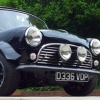
Shock Absorber Mount Repair
#61
Posted 10 October 2010 - 09:11 PM
The only reason I was going for a metric thread/bolt was that I thought UNF bolts would be harder to get hold of and that i'd have to get them made up at a nut and bolt place. But I just had a quick look on ebay now I know the thread and bought a pack of these for £3: Link
They're high tensile so should be nice and strong, zinc coated so they won't rot and being 3/4" long they should be pretty much the same size as standard.
So with the zinc primer I can just spray that onto the end of the box section and spray my repair pieces with it to protect them abit. The main thing i'm thinking is that plug welds obviously might not seal the end of the box section completely, so don't want an easy rust trap to form between the box section lip and repair pieces - Maybe i'm just thinking too far into it, but at the stage i'm at now I want to do it right so it'll be strong enough for coilovers in future aswell as long lasting.
One last quick question - How big should I drill the holes in my repair patches for the plug welds? I tryed to do abit of research on it and on the mig welding website: Link It says 7.5mm holes at 25-40mm spacing. But I was hoping to get maybe 4-5 plug welds onto each side of the box section, maybe about 4-5mm in size?
#62
Posted 11 October 2010 - 06:45 PM
Yeah, I know where the bottom mounting block goes as it just fell off whilst I was cutting near it.
The only reason I was going for a metric thread/bolt was that I thought UNF bolts would be harder to get hold of and that i'd have to get them made up at a nut and bolt place. But I just had a quick look on ebay now I know the thread and bought a pack of these for £3: Link
They're high tensile so should be nice and strong, zinc coated so they won't rot and being 3/4" long they should be pretty much the same size as standard.
So with the zinc primer I can just spray that onto the end of the box section and spray my repair pieces with it to protect them abit. The main thing i'm thinking is that plug welds obviously might not seal the end of the box section completely, so don't want an easy rust trap to form between the box section lip and repair pieces - Maybe i'm just thinking too far into it, but at the stage i'm at now I want to do it right so it'll be strong enough for coilovers in future aswell as long lasting.
One last quick question - How big should I drill the holes in my repair patches for the plug welds? I tryed to do abit of research on it and on the mig welding website: Link It says 7.5mm holes at 25-40mm spacing. But I was hoping to get maybe 4-5 plug welds onto each side of the box section, maybe about 4-5mm in size?
I tend to use 1/4" inch holes spaced roughly an inch apart. 7.5mm is a large hole but it means you will get plenty of strength in the plug weld. Plenty of power here is the key for the best penetration. 4-5mm holes are too small and will fill with weld too quick to form a joint.
The spacing of an inch is pretty much an industry standard on cars for spot welds so the distances mentioned are fine. There is absolutely no reason why you could not fit them closer especially if you are worried about making the joint water tight. In my industry Aircraft Engineering we have what is called the Sphere on Influence. Imagine drawing something like the Olympic overlapping circles and then put a rivet in the centre of each circle. Each rivet is of a certain size say 1/4", now the spacing between each rivet should be no more than 1" but 3/4" is ideal (3 to 4 times the diameter of the fastener.) This means that the clamped diameter of each rivet will overlap each over forming a water tight seal.
So if you have clamped your repair plate in tight and then plug welded quite close to each over then you should have a pretty tight repair. As i mentioned earlier you can pump in loads of Waxoyl into the back of the repair area so making it water tight/proof should be easy to achieve.
As to the Zinc rich primer yes liberally spray this over the area you need to weld straight onto the bare metal.
1 user(s) are reading this topic
0 members, 1 guests, 0 anonymous users