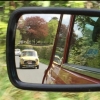
Rear Camber Adjustment:- Standard Outer Radius Arm Bracket
#16
Posted 30 April 2012 - 08:18 AM
#17
Posted 12 January 2015 - 09:47 PM
#18
Posted 19 February 2016 - 11:02 AM
(According to a MOT tester at Minispeed years ago) the MPI rear camber/tracking can be miles out - mine was!
Just fitted these from MIniSport http://www.minisport...ckets-pair.html
Got the suspension reset.... Job done & because they are ribbed they wont shift over time.
#19
Posted 19 February 2016 - 12:04 PM
The real key to optimum road holding with the classic Mini is not the front suspension, but accurate settings of the rear.
The fronts do seem to be tolerant of minor inaccuracies, but the rear needs to have zero to -0.5 degrees negative camber and 1 mm to 2 mm TOE-IN.
Get this right and the car will have good road-holding, it won't feel 'twitchy' when cornering hard and the handling will be safe and predictable at all speeds.
Compared to many cars, the Mini has little body roll and rear roll stiffness is good. The radius arms are true parallel vertically, so excessive rear camber, either way, will upset the 'sit' of the tyre onto the road thus reducing the road-holding and not helping the handling either.
Of course, it is ideal to set the front correctly, but as long as there is not excessive negative camber on the front and the TOE-OUT is 1mm to 2 mm it should drive well. This assumes that the suspension rubbers are all in good order and the car is not lowered or raised excessively from standard ride height. For best road-holding & handling on normal roads (as opposed to smooth race tracks) standard ride height gives the best results for driving the car.
#20
Posted 19 February 2016 - 06:33 PM
I opened up the hole in the bracket so there was a lot of play in all directions then made up a couple of stainless shims to space off the bracket in both directions from the subframe, camber and toe. I then used an old thick washer that goes between the trailing arm and bracket and placed this on the outside of the bracket then tightened up the nut on the trailing arm shaft finger tight. I then set the wheel/tyre to the camber and toe settings that I wanted then welded the thick washer onto the bracket. The shims I placed in between the bracket and subframe gives me a bit of adjustment either way. Only downside is that access to one of the fixing bolts for the bracket is now difficult to get to, and as a result I may replace them with adjustable ones then weld them up once I get the settings I want.
#21
Posted 19 February 2016 - 06:38 PM
#22
Posted 19 February 2016 - 10:11 PM
I opened up the hole in the bracket so there was a lot of play in all directions then made up a couple of stainless shims to space off the bracket in both directions from the subframe, camber and toe. I then used an old thick washer that goes between the trailing arm and bracket and placed this on the outside of the bracket then tightened up the nut on the trailing arm shaft finger tight. I then set the wheel/tyre to the camber and toe settings that I wanted then welded the thick washer onto the bracket. The shims I placed in between the bracket and subframe gives me a bit of adjustment either way. Only downside is that access to one of the fixing bolts for the bracket is now difficult to get to, and as a result I may replace them with adjustable ones then weld them up once I get the settings I want.
That is what I do.
#23
Posted 19 February 2016 - 10:31 PM
I opened up the hole in the bracket so there was a lot of play in all directions then made up a couple of stainless shims to space off the bracket in both directions from the subframe, camber and toe. I then used an old thick washer that goes between the trailing arm and bracket and placed this on the outside of the bracket then tightened up the nut on the trailing arm shaft finger tight. I then set the wheel/tyre to the camber and toe settings that I wanted then welded the thick washer onto the bracket. The shims I placed in between the bracket and subframe gives me a bit of adjustment either way. Only downside is that access to one of the fixing bolts for the bracket is now difficult to get to, and as a result I may replace them with adjustable ones then weld them up once I get the settings I want.
That is what I do.
If I remember I think it was you that advised me to do it this way!
#24
Posted 19 February 2016 - 10:46 PM
I think it was - and it worked too! Result.
#25
Posted 19 February 2016 - 10:48 PM
Is the welding mandatory on a road car?
Gonna check my rear camber in the comming days.. If its needed then I hope my MIG can handle it xd
#26
Posted 19 February 2016 - 11:03 PM
I always put a couple of tack welds to ensure the setting is maintained, but just clamping it may be enough - I've never tried though.
#27
Posted 20 February 2016 - 07:54 AM
OK so I measured the starting point at 2 degrees positive (Like I said a long way out) and got started. Following Coopermans suggestion I filed I/8" higher and this gave may 0.5degree improvement. Next step was 1/4" which gave 1 degree and a final 1/8" gave another 0.5 degree, So now I'm just about square. Problem is now the arm has come up so far it's partially covering the top bracket hole. I'm also able to bring it up more than standard due to a previous mod which converted the top bolt into a 'Torx' fitting so I don't have to worry about leaving clearance for a socket. I'm now very close, but I still don't think I've yet gone -ve.. I do not intend to resort to any work on the inside end of the trailing arm. So I've gone as far as I intend to and will get the thing finally checked with my friendly mechanic. The problem I have now is whether to use the tack weld to secure the washer on the bracket; If I do it would have to be broken should I ever need to remove it (as the arm will be fixed in a position fouling the top bracket bolt). My other solution is to fashion another bracket which has a 16mm hole for the arm and a small hole at the bottom through which I can pass a bolt to fix to existing bracket. I'm favouring the later, just so I can take it apart easily.
With that much adjustment needed, I really would be look to file the hole in the subframe for the inner mount and then weld a washer there too.
#28
Posted 20 February 2016 - 10:07 AM
#29
Posted 20 February 2016 - 11:26 PM
I would be wondering why it is so far out, i.e. is the subframe in poor condition, bent, cracked or corroded? Or, has the pivot seized at some time, causing the pin to rotate in the subframe, and wearing the hole at the inner end oval? Or maybe two consecutive bent radius arms. Quite possibly none of that, of course. But it just bugs me when things seem to be greatly exceeding their normal tolerances with no obvious reason. It would be nice to know.
But as Cooperman says, the vital thing is getting the toe correct, and the car can indeed be downright dangerously unstable if there is even a hint of toe out at the rear. Had that once, and it was horrible! I would have bought a Renault Dauphine (or several others from the early 1960s that were truly vile) if I had wanted that. As modifying the bracket to fix the camber has the potential to affect the toe, I would always advise having the toe checked asap. A good tyre dealer will do a full geometry check for a reasonable cost, especially if you are buying a set of tyres.
As for knowing how much to file, there is an easy way of estimating it. First measure the distance from the inner mounting face to the inside of the outer bracket, i.e. the length of the radius arm pivot including thrust washers. I don't have the exact figure to hand, but let us say for now that it is 9 inches. Now divide that dimension by 57.3. 9/57.3 = 0.157 inches. In that case moving the hole by 0.157 inches will change the camber by 1 degree. The same is true for toe, if you move the hole fore and aft, forwards to toe in. Works in metric too, just use mm or cm consistently for the pivot length and the hole movement.
I think someone stated the exact length of the pivot a while back, but can't find it right now. It wasn't a nice round 9 inches of course. Easily measured, a ruler or tape measure is good enough.
1 user(s) are reading this topic
0 members, 1 guests, 0 anonymous users