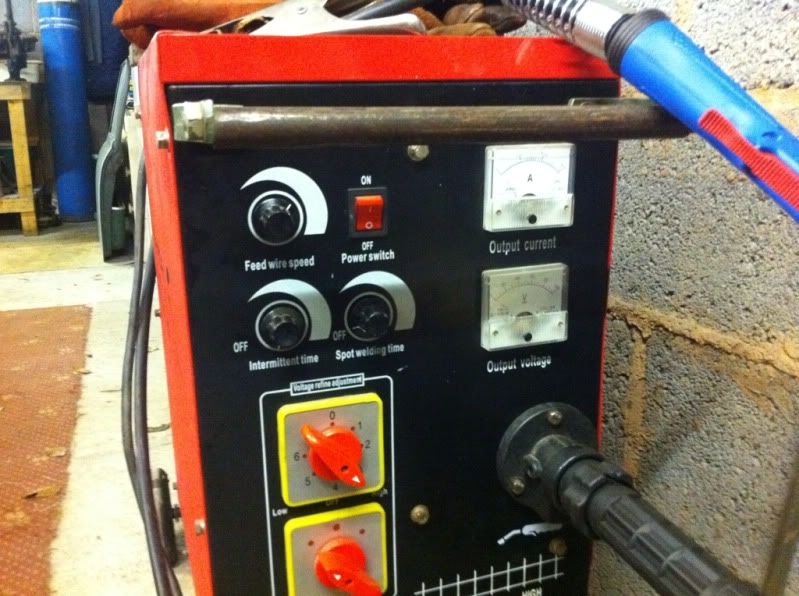
Edited by Daz1968, 16 April 2015 - 05:54 PM.
Posted 16 April 2015 - 05:54 PM
Edited by Daz1968, 16 April 2015 - 05:54 PM.
Posted 16 April 2015 - 07:46 PM
yeah so i figured out what i was doing was turning the power up and decreasing the wire speed.......
Posted 16 April 2015 - 08:22 PM
Posted 17 April 2015 - 06:32 PM
i had another go today and what a difference!!!!
i know the welds aint pretty but i didnt want to grind them too much just incase the welds wernt the best haha
went from this
to this :)
then tackled this part
dont think its terrible for a first go
Posted 17 April 2015 - 06:46 PM
Posted 17 April 2015 - 07:00 PM
Glad you got this sorted out, before long you'll be adjusting the weld settings based on noise and feel It took me ages to get it right but after watching loads of You Tube videos and asking questions on here and the Mig Welding Forum (Which also has some great tutorials on setting up a welder, I am now pretty proficient especially with thin stuff (Which is most of the Mini!!).
P.S Just about to tackle the same repair as you have shown here, after I finish the floor that is
Posted 18 April 2015 - 08:10 PM
Posted 22 April 2015 - 11:08 AM
Have also recently bought a Clarke 135TE, and like yourself its taken me quite a lot of practice, but thought i'd share my findings with you in case it helps.
I found that having the power setting on 1 - Min, wire speed around 5, and holding the torch just 20 degrees from vertical about 3/4mm from the metal surface to be the most successful with thin metal welding. I had the gas bottle that came with the welder on full as well, as the guy in machine mart told me the 1-6 marked on top of the gask pressure regulator is rather useless and its best just to consider it as on or off! As stated above, doing a tack weld every 30mm or so and then doing short bursts of welds between the tacks stops the metal getting to hot and the weld pool to big and hence blowing through.
hope that helps :) keep us up to date with your findings on settings for this welder, i'd be interested to know
Posted 23 April 2015 - 06:41 AM
Posted 24 April 2015 - 08:25 PM
I have a 135TE. The 2 settings i use are: 2 MIN and 7 for wire speed. Also 1 MAX and 6 wire speed for the large gaps and/or if previous setting blows through. I mainly weld 1.2mm to my mini. Also i use 0.6 wire and 10-15 CFM Hobyweld 5 argon mix gas. Hope that helps. heres and example of what i managed tonight.
From the Welded side https://dl.dropboxus...05/DSC_0046.jpg
From the inside https://dl.dropboxus...05/DSC_0050.jpg
Needs some touching up the grinder and some paint but you can how those settings work.
Edited by Ginge620, 24 April 2015 - 08:48 PM.
0 members, 1 guests, 0 anonymous users