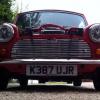
Headlamp Soldering
Started by
minidave1991-89
, Feb 09 2013 04:38 PM
20 replies to this topic
#16
Posted 10 February 2013 - 03:10 PM
I've never had a problem with a soldered joint. Crimping is often just a temporary repair or a bodge, might as well just be a twist and tape.
But I always use Lead Solder, Lead free doesn't stick very well.
But I always use Lead Solder, Lead free doesn't stick very well.
#17
Posted 10 February 2013 - 03:21 PM
the temporary crimped joiners cancorrode and fail very quickly. a proper brass crimped connetor is really the only thing that should be crimped on. we rent out a part of ur garage to auto electritians, and they swear by this and solder all joints.
they do have a large stock of the old proper bullet connectors, found on the early-ish minis as they are very good. much better and thighter fit than the newer orrible ones.
they do have a large stock of the old proper bullet connectors, found on the early-ish minis as they are very good. much better and thighter fit than the newer orrible ones.
Edited by Artful Dodger, 10 February 2013 - 03:21 PM.
#18
Posted 10 February 2013 - 03:55 PM
Ford banned all soldered wire joints years ago, because of high warranty claims
AML, Jaguar, Land Rover followed suit soon afterwards, most Japanese cars have always prefferred crimps.....
Porshe, BMW, Mercedes stopped using solder on wiring about 20 ish years ago
This is from supplier information from companies like
Yazaki
Leoini
Lear (UTI)
Delphi....
These are the big hitters in the automotive wiring harness design and manufacture and if soldering was of any benefit then they would be more than capable of tooling up for it and at a cost that is far cheaper than using copper based crimps...
Copper being a lot dearer than lead or tin based solders..
AML, Jaguar, Land Rover followed suit soon afterwards, most Japanese cars have always prefferred crimps.....
Porshe, BMW, Mercedes stopped using solder on wiring about 20 ish years ago
This is from supplier information from companies like
Yazaki
Leoini
Lear (UTI)
Delphi....
These are the big hitters in the automotive wiring harness design and manufacture and if soldering was of any benefit then they would be more than capable of tooling up for it and at a cost that is far cheaper than using copper based crimps...
Copper being a lot dearer than lead or tin based solders..
#19
Posted 10 February 2013 - 03:59 PM
I've never had a problem with a soldered joint. Crimping is often just a temporary repair or a bodge, might as well just be a twist and tape.
But I always use Lead Solder, Lead free doesn't stick very well.
Rubbish... Lead free sticks fine if you do it properly by using a flux on the wires first. It will enable the solder to flow and form a proper bond.
#20
Posted 10 February 2013 - 04:07 PM
Some crimps that are available are rubbish, however if you use the Tyco products PIDG crimps these are used by both the Military and Automotive sectors for repair work.
The 2 main issues with soldering wires are
1) fatigue at the point where the solder wicks to.
2) Corrosion due to the flux.
If you want to get good results then don't solder, however if soldering is your only option make sure that the above issues are minimised.
The 2 main issues with soldering wires are
1) fatigue at the point where the solder wicks to.
2) Corrosion due to the flux.
If you want to get good results then don't solder, however if soldering is your only option make sure that the above issues are minimised.
#21
Posted 12 February 2013 - 01:27 PM
The best joint from every point of view will be a crimp, properly made, with the proper size of terminal for the wire, and done with the correct (expensive) tool. Next best is soldering, given a modicum of skill, and worst, by a very big margin, are crimps made by the cheap, nasty tools which are readily available.
0 user(s) are reading this topic
0 members, 0 guests, 0 anonymous users