daughter wanted me to fix an oil leak. I presumed the flywheel housing seal had gone, but found that the housing bolts were only nipped and not torqued. At the time of disaasembly I didn't associate the two 'issues'. Presumably whoever fitted the idler assembly last time felt that this was the way to fix it and also allow the oil to weep away.
#12
Posted 27 December 2018 - 02:17 PM
#13
Posted 02 January 2019 - 04:35 PM
Having now completed a checking and measuring exercise, I find that I have a 4mm thrust on the inner face and a 3.5mm thrust on the outer. With a new flywheel housing gasket fitted to the housing, there is a 0.05mm clearance between the thrust washer and the gasket face (effectively the gearbox thrust face). Gasket is 0.67mm. Allowing for gasket crush of 0.02mm says to me that i could really do with swapping the 4mm thrust for a 3.5mm ending up with two the same. Am I thinking right here?
#14
Posted 02 January 2019 - 05:55 PM
Having now completed a checking and measuring exercise, I find that I have a 4mm thrust on the inner face and a 3.5mm thrust on the outer. With a new flywheel housing gasket fitted to the housing, there is a 0.05mm clearance between the thrust washer and the gasket face (effectively the gearbox thrust face). Gasket is 0.67mm. Allowing for gasket crush of 0.02mm says to me that i could really do with swapping the 4mm thrust for a 3.5mm ending up with two the same. Am I thinking right here?
I think you've got your measurements wrong? 0.5mm is 20 thou.
#15
Posted 02 January 2019 - 07:10 PM
Having now completed a checking and measuring exercise, I find that I have a 4mm thrust on the inner face and a 3.5mm thrust on the outer. With a new flywheel housing gasket fitted to the housing, there is a 0.05mm clearance between the thrust washer and the gasket face (effectively the gearbox thrust face). Gasket is 0.67mm. Allowing for gasket crush of 0.02mm says to me that i could really do with swapping the 4mm thrust for a 3.5mm ending up with two the same. Am I thinking right here?
I think you've got your measurements wrong? 0.5mm is 20 thou.
Ah! I think you might be right Alex! I've got .05mm clearance. I would gain .5mm with the thinner thrust washer, but would lose .02mm with the gasket crush. So, 0.05 + 0.5 - 0.02 = 0.53. I'm looking for 1.0mm - 1.8mm according to the Haynes manual, so that says I need to go to 3mm thrust and a 3.5mm to gain 1.0mm and end at 1.03mm. Does that sound better?
Edited by Sussex_pete, 02 January 2019 - 07:12 PM.
1 user(s) are reading this topic
0 members, 1 guests, 0 anonymous users