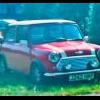
What Size Spot Weld Drill And Cutting Floors Out
#16
Posted 15 May 2010 - 09:28 AM
When I do a full floor repair I generally lap joint it/joggle ie, and then weld from the top and undernearth, give it a light dressing and a bit of seam sealer and job done.
Ok, you can still see the repair but I don't like grinding too much weld off structural areas.
#17
Posted 15 May 2010 - 05:52 PM
there is talk in the trade that all mechianics are quailfied before working on any motor car, there is already some guide lines in the bodyshop lines
dave
#18
Posted 15 May 2010 - 06:06 PM
well welding i remeber the hours when i was an apprentice how to stick weld, gas weld, mig weld, how to make a sheet of steel to turn into a cylinder when welding lines and it distorting.
there is talk in the trade that all mechianics are quailfied before working on any motor car, there is already some guide lines in the bodyshop lines
dave
So are you specialising more in the bodywork aspect of the trade these days?
#19
Posted 15 May 2010 - 06:07 PM
Ok, you can still see the repair but I don't like grinding too much weld off structural areas.
Agreed again. I genrally grind the top side or visable weld down as flush as i dare, usually still abit above surface, then ramp the edges with a flap disk, and genrally just skim the opposite side of the weld to make it slightly less obtrusive if anyone were to go looking around.
But people who make a repair and grind fully flush again have pretty much just removed the majority of the strength of the repair, obviously you should have penetration through the steel, however in comparison the weld sitting above the steel is what gives the joint the majority of its strength.
Rich
#20
Posted 15 May 2010 - 06:14 PM
David Isopon .. you sir are a god! (if your product is used as intended)
#21
Posted 15 May 2010 - 06:55 PM
But people who make a repair and grind fully flush again have pretty much just removed the majority of the strength of the repair, obviously you should have penetration through the steel, however in comparison the weld sitting above the steel is what gives the joint the majority of its strength.
Rich
I disagree with this if the repairer is competent with both welder and grinder then there is no strength loss. i have had welds that i have done this way tested and the failure point was not where the weld was. but there is actually a stress point along both sides of a weld that is left and this is commonly where when tested they fail but still exceeds requirements.
Each to there own to finish a weld this way most of the time is in tacking up and careful grinding/beating. If i left all my repairs visible then my customers will not be happy and thats why the cars i do win awards.
It is much easier to joggle the repair and if you are happy with that fine i was just advising that repairs needed to be seam welded to meet mot standards .
#22
Posted 15 May 2010 - 07:38 PM
I know in theory a weld should be just as strong when grinded flush as a solid piece of steel is, yet it never seams to be. Wether this is down to the heat of the welding process causing weakness i dont know, but where possible i always tent to try and leave as much of the bead in place as possible.
Rich
#23
Posted 16 May 2010 - 06:07 AM
After using the machine for a few years now I feel I bought well, as long as the metal is clean it gives a clean weld that gives deep penetration and the weld protudes no more than 1.5 mm off the surface. Personally I found the "hobby welders" are just not powerful enough to cut the mustard.
I have to agree with Rich, a correctly welded seam should be virtually invisible, that is why we finish with a skim of filler, prime the repair and paint in body colour. Nothing looks worse when you lift a carpet to be greeted with ill fitting plates "welded" by Charle the pidgeon then slapped over with underseal.
#24
Posted 16 May 2010 - 06:21 PM
dave
#25
Posted 16 May 2010 - 06:33 PM
welding requires power clean metal proper gas and knowing how to do it
And a decent auto darkening welding helmet so you can see what you are doing.
#26
Posted 16 May 2010 - 06:50 PM

Rich
#27
Posted 16 May 2010 - 09:56 PM
#28
Posted 17 May 2010 - 08:08 AM
I took the frame out because i had to get to the boot floor aswell. However i had the problem that every sub frame mount was corroded/snapped/moved. So alot of it was positioning then checking angles and levels.
But basically yes, i took it out, then redid the rear bootfloor as the rear sub frame brackers are fairly obvious where they go and its quite hard to put them in the wrong place. Once i put there in i just kept offering up the subframe and sticking the 4 rear bolts in, and tacked the front mounts into place. The opposite side to this was ok as the rest of the rear heelboard (I think thats what its called) was ok, but on this side i had to replace most of the rear corner, hence why i welded the mount on like his instead of attatched to the heelboard.
Rich
#29
Posted 17 May 2010 - 01:59 PM
A trip to BOC is in order I think!
1 user(s) are reading this topic
0 members, 1 guests, 0 anonymous users