Do you place a plain (flat) washer under the crank pulley bolt ?
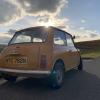
Loctite 243 Uses

Best Answer Spider , 12 October 2020 - 06:56 PM
I keep reading that lock tabs are too soft these days, so I’m going to use a thread lock instead.
Is 243 ok for the crankshaft damper pulley bolt, cam nut and also the flywheel bolt? How is the torque setting affected and how long should it be left for a full cure?
The 243 is what I've been using on those fasteners (and others) for the past 15+ years now.
I use the factory Torque numbers for all, except for the Damper and Flywheel Bolts. The Factory Number here for the Damper is 70 ft / lb, however, nearly always I found that was not enough, even when I using locktabs. Chatting with a few other locals, they have found the same. I Torque these up to 100 - 110 ft/lb and that does the trip. One of our local commercial shops does them to 125 ft/lb, I had my nose in one of Clive Trickey's books the other day (he was a well known racer in the 60's) and I note he was doing them to 150 ft/lb
I've found going to 110 ft/lb hasn't been an issue and in fact, solved one. I'm sure the reason this fastener tends to work loose is due to the normal Torsional Vibration at that end of the Crank, effectively working like a rattle gun.
The Flywheel Bolt I do to a minimum of 150 ft/lb. I've not had issues with the bolt itself coming loose here, but I've found the 115 ft/lb quoted by the factory very marginal to totally inadequate to stop fretting of the Flywheel on the Crank Taper. Looking at the issues many have removing their Verto Flywheels, it's apparent to me that's especially with that set up, 115 isn't nearly enough. IMO, the 'secret' to making Flywheel Removal painless is to get it on very tight in the first place, yes, that sounds back to front I know, but when they sit tight and not fret, they will come away clean and fairly easily, however, when they Fret, I think we've all seen many here have to take to the flywheel with an angle grinder to get them off and a few have had buggered crankshafts from fretting. Tight is right

#31
Posted 26 June 2025 - 07:12 AM
#32
Posted 26 June 2025 - 10:13 AM
I interpret it as that you do use spring washers and if so, why? I have designed and dimensioned a lot of bolt/nut interfaces and cannot work out why you would like an extra layer (or inconsistent spring) in a clamping joint. It certainly does not make the clamping force more consistent.
Same reason they are used by many millions, including BMC / Leyland / Rover, in zillions of joints.
Taken from the RS Webpage;-
" The primary purpose of spring washers is to provide tension and preload in a joint assembly. This helps to maintain clamping force and prevent loosening or loss of tension due to vibration, thermal cycling, or other factors."
I do know that! The question is if it really works. The sum off all clamped parts stiffness together with the pretension is what makes up the clamping force. How much of the specified torque that actually ends up as clamping force is highly dependent on settlement and friction in interacting surfaces and threads. More interfaces makes more settlement and more friction, i.e. less wrench torque ends up as clamped force. On top of this is the uncertainty in what the friction really is in each of these interacting surfaces. To cut it short, more clamped parts gives a larger portion of uncertainties and a larger variation in resulting clamping force (even though assuming strictly cleaned surfaces and threads).
So, I am not convinced that a spring washer (with a highly unlinear stiffness characteristic) will (without doubt) contribute to an initial clamping force that is larger than external load due to normal operation.
As mentioned many a times, spring washers are useless - or even detrimental. Conical spring washers require a meticulous torque calculation and application to work. Star washers cannot deal with impact forces at all. The only system to work is Nordlock-washers, but that is expensive. Lock nuts are no better by the way.
I have, for quite some time now, switched to Loctite too but do use spring washers in addition on restoration work, to imply originality.
Edited by MiNiKiN, 26 June 2025 - 10:15 AM.
#33
Posted 26 June 2025 - 10:36 AM
#34
Posted 26 June 2025 - 10:36 AM
As mentioned many a times, spring washers are useless - or even detrimental. Conical spring washers require a meticulous torque calculation and application to work. Star washers cannot deal with impact forces at all. The only system to work is Nordlock-washers, but that is expensive. Lock nuts are no better by the way.
I have, for quite some time now, switched to Loctite too but do use spring washers in addition on restoration work, to imply originality.
I don't know if it's mentioned elsewhere in this thread, but there are different Grade Spring Washers.
If the Spring Washers are poorly made, or too light, yes, I agree, they are useless or even detrimental, as they can crack or simply uncoil, leaving the bolted joint loose.
However, decent Spring Washer work extremely well. I just about swear by them. When the right washers are undo is when you'll find out if they are any good. Most (all) that I use need a decent 'crackin' to start them off and need spannering for more than a full turn before they can be spun off with the fingers.
#35
Posted 26 June 2025 - 11:20 AM
When I said elsewhere, I was talking about engineering rule books
If they work in your applications, congrats you lucky bastard Probably because you haven't had critical load cases yet.
As shown in this video, the critical load case is shear vibration, rather than axial vibration. Though this is a promotional video, I does provide some good visualisation based the standardized Junker test (DIN EN 65151 und ISO 16130)
https://youtu.be/IKw...pmXzcX7S1MPACST
#36
Posted 26 June 2025 - 05:49 PM
For critical load, eg, Big Ends, Mains, Flywheel, Harmonic Damper etc, I wouldn't use them in these places, but on the Chassis, Suspension etc, in many places here I am happy to use them, however, if it's a part that's subject to lots of cyclic movement, eg, lower inner arm pin, shocks etc, I use Cone Locks. On the Radius Rods, I use Lock Nuts.
#37
Posted 26 June 2025 - 06:52 PM
The one point of using LOCTITE that gets over looked is it prevents corrosion in the joint, threaded or bushed. Plus point here the parts don’t corrode together. Which means that taking apart is a whole lot easier.
I use LOCTITE 222 on all threaded assemblies that don’t call for it and 243 for those that do.
Use LOCTITE 638 on core plugs and LOCTITE 518 on flanged assemblies such as thermo housing etc.
#38
Posted 27 June 2025 - 07:03 AM
I'd like to know the best (correct way) to apply loctite. Also interested to hear you say it makes the taking apart process easier. My fear with loctite is that I will not be able to disassemble.
#39
Posted 27 June 2025 - 07:16 AM
I'd like to know the best (correct way) to apply loctite. Also interested to hear you say it makes the taking apart process easier. My fear with loctite is that I will not be able to disassemble.
Loctite do have some good guide, but 99% of the time, I clean the parts as I normally would, then give them a final clean with Paint Thinners, then apply the Loctite.
Taking apart easier ? Definitely not ! I've found additional force is needed to 'crack' the fasteners and even then, they need to be spannered off to about the last 3 to 5 threads.
The Red Loctite is one to be careful of, it's permanent and will damage threads unless it's first 'released'. Usually warming the parts up to about 150 degrees will be enough to get it to release.
#40
Posted 27 June 2025 - 08:47 AM
A couple of things on the last two posts
1, One don't go on colour, there are high strength red threadlockers and some thread sealers so low strength. Always go by the numbers as different regions have different grades as front line products.
2, Easier to get apart - Yes and possibly no. LOCTITE 222 is a low strength thread locker, basically designed for M6 and small so you don't snap the head of the bolt/screw. So basically what ever on Torque you have put to the fixing the off torque will be 80% of that. It also doesn't have any prevailing torque. Whats that? Prevail torque is whats needed once you crack the joint, some high strength threadlockers have a higher prevailing torque than the break torque, this is for assemblies you really don't ever want to take apart. Think about fixing in prison cells, you don't want things coming undone easily in these situations.
Reason I say easier is by putting LOCTITE 222 or 243 (both designed for regular maintenance and to be taken apart with hand tools) stops these corroding together. LOCTITE threadlockers cure with metal to metal contact and absence of air and it cures to a thermoset plastic. This stops water etc getting in, we have all tried to get assemblies apart from under the car that have just fused together, yes the end of bolts will still corrode but you can clean this off easy enough but the thread in the joint is protected.
Application.
Use a good cleaner - LOCTITE 7063 is the front line cleaner, be careful with cheap brake cleaners as they can leave nitrates on the surface which can inhibit he cure. LOCTITE 243 is oil tolerant so will work with as received bolts but think of it this way. The LOCTITE will try and adhere to what on top, so you want it to adhere to the bolt and housing so a clean surface will allow product to secure to the substrates.
If its a blind hole apply LOCTITE to the hole (female thread) won't hurt on the bolt as well. This is key, if you apply to the bolt on the blind hole only as you screw in it creates a seal and all the air trapped in the hole pushes the LOCTITE out so you get very little in the joint. If a through hole then apply to male thread (bolt) as no pressure LOCTITE gets fed in.
https://www.henkel-a...eadlocking.html
#41
Posted 27 June 2025 - 12:11 PM
Just checked - I've got 638 in my garage. Looks like I need some 222 or 243
#42
Posted 27 June 2025 - 03:26 PM
Just checked - I've got 638 in my garage. Looks like I need some 222 or 243
Don't put 638 on your bolts, that is a high strength retainer - basically higher strength than a high strength Threadlocker!
Fine for core plugs or anything else you don't want to get undone!
#43
Posted 27 June 2025 - 04:37 PM
See that's why just saying loctite them in has always scared me. With all the numbers etc, it's like learning a foreign language!!
#44
Posted 27 June 2025 - 05:41 PM
See that's why just saying loctite them in has always scared me. With all the numbers etc, it's like learning a foreign language!!
There's only 3 I use on Minis;-
263 (Red) - this is a high strength one for small fasteners and stuff you never want to undo. Needs to be heated to release. I hardly use much at all.
243 (Blue) - this I use for probably 95% of 'loctite' applications. It has some gap filling, I use it for locking the Ball Joint Cups, the Bolts holding the Main Mainshaft Bearing Retainer, Flywheel, Damper and Cam Fasteners, Oil Plugs In the Block) for thread sealing, Freeze Plugs, lots and lots of 'stuff'.
609 (Green) - This is a retaining Compound. I use this on the Mainshaft Bearing in to the Case, and on the Cups of Wheel Bearings.
While they have available various cleaners and 'activators' - and I have tried them - certainly for those I've listed above, all that's needed for cleaning prior to application is paint thinners. I was rather browned off with their cleaners as they come an a small and expensive aerosol can and soon after their first use, they loose all their gas. I regularly pull down my front hubs, including the Ball Joints. None of my engines leak Oil or Coolant. I can attest to the cleaning method I use as being good.
#45
Posted 27 June 2025 - 05:55 PM
Thank you. I'm saving this thread!
1 user(s) are reading this topic
0 members, 1 guests, 0 anonymous users