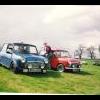
Diy Braided Brake Lines
#16
Posted 01 March 2008 - 12:20 AM
12000 or 10000psi would blow most solid pipes never mind flexi's not to mention your pistons etc.
That aside
I would still recommend Aeroquip, just need to speak to them to ensure you get the right stuff.
I use Aeroquip daily where I work and some of our equipment operates around the 4000psi mark. Their ultra high pressure stuff is for above 4000psi but there is no way on earth you will require that.
http://apps.esg.aero...n.asp?FAM=m_hfa
#17
Posted 01 March 2008 - 12:29 AM
a top spec 4 pot affair on a rally car would need to be capable of handling around 2000psi.
The compatition ones i've came in to contact with are only ever tested to 2500psi.
Mini would be quite a bit below that.
#18
Posted 01 March 2008 - 12:59 AM
DASH 3
• 600-03 is our original brake hose design. Extremely versatile, very flexible, and proven in every
type of racing. Stainless steel woven outer braid, with a natural clear PTFE inner tube, it has
extremely low expansion – less then 1% at 3,000 psi - providing a stiffer pedal feel.
Part number - Weight -- Pressure (psi) - Bend radius - Inner diameter - Outer diameter - Temperature
------------------- (g/m) -- Working / Burst ---- (mm) ----------- (mm) ------------- (mm) ---------- rating (°C)
--- 600-03 ------- 60 ----- 4250 / 12750 ------- 18 ------------- 3.50 -------------- 6.45 ---------- -70 / +235
Designed for use with stainless steel, mild steel, aluminium and titanium fittings, in both re-usable and
crimped versions. Section 3 - Goodridge catalogue
And having read that I've remembered why it is that flexible brake lines have such a high pessure rating. It's not to do with operating pressure, it's for pedal feel. Flexible hose will deform far more as it approaches its rating than solid lines will. Solid line can operate fairly close to its maximum pressure with no real loss of pedal feel while a flexible hose that is near to its burst pressure will stretch, since it is by nature elastic. That results in a loss of pedal firmness as braking effort increases which is very un-nerving.
#19
Posted 01 March 2008 - 08:04 AM
I've been and looked up the specs for Kunifer (the copper alloy pipe that most of us replace our brake lines with) and it seems it's only rated to 2250 PSi.
braking systems are somewhere between 3000 and 5000 psi
Do we take from this that the pressure in a Mini braking system is much lower than the average?
#20
Posted 04 March 2008 - 10:20 AM
You might be able to generate 1500 psi pressure in a hard brake application, so talk of deformation near the burst/maximum pressure will never be a problem.
And remember most of you will already have flexible lines already in your system (rear subframe and front calipers) which are most likely rubber, a change to teflon braided makes sense.
#21
Posted 04 March 2008 - 10:30 AM

http://www.speedflowshop.co.uk/
1 user(s) are reading this topic
0 members, 1 guests, 0 anonymous users