
Radius Arm Bracket Bolt Spinning
#1
Posted 09 December 2011 - 11:36 AM
I have removed three of the four bracket bolts and I have one left to remove but it keeps spinning and not turning out.
The bolt which is causing a problem is one of the two bolts you loosen from underneth the car. It is the one closest to the grease nipple of the radius arm. Is there any way of removing it?
I was hoping to just cut the head off and once the bracket is removed I should be able to see why the bolt was not coming out, since the bracket covers any access to the thread of the bolt - but wanted your expert opinions first. Thanks
#2
Posted 09 December 2011 - 11:45 AM
also the side your saying is hidden in the subframe so someone else may tell you how to get over this.
Edited by greensilver mini, 09 December 2011 - 11:51 AM.
#3
Posted 09 December 2011 - 05:45 PM
What do you think?
#4
Posted 09 December 2011 - 05:46 PM
#5
Posted 09 December 2011 - 05:51 PM
Also what would punching the nut do - and would i do this against the top of the frame?
#6
Posted 09 December 2011 - 06:21 PM
#7
Posted 09 December 2011 - 06:25 PM
#8
Posted 09 December 2011 - 07:37 PM
cheers - one more thing - I have been told welding upside down can be tricky with mig correct? I think this is where I am going to struggle.
Just put a couple of quick tacks to hold it then seam weld around and you will be fine. MIG welding upside down is not a problem, but sorting helmet clamps etc etc can be! Obviously if you are directly under it there is more of a risk of getting covered in spatter so be careful, but I would think this would be more of a side on-uphill job than one where you would lie on your back if that makes sense.
If you haven't got one already then an auto darkening helmet will be the best money you've spent in a long while.
#9
Posted 09 December 2011 - 08:17 PM
#10
Posted 09 December 2011 - 08:40 PM
#11
Posted 09 December 2011 - 08:45 PM
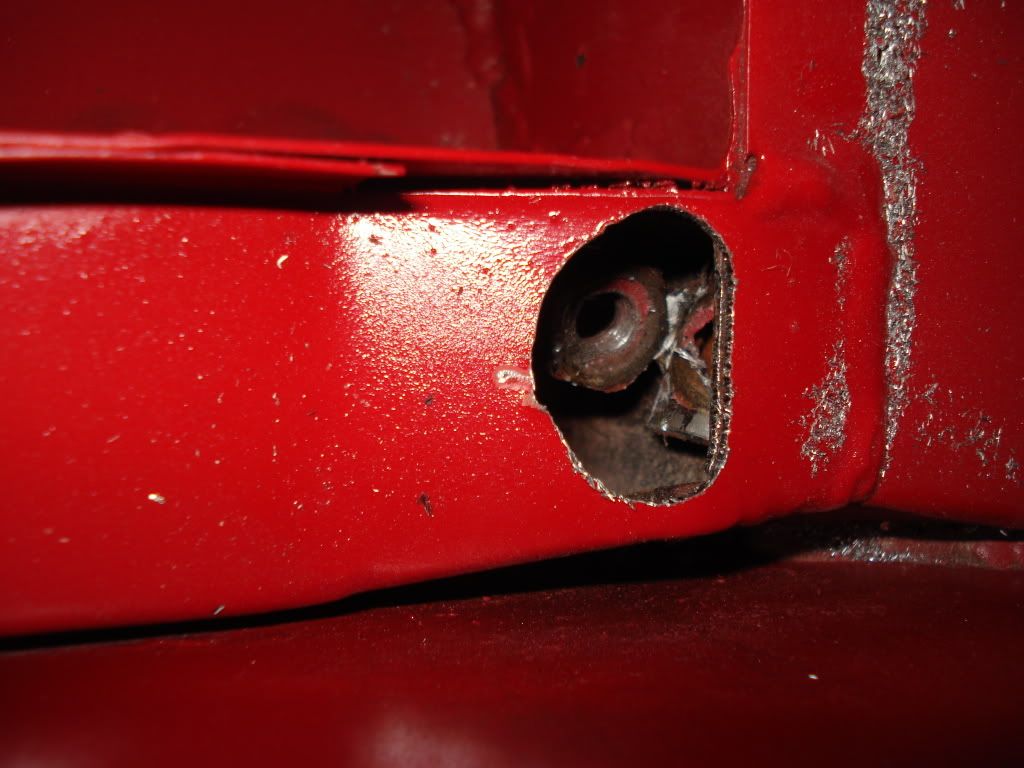
I will be fitting a blanking plate using an anchor nut to secure it.
#12
Posted 09 December 2011 - 08:47 PM
#13
Posted 09 December 2011 - 08:51 PM
The annoying bit for me was it was a Heritage heelboard as well which was a bit of a shock. Such is life.
#14
Posted 09 December 2011 - 08:57 PM
Unfortunately for us after spending a lot of time paint and stone chip i really did not want to cut into a brand new sill. Other wise i would agree with doing it your way Cooperman and i see what you mean about the mounting bracket.
The annoying bit for me was it was a Heritage heelboard as well which was a bit of a shock. Such is life.
It pees you off when it happens on an old and slightly corroded heelboard, but on a new one it's just poor quality.
#15
Posted 09 December 2011 - 09:03 PM
1 user(s) are reading this topic
0 members, 1 guests, 0 anonymous users