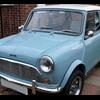
Leyland Mini 1000 1980 Restoration Project
#31
Posted 01 November 2011 - 07:04 PM
take it you have a spot welder to speed things along ?? Very neat work, love it !!
Graham
#32
Posted 02 November 2011 - 08:27 PM
#33
Posted 02 November 2011 - 10:00 PM
Edited by grahama, 02 November 2011 - 10:00 PM.
#34
Posted 02 November 2011 - 10:59 PM
Dave
#35
Posted 03 November 2011 - 07:41 PM
Hi Davie Boy, thanks for the interest. Those over sills are nasty things! They don't let the inside of the sills breath and trap any moisture in. Both of my minis had them and the first had a piece of masking tape on inside (in perfect condition) with the name of the garage who fitted them on it, but the panel had rusted around it!
#36
Posted 03 November 2011 - 09:27 PM
Hope you don't mind me asking but you but out all the inner sill. Took the floor out all the way from front to back. Did you already have the panel to know where to cut and just marked it out? Or did you just cut out the rust. Then see what you have left? Also once cut out did the mini hold Shape ok without extra support?
If yet could help that would be great!
Dave
#37
Posted 04 November 2011 - 07:57 PM
#38
Posted 04 November 2011 - 11:59 PM
Rear bracket.
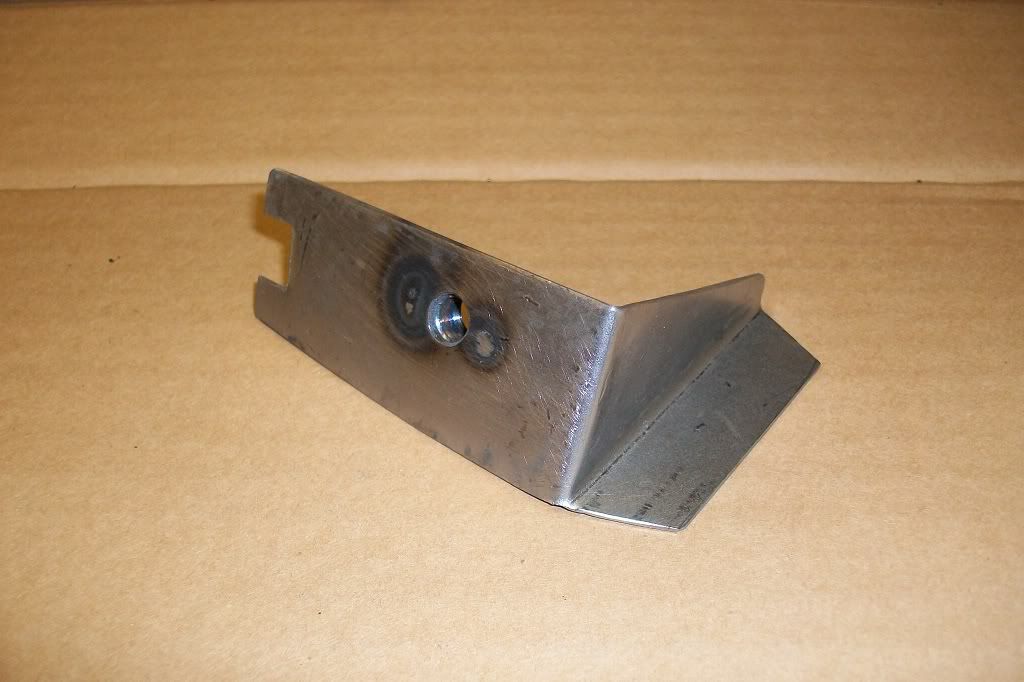

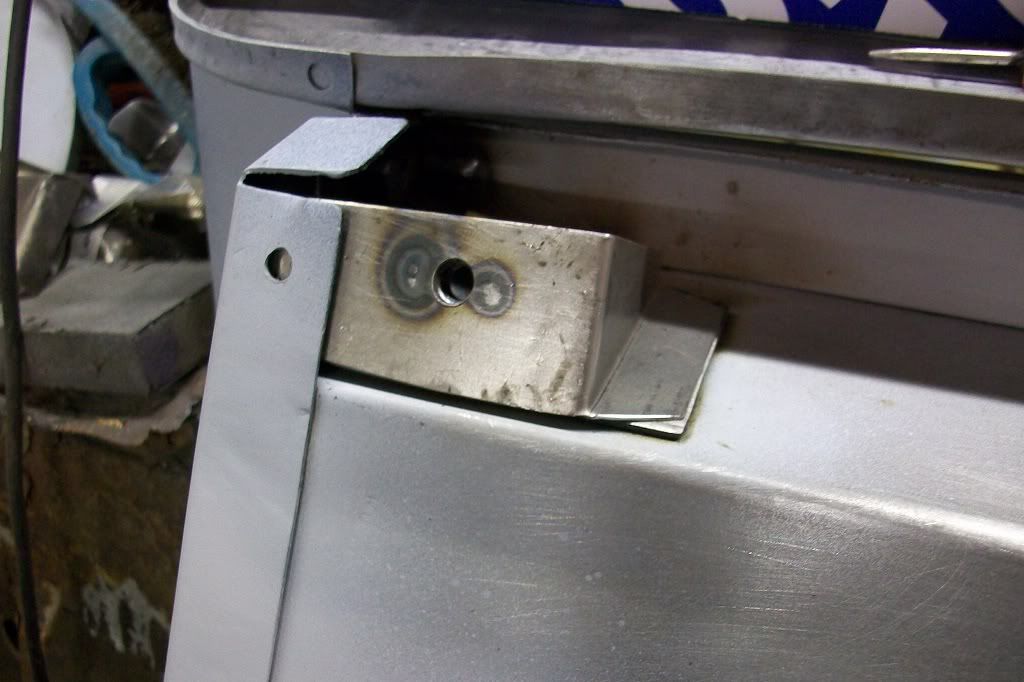
Rear slinging bracket fitted. This is a heritage part 24A42 for right hand.
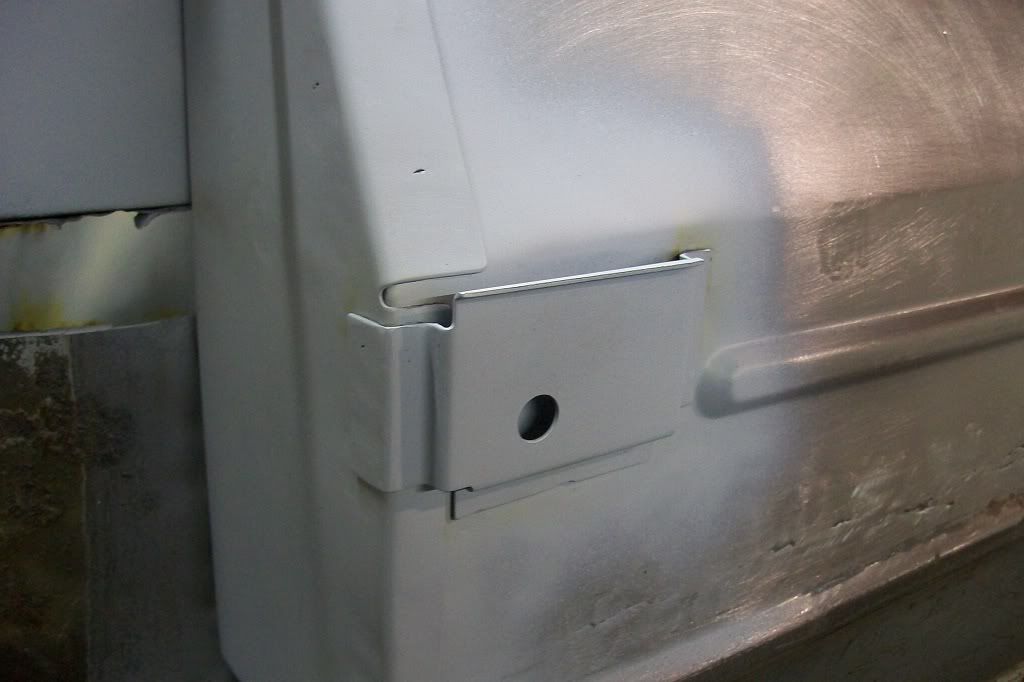
Drilled the spot welds out of the right hand inner wing and removed.
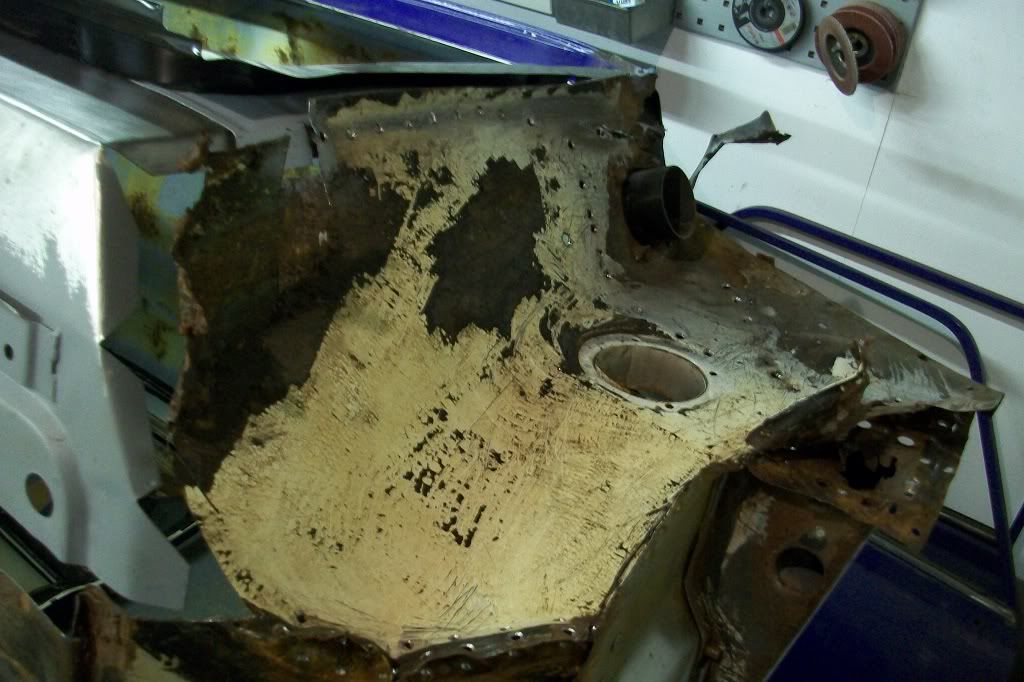
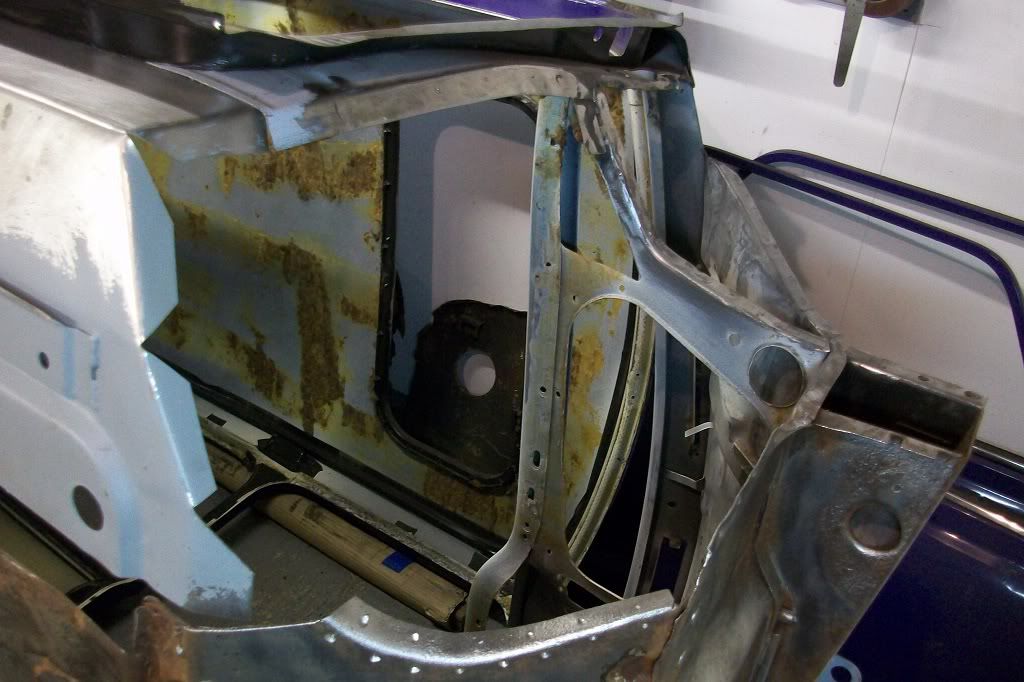
Right hand footwell removed.
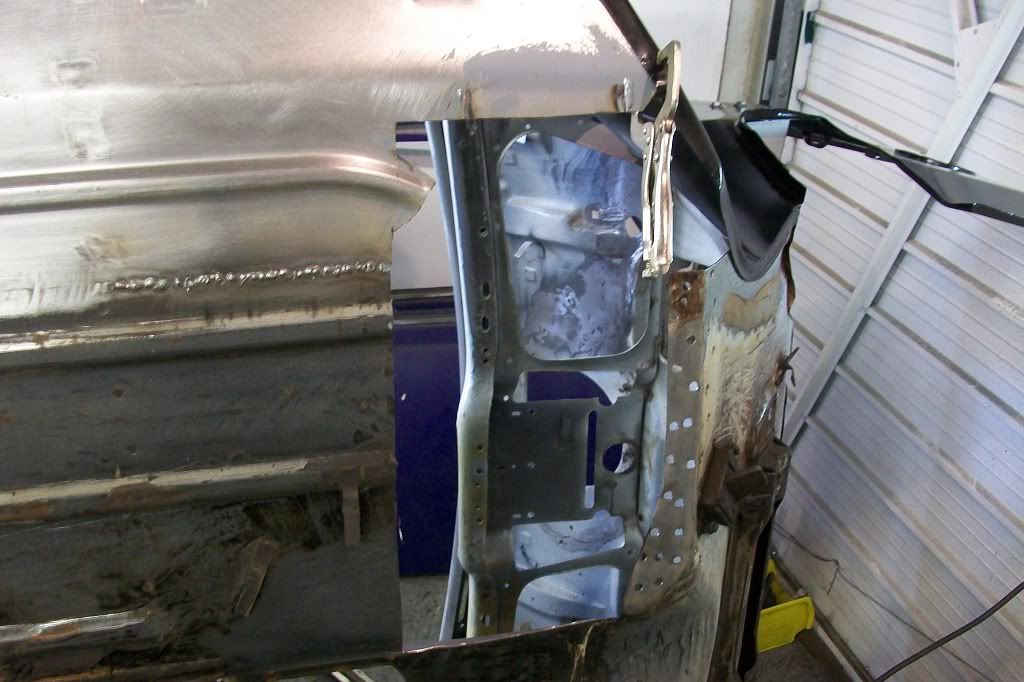
Offered up the new inner wing, complete with A panel, to check fit. Heritage panel ABD36006 for right hand.
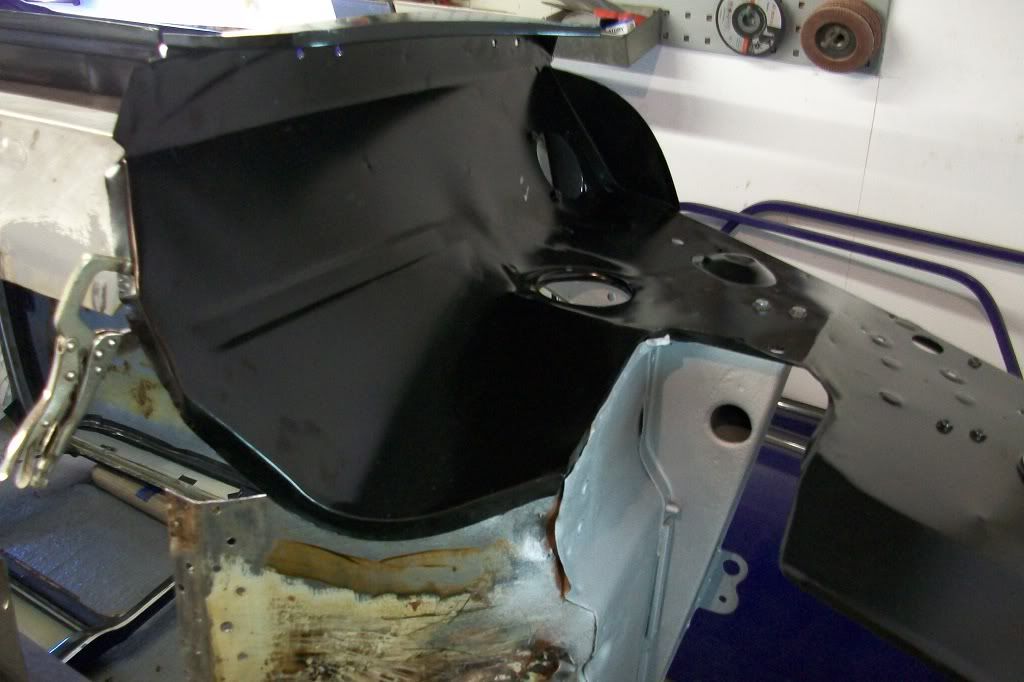
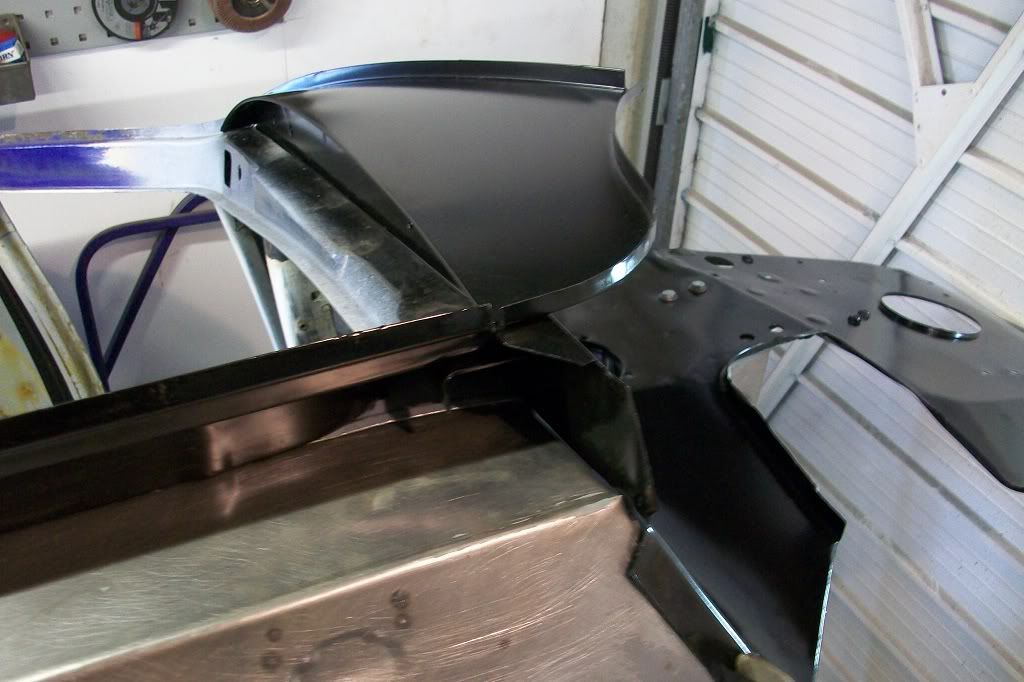
With the inner wing in place, I used the new outer sill to line up the jacking point, removed the outer sill and welded in the jacking point. Heritage part 14A8374 right hand.
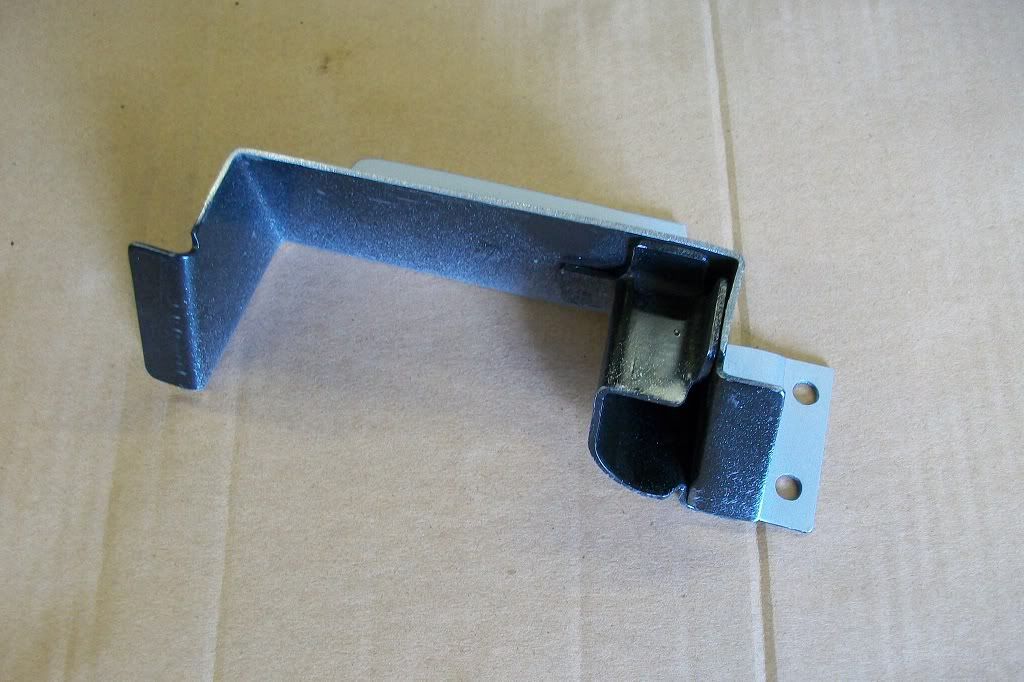
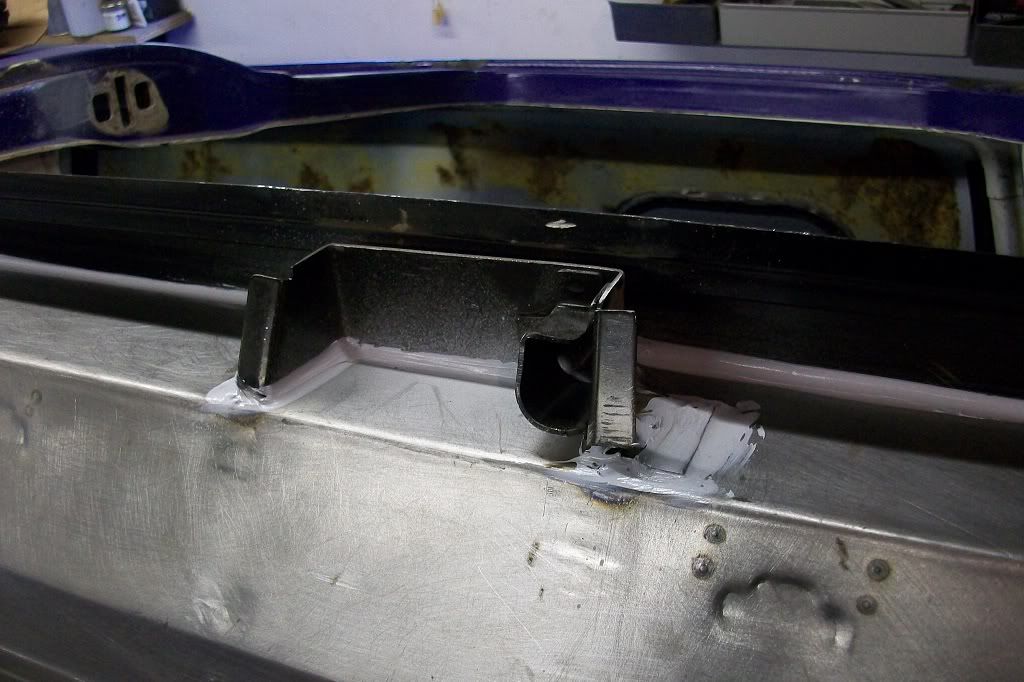
Seam sealed inside sill.
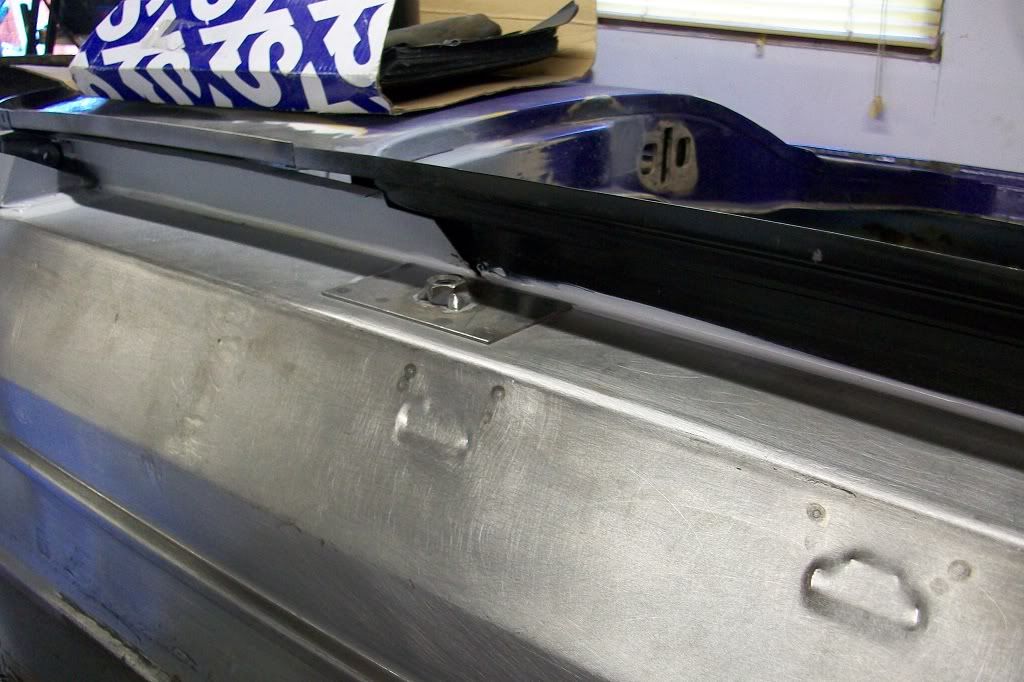
Fabricated the front reinforcing bracket from a cardboard template of the old bracket.
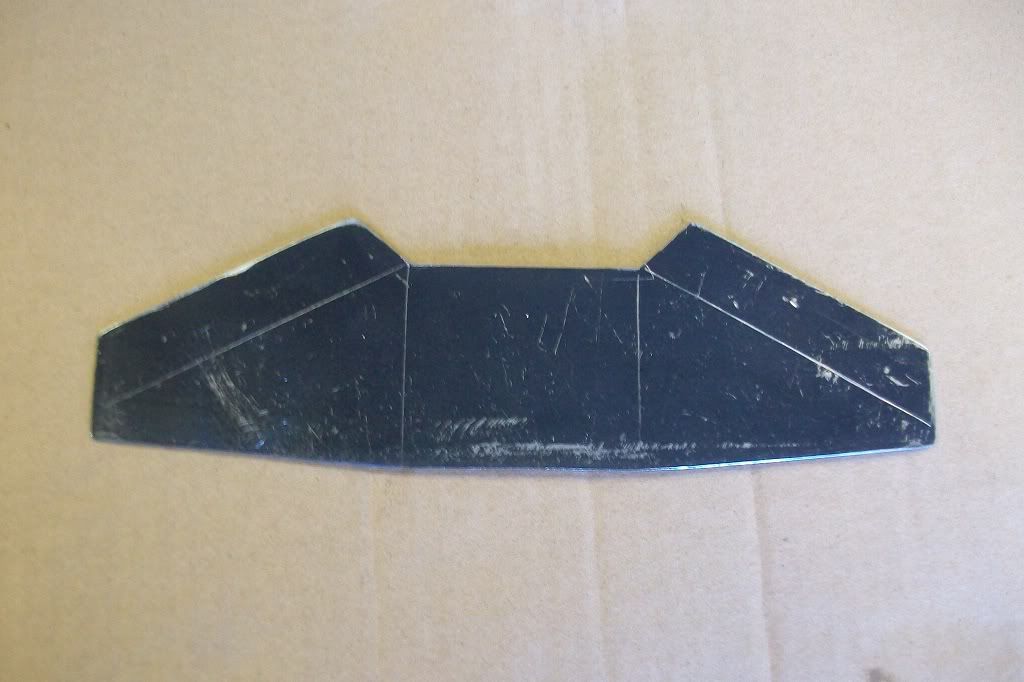
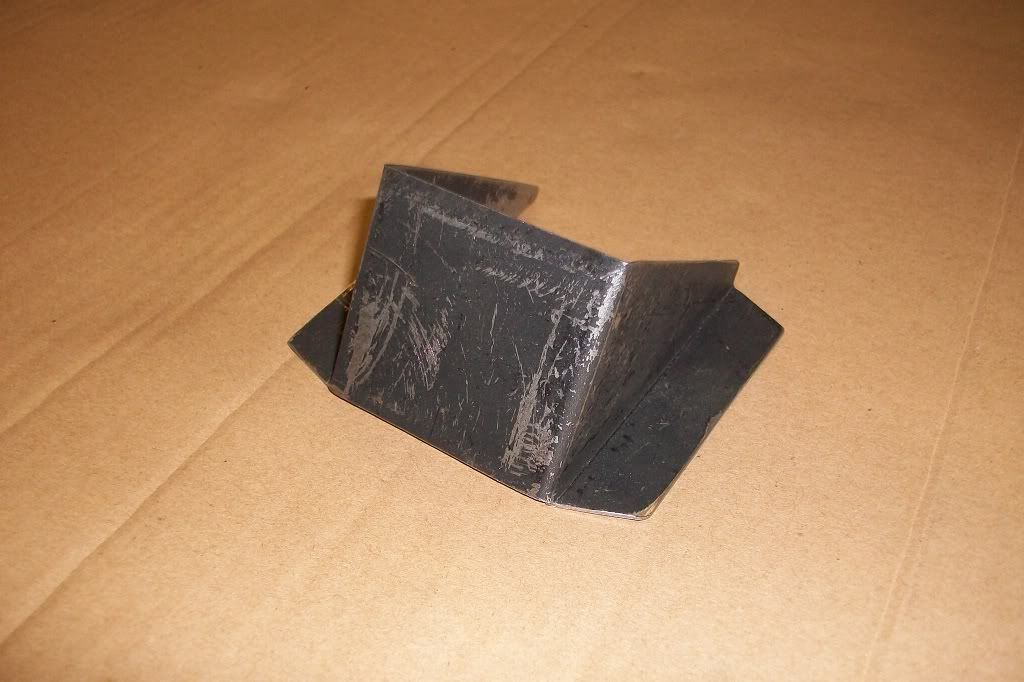
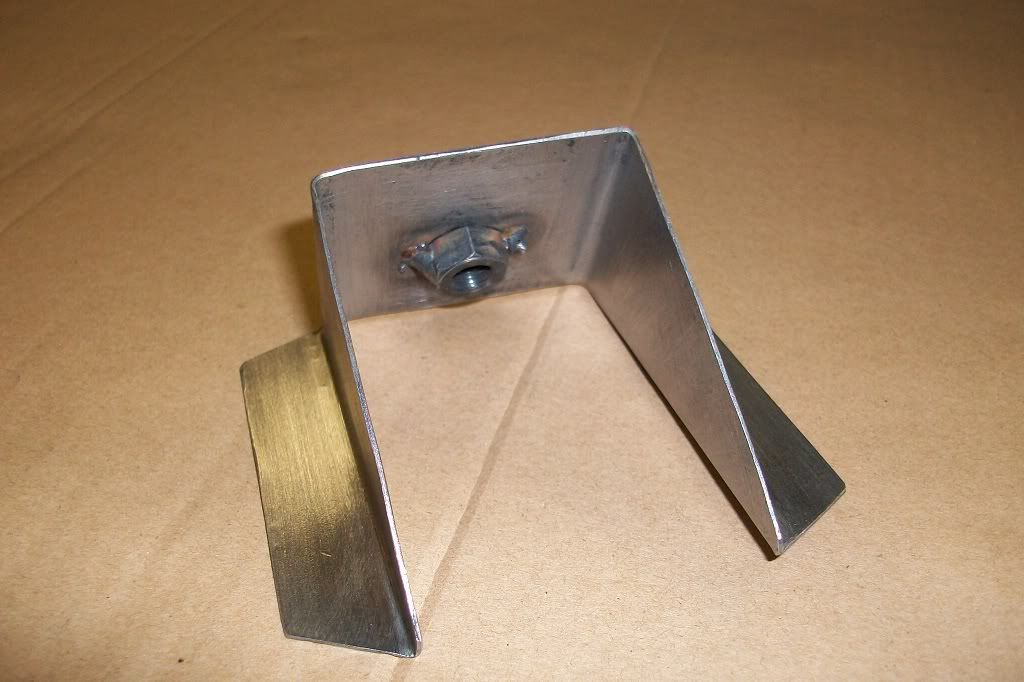
And spot welded in whilst I could gain access with the inner wing removed.
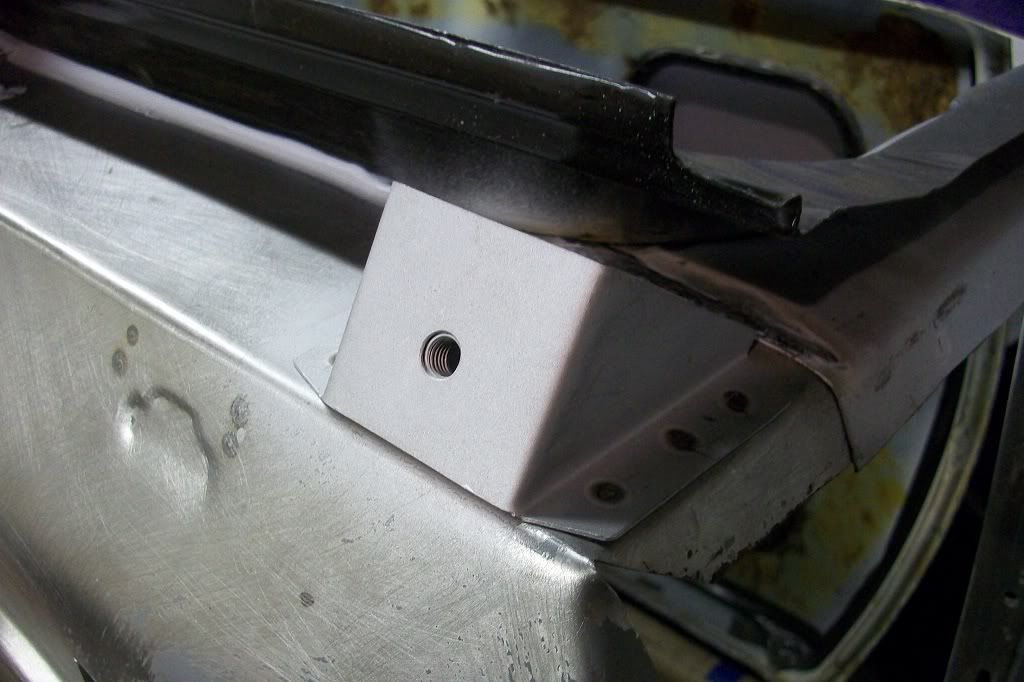
Thats it for now, thanks.
Edited by minifcd, 05 November 2011 - 12:03 AM.
#39
Posted 05 November 2011 - 12:56 AM
#40
Posted 05 November 2011 - 10:41 AM
Does that the new inner wing, complete with A panel prevent some of the adjustment needed when fitting the front wings, bonnet, doors etc? Is the A panel already welded to the inner wing?
I ask since I had to beat the A post forward a bit to enable enough clearance for the rear of the driver's door. The A panel can slide across the A post before welding to allow some adjustment. An all-in-one ready welded panel might not allow this. I'm thinking in advance of the passenger side.
Thanks,
Adam
Edited by BusheyTrader, 05 November 2011 - 10:42 AM.
#41
Posted 05 November 2011 - 03:40 PM
So i guess you always buy the panels (or you make them)

Must say you really do make it look easy!
Keep up the good work. the car is really taking shape now!
Fantastic to see how to do it properly!
#42
Posted 05 November 2011 - 04:36 PM
Hugh
#43
Posted 06 November 2011 - 11:09 AM
Thanks dave, yes I buy, (or make) any panels before cutting out, the old so as not to go wrong.
Hugh thanks for your kind words, I'll post the next two months work in the next few days!!
#44
Posted 10 November 2011 - 07:22 PM

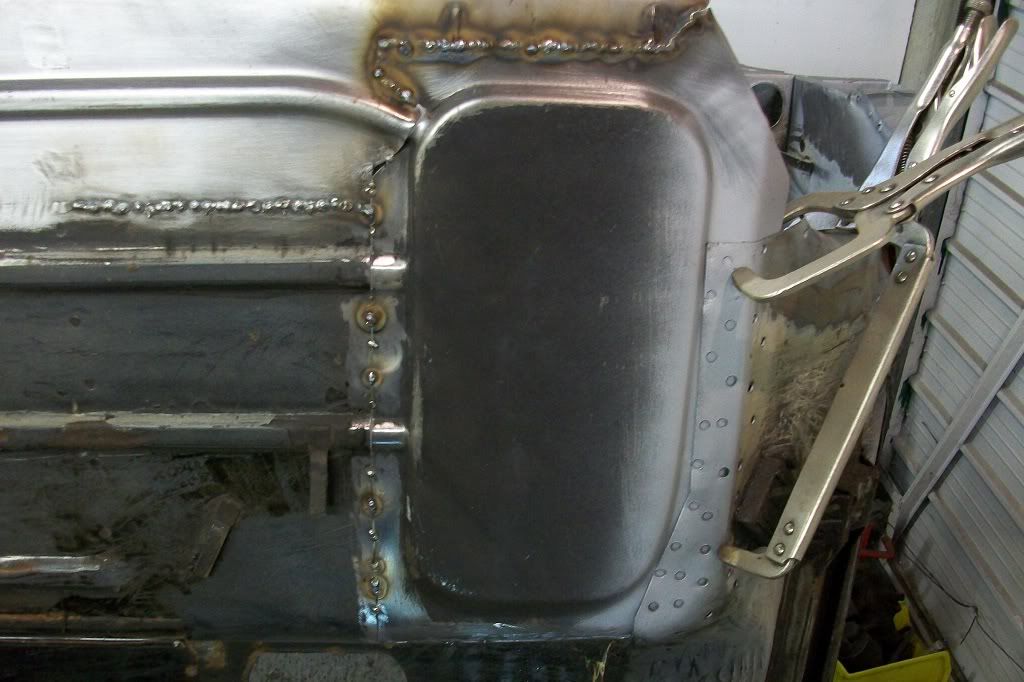
A repair piece had to be made for the corner of the toe board and welded in.
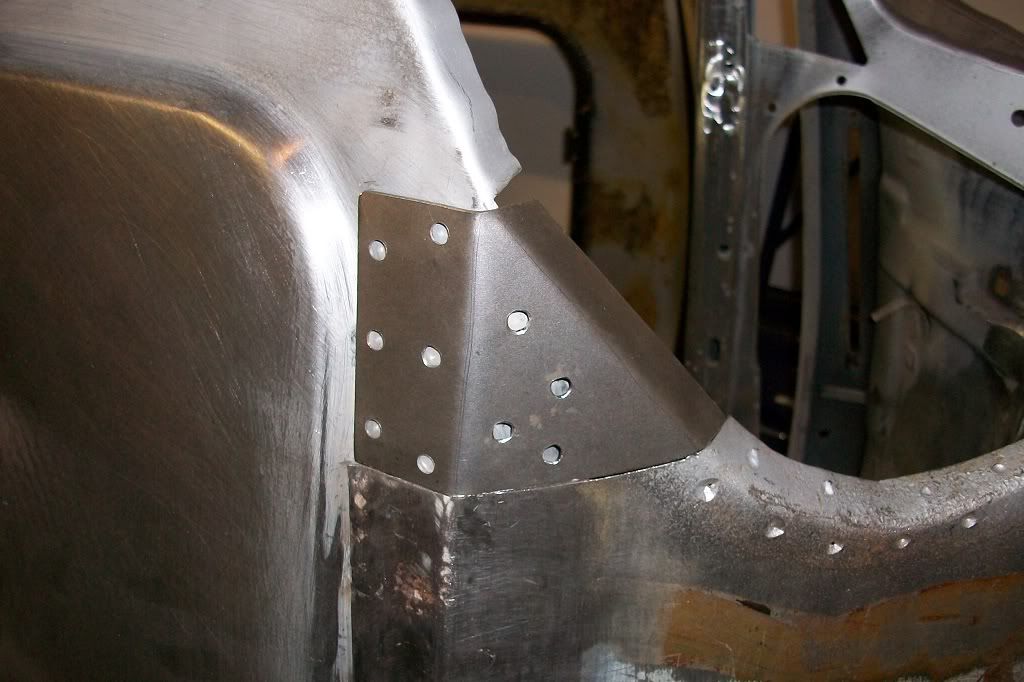
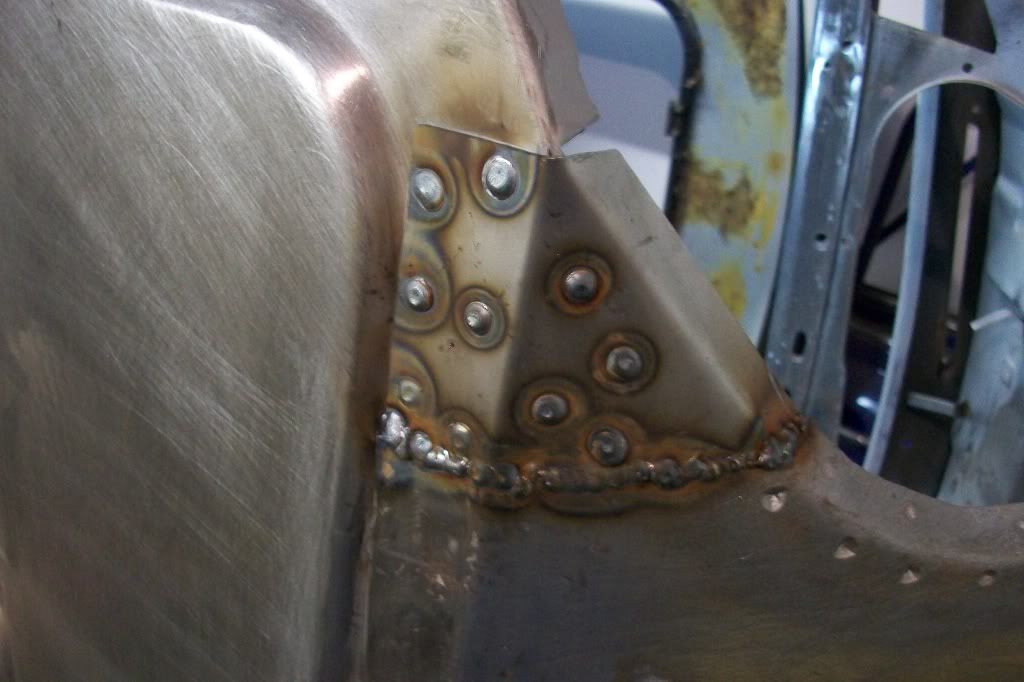
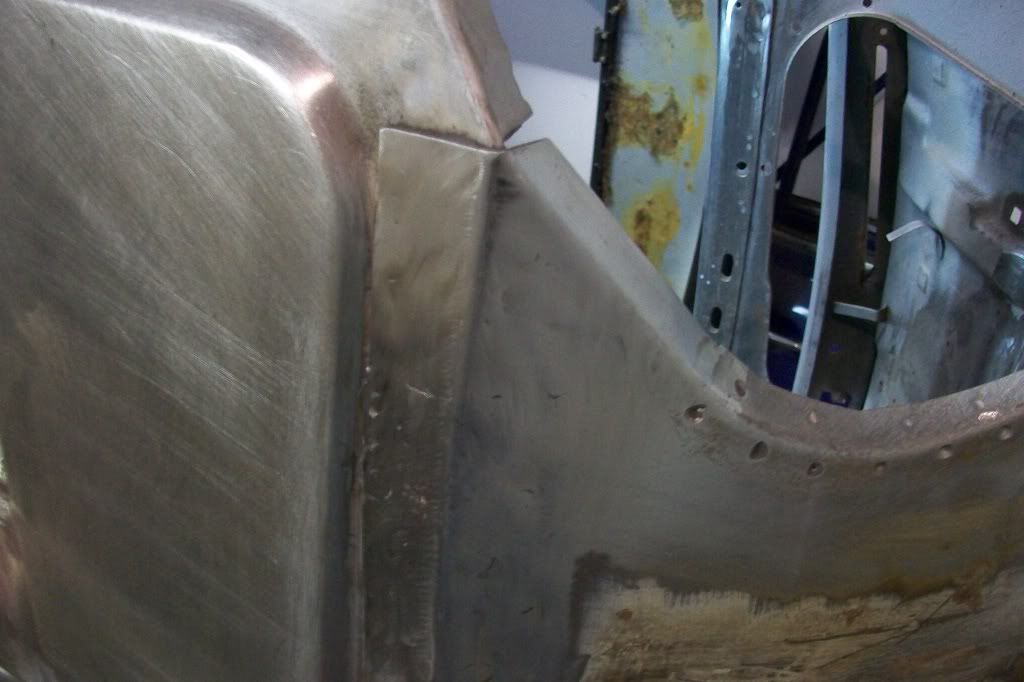
Before the inner wing was fitted I had to make a new piece for the heater ducting to fit to, as the new panel does not come with it and the old panel was too badly corroded to re use. A measurement was taken from the old piece and a template was made from card. This was transfered to metal and three impressions were added at the correct distance, using the end of a panel pin hammer and a large hammer, to punch the shape into another piece of thicker metal below, with an oval shaped hole in it.
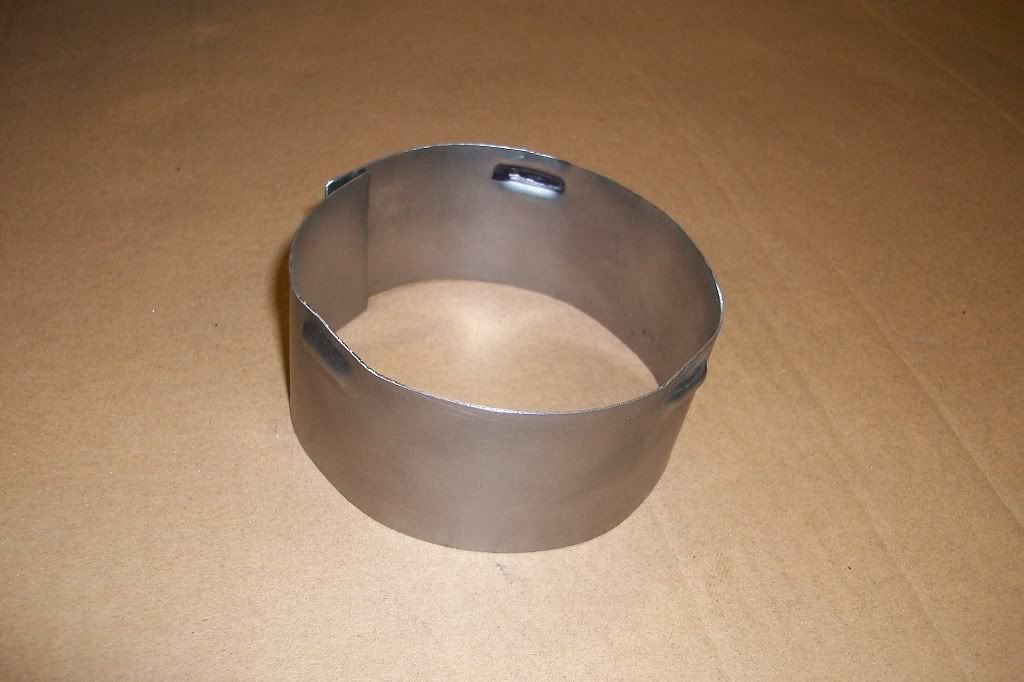
Spot welded to new panel.
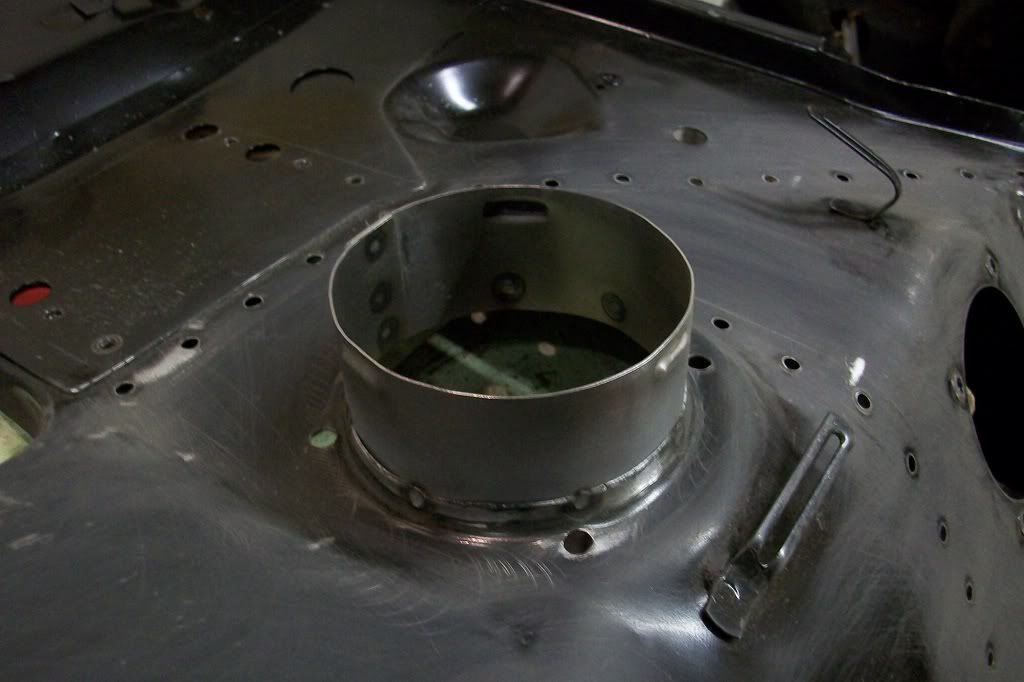
The inner wing was then fitted and plug welded into place.
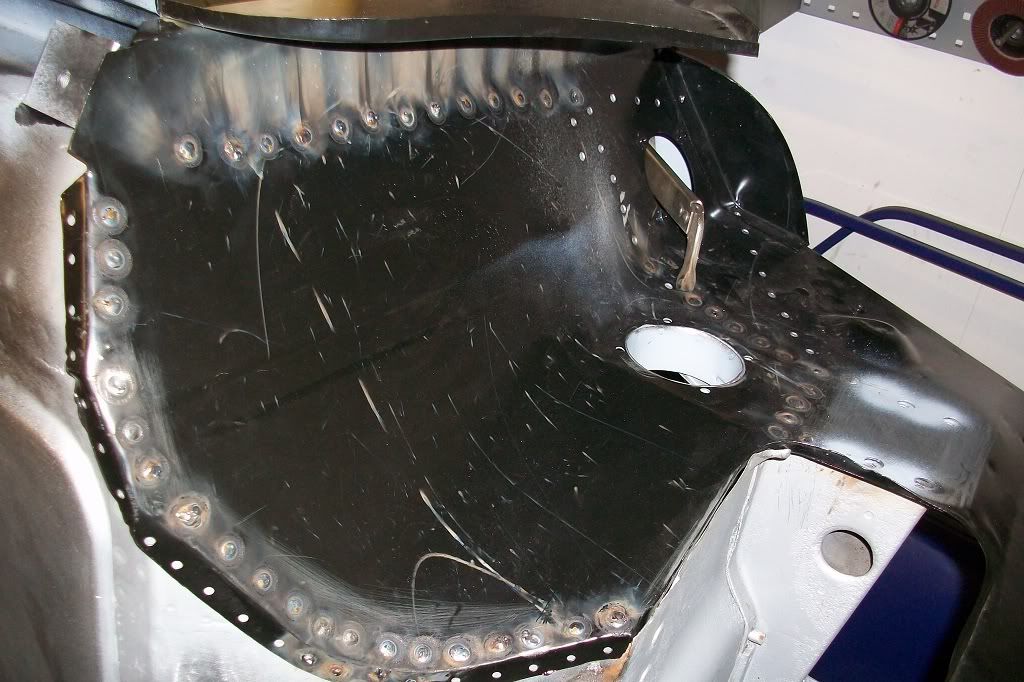
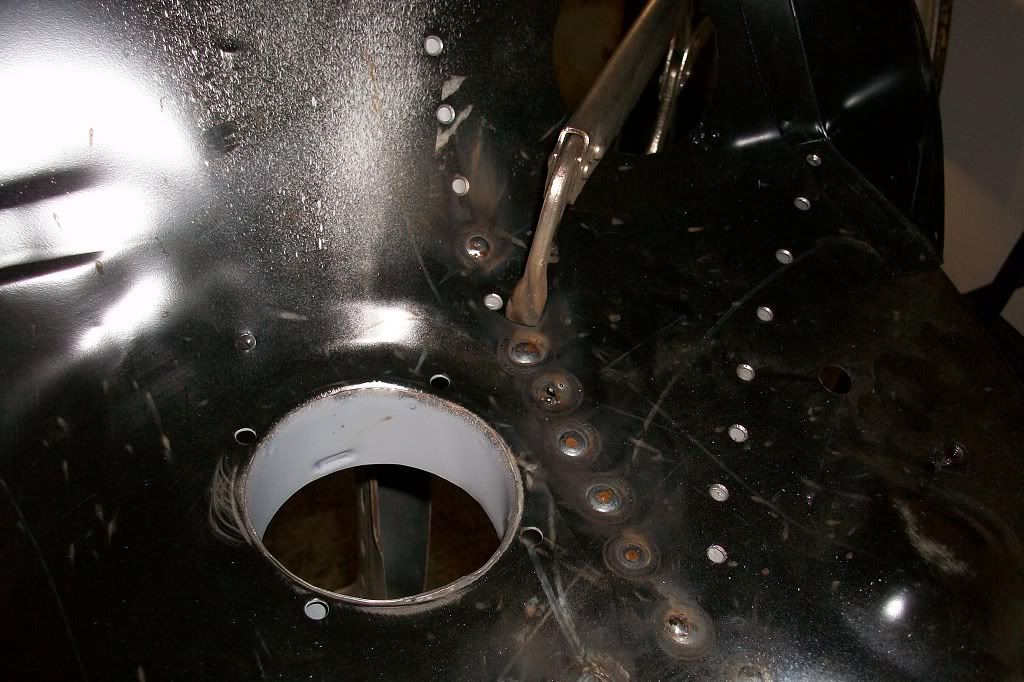
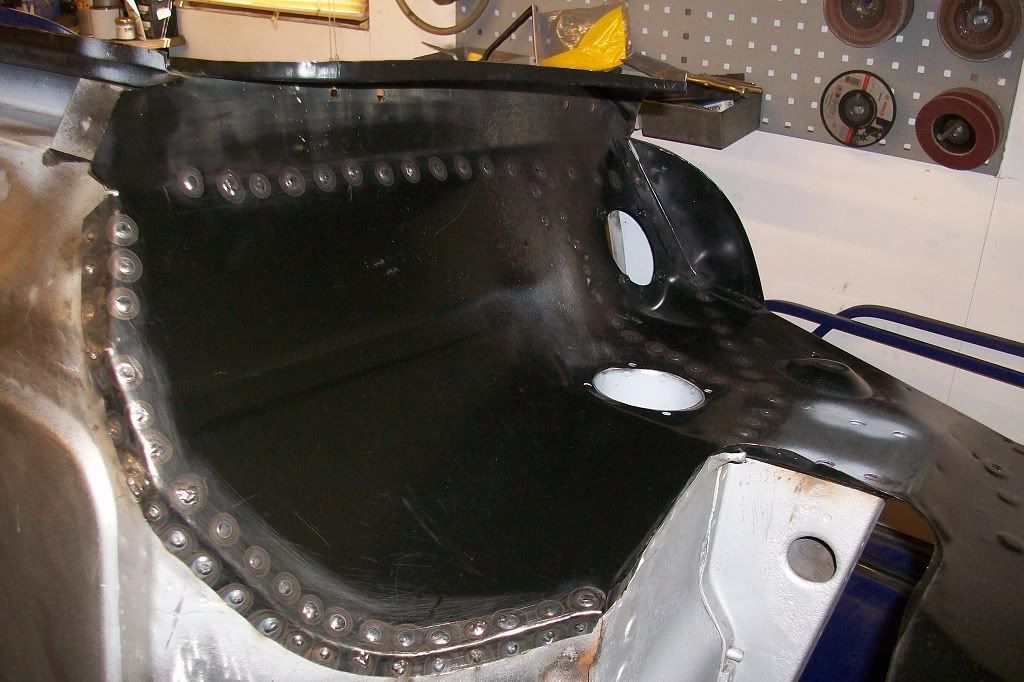
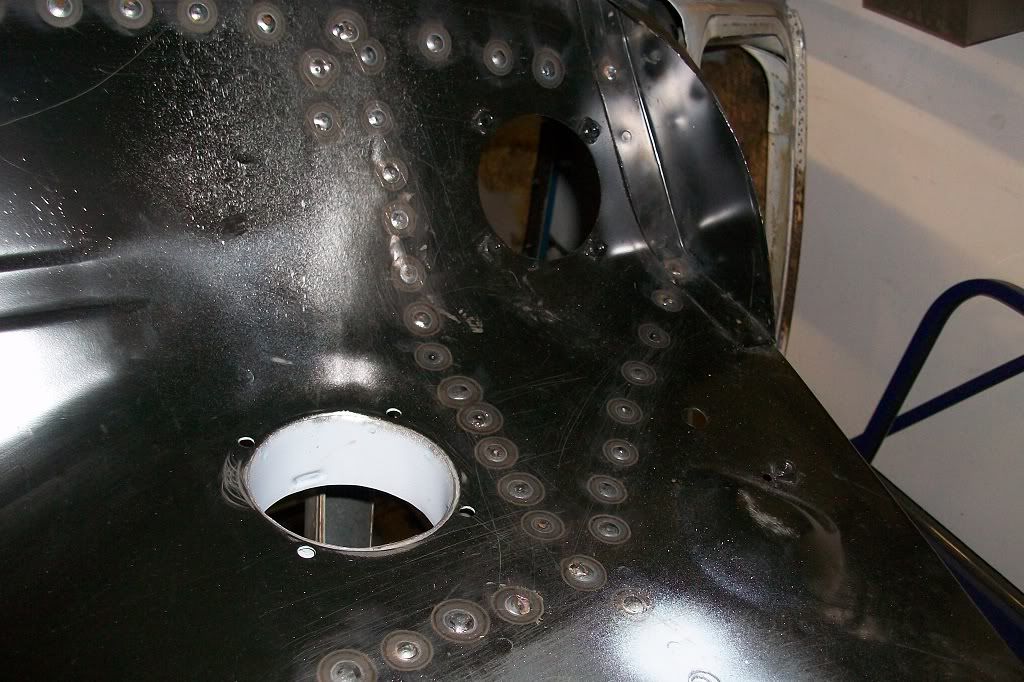
Welded at the A post,
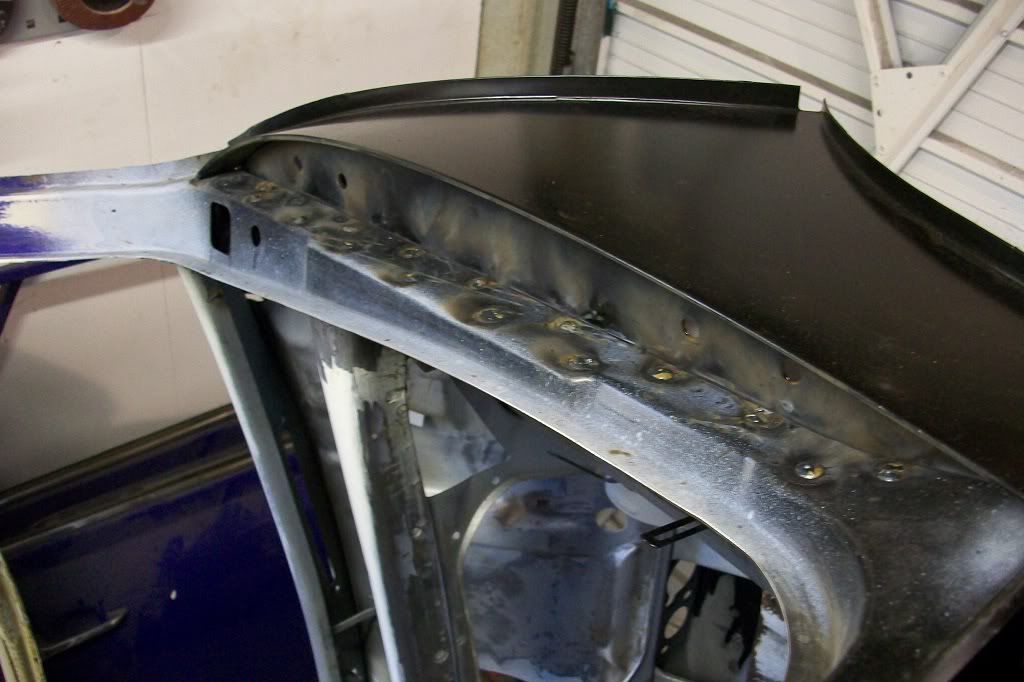
and ground down.
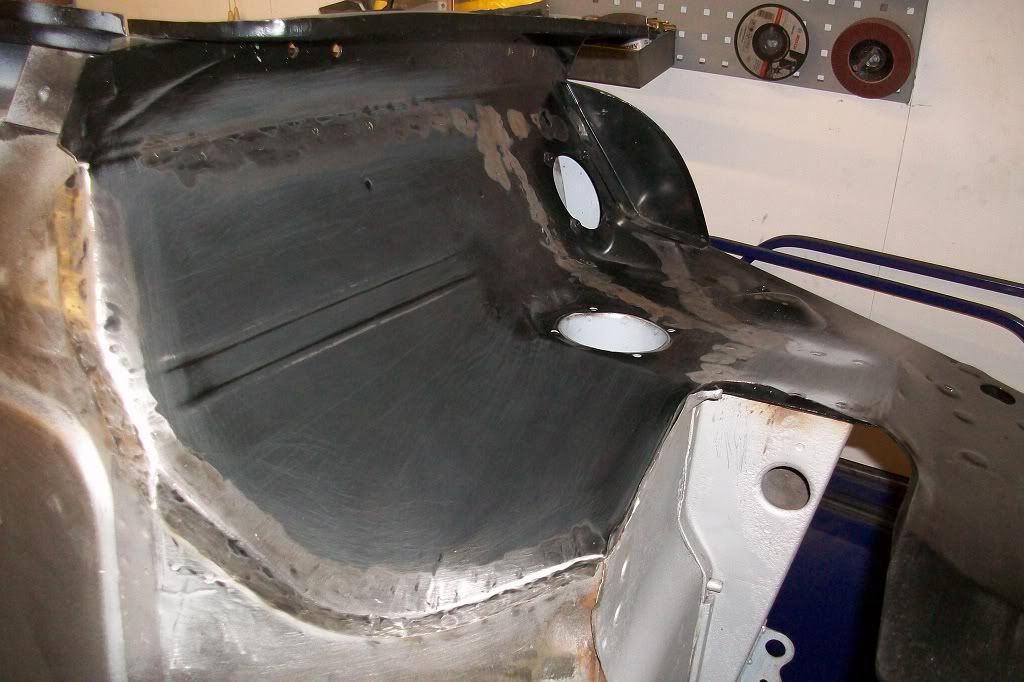
With the footwell and inner wing done, I then painted the inside of the inner sill.
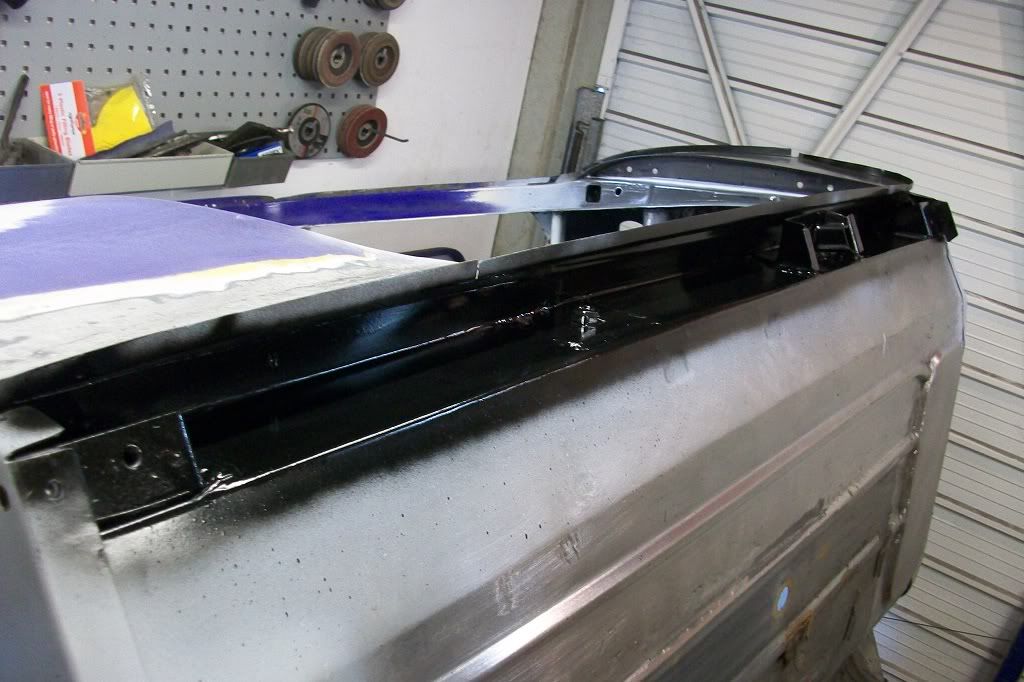
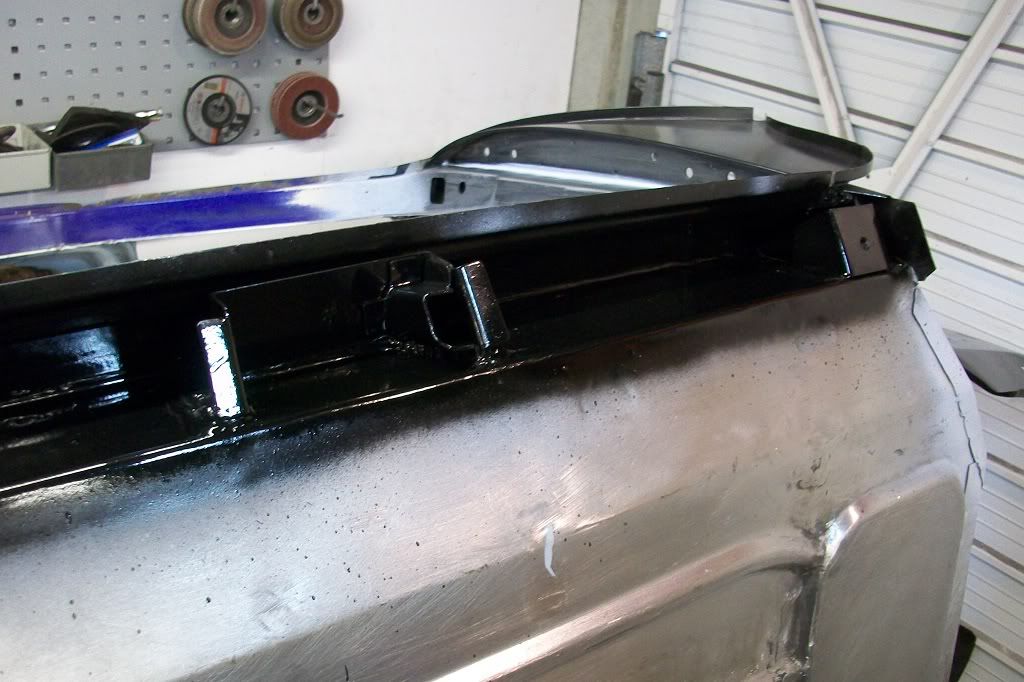
The outer sill was then welded on. A heritage panel 14A9534, plug welded to the inner sill and spot welded to the door step and rear quarter.
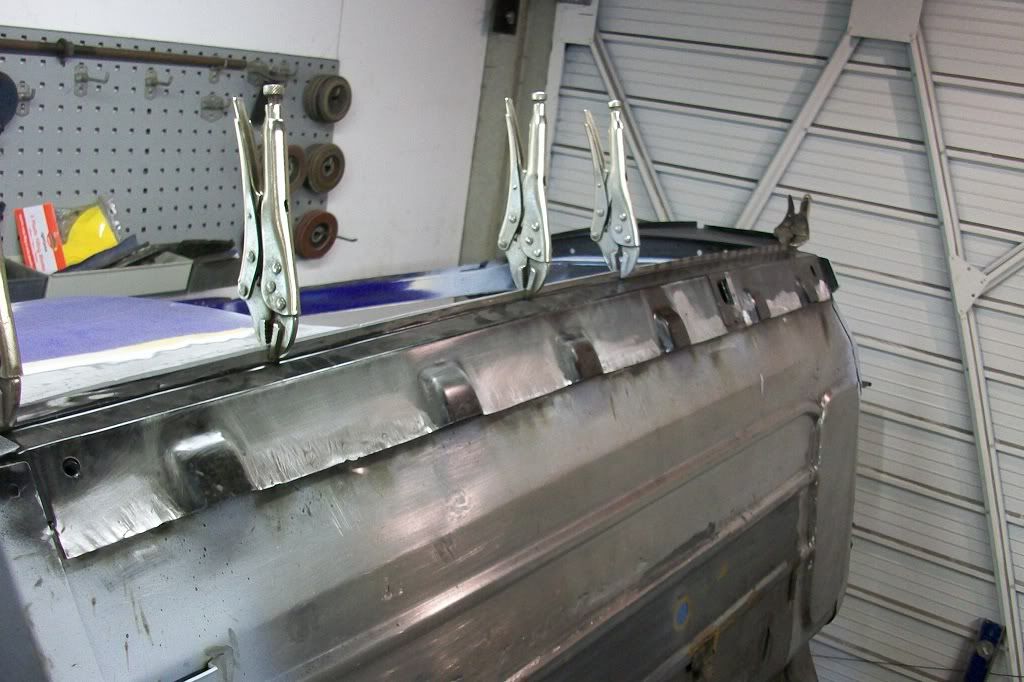
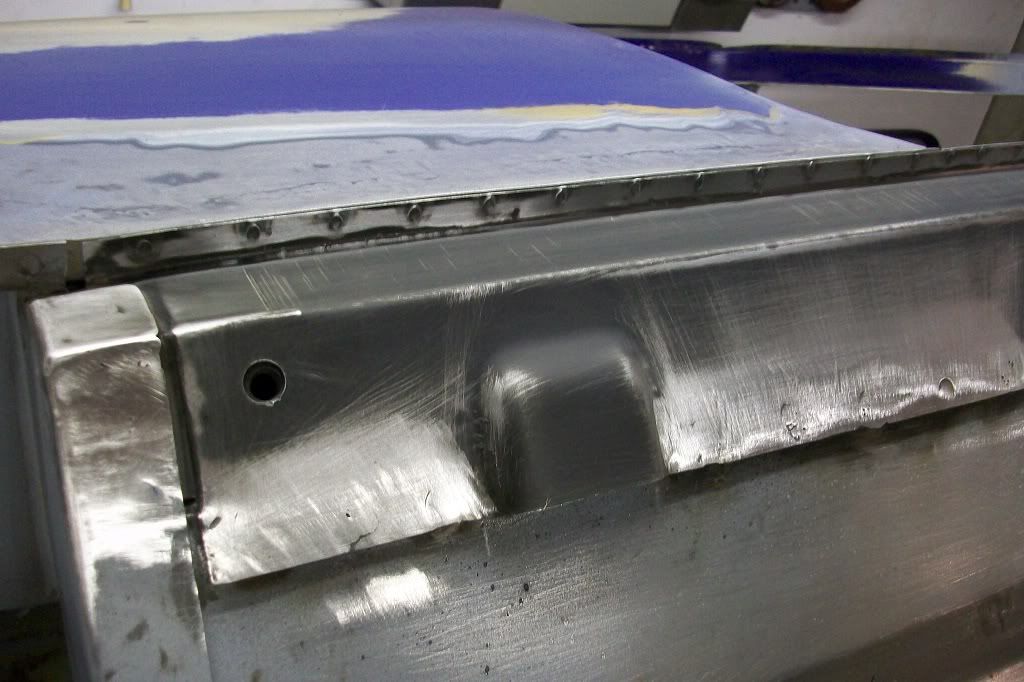
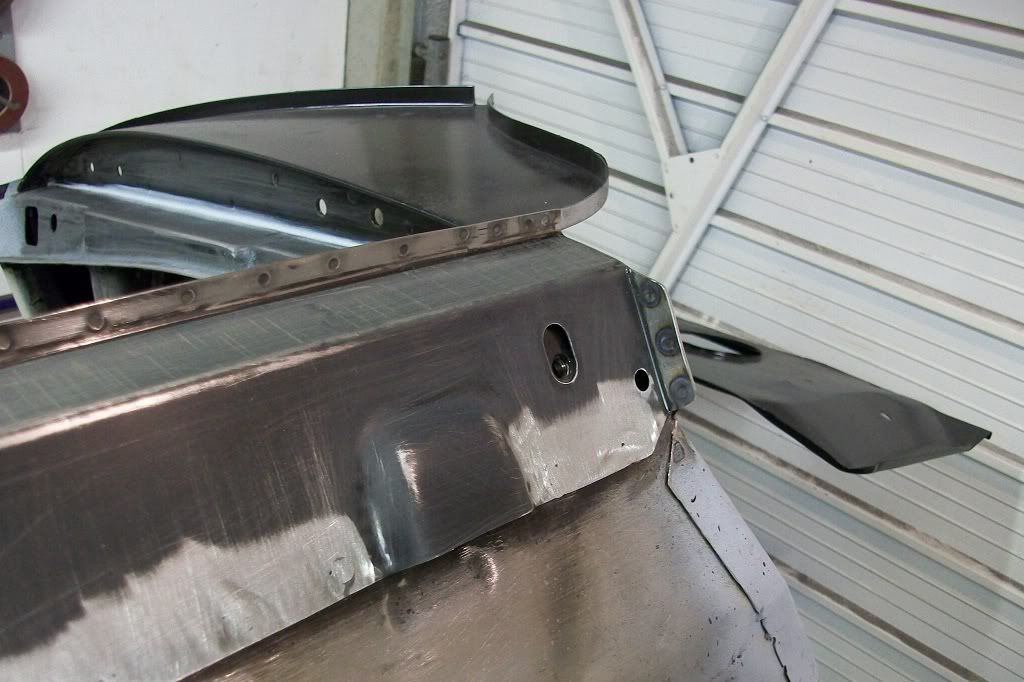
Thats it for now. Thanks.
#45
Posted 10 November 2011 - 09:40 PM
0 user(s) are reading this topic
0 members, 0 guests, 0 anonymous users