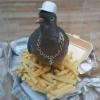
Increasing The Gearbox To Engine Bolts To 5/16"
#1
Posted 06 January 2011 - 06:46 PM
#2
Posted 06 January 2011 - 06:57 PM
#3
Posted 06 January 2011 - 07:02 PM

#4
Posted 06 January 2011 - 10:11 PM
Make sure you use a pillar drill to open the block holes out so they are square!
#5
Posted 06 January 2011 - 10:13 PM
The larger bolts would be stronger than the case and you wouldn't expect that to just fail.
#6
Posted 06 January 2011 - 10:47 PM
No point. No advantage. waste of time.
The larger bolts would be stronger than the case and you wouldn't expect that to just fail.
Not the case at all. I had regular failure of front centre 1/4 unf bolt, fixed by using 5/16. As BMC eccosse says, you need to use cap screws on the front as there is little clearance for 1/2 af heads. This unfortunately means it is a time consuming job getting them in and out. Buy a ball end Allen socket.
#7
Posted 08 January 2011 - 09:42 AM
No point. No advantage. waste of time.
The larger bolts would be stronger than the case and you wouldn't expect that to just fail.
Not the case at all. I had regular failure of front centre 1/4 unf bolt, fixed by using 5/16. As BMC eccosse says, you need to use cap screws on the front as there is little clearance for 1/2 af heads. This unfortunately means it is a time consuming job getting them in and out. Buy a ball end Allen socket.
Can you elaborate on the failure. When did it happen? why only one? I've heard of them comming loose but never breaking. I can't actually see a time when only one can break.
#8
Posted 08 January 2011 - 09:47 AM
#9
Posted 08 January 2011 - 10:00 AM
Not a necessary job, there are some monster power motors that are perfectly fine with the original 1/4"unf's. If inferior bolts are used I can see a problem but Ive observed most of the failures Ive read about on various forums are due to human error rather than the parts. Original bolts are fine.
Paul
Oh, you dont need to fit studs above the diff, bolts fit easily
Edited by Paul Wiginton, 08 January 2011 - 10:02 AM.
#10
Posted 08 January 2011 - 10:32 AM
It is a common issue for gaskets to be blown out between the crank case and gearbox, so instead of using a gasket they just use a bead of RTV, increasing the size of the screw from 1/4" to 5/16" means you can increase the torque to which screws can be tightened, which implies the gearbox and crankcase are held tighter together giving a better seal with the RTV.
#11
Posted 08 January 2011 - 01:12 PM
No point. No advantage. waste of time.
The larger bolts would be stronger than the case and you wouldn't expect that to just fail.
Not the case at all. I had regular failure of front centre 1/4 unf bolt, fixed by using 5/16. As BMC eccosse says, you need to use cap screws on the front as there is little clearance for 1/2 af heads. This unfortunately means it is a time consuming job getting them in and out. Buy a ball end Allen socket.
Can you elaborate on the failure. When did it happen? why only one? I've heard of them comming loose but never breaking. I can't actually see a time when only one can break.
Used to break the head off the centre front bolt, the one in line with the centre main in a well used S thin flange block inside 100 miles of use. Didn't do it initially, but after about 200 miles of use from build, it used to snap them regularly. After the 3rd one, fixed by changing to 5/16 and never broke another
#12
Posted 08 January 2011 - 02:26 PM
#13
Posted 08 January 2011 - 02:36 PM
there is a seller on ebay that often has ultra high grade std size gearbox bolt sets for a good price, (and also main bearing sets) using these would be the route I would suggest.
this is the chap...
http://cgi.ebay.co.u...=item25600e58d9
failing that, I have taken mine out to mate in the past, as its easy to get hold of strong bolts in this size, just use socket heads, they are usually 12.9 grade iirc
Although I did mine, I do agree with Wil.
Not a necessary job, there are some monster power motors that are perfectly fine with the original 1/4"unf's. If inferior bolts are used I can see a problem but Ive observed most of the failures Ive read about on various forums are due to human error rather than the parts. Original bolts are fine.
Paul
Oh, you dont need to fit studs above the diff, bolts fit easily
Edited by mini13, 08 January 2011 - 02:38 PM.
#14
Posted 08 January 2011 - 02:47 PM
well, ive already drilled and tapped mine, just need to drill the holes in the gearbox casing when i rebuild the transmission. Allen key type bolts (forgot the name, lol) will be coming from mra minis, so should be good quality. Thanks.
Edited by samsfern, 08 January 2011 - 02:50 PM.
#15
Posted 08 January 2011 - 03:17 PM
Thanks for the Vizard reminder Sam, if he says revs (not torque/bhp) are the cause, then the source must be the reaction forces from holding the crank. Perhaps the reinforcement webs on the A+ are a better remedy that wasn't available to those engines when DV wrote that section?
1 user(s) are reading this topic
0 members, 1 guests, 0 anonymous users