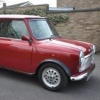
Top Engine Steady Broken Off Bulkhead
#16
Posted 30 May 2013 - 07:44 PM
#17
Posted 30 May 2013 - 07:49 PM
#18
Posted 30 May 2013 - 08:00 PM
Bolting it in would be a tight fiddle with all things in place but not bad if it works out cheap enough
Haha yeah a tmf row may begin on the poly vs rubber gurus so i'l shhush
#19
Posted 30 May 2013 - 08:56 PM
How do. I happen to have a spare steady bracket lying around in my shed, you can have it if you want?
#20
Posted 30 May 2013 - 09:10 PM
Yes, you have to drill the holes on the bulkhead. I removed clutch master and slave as a unit since the bracket is slotted for the fluid pipe. Installing the nuts and washers from the inside was not easy but doable. I had to replace the upper bracket under the clutch master too since it was cracked.
How did you get to the other side to put the washers and nuts on? Did the bolts come out behind the dash or perhaps under the carpet (as in where it is almost vertical behind the pedals)?
How do. I happen to have a spare steady bracket lying around in my shed, you can have it if you want?
Do you mean a repair panel to be welded on? If so, then yes please . Blackpool is probably a tad too far to come and pick it up, so how much do you want for it/postage? Even if I put on a minisport 'ultimate steady' as a quick fix, it will still be good to get this for when I do it properly.
Edited by Calderwood, 30 May 2013 - 09:11 PM.
#21
Posted 30 May 2013 - 10:03 PM
Yes, you have to drill the holes on the bulkhead. I removed clutch master and slave as a unit since the bracket is slotted for the fluid pipe. Installing the nuts and washers from the inside was not easy but doable. I had to replace the upper bracket under the clutch master too since it was cracked.
How did you get to the other side to put the washers and nuts on? Did the bolts come out behind the dash or perhaps under the carpet (as in where it is almost vertical behind the pedals)?
If you look at the picture in post #14 by sonikk4, there is a cavity above and to right of steering bracket that looks whitish in the picture, that is where the nuts will go . Obviously, with the pedals in place it is more difficult but not impossible since that is how I did it with my "sausage fingers". Long socket extensions and universal joints are needed as well as open and closed end spanners and a helper would be great. I did have the engine out when drilling.
#22
Posted 30 May 2013 - 10:11 PM
There is another option but will still require some welding. decide on how many bolts you want to use to secure the bracket. Pitch them in then drill through the bracket and crossmember. I would suggest using an 1/8th drill here.
Now depending on the bolt size you are going to use, use a good quality stiff nut but not a nyloc. Drill a hole to the size of the external diameter of the nut, Weld the nut into the crossmember but remember to ensure it sits flush and square in the hole.
Open up the holes in the bracket and then fit. Captive nuts and an easy to remove bracket if required.
#23
Posted 30 May 2013 - 10:43 PM
Do not under any circumstmces use an ultimate engine steady as a substitute for the broken top steady. It is in entirely the wrong place to react the engine torque against the standard lower steady, and will result in the engine trying to rotate about a vertical axis, most likely breaking both main mounts fairly soon, and possibly breaking the exhaust or even the manifiold.
Also please disregard the suggestion about using B&Q threaded rod. It is only mild steel and no way suitable for use anywhere on a car.
Welding the bracket properly is easy, almost trivial, on models without a servo in the way. In this case the servo is a real nuisance, but there is probably no alternative to taking it out. That is the major part of the work, and of course bleeding the brakes afterwards.
The bolted bracket suggestions are ok, in fact the stainless one looks seriously impressive, but anyone who has ever needed to access the brake and clutch clevis pins will know why I for one would prefer a welded repair. It is a real pain to get inside the crossmember with the nuts. Welding needs only one sided access, although a squirt of Waxoyl should be applied inside afterwards as the welding will burn off the paint. And, a MIG torch will often go where a drill will not.
I welded one some years ago. No servo in the way, and the job only took a few minutes. Just a couple of plug welds, and a seam across the top of the bracket, where the stress is highest.
#24
Posted 01 June 2013 - 01:21 AM
There is another option but will still require some welding. decide on how many bolts you want to use to secure the bracket. Pitch them in then drill through the bracket and crossmember. I would suggest using an 1/8th drill here.
Now depending on the bolt size you are going to use, use a good quality stiff nut but not a nyloc. Drill a hole to the size of the external diameter of the nut, Weld the nut into the crossmember but remember to ensure it sits flush and square in the hole.
Open up the holes in the bracket and then fit. Captive nuts and an easy to remove bracket if required.
Hang on a minute lads, I've got a great idea! What about cutting a flat strip of sheet metal matching the bracket where the four holes are. Then match drill the strip to the four holes on the bracket and match drill the bracket holes to the bulkhead on the proper location. Now get the four nuts as sonikk4 proposed and weld them to the flat strip of sheet metal lining them up with the pre drilled holes. During the installation all you need is to be able to push the "nut plate" against the bulkhead from the inside while engaging only two bolts from the outside. The other two bolts will already be aligned with their respective nuts. No sockets with long extension or special contortions needed nor any welding on the car.
#25
Posted 01 June 2013 - 03:22 AM
Go one better and make it a stud plate.
#26
Posted 01 June 2013 - 07:02 AM
Good idea, but as I said, if you can get a drill in there, you can also get a MIG torch in. It comes down to individual preference, and any concerns that you have about originality.
#27
Posted 02 June 2013 - 05:00 AM
Edited by Captain Mainwaring, 02 June 2013 - 07:41 AM.
#28
Posted 02 June 2013 - 03:25 PM
It took me 3 minutes. I must be slow.
#29
Posted 02 June 2013 - 04:42 PM
Its really down to what tools you have available and whether the OP can weld. Also even if there is a welder available will the weld be strong enough.
The OP has been given a few choices so it will be up to him which will suit his needs to be honest.
#30
Posted 02 June 2013 - 11:43 PM
Its really down to what tools you have available and whether the OP can weld. Also even if there is a welder available will the weld be strong enough.
The OP has been given a few choices so it will be up to him which will suit his needs to be honest.
Uhm true, and even if the OP can weld, does he have a welder? Does he have wire and gas? Has he paid the electricity bill?
He could always phone a friend who can weld, but then the same caveats would apply.
One thing that is sure....the weld be be strong enough.
1 user(s) are reading this topic
0 members, 1 guests, 0 anonymous users