I decided to de'seam the convertible, i'm replacing the front end with a flip front which includes the a-panels so half the work won't be needed there, and the rear posts don't need doing for obvious reasons!!!! i'm leaving the gutters though, otherwise water will get in to the rag top for sure!! whats the practice for the rear bumper seam??
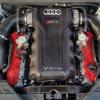
de seeming a mini shell
Started by
Spoonz
, Mar 11 2006 08:06 PM
18 replies to this topic
#16
Posted 28 March 2006 - 09:00 PM
#17
Posted 28 March 2006 - 09:15 PM
They way I've done it ( twice now - sonn to be thrice ) is..
Remove lights and petrol tank
Remove all the seam sealer ( if still there ) from the rear panel to boot floor joint on the inside, and then seam weld the whole joint.
The from the outside remove 4" to 6" sections of the bumper lip at a time and then seam weld where removed. work your way to the centre. Then start from the other end, and do the same...
Takes about an afternoon... then it's just a matter of blending in the panels with vast quantities of filler
If doing the seams up the back, then I would again remove the sealer from the seams, and weld together, but would also add a couple or three small plates to support the joint on the inside, then grins the seam away and weld again. As the panels are generally a better fit there, you may get away with just a skim of filler or if you know someone who can do it, lead fill it.
Remove lights and petrol tank
Remove all the seam sealer ( if still there ) from the rear panel to boot floor joint on the inside, and then seam weld the whole joint.
The from the outside remove 4" to 6" sections of the bumper lip at a time and then seam weld where removed. work your way to the centre. Then start from the other end, and do the same...
Takes about an afternoon... then it's just a matter of blending in the panels with vast quantities of filler

If doing the seams up the back, then I would again remove the sealer from the seams, and weld together, but would also add a couple or three small plates to support the joint on the inside, then grins the seam away and weld again. As the panels are generally a better fit there, you may get away with just a skim of filler or if you know someone who can do it, lead fill it.
#18
Posted 28 March 2006 - 09:15 PM
same as all the others, chop a bit out at a time and weld it up, alternate to reduce the risk of warping, jobs a good un
giving mine bum lift surgery in the summer


#19
Posted 28 March 2006 - 09:42 PM
Yes its weak if done wrong.
Yes its super strong if done right. Anyone saying its a death trap seems a little narrow minded that the fact deseaming involves seam welding the panels together.. where as seams are just 2 return lips spot welded at various distances with a clip on cover over the top....
I have done about half my mini so far. Its a long job if you have C**p tools. Decent welder(gas helps), some decent soft grinding pads and a good panel hammer and panel dolly. As well as mentioned, fair bit of good body filler.
You might find how badly panels on mini's are lined up from the factory, so you need to be pretty good with rubbing filler, or know somebody who can finish it off after getting it into shape.
The way I have done it is cut of the seams in 3-4" lengths, leaving around 1/8th inch left sticking up, this ensures a good weld without burning through.
Make sure the surrounding area and back is clean from sealer, paint etc etc... weld the 3-4" at a time, quickly but neatly and while the weld is still glowing hot, give it a good smack with a panel hammer to try and recess the weld abit.
After completing one pillar or seam, run the grinder along your welds until they are good to skim over.
Skim with filler and have plenty of hours fun rubbing down!
Yes its super strong if done right. Anyone saying its a death trap seems a little narrow minded that the fact deseaming involves seam welding the panels together.. where as seams are just 2 return lips spot welded at various distances with a clip on cover over the top....
I have done about half my mini so far. Its a long job if you have C**p tools. Decent welder(gas helps), some decent soft grinding pads and a good panel hammer and panel dolly. As well as mentioned, fair bit of good body filler.
You might find how badly panels on mini's are lined up from the factory, so you need to be pretty good with rubbing filler, or know somebody who can finish it off after getting it into shape.
The way I have done it is cut of the seams in 3-4" lengths, leaving around 1/8th inch left sticking up, this ensures a good weld without burning through.
Make sure the surrounding area and back is clean from sealer, paint etc etc... weld the 3-4" at a time, quickly but neatly and while the weld is still glowing hot, give it a good smack with a panel hammer to try and recess the weld abit.
After completing one pillar or seam, run the grinder along your welds until they are good to skim over.
Skim with filler and have plenty of hours fun rubbing down!
0 user(s) are reading this topic
0 members, 0 guests, 0 anonymous users