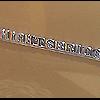
3D Printing - The Turnaround For Long Lost Parts?
#31
Posted 09 July 2013 - 08:56 PM
#32
Posted 09 July 2013 - 10:27 PM
I know its not 3D printing but i kinda remember martin at MRA was trying to CNC machine a 295 cylinder head
Give them a few years of developement and these modern technologies will be able to replicate almost anything from a cylinder head casting to a speedwell centre binnacle
#33
Posted 09 July 2013 - 10:46 PM
The process will never be used to make ball joints. In any case, do you know of even one that did not fail due to incorrect shimming? Almost always, they are set up too tight, and fatigue failure is guaranteed. Making ball joints does not require anything like a 3D printer, only a "screw machine" lathe (a sort of mechanically configured precursor to an NC machine), or a proper NC lathe and a fairly simple program. With a very good tool, you will get a better finish off the lathe than the junk suppliers are getting after grinding. You could even run a few off by hand, if you have a simple radius turning attachment, and you could grind them to a high finish with a tool and cutter grinder. All the sort of stuff that you can read about in magazines like "Model Engineer's Workshop". The hard part is picking the correct material (maybe someone knows the correct grade of steel?) and applying the appropriate heat treatment to harden them after machining, without causing them to become brittle.
But returning to what 3D printers can do, they are only useful for very small quantities of parts, as they are of necessity slow. But if you need a one-off plastic bit like maybe a gear for your odometer, or a moulded body for an odd type of electrical connector, they may well be the best way forward. Never for structural parts, but maybe a metal printing process would just about manage some carburettor parts or something like that. I see them as being of most use to owners of very rare cars, where there are no other ways of replacing broken parts. Any Mini part will be needed in quantities well above the viable economic limit for printing.
And yes, you can build yourself a working 3D printer for well under £1000, which will be able to print the plastic parts to build more printers.
Thomas Watson, former CEO of technology giant IBM, once said he thought there was a market for maybe five computers in the world. Never say never with technology, a lot of research is being invested in these machines now and soon they could be able to print much more significant parts than the relatively simple prototypes of today - this technology is only a baby!
#34
Posted 09 July 2013 - 11:08 PM
They also said for Windows 3.1 that 64 k of memory was adequate.
#35
Posted 09 July 2013 - 11:09 PM
Its worth noting that the machine in the video is a good 60k.
You could build an extrusion based machine at home for £500 if you were really careful and had a an old pc lying around.
#36
Posted 10 July 2013 - 08:59 AM
I've seen titanium 3D printed into mechanical parts. The process used a highly modified CNC laser cutter - a bed of Ti powder is laid down and the laser does a pass melting the surface layer. A trough and wiper then passes over laying a fresh bed of powder. Then the laser does another pass. It all has to be done in an inert atmosphere for the sort of quality required. Whilst it's a very simple concept getting it perfect takes a lot of work - getting each layer fused perfectly with the layer below relies on just the right density and thickness bed of powder combined with just the right power of laser at the right speed over the surface. Once the parts were complete I think they were heated to just shy of liquid to make sure of the fusing of the layers and to anneal them - no mean feat with Ti.
It's a very expensive process but the kit is out there right now to print every component for a high performance engine - even a jet engine or turbine. Because of the last step you couldn't print an assembled engine - the parts would fuse together.
It's getting cheaper but for the moment a lot of these parts would be cheaper to make by conventional methods. I have thought of some of the plastics that are NLA though. Aren't there some plastic bushes on the early Cooper driveshafts that are impossible to get nowadays? Some of that stuff would lend itself to the current high resolution printers but you would need to be making a wide range of parts for the cost to be less than dies for an injection moulding machine that anyone looking to manufacture this type of stuff would already have.
Iain
#37
Posted 10 July 2013 - 10:28 AM
Making a rubber bush is in essence a very simple but it plays a critical role in making your suspension or steering work correctly.
When Rover or BL etc designed their parts, each part is durability tested and will be checked with some sort of quality inspection. Duff parts are rejected and good parts are fitted. With the speed at which technology evolves and becomes cheaper allowing more people to access it, the risk of people making their own potentiality dodgy parts increases, thus increasing the risk accidents from failed home components.
#38
Posted 12 July 2013 - 08:12 AM
Could always seek out professional printers at least that way you have the backup as a consumer of quality of product rules and regs.
Something that popped up on the feed today: http://www.thingiver...om/thing:113865
#39
Posted 12 July 2013 - 08:30 AM
Interesting topic this - we do a lot of rapid prototyping (I work for a design consultancy) using these technologies to prove out designs at the conceptual stage. At present the cost of these machines (for anything of decent quality) is prohibitively expensive - even for a small business, which is why we use RP companies and outsource our prototyping.
Most replacement parts for the Mini are mass-manufactured which makes them uber-cheap (and less face it - lots of the bits for Minis are dirt-cheap) so I don't see much advantage to creating bits on an RP printer........but it makes total sense to make one-off replica parts of bits that are getting hard to get hold of or discontinued, or to create one-off designs for bespoke styling bits and the like.
One example for me would be the Clubman indicator lenses/backplates.........(not sure whether these are available yet - haven't looked for a few years but they weren't when I repaired mine)
One thing that sometimes gets overlooked in the hype over 3d printing (especially by the press) is that you need a 3D file to print from. Unless you're proficient in using CAD software then you'll be limited to what you can download off the 'net.
Edited by sherly, 12 July 2013 - 08:33 AM.
#40
Posted 12 July 2013 - 11:09 AM
1 user(s) are reading this topic
0 members, 1 guests, 0 anonymous users