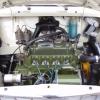
Drilling holes for engine number plate
#1
Posted 02 December 2006 - 01:46 PM
I wish to install the engine number plate on my engine, and have the correct drive pins. Except, when I try and drill, the block seems really hard and I cant get the drill to cut a hole. I know my drill bits are not blunt.
Has anyone tried drilling into the block in order to put in an engine number plate?
What can I do to make the holes?
Thanks
#2
Posted 02 December 2006 - 01:56 PM
sorry i couldnt be of any more help
#3
Posted 02 December 2006 - 02:23 PM
#4
Posted 02 December 2006 - 03:05 PM
I've had that problem so mant times and it took ages for me to work out why it wasnt drilling through the metal! Silly me!check the drill isnt in reverse!!!
#5
Posted 02 December 2006 - 07:12 PM
firstly engine blocks are super hard. Ive never drilled into a engine block b4
********!
They are soft as chease. The last part of your statement says you shouldnt be advising on something you havent done.
The big question i will ask is, why do you need to drill the block, the holes should be there. Unless the pins have not been removed and machined off, in which case you will find it very difficult as the pins are stainless and hard. Drill down the side. if you still find it hard then its one of two things, the bit is infact blunt or the rotation is incorrect. Use the drill on slow speed. Cutting compound is not nescisary, but can help the life of the drill bit, it does not magicaly make blunt bits cut better.
#6
Posted 02 December 2006 - 07:26 PM
#7
Posted 03 December 2006 - 03:02 AM
they have all sorts of bits on there!! tungsten tippers, with diamond cut edges, all sorts!!
#8
Posted 03 December 2006 - 03:11 AM
had some tungsten coated ones before (expensive) used one snapped. Returned it and got a set of HSS ones from coopers down the road.
#9
Posted 03 December 2006 - 03:14 AM
#10
Posted 03 December 2006 - 03:17 AM
I prefer my HSS ones. I know the quality of the brand I buy. It's not great but it works for me.
Sorry for going off topic by the way.
#11
Posted 03 December 2006 - 02:43 PM
what he said!!
Edited by fikus01, 03 December 2006 - 02:43 PM.
#12
Posted 03 December 2006 - 05:14 PM
There are tungsten-carbide tipped drill bits for use in very hard materials. Similar but crude versions are used to drill holes in masonry. The coated bits (typically gold in color) are pushed all over the place now with promises of longer life. That coating may help on soft metals and wood but I haven't seen any significant change on ferrous materials.
Regarding the block... I've never seen one that's particularly hard. They are, after all, cast iron, not steel. As others suggested, use a first rate drill bit, put some engine oil around the spot you want to drill, make sure you've center punched it first so the bit won't walk, and make sure your drill is in FORWARD, not reverse. ALSO, drill a slightly smaller pilot hole first if you're having any difficulty. Follow the pilot hole drill with the size you actually need for the drive pins.
#13
Posted 03 December 2006 - 05:43 PM
1 user(s) are reading this topic
0 members, 1 guests, 0 anonymous users