We aquired our Mini in September it’s a 1990 Mayfair Henley Blue Old English White Roof 12 months MOT with a genuine 47,000 miles for which we have every MOT and service stamp and receipt. It will be my son’s first car when he hits 17 next March so the pressure is on to get moving with the rebuild. So this winter will be spent in the Garage by the looks of it

I have just spent the best part of two years rebuilding a 1975 Triumph Stag, which is now around 90% done. But I am in no rush as that went back on the road in July and the remaining work is just me wanting to improve it. My lad has never wielded a spanner before so he has a steep learning curve to go with his A level studies

Back to the Mini, my lad and his mates have nicknamed it the Smurf for obvious reasons I guess!
The aim is to have a really solid mini which looks cosmetically good and drives well. I am not aiming for concours so the rebuild will be limited to replacing what it needs and not a complete restoration and strip down. Having said that I won't be missing out anything either so it will be done properly.
Mechanically the car is A1 and runs like a sewing machine, unfortunately the not so optional extra of the mini "tin-worm" has surfaced and chewed its way through some of the body in the usual places.
This is what we started with as with all photos looks good eh?
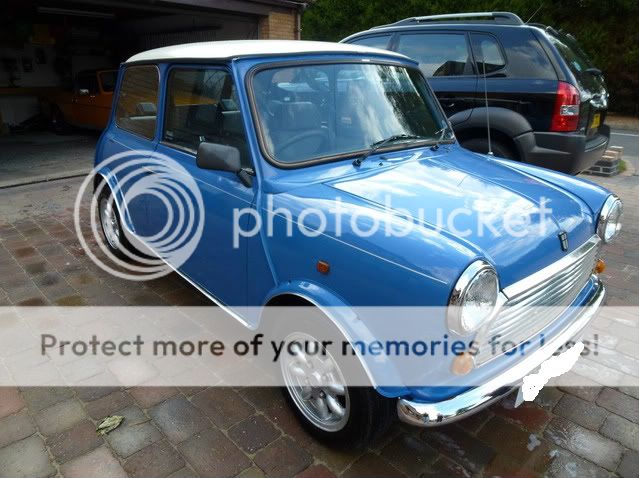
Then I started work on stripping the front, having decided to work from front to back. The wings a gonner, other side was similar

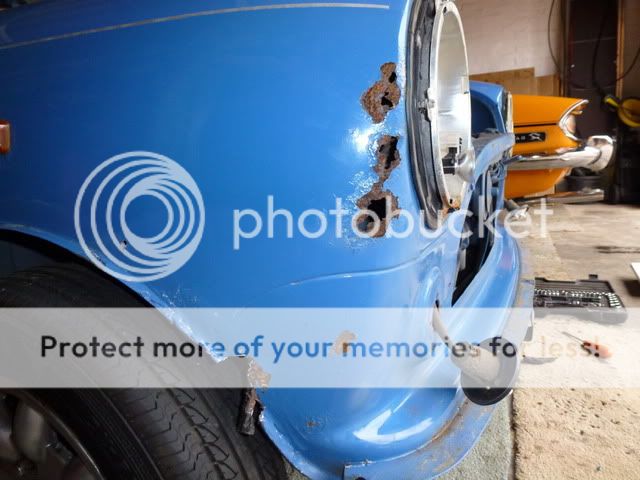
Then the front panel, much of the same with a few bits of welded plate over the top here and there, leaving the rust in for good measure

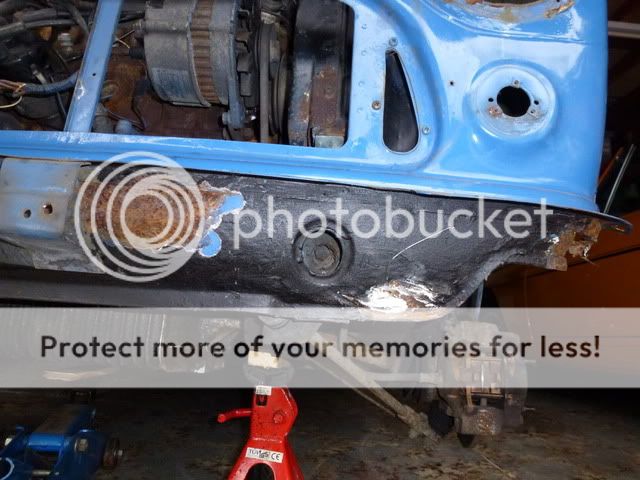
But the floors and underneath are very good and won't need much more than a clean up and paint on the underside. Boot floor and battery box are like new too

Sills have been replaced but I may have them off to double check whats going on under them as I sense any new metal has just been welded over the not so nice bits! Probably done by the garage for the MOT !
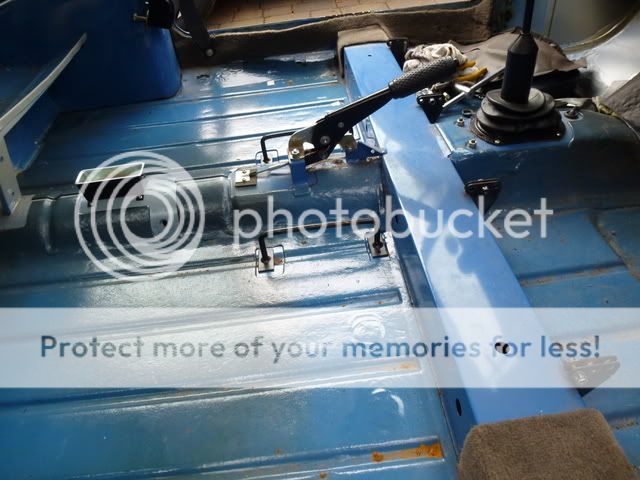
So I have cut off the front sections and already found the odd bit of bodgery. At some stage the A panels had been “replaced” but only half of them. The lower half had been cut away and a new section welded in. The fold on the inner wing door section hadn’t been completed as you can see (hopefully) in the photo. This was the same on both A Panels. Luckily apart from the Front panel welding this was the only work I could find that had been done on the front end.
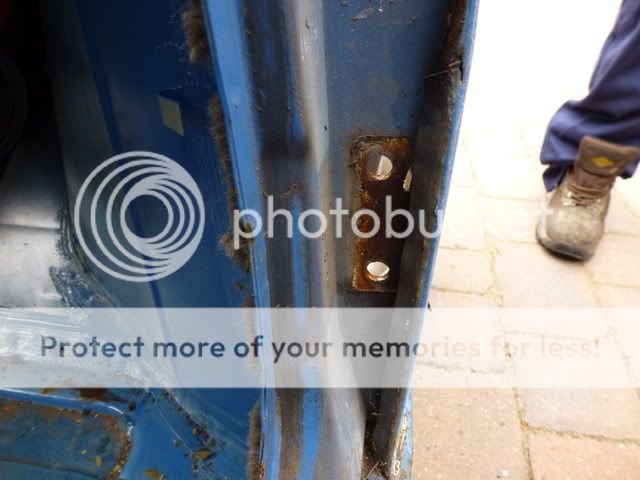
Made getting the door off a bit harder as it was across the hinge! I was left with one question …Why??
Overall though I am pleased and replacement parts seem easy to obtain, so it won't be long before I have the MIG out and the rusty bits chopped out and repaired properly! More photo's when I can load them up.
Cheers
Glyn