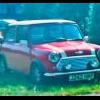
What Size Spot Weld Drill And Cutting Floors Out
#1
Posted 13 May 2010 - 01:21 PM
What size spot weld drill do folks recommend?
Any tips on getting the cut along the floor to match up? I was thinking about getting the sills out the way and chopping back to just before the channel, offering the part up and scribing along before cutting again to form a neat and tidy butt weld. Thought on this anyone?
good
#2
Posted 13 May 2010 - 06:58 PM
Use a nice HD grinding disc to remove the current spot welds, they are normal easy to spot (excuse the pun)
To cut the floor I would recommend a thin slitting disc, unless you have a plasma cutter of course
#3
Posted 13 May 2010 - 07:50 PM
On the joggling, I presume the lap would go underneath the car? Just trying to understand how to deal with the joint under the crossmember which is also to remain in place. Would I seam weld both sides of the joint?
I'm still a bit unsure about measuring the cut along the floor too. Roughly cut out, offer up the new, scribe and cut again?
#4
Posted 13 May 2010 - 07:56 PM
I am not a fan of joggled repairs for myself but each to there own just remember that it is an mot failure if you put a seam where there is not an original one if it is not seam welded!
#5
Posted 13 May 2010 - 08:15 PM
i use a mixture at work of 6mm and 8mm you should find 6mm fine oh and dont go buying one of those removable cutter type get a carbide one and run it slow and dont over heat it.
I am not a fan of joggled repairs for myself but each to there own just remember that it is an mot failure if you put a seam where there is not an original one if it is not seam welded!
Interesting about the mot point. So, Are you saying I have to make a butt joint, dress it to invisibility to get a pass?
#6
Posted 13 May 2010 - 08:36 PM
I am not a fan of joggled repairs for myself but each to there own just remember that it is an mot failure if you put a seam where there is not an original one if it is not seam welded!
So are we saying that a sill that was factory spot welded to the floor, then replaced and seam welded with a mig is an MOT failure? My understanding, is that as long as the car has not corrosion within 300mm of seat belt / subframe mounts the car is MOT acceptable. Welded seams are surely created when fitting quarter floor pans? AS long as the weld has penetrated
Edited by Senile Old Git, 13 May 2010 - 08:40 PM.
#7
Posted 13 May 2010 - 08:43 PM
Shame these things don't bolt together!
#8
Posted 14 May 2010 - 06:30 AM
as for the floor joints, I joggle the joint by 1/4 inch and seam weld all non factory joints, then on the other side, i put 1/2inch weld 1/2 gap as this it purely to keep everything tidy, then grind and finsih off.
Each person has there veiw but i will say of you but weld and grind the weld flat, then its not very strong, try it on the bench, the joggle method is stronger
dave
#9
Posted 14 May 2010 - 07:33 AM
my personal way is i butt weld and grind back both sides to an original factory look but this has come from years of experience restoring cars for a living.
But if you can get away with it that's great every mot inspector is different and can use there discretion and once sealed and painted some repairs are hard to see. some very strict mot inspectors i have dealt with over the years have even wanted to see the repairs in metal before sealed or painted
#10
Posted 14 May 2010 - 10:04 AM
At the moment I'm trying to work out how best to make the cuts In the floor and get the old inner and out sill assembly out to fit a new complete section.
I think that spot weld drilling along the door step, what's left of the inner a pillar and unstitching the companion box from behind the drivers seat should free it up. The heelboard has got to be repaired and the outer sills (yes, plural!) have already been cut along underneath the door step and rear quarter panel. Rear quarter panel has also got to be replaced.
Better crack on with it..
#11
Posted 14 May 2010 - 12:16 PM
#12
Posted 14 May 2010 - 09:59 PM
You will find once you've drilled all those weld outs (theres alot!) there wont be much steel left on the step flange to weld back too.
For this reason I would advise you cut alot the sill with a thin slitting disk or air saw then grind the remainder away from the door step until the spot welds become blue and then dissapear.
I would also joggle (10mm or so) the floor and seam weld. I would spot or plug weld the sill back to the door step.
If your replacing the inner and outer I would contact M machine for an all in one panel they do which is excellent quality. It includes the inner cross member strengthener and other bits and bobs.
#13
Posted 15 May 2010 - 06:49 AM
dave
#14
Posted 15 May 2010 - 06:59 AM
I took a cover sill off fitted buy a garage the other day and it took 2mins, because it had no penitration.
dave
This is a common situation, I heard from my MOT station that it is being discussed by VOSA that structural welding may only be carried out by qualified welders.
As Minidaves says .. welding on dirty metal rarely gives any significant penetration and has the stength of a Pritt glue stick, I personally think structural welding should be regulated
#15
Posted 15 May 2010 - 07:42 AM
I took a cover sill off fitted buy a garage the other day and it took 2mins, because it had no penitration.
dave
This is a common situation, I heard from my MOT station that it is being discussed by VOSA that structural welding may only be carried out by qualified welders.
As Minidaves says .. welding on dirty metal rarely gives any significant penetration and has the stength of a Pritt glue stick, I personally think structural welding should be regulated
Nothing would surprise me any more! Anything to get old cars off the road...
With the spot weld drill, it's the upper edge of the door step I'd be unpicking. As for the join to the outer sill, that's already been cut open with a slitting disc, revealing two old sills under the oversill

I am intending to use the M-Machine inner/outer sill assembly. Glad others recommend it.
1 user(s) are reading this topic
0 members, 1 guests, 0 anonymous users