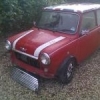
Why Don't They Make Stainless Panels?
#31
Posted 30 December 2011 - 10:22 AM
#33
Posted 30 December 2011 - 07:21 PM
#34
Posted 31 December 2011 - 03:57 AM
It actually weakens the structure because every time you go over a bump, the mass of the horrendously heavy battery is causing the floor to flex.
But as for welding mild steel to stainless, I saw some special MIG wire advertised somewhere which lets you do that, but it was horrendously expensive. Or you could use MIG "bronze welding" wire, which is not the same as brazing, so should pass MOT, but is even more expensive, something like £800 for a reel if I recall correctly. Why?
You could use a corrosion resistant steel like 3Cr12, which is not a true stainless, as it suffers minor surface rusting, and does weld to mild steel, as well as being more workable than stainless, but I don't know if you can get it in 0.9mm and 1.2mm sheets. Pity, because if it could be pressed on the existing tooling, which I think probably not, it would be possible for Heritage to make us a new and almost everlasting bodyshell for not a lot more money than a normal mild steel one. If the extra cost was only material, it might be about £500 extra,
Aluminium is a very bad material for building cars, especially those which are designed to be made of steel, because it has very poor energy absorption in a crash, and suffers from fatigue. I would give an aluminium Mini front end 5000 miles max before it fell apart.
#35
Posted 31 December 2011 - 10:34 AM
#36
Posted 31 December 2011 - 03:04 PM
I am guessing that you may indeed have 3Cr12. Please ensure that it is well protected by paint around the welded area, as in that region the corrosion resistance will be lost.
http://www.mig-weldi...forum/index.php is the place for definitive information on every aspect of welding.
http://www.askzn.co....grade_3cr12.htm is one useful source of information on 3Cr12. Note that it does not tolerate battery acid particularly well, but it does have good fatigue properties, unlike most types of stainless. Most people weld it with 316L stainless MIG wire.
#37
Posted 31 December 2011 - 04:02 PM
#38
Posted 31 December 2011 - 06:15 PM
#39
Posted 01 January 2012 - 03:08 AM
The complication comes if and when you need to change registration details, such as an engine change to a totally different type, because then you may be asked about how much of the car is original, or like for like replacements due to normal wear of course, i.e. are the suspension, axles, gearbox and steering assembly the original type? Lose too many points and it may be time for an IVA. Admit to modifying the monocoque and it will definitely be time for the dreaded IVA, which will need radical mods to the shell and other things to have a chance of passing.
A welded in stainless steel battery box could legitimately be said to be the same as the original in my opinion. Paint it and they would not see the difference anyway. A bonded in fibreglass box, no. But if you don't do anything to the car which attracts their attention, such as an engine change, they don't need to know.
Your insurance company however does need to be told of all modificarions, but I can't see them charging extra premium for a corrosion resistant battery box.
#40
Posted 01 January 2012 - 04:22 AM
#41
Posted 01 January 2012 - 07:48 AM
#42
Posted 01 January 2012 - 08:58 AM
anyone a MOT tester for your views ?
#43
Posted 01 January 2012 - 11:26 AM
The battery box on a Mini, as someone said, is part of the monocoque, just by being welded in.
A monocoque gets its strenght by the way that one panel braces another. In a properly designed monocoque, with no excess weight, no panel can safely be removed, as they are all carrying structural loads and/or stiffening another panel to prevent buckling. There is not much excess metal on a Mini. Certainly the centre of the roof, so you can fit a sunroof. But that is about the limit for safe use on the road, long term, unless bracing is added to replace whatever is removed.
is that not dangerous advice? removing a part of the monocoque shell and non welding a fg part in place?
Edited by midridge2, 01 January 2012 - 11:31 AM.
#44
Posted 01 January 2012 - 02:21 PM
normally they like new metal seem welded in place not bonded glassfibre, especially with in 30cm of the subframe mounts
#45
Posted 01 January 2012 - 06:51 PM
0 user(s) are reading this topic
0 members, 0 guests, 0 anonymous users