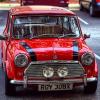
1981 Hl Project Orange
#31
Posted 09 January 2013 - 02:33 PM
#32
Posted 14 January 2013 - 12:05 AM
Headlight retaining ring not looking too good here after adjustments

So I removed it

Tweaked the wing

Spot welded and dressed it

Then went about reattaching the retaining ring

Welded and dressed

Same problem with the flange on this side, soooo....

Had to remake the front half this time, though, since it was pretty rough

Also had a bit of a gap problem, so I sectioned and folded the inner wing flange down to allow for spot welding the wing. While it looks wonky right now, I'll massage it so it looks fine once I get some more welding wire.

Started welding the flange on, but ran out of wire. So here is a partial weld and the wing as it sits on the body.


Spent all day in the garage which was good. All that time was spent working over a new panel which was not good. Still, it's beginning to get there. I'll get some wire tomorrow so I can keep pressing on. Thanks for looking!
#33
Posted 14 January 2013 - 01:22 AM
#34
Posted 14 January 2013 - 09:20 AM
Did you build your bench yourself or buy off the shelf? I'm at that stage myself.
#35
Posted 14 January 2013 - 12:03 PM
Ba-tat--the bench and shelving are actually a little of both. Workbenches of any consequential size are REALLY expensive. I found this product by 2x4 Basics which is all the black plastic end pieces in the picture. Essentially, you buy a kit of whatever you want to build (in this case a workbench), and then you design/build it to your specs using local store lumber. Really is a great product because it allows you to make whatever you want. I think I spent about $150 to build an 8' x 3' bench with a pegboard back. By contrast, a solid wood, 6' x 2' bench from Harbor Freight is around $200. Metal stuff, forget about it. As luck would have it, we also replaced our flourescent kitchen light with multiple cans, so I repurposed the old light in the bench. The plastic is super strong, too, so the bench is nearly indestructible. I'd do it again if I needed another one later (which I would like to have a smaller one for parts, etc). Really is good stuff with lots of ways to customize it for your needs.
#36
Posted 14 January 2013 - 07:42 PM
#37
Posted 21 January 2013 - 12:55 PM
So, had the passenger side wing channel fitment issue last time. Just not enough space to reattach the flange and weld it to the car.

So I flattened what was there.

By far one of the simplest, but coolest tools...the air punch. One side punches holes for plug welding, the other acts as a mini press to straighten things. Highly recommended as it saves a ton of time drilling.

Added some metal.



Slotted it to make the bend upward.

And nearly done

Here you can see the holes punched into the wing using the aforementioned tool. So easy and fast. Think the tool cost about $20.

Next, the A panel flanges on both sides simply were not up to snuff.


So I sliced them off and built new ones. I think I've become king of the flanges as I've had to repair a lot of them.

Another great tool...a piece of copper tubing from the hardware store flatted on one end. The welds won't stick to it, so it works great as a backer to larger gaps. Instead of cutting out patches to fit the area, I use the copper tube behind the gap and fill it with weld, then grind it smooth. Works great.






This is where I ended due to going to dinner with some friends. The flanges are overly large at the moment, but this gives me a solid spot to mount the wings on to. Once they are on, I'll grind them down flush with the wings' flanges for a nice uniform look. Surprising how much stronger they make the A panel. Next update will hopefully see the wings as part of the car. Then I'll tackle the hood pins

#38
Posted 27 January 2013 - 11:55 PM
Pre-spot welded, gaps a little off


Fully welded and dressed

Also had this little guy to put in.


I remember when that area was just a hole. Nice to have something done. I also couldn't resist tacking on a bit of the brightwork after putting it all together again for a fit check.

Looks awesome! I find I do this a lot :) Anyway, that was it for today. Next outing will see the wings become permanently attached. I'll then work on the hood pins and seal the gaps. I still have the right side outer sill to tack on, but I wanted to seal inside before doing so. Now that I have a few things to seal, I can just do it all in one go. Saves the sealant from drying in the tube.
That's it for this update. Cheers!
#39
Posted 28 January 2013 - 08:59 PM
#40
Posted 28 January 2013 - 09:07 PM
#41
Posted 29 January 2013 - 11:37 AM
#42
Posted 02 February 2013 - 11:57 PM

Finally got the wings welded in place. Not a lot of photos this time as it is pretty straight forward, but I have a few.
Top in work

Set up for the underside

Underside. Of note, you can see my little magnetic flashlight here. It is actually a grill light, but it works great for welding. Can position it most anywhere and it doesn't auto darken the helmet.

And done.





Got a good look at my next bit of work while underneath. After the other side, this shouldn't be too hard.

All in all, pretty good day. Cheers!
#43
Posted 10 March 2013 - 01:13 PM
Actually needed to fill in those two indentations before proceeding. Not terribly difficult, but took a little time.




Again, not really exciting, but it is progress. Since it is kind of a boring update, thought I'd give you a preview of my next project...

1958 VW ragtop...cheers!
#44
Posted 10 March 2013 - 05:34 PM
#45
Posted 10 March 2013 - 07:04 PM
1 user(s) are reading this topic
0 members, 1 guests, 0 anonymous users