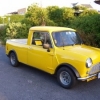
Fabricating A Fuel Tank
#1
Posted 04 October 2013 - 08:23 AM
Would you butt weld or lap weld/ joggle the edges to be welded?
Mig or tig weld the tank?
Last question, how would you test the tank, is it pressure tested or is there another way of ensuring that there are no leaks etc.?
Thanks in advance :)
#2
Posted 04 October 2013 - 08:44 AM
#3
Posted 04 October 2013 - 08:57 AM
How did you test it?
#4
Posted 04 October 2013 - 09:05 AM
#5
Posted 04 October 2013 - 09:08 AM
Commercially they are pressurised and dunked in a bath of soapy water - bubbles means leaks.
It's possible to do it with MIG but you will have leaks that you need to go back to (how many and how bad depends on the skill/experience of the welder). Once you've got them all down to pinholes Frost (and no doubt others) do a kit to repair tanks that consists of a resin coating that you pour into the tank and then roll the tank around to ensure it's coated all over. Usually designed for older tanks which are hard to replace but no problems doing it to seal a brand new tank so long as the welding is structurally sound and you really are just using it to seal pinholes in the welds.
Iain
Edited by ibrooks, 04 October 2013 - 09:13 AM.
#6
Posted 04 October 2013 - 09:10 AM
#7
Posted 04 October 2013 - 09:14 AM
Ok thanks for the tips on pressure testing.
Any suggestions with regards whether or not to butt weld or lap/joggle the edges together?
I am looking at fabricating a tank out of steel.
#8
Posted 04 October 2013 - 09:27 AM
But weld, with oxy-acetylene torch,(old school) or Tig if you have access, laps/joggles are harder to get a good seal and if not done correctly can promote distortion and later on, corrosion.
Others may have a different opinion, but this is how I would go about it.
#9
Posted 04 October 2013 - 10:44 AM
Alloy and tig weld, fabricated many fuel, water, oil tanks for kit cars, boats and buggies. Pressure test and also fill test.
#10
Posted 04 October 2013 - 11:58 AM
The company next door to me used to make fuel cells/tanks for Naval and Air Force use. The did a couple of different types of testing, non-destructive and destructive (destructive is great fun, lol!).
To test the tank for leaks etc. it needs to be pressure tested. DO NOT try pressurising the tank with compressed air, this makes for a very dangerous explosion similar to that of a Frag Grenade if the tanks splits/fails. Instead, fill a large vessel with water with a little washing liquid and then submerge the tank. Next, seal the all fuel hose outlets except one. Fill the tank with water to the top of the filler neck and then seal that too. NOW you can add a little air pressure to the tank via the remaining fuel hose. You only need to be just above atmospheric pressure, since the tank should never be under any internal pressure anyway. If the tank has any leaks, the pressure will drop. Bubbles may form. If the tank does rupture, the water inside and the water outside in the tank will contain the pressure change and stop the "explosion". It's a bit of a bugger getting all the water out afterwards but much safer than trying to pump straight air in to the tank!
This way is very similar to how the test scuba diving cylinders (hydrostatic testing).
Edited by mattiek, 04 October 2013 - 12:00 PM.
#11
Posted 04 October 2013 - 02:32 PM
For my grasser (micra) i use RSM in manchester. He does mainly motorsport stuff but if you ask sure he will sort something out
Link to his ebay items.
http://www.ebay.co.u...utograss&_sop=7
#12
Posted 04 October 2013 - 06:18 PM
#13
Posted 07 October 2013 - 11:32 AM
Just pressurise with air - you only need to go to 5psi or so and that's not going to give you a catastrophic failure or shrapnel even if it does split a seam. Scuba tanks are tested to thousands of psi so a different kettle of fish altogether.
Iain
#14
Posted 08 October 2013 - 12:54 AM
Imo TIG welding is far easier than oxy welding (and is a bit outdated to weld with) apart from round the filler neck etc were you would probably need to use the torch.
Edit- didn't realise you didn't state what metal, I responded as to you using aluminium which would be the best choice
Edited by jmmini, 08 October 2013 - 12:56 AM.
#15
Posted 08 October 2013 - 05:54 AM
For aluminium, yes Tig is the way to go. but as it was stated that he was using steel, My preference would be for Oxy as it is easier.
But then, this describes me perfectly " (and is a bit outdated ) "
Edited by Yoda, 08 October 2013 - 05:55 AM.
1 user(s) are reading this topic
0 members, 1 guests, 0 anonymous users