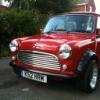
Binning The Bullet Connectors
#1
Posted 31 March 2009 - 07:08 PM
Any issues with this?
Any tips?
H
#2
Posted 31 March 2009 - 07:09 PM
#3
Posted 31 March 2009 - 08:39 PM
Failing this I would look for some alternative connectors to crimp into place, again with some copper grease. Be aware that alot of those connections are for headlights/spots which carry a bit more of a current than many other circuits and the wires will be a bit thicker so check the size of any connectors you do go for

#4
Posted 31 March 2009 - 08:48 PM
why not solder and heatshrink?To be honest I wouldn't try soldering and heat shrink on this issue. Have you tried giving them a good clean up, including the inside of the bullet sockets, and using a bit of copper grease on them to stop future issues?
Failing this I would look for some alternative connectors to crimp into place, again with some copper grease. Be aware that alot of those connections are for headlights/spots which carry a bit more of a current than many other circuits and the wires will be a bit thicker so check the size of any connectors you do go for
#5
Posted 31 March 2009 - 08:54 PM
#6
Posted 31 March 2009 - 08:58 PM
so heatshrink over new connectors would be the way forward?what happens if you need to remove them? bit buggered lol, you can buy new multi spade connecters for like 40p a piece
#7
Posted 31 March 2009 - 09:00 PM
why not solder and heatshrink?
Well, in theory it is fine, but it is possible to get a 'dry joint' when soldering and even with heatshrink on there it could end up corroding, plus vibrations might lossen the connection and so on. I'm being quite pedantic about it, and yes it would probably be fine for 1000s of miles, but later on it could turn out to be nasty to trouble shoot if problems do arise.

#8
Posted 31 March 2009 - 09:01 PM
alot easier than solder and heatshrink imho just cut nd crimp n ur done easy remove aswell
#10
Posted 31 March 2009 - 09:03 PM
so heatshrink over new connectors would be the way forward?
Depends on the connectors, but that's the idea. Belt and braces approach - proper crimp terminals (not the ones with the insulation already on them in blue yellow or red), wires crimped in using a good crimping tool, soldered well with a good flow of solder through the wires, then heat shrink over the crimp terminal root (ie the bit where the wires go into the back of the crimp terminal) and finally the flexible plastic sheathing you get for the crimp terminal....
#11
Posted 31 March 2009 - 09:05 PM
Heatseal pre-insulated terminals
I will be using these on my loom.
To be clear about my post, I was not referring to these as I have not used them before. I meant the ones you get from Maplins, not these heat seal ones... never tried those so can't judge!
#12
Posted 31 March 2009 - 09:38 PM
Heatseal pre-insulated terminals
I will be using these on my loom.
Thanks for this. I might go down this route after all. Nice.
I know it will be a pain should I need to remove it all but if it means a fully weather proof joint to end the weird goings on that currently plague the electrics at the front, then its acceptable!
Any tips on where to move the bundle of wires at the front to? They are currently attached to the centre grille support.
#13
Posted 31 March 2009 - 09:43 PM
Your wires are obviously getting wet/damp being at the front by the grill, you can however buy split plastic loom covers. Sort of like 'wire tidies' they will protect your wires from the elements a bit better and make everything look better too.
When I did the wiring for my spotlights and horn I got a hose pipe and sprayed the grill looking at where the water collect, drips and flows etc - I was then able to find best spot to route the wires and wrapped them as well as covered them in the plastic split loom cover. Use a few cable ties and it remains pretty water tight.
#14
Posted 31 March 2009 - 09:47 PM

#15
Posted 31 March 2009 - 09:50 PM
1 user(s) are reading this topic
0 members, 1 guests, 0 anonymous users