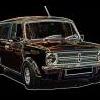
Jayare's Clubman Estate Rebuild & Conversion
#61
Posted 05 July 2010 - 10:34 PM
Kam - glad you enjoyed reading through so far - still a long way to go though!
JR
#62
Posted 05 July 2010 - 11:36 PM
Good on ya mate! Flip fronts are cheating!
#63
Posted 06 July 2010 - 05:38 PM
Al
#64
Posted 06 July 2010 - 10:34 PM
JR
#65
Posted 18 July 2010 - 12:02 AM
Anyway - these are the panels I picked up:
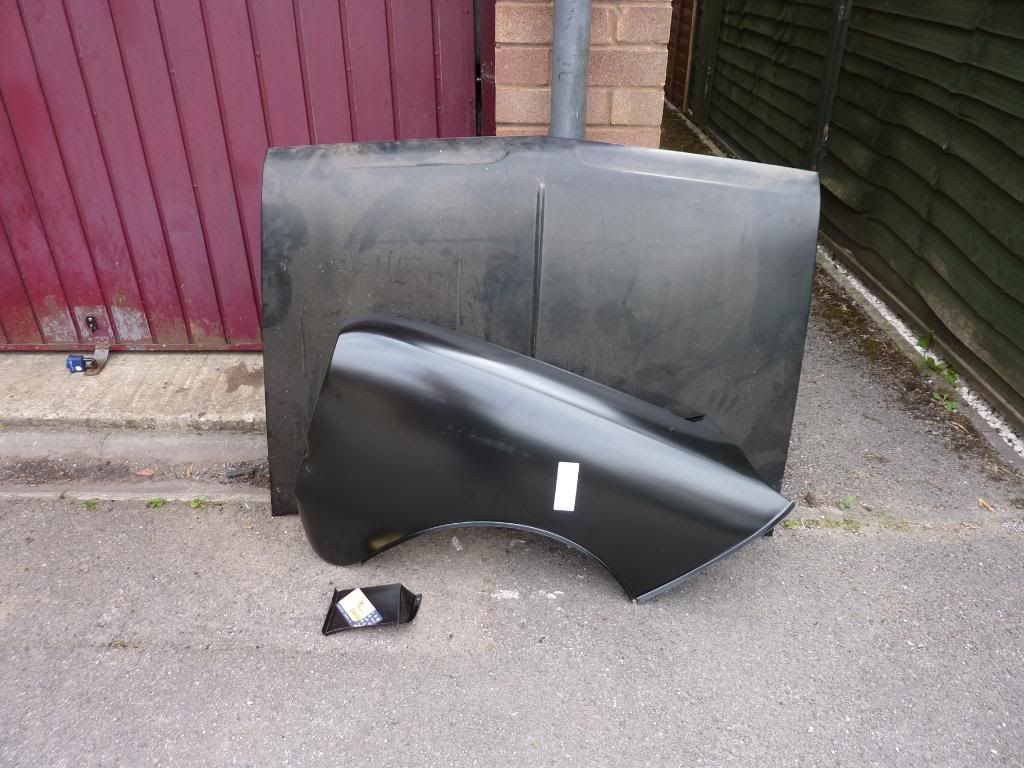
Today I spent a few hours in the garage after a lie in and chill-out morning. I decided as I still haven't got any 1.2mm steel sheet that I would start at the back of the floorpan instead of the front. I removed the closing/stiffening panel from the top of the inner sill in the pocket. The rear end of this had gone all crispy so using CAD made up a section and welded it together:
CAD in action:
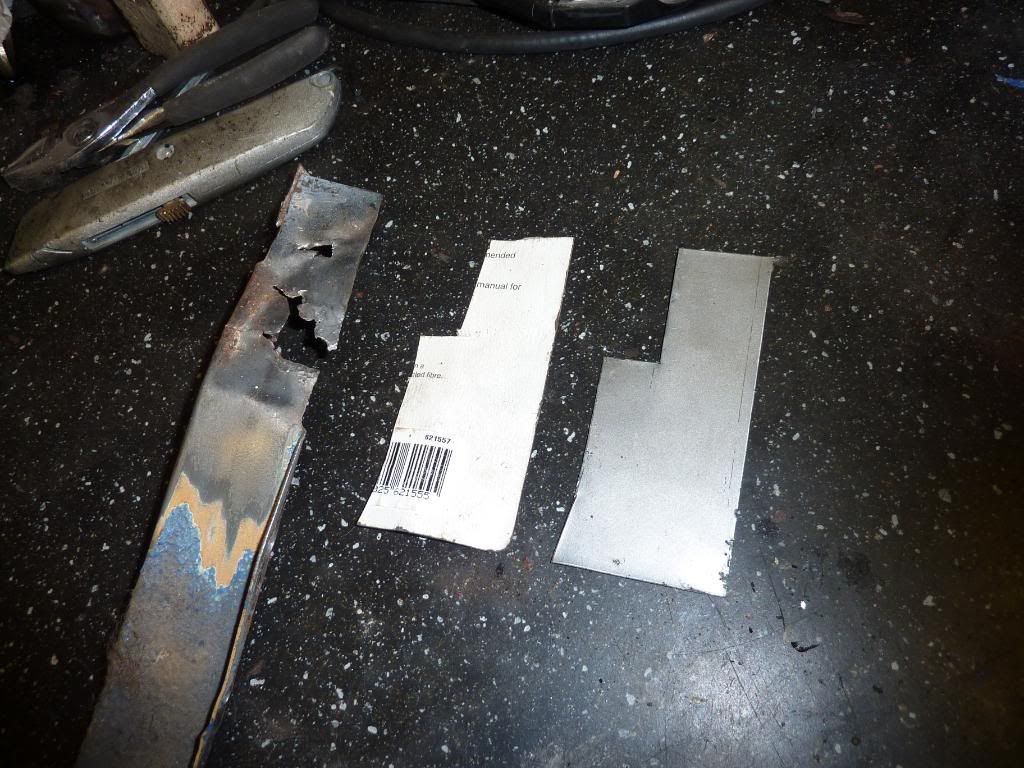
Repaired panel:
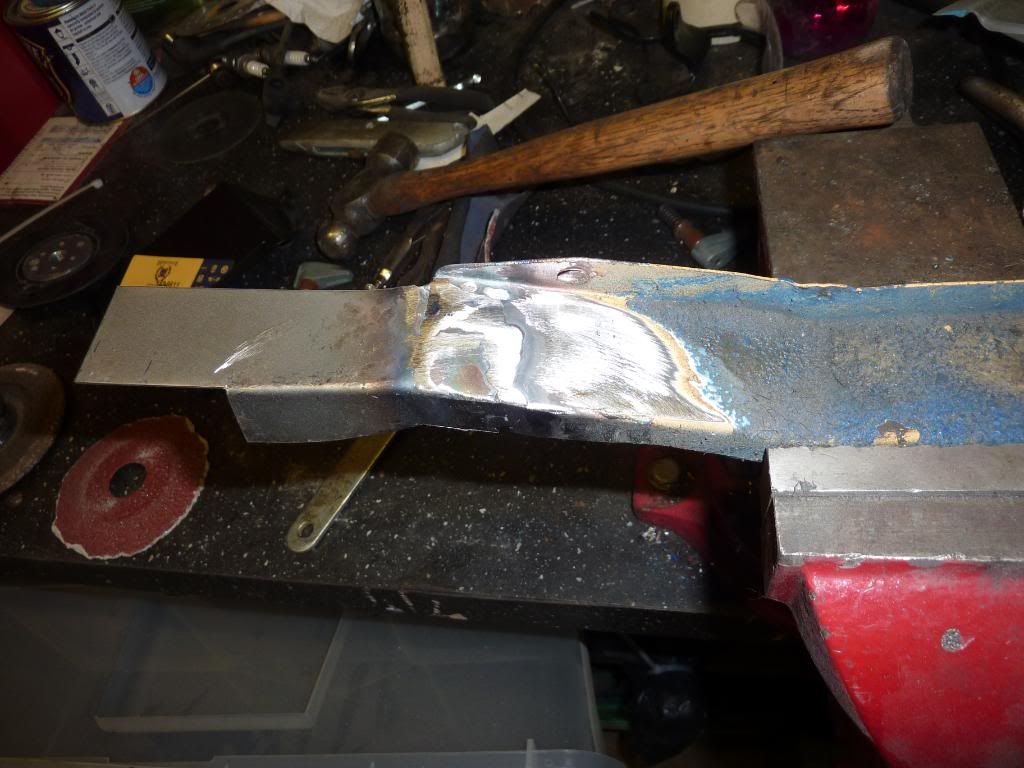
I've also tried it back in place to make sure it still fitted and all was good so moved on to the closing panel above the rear subframe mounting so that got chopped out and also a couple of inches next to the closing panel which had been repaired previously but wasn't great.
All cut out:

And with the new closing panel and repair panel I made up (more CAD!) in place:
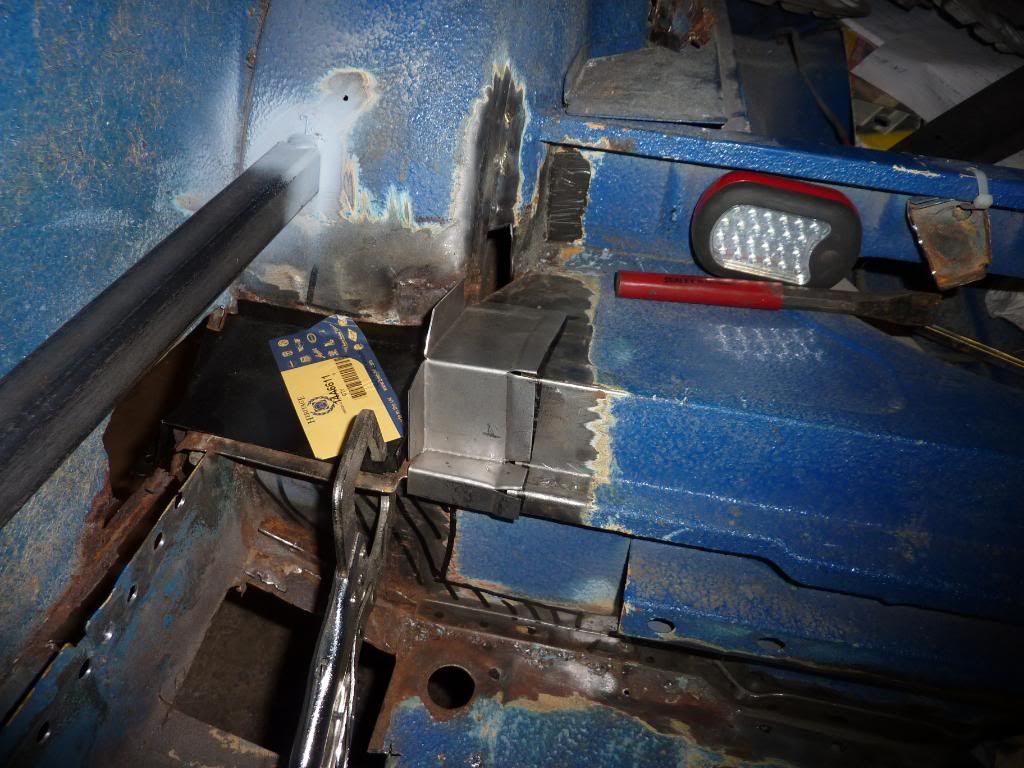
I need to repair the pocket at the back edge (it fits down in between the closing panel and the repair panel to close a gap due to the different heights of the panels (as per standard - not from dodgy repair panel fabrication!)
I have also decided to replace the end of the heelboard - it's a similar story to a lot of the other areas on the car - it's not bad and could be patched up and last for a good few years but I want to make sure that if there is something I can sort relatively easily now I'm going to do it now rather than try to do it in a few years time, wrecking the paint, etc.
Plan for next weekend (I have to work tomorrow so no time to work on the car) is to get the closing panel and repair welded in (but not to the heelboard as that will be coming out). I should be able to get the 1.2 sheet for the front this week and get that end sorted as well. Then it's deep breath time and cut out half the floor!
JR
#66
Posted 28 July 2010 - 02:29 PM
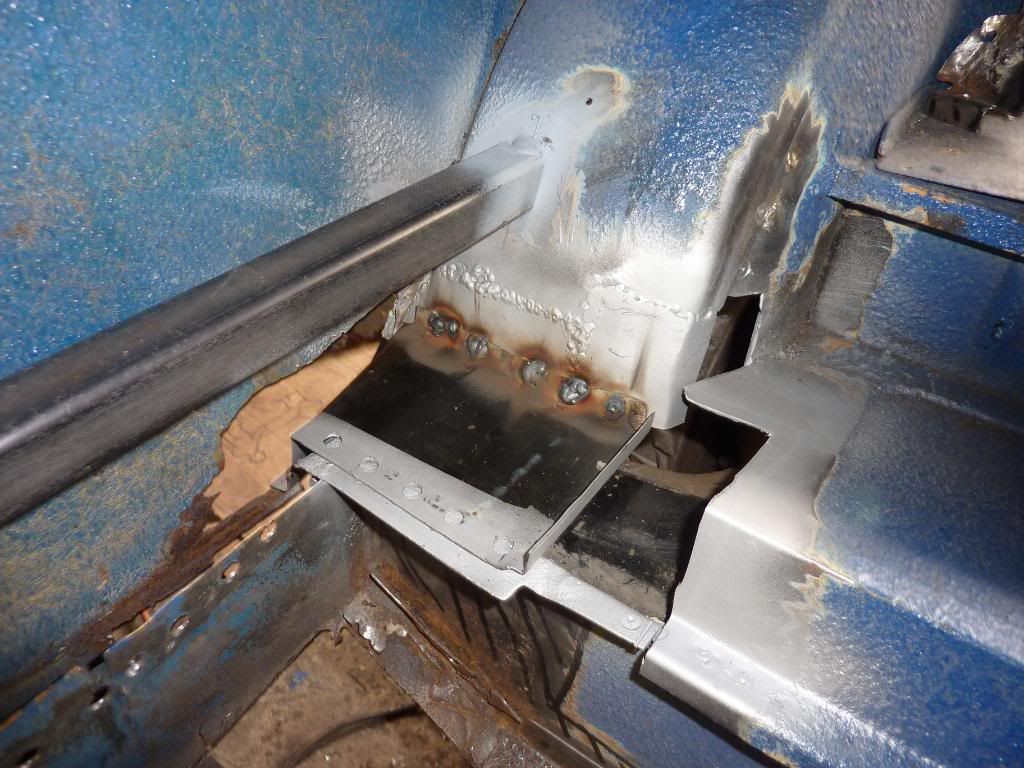
I haven't plug welded it to the heelboard yet as the end is going to be replaced. I also fitted the patch next to the closing panel:
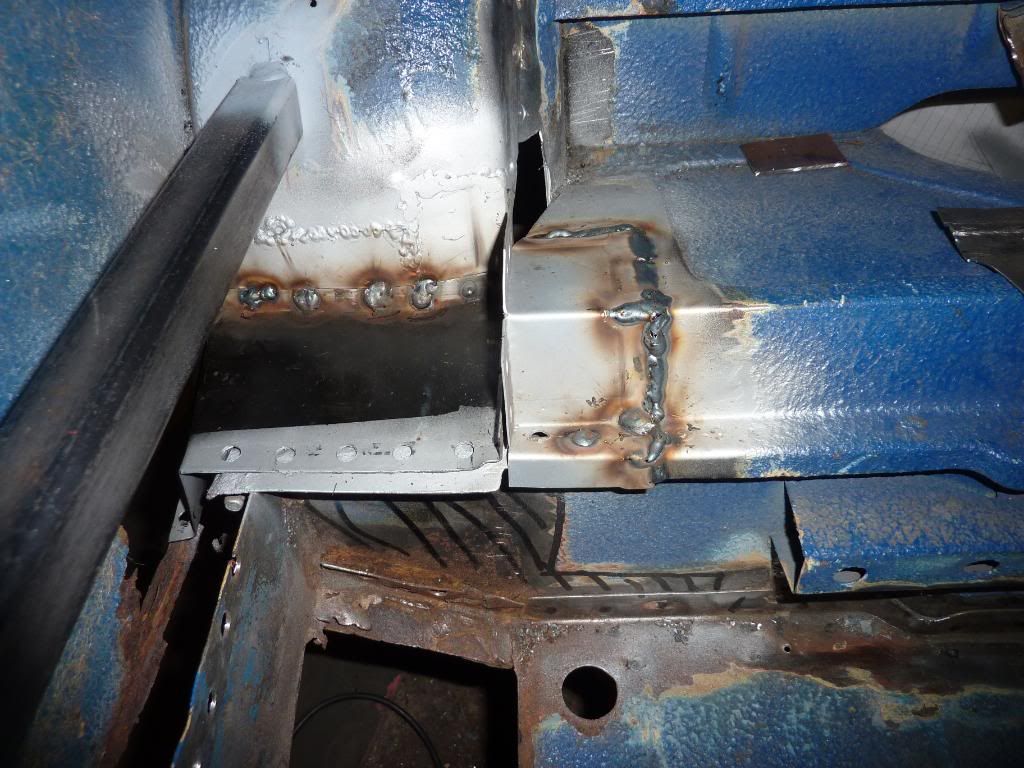
and re-fitted the inner sill closing panel - this is just welded to each end at the moment as the inner sill will be coming out.
I also repaired the pocket - the bottom rear corner was really thin once cleaned up and in removing it I had to cut a corner off it. This slips between the closing panel and the patch above to close the gap off:
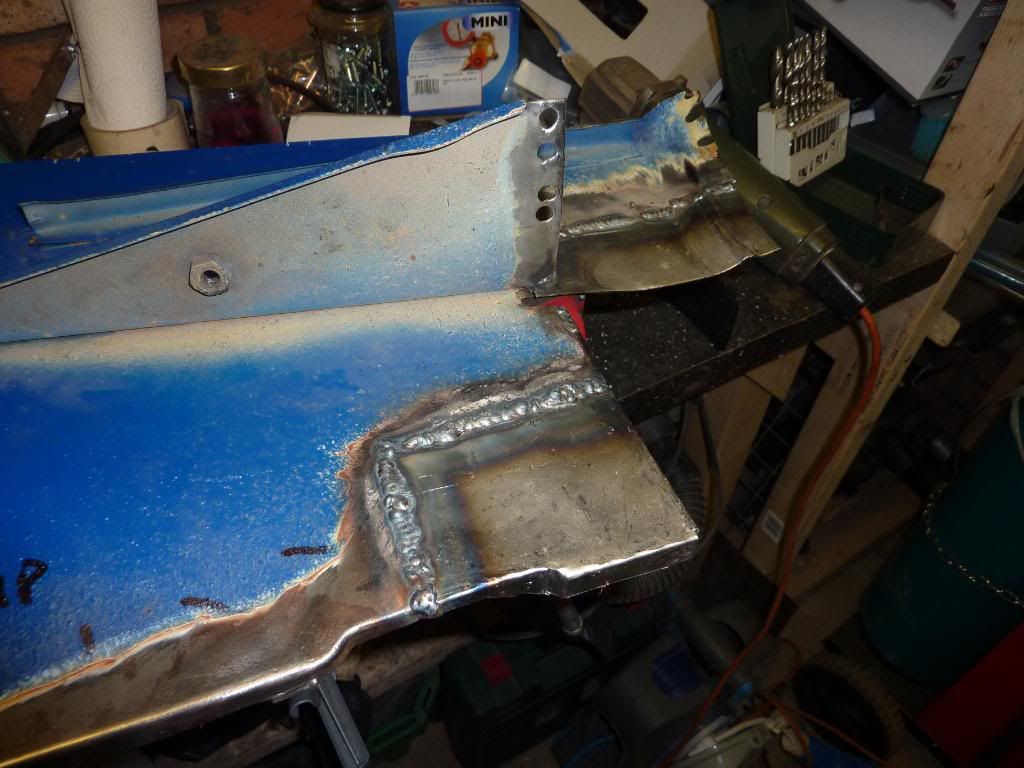
At this point progress slowed down! I got hold of some 1.2mm sheet steel from the local motor factors which was a bit dearer than the steel stockholder but at least they gave me the correct stuff! With this I started to make up the repair panel for the toe-board but even after a couple of hours of faffing round with it I can't get it to sit correctly in relation to the other side or the remaining bit of toe-board on the drivers side and that's without even considering the compound curve in the front corner of the floorpan that I've got to try and create. In the end I just had to leave it as I was getting frustrated! This is how it stands at the moment:
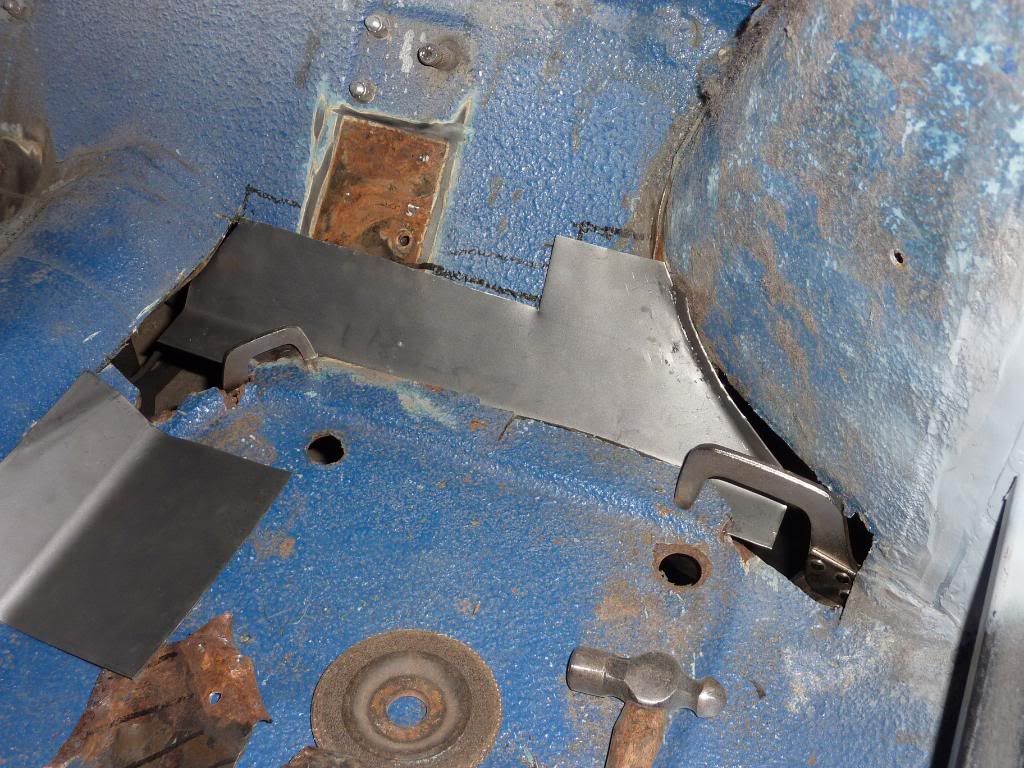
Hopefully going back to it fresh this weekend it will all fall into place!
JR
#67
Posted 28 July 2010 - 04:22 PM
Wigi
Edited by Paul Wiginton, 28 July 2010 - 04:23 PM.
#68
Posted 29 July 2010 - 06:57 PM
JR
#69
Posted 02 August 2010 - 11:51 AM
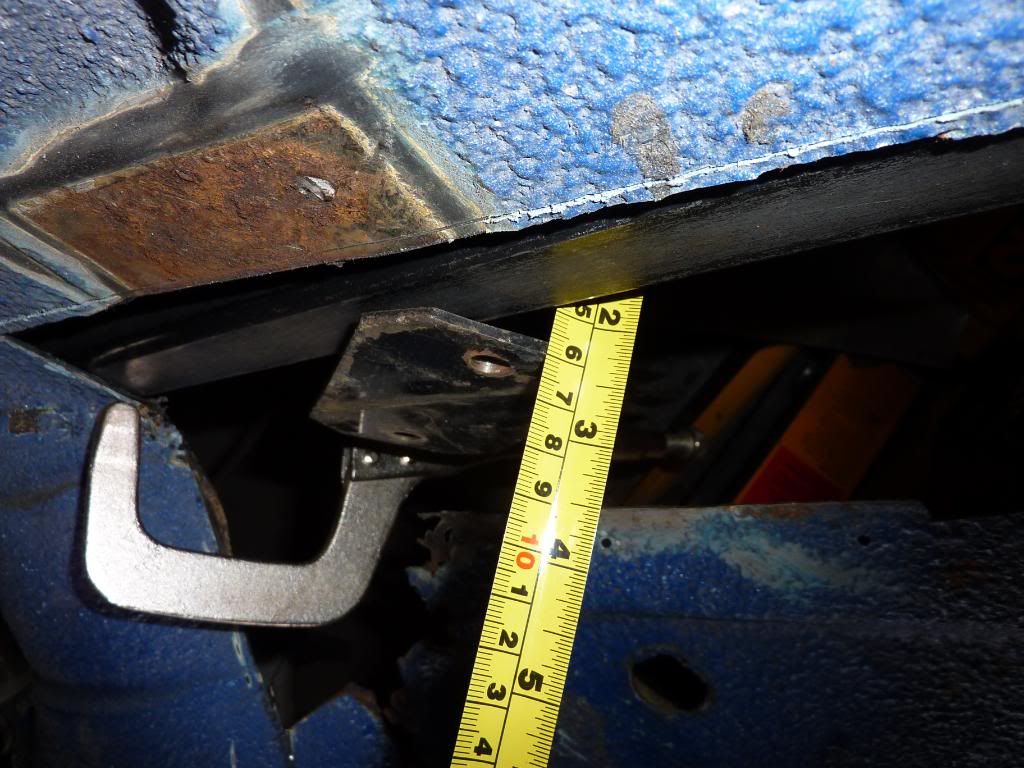
So I had to drop the subframe out to make the repair - I would rather make the subframe fit the car than the other way round - at least that way I could go back to a standard subframe (unlikely!!). Trouble was the car is supported on the subframe to had to make a wooden trestle to mount up under the cross-member. Once that was done I could get on with the repair. The difficult bit was shaping the compund curve at the tunnel end - it's still not great but it will do! Got that welded in along the top edge - the rest will be done when the floor goes in:
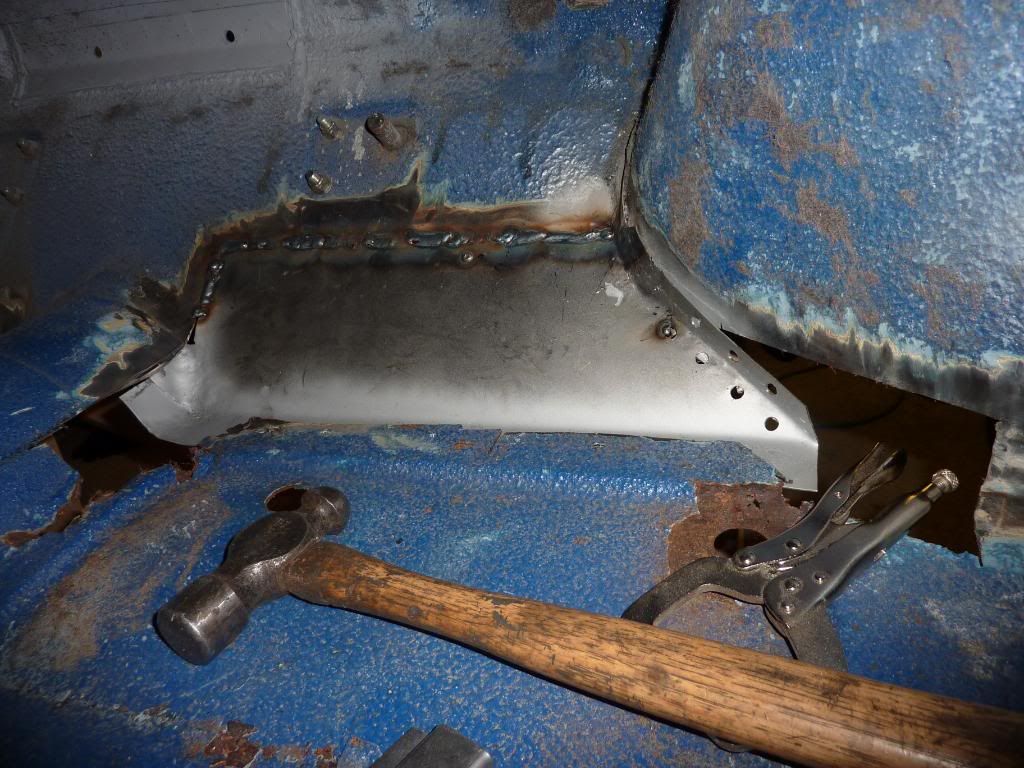
It doesn't look like much but I spent nearly 9 hours getting that done! On to Sunday and the heelboard and floor extension piece were the next target for replacement. Got all Heritage panels (heelboard, floor extension, outer sill) so did a quick mock-up with all the panels on the bench to figure out how it all fitted together:
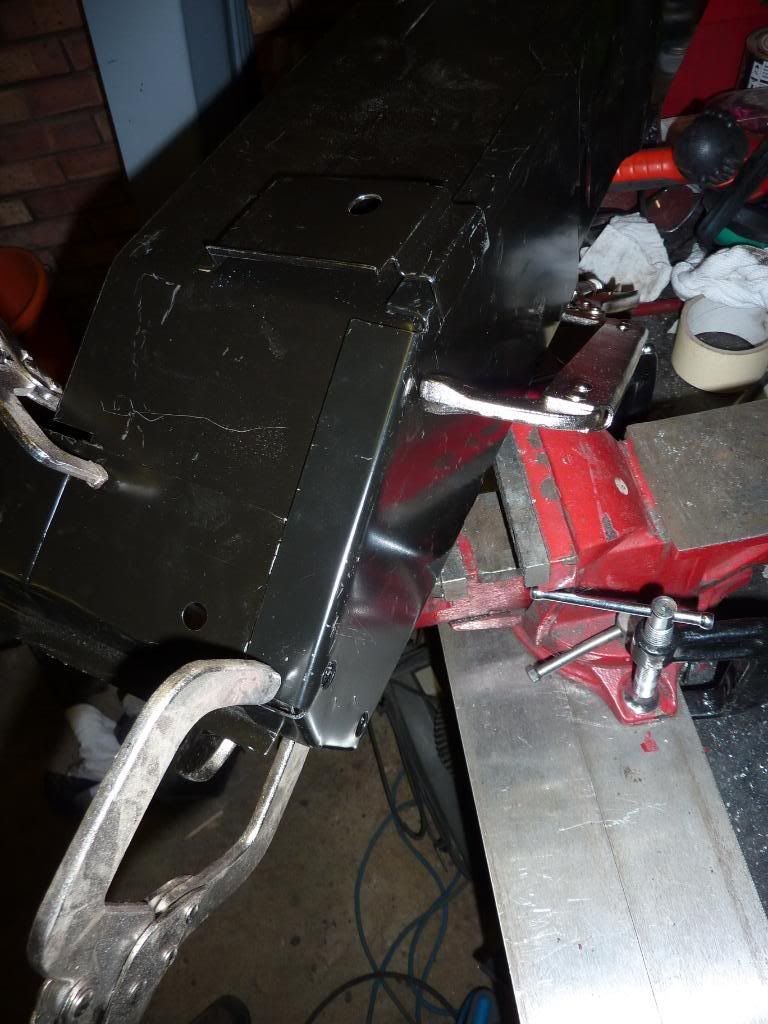
Then tried to run a tap through the subframe bolt fittings in the heelboard but the threaded inserts weren't actually behind the holes in the panel:
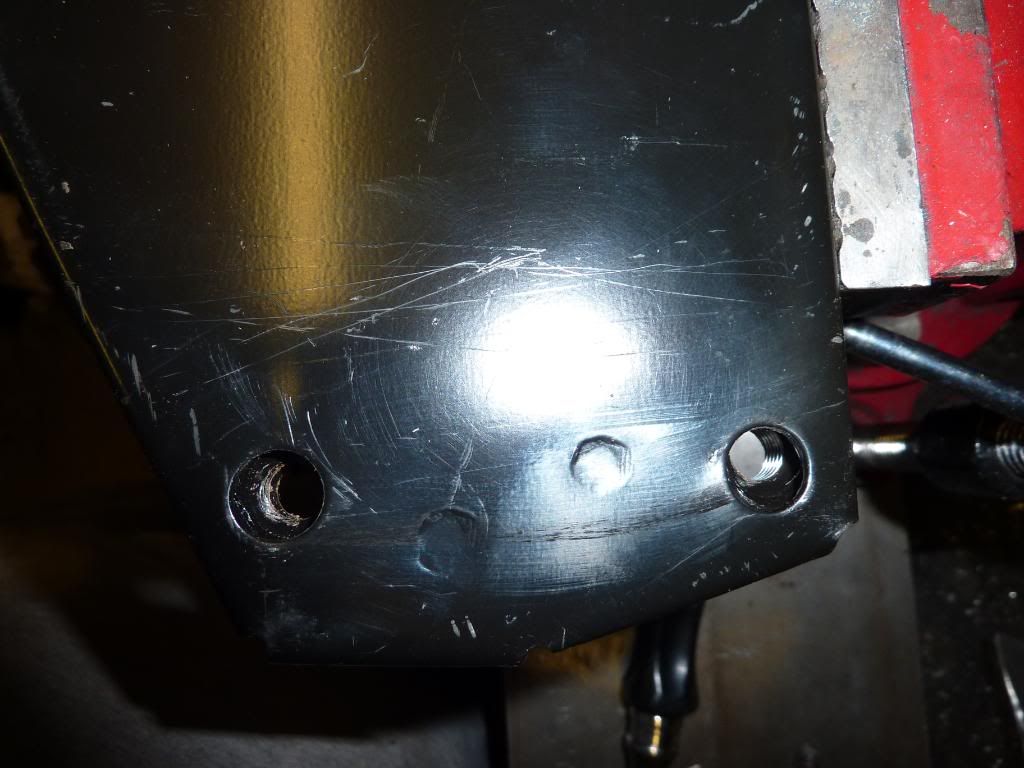
A bit more investigating and it appears the stiffener with the nuts on had been welded to the main panel in the wrong place and on the *******:
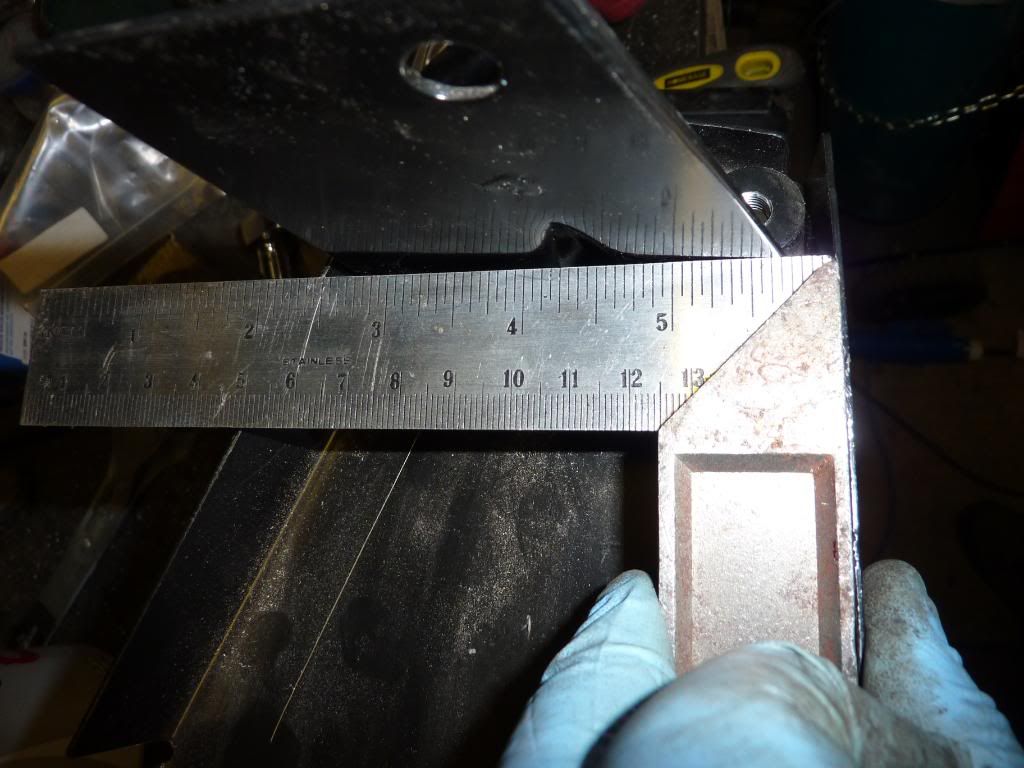
How the hell Heritage use these panels to make actual shells I'll never know - maybe that's why they cost so much these days. Anyway drilled out the 2 spot welds holding the 2 bits together and removed the stiffener - I fitted the main panel and then bolted the stiffener on with the subframe mounting bolts and welded it in the right place.
Heelboard area almost ready for repair panel:
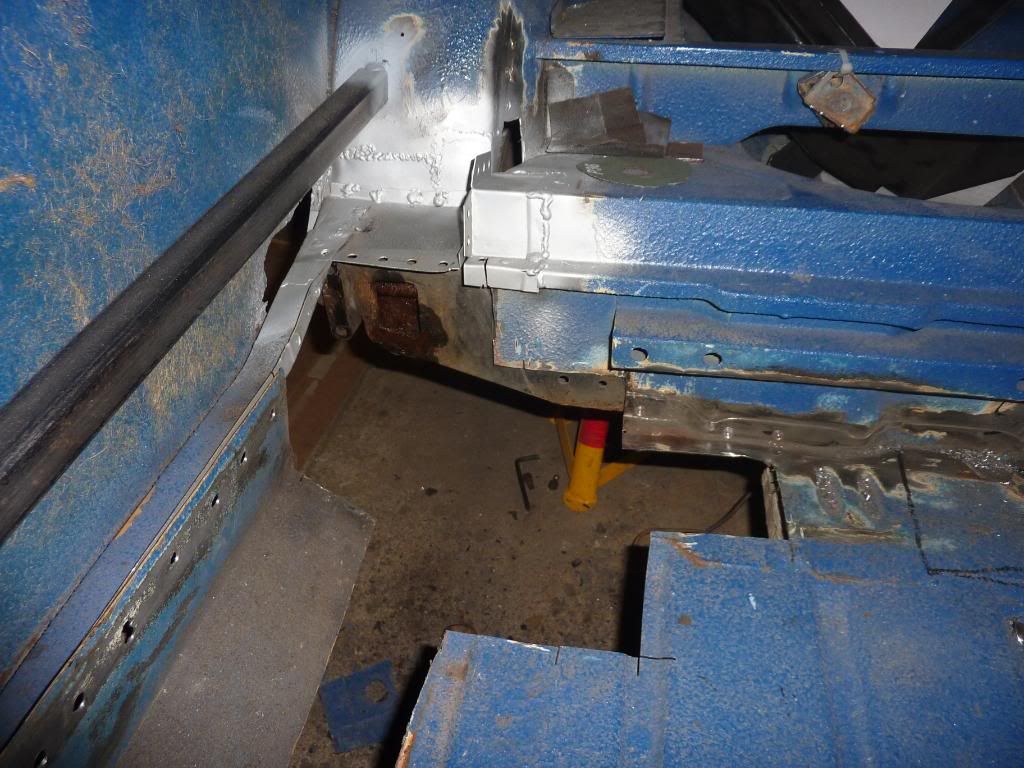
And welded into place complete with stiffener:
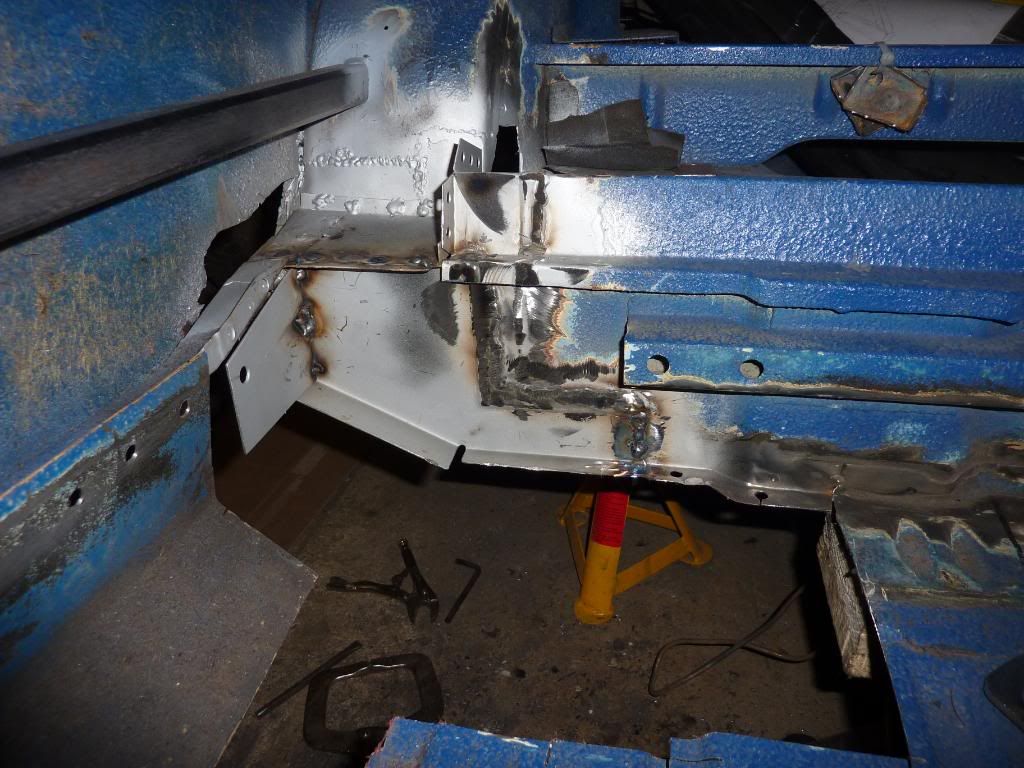
Then moved onto the floor extension - cut out the old, prepared all joints with weld-though paint:
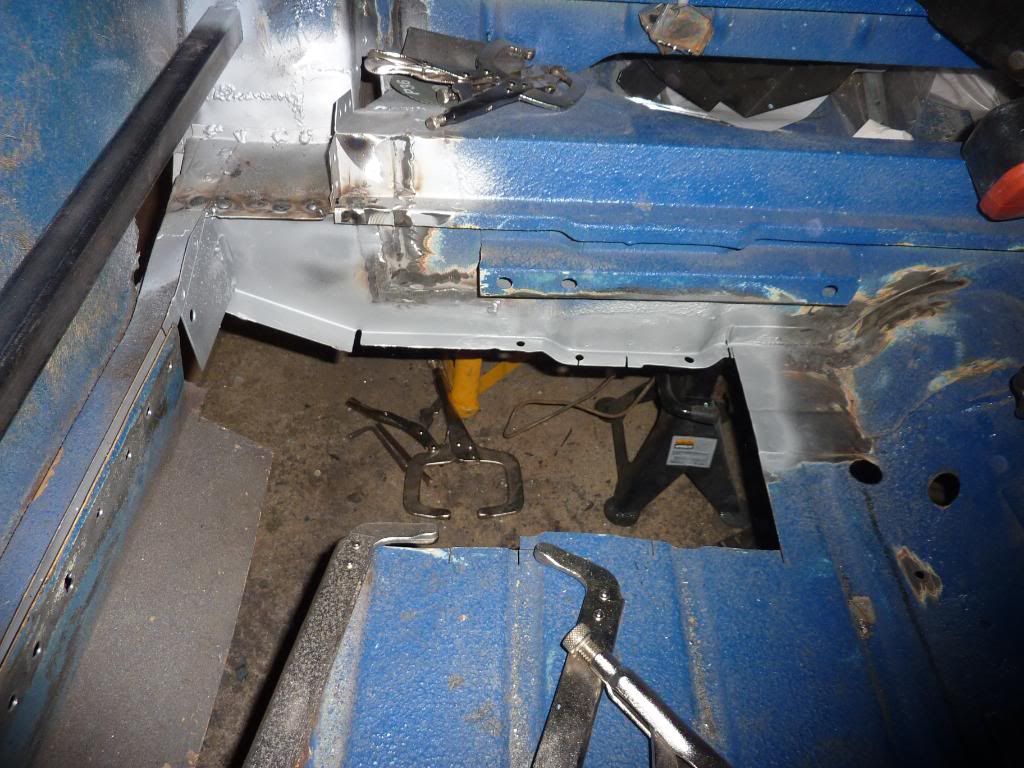
And started to weld in the new panel. I was having all sorts of problems with the welding though - almost certainly settings & technique - I was pretty tired by this point so decided that I would be better off leaving it and coming back to it rather than carry on and make a complete *******-up of it and giving myself more work to do later. It's looking better now I'm filling up some holes rather than making them!
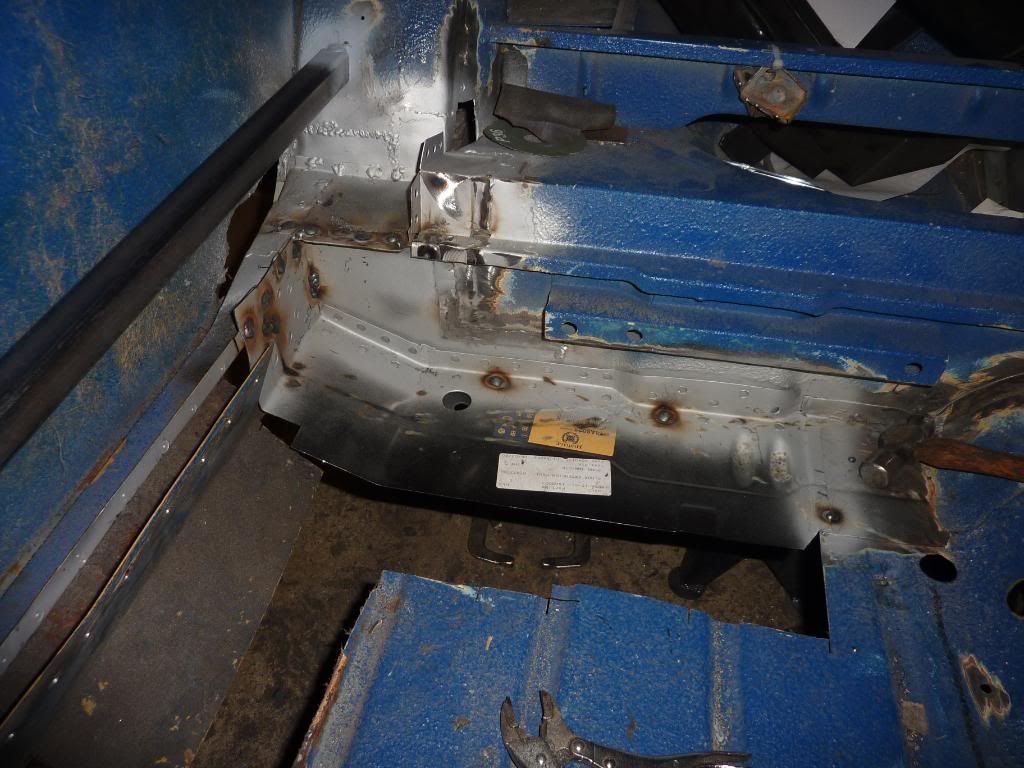
Once that's fully welded in it's on to chopping the floor out

JR
#70
Posted 02 August 2010 - 12:54 PM

#71
Posted 02 August 2010 - 04:24 PM
#72
Posted 08 August 2010 - 07:39 PM
Anyway after having issues with the welding last weekend I started today by preparing some of the off-cuts in the same way as I had on the car so I could do a bit of practice and get the settings adjusted before tackling the car again. I upped the wire speed a little as it seemed like the wire was melting back then falling off in little balls and had a go - it was noticeably better so up a touch more and all seemed good - did the following practice plug welds:
Front:
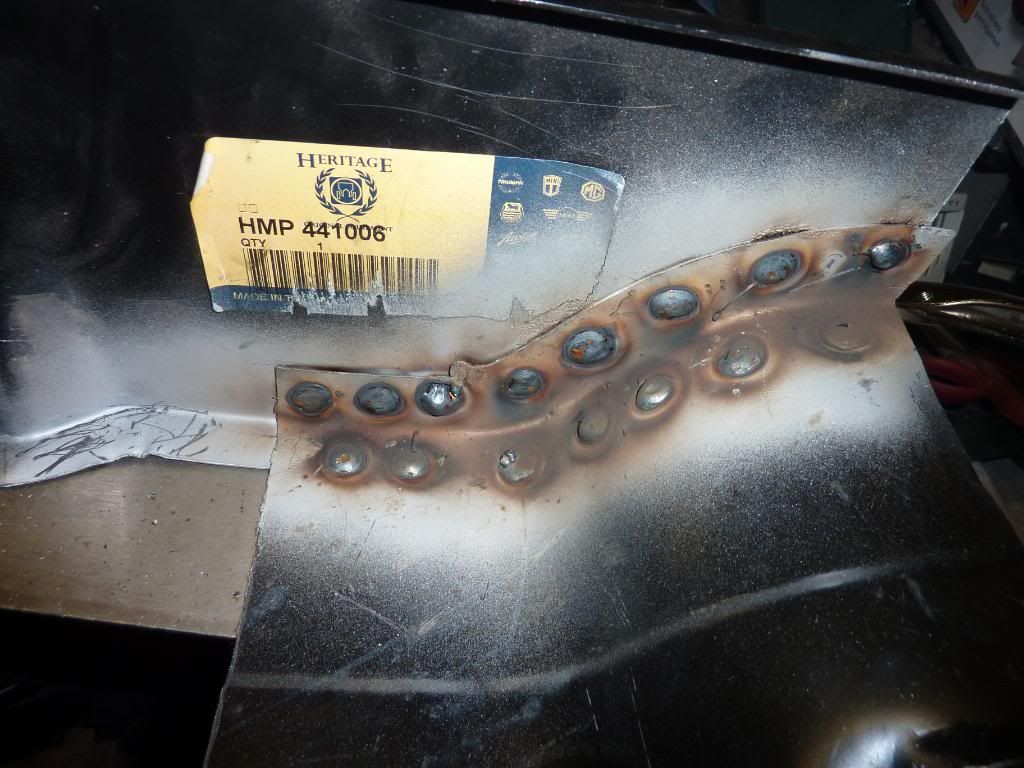
Back on horizontal welds:
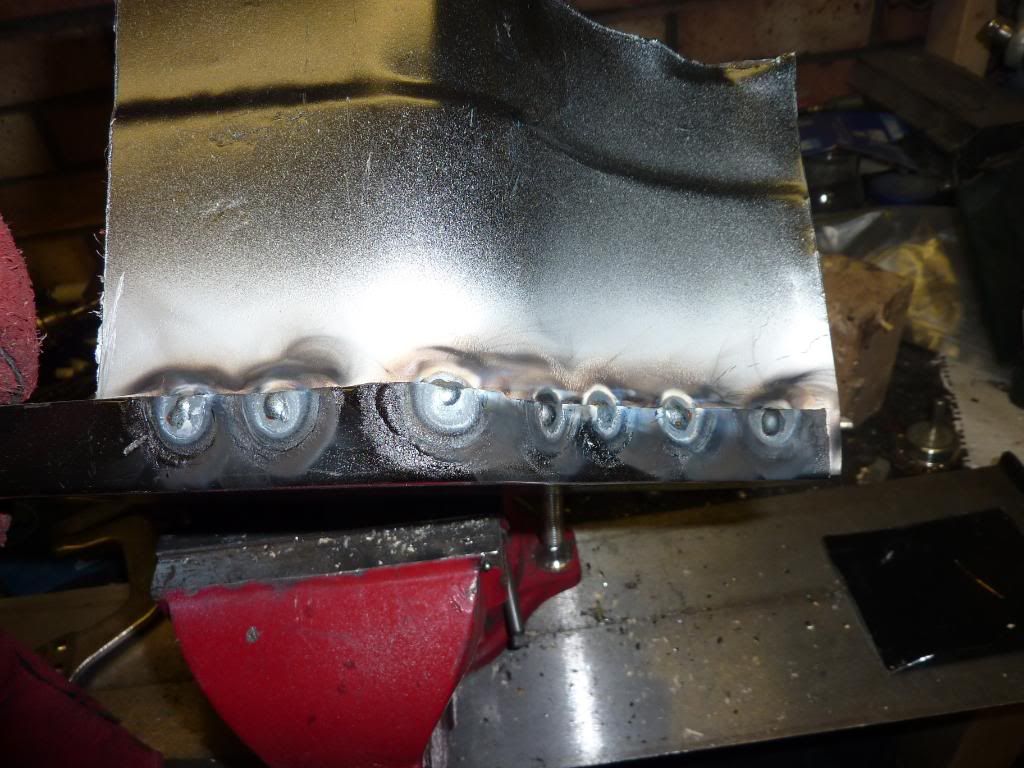
And on vertical ones:
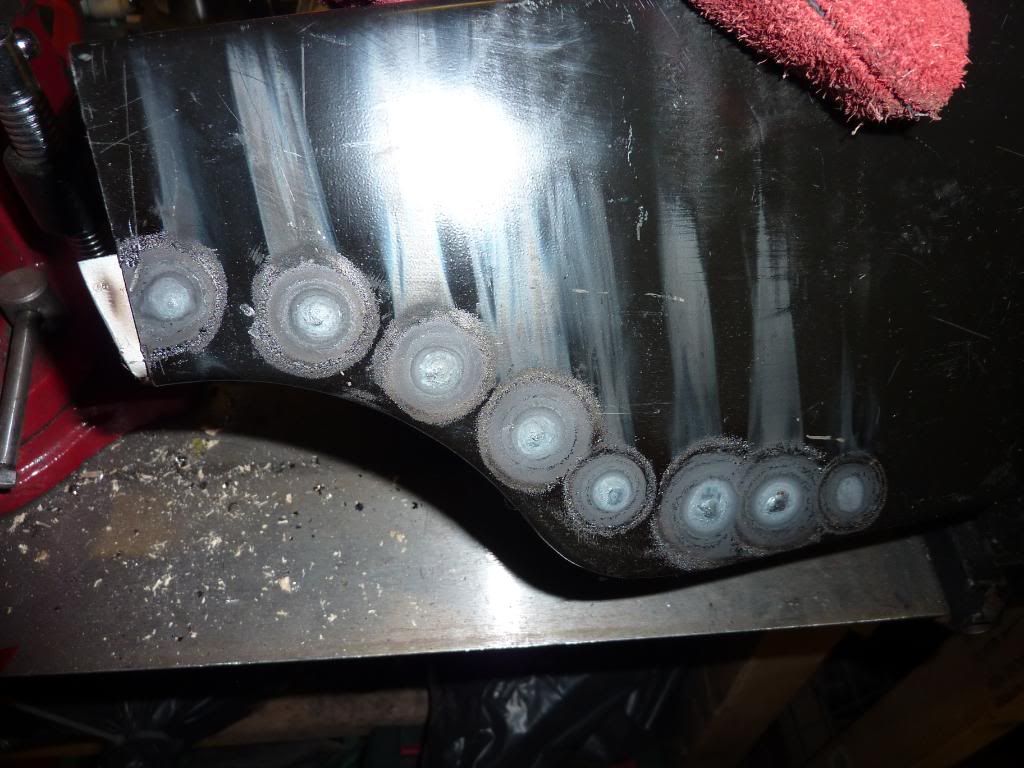
So happy I'd got the settings sorted out, I went on to finish welding the floor extension in which I seem not to have taken a photo of

Then set about one of the 'big visuals' and cut the floor out

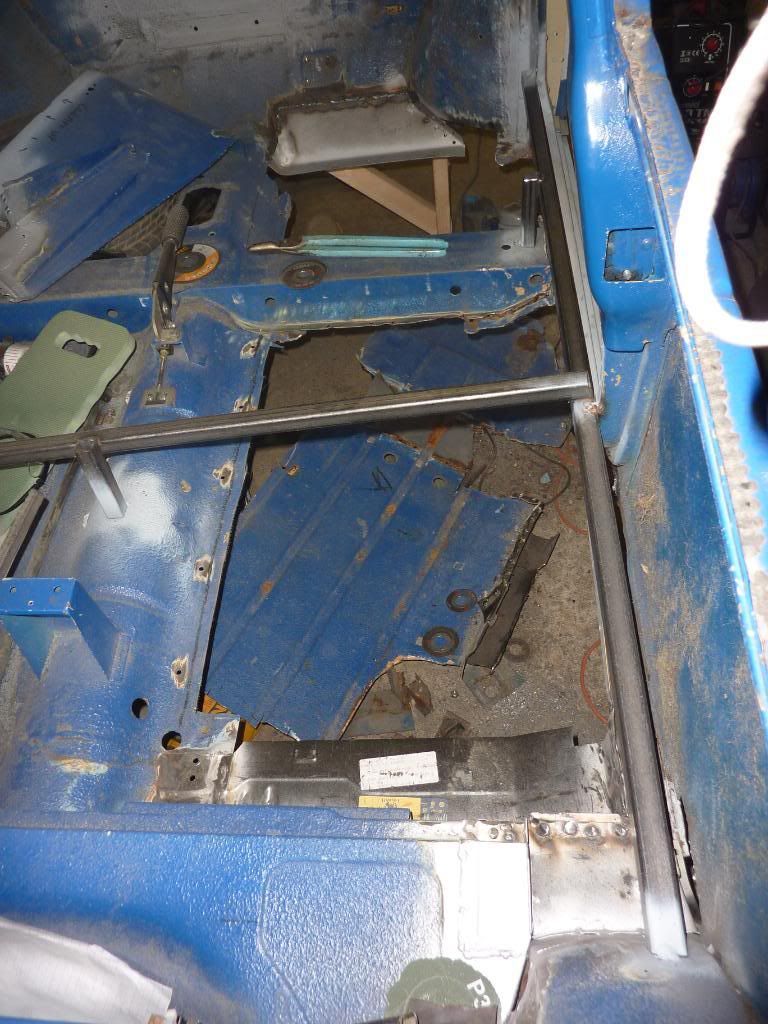
Pleasingly the inside of the cross-member is in good nick - just a little cleaning up and dressing of the flanges needed:
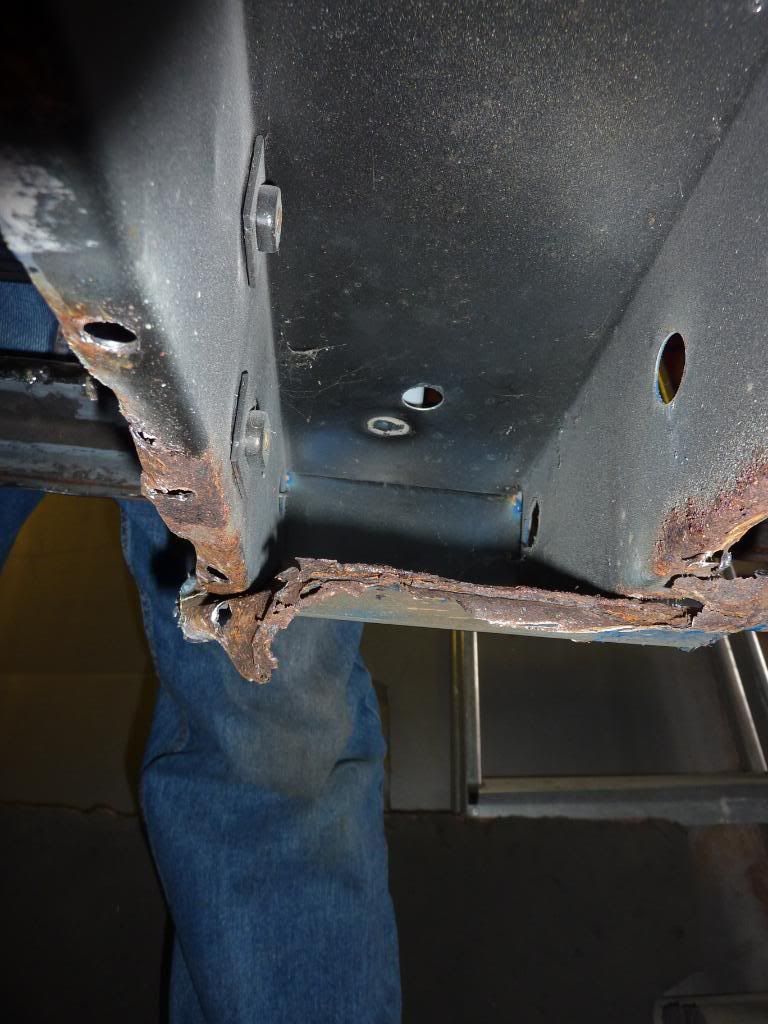
It will be nice to get a big lump welded back in - might get a couple of hours in through the week and next Saturday then MITP on Sunday - hopefully get to meet some of you guys and have a look at some finished cars to give me some more motivation!
JR
#73
Posted 08 August 2010 - 07:51 PM
Fair play to you.. Look forward to seeing it finished

#74
Posted 11 August 2010 - 08:18 PM
Good move on sorting out the wire speed on the off-cuts rather than on the masterpiece!


Nice work mate, keep at it

#75
Posted 12 August 2010 - 07:33 PM
Kam - I think even the flintstones didn't have a hole that big in the bottom of their car

I spent a couple of hours this evening doing a few of the fiddly bits and cleaning the edges up - I may cut a couple of little bits out of the cross-member to get rid of some thin & pitted bits which were over the rotten flute in the floor. As I'm using a saloon length floor panel as per original, I had to flatten the vertical flange which would normally get welded to the heelboard in a saloon as this fits under the floor extension in the estate. I also made a card template for the bottom of the flitch panel so I can cut the last remains of the old one off in order to get the floor panel in.
No pics for this update as I forgot to take the camera out. I may get a little more done tomorrow and then half a day or so on Saturday - I'm hoping to get somewhere close on the floor fitment before MITP and start welding it in the weekend after.
JR
2 user(s) are reading this topic
0 members, 2 guests, 0 anonymous users