Take out heater pipes then clean and cut out rust/paint off around surrounding area
Make a paper/card template then cut that out of steel plate then tack in place, once tacked in place and ur happy seam weld the rest
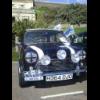
Yucky Welding!
Started by
mike49
, Sep 03 2007 08:01 PM
18 replies to this topic
#16
Posted 04 September 2007 - 10:24 AM
#17
Posted 04 September 2007 - 10:55 AM
yeah ive already patched one part, but this is proper awkward to get to as it goes up in the scuttle :S
also, the bottom of the scuttle in that part has rusted through, so would you weld a new bottom to, or is it strong enough without?
thanks alot!
oooo also, seeing as you seem to know your stuff!.. would you try fitting in a new piece the exact shape of the hole, or like place it over exisiting good metal and weld it on top?
cheers:D
also, the bottom of the scuttle in that part has rusted through, so would you weld a new bottom to, or is it strong enough without?
thanks alot!
oooo also, seeing as you seem to know your stuff!.. would you try fitting in a new piece the exact shape of the hole, or like place it over exisiting good metal and weld it on top?
cheers:D
Edited by mike49, 04 September 2007 - 11:00 AM.
#18
Posted 04 September 2007 - 01:51 PM
Thats not that bad i had tis to do on mine
[attachment=39100:65._25th.9.06.JPG]
The way I have always patched holes is to clean up the area with a grinder/wire brush combo to find the edges of the hole, don’t be surprised if it grows in size. Then I cop out the rust and some of the surrounding leaving only good clean metal to weld to and to make sure it’s all gone as squarely as possible to make fabricating the patch easer and neater.
Then make up a template in thin card that’s the exact same size as the hole, once done lay that template onto another piece and draw round it, then al the edges were you can I draw another line about ½” or the thickness of the masking tape I use and that will be the final size of the patch.
Once that patch has been transferred to meat and am happy with the size/fit I tack/weld it into place on both sides of the patch were possible, I do this for three reasons, one it’s much easer to lap weld rather that but weld and blow big holes, two for strength as your welding it twice and thirdly once seam sealed and painted there is now way for moisture/water to get in between the patch and existing metal work forming rust.
[attachment=39100:65._25th.9.06.JPG]
The way I have always patched holes is to clean up the area with a grinder/wire brush combo to find the edges of the hole, don’t be surprised if it grows in size. Then I cop out the rust and some of the surrounding leaving only good clean metal to weld to and to make sure it’s all gone as squarely as possible to make fabricating the patch easer and neater.
Then make up a template in thin card that’s the exact same size as the hole, once done lay that template onto another piece and draw round it, then al the edges were you can I draw another line about ½” or the thickness of the masking tape I use and that will be the final size of the patch.
Once that patch has been transferred to meat and am happy with the size/fit I tack/weld it into place on both sides of the patch were possible, I do this for three reasons, one it’s much easer to lap weld rather that but weld and blow big holes, two for strength as your welding it twice and thirdly once seam sealed and painted there is now way for moisture/water to get in between the patch and existing metal work forming rust.
Edited by 1984mini25, 04 September 2007 - 01:52 PM.
#19
Posted 04 September 2007 - 05:59 PM
hi mate, thanks alot thats very useful

1 user(s) are reading this topic
0 members, 1 guests, 0 anonymous users