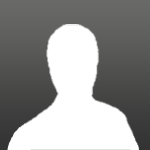
Problems Bolting Lcb Manifold Roll Cylinder Head
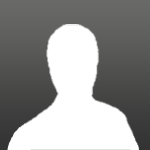
Best Answer postve , 21 February 2020 - 08:12 PM
Being able to remove the head on a competition car easily is a big advantage. Wrestling with more studs, engine steadies etc is a pain if you’re trying to change a head gasket it a hurry.
i use similar to Cooperman, but I use socket head cap screws as I find an extra long ball-ended hex key easier to get in past the carbs.
That makes sense as a daily Joe like myself who uses for weekend road warrior battles would not be so fussed - unless of course I crack something up:(
If not a pain in the arse, and when you have time, could you drop a picture in so I can see for myself?
thx
Go to the full post
#1
Posted 20 February 2020 - 11:51 AM
Simply putting it back together and I will be damned if I can get those bolts to match up to the holes - millimeters off but might as well be a foot. I can get one side, centre and other side becomes a pain and no flex??
This is too simple to be having this problem but has anyone experienced the same?
I am going to have a tea tonight after work and back at it..
#2
Posted 20 February 2020 - 12:05 PM
It's a common problem caused by the unavoidable way in which metal moves when heated
The original welding creates a stress in the whole thing which manifests itself after repeated heating and cooling when in use
It's best not to elongate the hole one end as that will simply allow it to move even further in next time.
You say 'bolts' which is also what I use.
You'll have to put some kind of bar down onto somewhere strong. I use one of the webs on the block with A+ versions. It can be done alone, spring it, get a bolt in and don't release until the bolt is in several turns.
If they're studs, I have used my fly press to physically spring it past the point so as to get the hole centres back where they should be. But it will happen again
#3
Posted 20 February 2020 - 12:25 PM
Edited by postve, 20 February 2020 - 12:27 PM.
#4
Posted 20 February 2020 - 01:36 PM
It's a common problem caused by the unavoidable way in which metal moves when heated
The original welding creates a stress in the whole thing which manifests itself after repeated heating and cooling when in use
It's best not to elongate the hole one end as that will simply allow it to move even further in next time.
You say 'bolts' which is also what I use.
You'll have to put some kind of bar down onto somewhere strong. I use one of the webs on the block with A+ versions. It can be done alone, spring it, get a bolt in and don't release until the bolt is in several turns.
If they're studs, I have used my fly press to physically spring it past the point so as to get the hole centres back where they should be. But it will happen again
Glad to see I wasn't losing my mind the last time I went to put my LCB back on. I had a similar issue one side just didn't want to go on, it took a little effort and I was able to get it without pulling out a pry bar.
#5
Posted 20 February 2020 - 05:50 PM
Wrapping also causes issues.
#6
Posted 20 February 2020 - 06:00 PM
Hey nicklouse, good to hear you chime in. This was just me adding a generic manifold wrap to keep the heat down - not completed as just put on yesterday with steel tie rods (that is what we call them in Canada).
What are your thoughts - rubbish - or worth trying?
#7
Posted 20 February 2020 - 10:02 PM
Hey nicklouse, good to hear you chime in. This was just me adding a generic manifold wrap to keep the heat down - not completed as just put on yesterday with steel tie rods (that is what we call them in Canada).
What are your thoughts - rubbish - or worth trying?
What is the manifold?
for most performance UK manifolds wrapping is a total Waste of time as is shortens the life of the manifold by reacting with the steel making it brittle. It also just moves the heat to the tunnel and that can burn off the paint.
#8
Posted 20 February 2020 - 10:07 PM
Sorry - LCB - and I heard that before but my usage is limited to at most 2000K per year - summer months only over here..but..you are the 3rd person to warn me and may just rip it off - last guy had previous in ceramic costing and basically rusted all to hell.
Just have to get the damn thing back on for the weekend as going up to 6C which is balmy weather over here during this time
Edited by postve, 20 February 2020 - 10:08 PM.
#9
Posted 20 February 2020 - 10:23 PM
Long Center Branch manifold. Normally bent tubes welded onto flanges.
yours looks cast? Original? but does not look like it is?
#10
Posted 20 February 2020 - 10:52 PM
#11
Posted 20 February 2020 - 11:04 PM
#12
Posted 20 February 2020 - 11:26 PM
Personally I always use hex. head 5/16" UNF bolts 1.25" long. You do need the big washers for 4 of the bolt/stud positions and normal flat washers at each end bolt/stud.
The big advantage of bolts is the ability to remove the head without disturbing any of the engine steadies.
#13
Posted 20 February 2020 - 11:32 PM
No manifold washers?
Hell ya, just prepping.
#14
Posted 21 February 2020 - 09:39 AM
Long Center Branch manifold. Normally bent tubes welded onto flanges.
yours looks cast? Original? but does not look like it is?
Some of the cheaper LCBs use these cast flanges with tube welded into them:
http://www.minispare...|Back to search
#15
Posted 21 February 2020 - 09:49 AM
Long Center Branch manifold. Normally bent tubes welded onto flanges.
yours looks cast? Original? but does not look like it is?
Some of the cheaper LCBs use these cast flanges with tube welded into them:
http://www.minispare...|Back to search
Ahh not seen them.
1 user(s) are reading this topic
0 members, 1 guests, 0 anonymous users