Seems to me the bonnet edges could use a fair bit of reinforcing. Mine had some bend cracks occurring right where the rear side gussets stopped. I placed some alu angle bracket along that affected area and stuck it in place using thickened epoxy (will have a better weld repair when its time for bonnet repaint). This was happening b/c my original hinge points were much too tight (previous restorer?) and lifting/closing bonnet was putting stress on the metal trying to move rotate the hinge points.
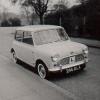
Bonnet Hinge Bulkhead Brackets.
#16
Posted 07 October 2021 - 06:19 PM
#17
Posted 08 October 2021 - 08:09 AM
Getting hold of the brackets shouldn't be a problem. You just need to put the word out and I'm sure someone can cut them from a scrap shell and send you them.
As for positioning, when the originals were removed, did they drill the spot welds from the engine side of the bulkhead?
If so, and they didn't drill right through, you should be able to see the spots from the back of the bulkhead. If so, this will greatly help with your chances of lining them up correctly as you can drill through the centre of the spots, use the new holes to position the brackets and then plug weld them kn from the inside of the car which will solve the access issue of the scuttle being jn the way.
However you approach it, you will need to do lots of careful adjustments to get them just right so maybe consider tacking them in once you are happy and then try the bonnet to make sure/make adjustments before fully committing.
Good luck
Ben
#18
Posted 08 October 2021 - 11:52 AM
#19
Posted 08 October 2021 - 09:38 PM
Finally got it sorted. To date this was the most awkward job I'd done on a Mini. Just wanted to say thanks for the help and suggestion as it turned out a lot better than I thought. Couldn't have done it without TMF.
#20
Posted 08 October 2021 - 09:48 PM
What did you do in the end?
#21
Posted 09 October 2021 - 03:12 PM
What did you do in the end?
You know you’re going to wish you hadn’t asked!
This was a friend’s car, so I got some rough measurements from my car and made up four angle brackets and fixed these to the bonnet hinges with a ¼” x ½” clevis pin and “R” clip so that we could get the bonnet off without loosening the hinge bolts.
The measurements I had from my car were from the underside of the scuttle and the side of the inner wing, to the bracket hole. So I offered up the new angle brackets and marked the bolt holes on the bulkhead. Unfortunately, the underside of the scuttle and the side of the inner wing was very vague from inside the car, and I couldn’t drill any of these holes from the engine side and so to transfer the markings to inside the car, I drilled a 1/8” hole below the bulkhead bracket and another to the side of the bracket, wherever I could get access, under the bonnet. Using two pieces of Meccano strip and two small magnets I made a flat adjustable compass with a spike one end and a pencil in the other, and transferred the markings by triangulation, one at a time to the inside. I drilled the holes from the inside and to my utter amazement lined up with the markings outside.
I indented to use floating anchor nuts on the bulkhead to give me some wiggle room but I had no tool that would get into the scuttle corner to tighten the bolts, so I ended up using 6mm weld nuts on the brackets and drilling 8mm holes in the bulkhead. We offered the bonnet up and had just enough wiggle room to align the bonnet also using the normal adjustment as well. I filled the four 1/8” holes with countersunk pop rivets, hardly noticeable with a blob of paint.
My friend spent days stripping out the complete dash and removing the wiper motor and servo to allow me access, and obviously this needed all putting back, but he said he didn’t mind. (This is his first Mini). All in all a bit of an epic.
#22
Posted 10 October 2021 - 03:46 PM
As the old saying goes 'Necessity is the mother of invention'
1 user(s) are reading this topic
0 members, 1 guests, 0 anonymous users