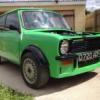
Galvanised Body Shell
#1
Posted 15 June 2015 - 03:55 PM
#2
Posted 15 June 2015 - 03:57 PM
Hot galvanising would warp it.
#3
Posted 15 June 2015 - 04:08 PM
+1 on warping
I make machinery that is 4mm + thick and that warps some times when hot zinc dipped
+ all the cavity's would hold zinc
electroplate would be better , but would require a massive tank , & clever electrode placement
make a shell out of galv steel would be better
#4
Posted 15 June 2015 - 04:13 PM
The company I have contacted near Southampton airport do a cold dip. I didn't think the cavitys would be that much of an issue seeing that a mini shell is 85% single skin??
#5
Posted 15 June 2015 - 04:33 PM
Edited by Steve220, 15 June 2015 - 04:34 PM.
#6
Posted 15 June 2015 - 04:53 PM
#7
Posted 15 June 2015 - 04:59 PM
With proper care and attention to your repairs, body sealing and paint followed by liberal coatings of cavity wax, there is no reason why your mini won't last well.
Remember it was only the poor sealing up and paint at the factory followed by years of bodge repairs that lead to most Mini's being rotten anyway so i would just spend you money getting the shell preped right in the first place and then maintaining it properly afterwards
#8
Posted 15 June 2015 - 05:44 PM
wish I could pay the original owner back in 89 to get mine zebarted
but I wouldn't have got it now - would have been too £xpensive
hind sight is a wonderful thing
#9
Posted 15 June 2015 - 06:21 PM
All is good with it but when I took loads of pictures before it went I took one of the sills both sides and as the flash went of you can see what looks like surface rust in between both sills I.e. Inners and outters. I will be getting it back once fully welded as I want to finish myself.
Just have not had the time what so ever to work on it as I have been busy getting the other pig on the road.
I have all paper work for it and the latest is 2010 in total it had about £2,500 of work to the shell done but then left in a quick primer for one reason or other. And the void between sills is the only place that is concerning me.
As I want it in zinc befor the top coat it was suggested to me about having in galvinised so thought I would cheek up on it.
#10
Posted 15 June 2015 - 07:22 PM
If it was galvanised would it not be really difficult to weld? Might have to get some special primer as well before you can paint it.
#11
Posted 15 June 2015 - 07:30 PM
It would also be about 70-80 kilos of zinc I believe. Like having an extra passenger all the time.
#12
Posted 15 June 2015 - 07:35 PM
#13
Posted 15 June 2015 - 09:01 PM
i think the cons outweigh the pros.
Like i said above, proper preparation and attention to detail will make for a long lasting shell
#14
Posted 15 June 2015 - 09:30 PM
Our Late Production Moke Shells from Nov 1979 on were Galvanised. Some were actually Hot Dipped though most were made from Galvabond.
The Hot Dipped ones were the better of the two as everything, including all the welds got Galvanised. My Wife's Moke was one of these.
It doesn't warp the bodies when done by the right process, after all, they do sell Hot Dipped Galvanised Sheet Metal down to 0.5 mm thick off the shelf and that's awfully flat.
#15
Posted 15 June 2015 - 11:14 PM
Maybe BH should make a super shell out of stainless steel, ala Delorean.
Edited by peter-b, 15 June 2015 - 11:17 PM.
1 user(s) are reading this topic
0 members, 1 guests, 0 anonymous users